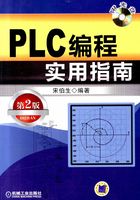
0.1 PLC的产生
关键词:触点控制电路、继电器控制电路、继电器、接触器、常开触点、常闭触点、可接插逻辑控制器、顺序控制器、GM 10条、可编程序控制器(PLC)
0.1.1 继电控制电路
继电控制电路是指,用一些控制电器的触点,如按钮、开关或继电器触点,控制用电器的电路。这些控制电器触点及其与用电器的不同连接,可反映它们之间不同的逻辑关系,以实现不同的控制。
继电器控制电路历史悠久,有了电的应用也就有它的存在。几经发展,越来越便于人们的使用,已在电控领域独领风骚100多年的历史了。尽管PLC的出现与进步已极大地压缩了它的使用空间。但正如飞机、火车、汽车、自行车的相继出现,前者不能取代后者一样,PLC的出现,也不可能完全取代继电控制电路。所以,在了解PLC的产生的同时,简单地回顾一下继电控制电路是必要的。
控制电器有手动的,它的触点的接通、分断用人工控制,如按钮、手动开关。还有自动的,它的触点的通断能自动实现,如行程开关、各种继电器。
继电控制电路有触点控制电路及继电器控制电路。以下分别对其进行介绍:
(1)触点控制电路。触点控制电路是指用手动控制电器触点的接通与分断,去控制用电器的电路。图0-1示的就是触点控制电路之一。
图0-1a为串联电路。它用两个触点串联控制一个电灯L。如图所示,只有两个按钮同时接通,此灯才能亮。从逻辑的关系讲,灯亮的条件是两个按钮“接通的与”。反之,灯不亮的条件是任意一个按钮分断,即两个按钮“分断的或”。
图0-1b为并联电路。它用两个触点并联控制一个电灯L。如图所示,两个按钮任意一个接通,此灯就亮。从逻辑的关系讲,灯亮的条件是两个按钮“接通的或”。反之,灯不亮的条件是两个按钮要同时分断,即“分断的与”。
图0-1c为混合电路。用触点串联后再并联,去控制一个电灯L。如图所示,只有X1、X2两个按钮同时接通,或按钮X3、X4同时接通,此灯可亮。从逻辑关系讲,灯点亮的条件是“X1、X2两个按钮接通的与”和“X3、X4两个按钮接通的与”的“或”。
图0-1 f也为混合电路。但它是触点并联后再串联,然后去控制一个电灯L。如图所示,只要按钮X1、按钮X2任意一个接通,同时按钮X3、X4任意一个接通,则此灯亮。从逻辑关系讲,灯点亮的条件是“X1、X2两个按钮接通的或”和“X3、X4两个按钮接通的或”的“与”。
图0-1 触点控制电路之一
提示:先串后并到先并后串的转换,可从原电路断的条件确定并的每一个并的小段,然后再把所有小段串联;先并后串到先串后并转换可从原电路的可能通路确定每一个串的支路,然后再把每一支路并联。
图0-1g为桥接电路。如图所示,除了触点串联、并联还有像按钮X6那样的桥接。它不能用简单的“与”、“或”,去反映它的逻辑关系,故也称复杂电路。相对于复杂电路,仅用触点串并联的控制电路称为简单电路。
要表达复杂电路的逻辑关系,可根据可能产生的通路情况,先求出在控制功能上,与其等价的简单电路,然后用等价电路的逻辑关系来代表它。图0-1d即为图0-1e的等价电路。从图知,它除了按钮X1与按钮X2串联,按钮X3与按钮X4串联,然后并联之外,还有因桥接按钮X6接通,又增加了的两路串联后的并联。
当然也可连接成先并后串的桥接等价电路。这点还是留给读者自己思考吧!
提示:在PLC梯形图程序中不允许出现桥接的逻辑关系。
图0-2是触点控制电路之二。
图0-2a为先串后并表决电路。这里用了3个按钮X1、X2、X3,当3个中任意2个,或3个全部按下,都将使灯L亮。这里只有3个按钮参与表决,如果增多,也可实现。只是电路要复杂些。
图0-2b为先串后并再串比较电路。这里用了两组4个按钮X1、X2及Y1、Y2,当这两组接通及分断情况相同时,灯L亮。否则,灯L不亮。当然,用3组或多组比较也是可实现的。只是电路再多串入一组或多组按钮。
图0-2c为先并后串表决电路。与图0-2a的功能相同。
图0-2d示的为先并后串比较电路。与图0-2b的功能相同。
图0-2e示的为先串后并等权控制电路。这里用了3个按钮X1、X2、X3,当3个中任意1个改变状态,都将改变灯L的状态。把这三个开关安装不同位置,可用以实现三地开关对一个灯的等权控制。这里只有3个按钮参与等权控制,如果增多,也可实现。只是电路要复杂些。
图0-2 触点控制电路之二
图0-2f为先并后串等权控制电路。与图0-2e的功能相同。
从以上分析可知,对一些常见的逻辑关系,用触点控制电路是可以实现的。但要实现更复杂的逻辑关系或要用小开关去控制大动力的电路就得求助继电器控制电路了。
(2)继电器控制电路。继电器控制电路除了使用手动控制器触点,还使用继电器触点,其控制对象既有用电器,又有电磁继电器自身线圈。
图0-3 异步电动机点动控制电路
图0-3为异步电动机点动控制电路。图0-3a为它的工作示意图,图0-3b为它的电气原理图。
从图知,按钮SB按下,其触点使控制回路通,接触器KM线圈得电。线圈得电,电磁力克服弹簧力,使KM主触点接通,电动机M得电、工作。按钮SB松开,则控制回路分断,KM线圈失电,电磁力消失,弹簧力使KM主触点分断,电动机M失电、停止工作。按钮按下,电动机工作,按钮松开,不工作,所以称之为点动控制。
图中S为刀开关,合上后才能实施控制。FU为熔断器,用以确保用电安全。
由于这里使用了比按钮触点可通过更大电流的接触器,所以,可用一个小小的按钮灵活地控制一个较大功率的电动机。
图0-4 串联起、保、停电路
图0-4为串联起、保、停电路,是用按钮控制用电器工作最常见的控制电路。
从图0-4a可知,按钮SB2按下,则控制回路通,接触器KM线圈得电,其常开主触点KM合上,电动机M得电、工作。KM的常开辅助触点与SB2是并联的。因而之后即使SB2松开、触点分断,仍可使KM线圈得电,继续工作。工作后,按钮SB1按下,其触点分断,使接触器KM线圈失电,进而也使电动机M失电、停止工作。由于KM触头已分断,之后即使SB1松开、常闭触点再合上,KM也仍失电,电动机仍保持停止。可知,此控制电路可控制电动机的起、保、停。
图中QS为刀开关,合上才能实现控制。FU1、FU2为熔断器,用以确保用电安全。
图0-4b为图0-4a的简化。这个电路的要点是,把接触器的常开辅助触点与起动按钮并联,之后再与常闭的停车按钮串联。因此,按钮SB1可起动被控设备工作;起动后能使被控设备保持工作;按钮SB2可停止被控设备工作。故称之为起、保、停控制电路。
除了上述用串联控制起、保、停电路,还有并联控制及混合控制的类似电路。
图0-5即为并联起、保、停控制电路。
从图知,这里起动按钮SB1改用常闭触点,停车按钮SB2改用常开触点。继电器触点也改用常闭触点。并还增加了吸收电阻R。为了KM能正常工作,电源电压要比KM的额定工作电压高。
图0-5 并联起、保、停控制电路
用以上类似的分析,可知,此电路的功能与图0-4b是完全相同的。
提示:这里吸收电阻是不可或缺的。不然将出现电源短路,那是绝对不允许的。
图0-6为混合电路。SB1、SB2、KM全用其常开触点。它也是用以实现起、保、停逻辑。与图0-5不同的是,在KM停止工作时,吸收电阻不工作,不消耗能量。
图0-5电路进一步演变可得到图0-7的电路。
图0-6 混合起、保、停控制电路
图0-7 矩阵连接起保停电路
从图0-7可知,其左边画的控制触点SB1、SB2为电路输入;控制触点KM为继电器KM的常闭触点,用做输出反馈。右边画的继电器线圈KM,为电路输出。中间用点画线框起来的竖线与横线为逻辑方阵。其中R为吸收电阻,竖线与横线的联系通过二极管(用小斜箭头表示)实现。
如图所示,P点的高电位是由P1与P2两点高电位的“或”实现,而P1、P2高电位则取决于控制它的触点分断的“与”。可以看出,如图所示的逻辑关系,也是起、保、停逻辑。
图0-7所示的电路用的元件多,但可把控制电路“标准化”了。从设计思想上讲,这里有两个突破:
1)便于更改控制逻辑关系;
2)控制触点使用次数可不受限制。
这两条突破,可使控制电路实现各种逻辑控制变得方便、灵活,是很有意义的。
使控制电路便于设计,便于更改,有人还曾做过其他方面的探讨。有的还设计成可进行程序预选及反馈预选的电路。然而,它总是要靠触点的通断实现控制,所以,不可避免地存在如下一些缺点:
1)触点转换总是需要时间的,总是有电滞后及机械滞后。这两个滞后加起来,长的可达几十毫秒,甚至更多。这两个滞后可能造成控制不及时、不同步。不及时,会降低控制精确度;不同步,有时会使电路工作出现竞态。这是在电路设计时,不得不采取措施加以避免的。
2)触点频繁通断,易受电火花烧蚀与机械磨损,并因此随着使用次数的增加,总是会带来一些故障。
3)体积大,安装这些元器件有时需庞大的控制柜。
4)消耗电能多。初次投资费用不大,但日常使用费用很高。
5)难以或不便实现逻辑关系复杂的控制。
6)电路不通用,每种电路多数都要单独设计、单独制造,更改也不便。
所以,要实现复杂的、灵活的、更可靠的、小型化的电气控制,必须寻找别的出路。
0.1.2 可接插逻辑控制器与顺序控制器
(1)可接插逻辑控制逻辑。在图0-7电路中,吸收电阻、隔离二极管是直接与继电器线圈串联的。继电器工作时,通过它们的电流都相等;继电器不工作时,通过吸收电阻的电流则更大。这既浪费电能,又得考虑散热问题。所以,不大适用。
图0-8电路是它的改进。图0-8a的继电器线圈通过晶体管带动。吸收电阻、隔离二极管与带动继电器工作的晶体管的基极相连,所以,消耗的功率小得多。
图0-8b用RS触发器代替继电器。输出为无触点元件。不仅消耗功率低,而且转换速度快,工作可靠,工作寿命也长。
图0-8 可接插控制逻辑
在这个基础上,还可用一些集成电子元件,使控制器小型化,成为可编程序逻辑控制器,可方便地用以实现输出与输入之间的逻辑变换。但是,它的变换编程只能通过逻辑方阵中竖线与横线的不同连接实现,所以,实际上应称之为可接插逻辑控制器。
图0-9 程序步进控制电路
(2)可编程序顺序控制器。搞过逻辑设计的人都有这样体会,用逻辑运算的方法做逻辑综合是比较难的。特别是时序逻辑,处理起来更难。而用程序步进控制的思路处理它,则比较容易。
图0-9为程序步进控制电路。图中的程序步进器按顺序1、2、3…转换程序。程序与输出的对应关系通过逻辑方阵(图左下方)预选。如图所示,程序1与输出B相连、程序2与输出C相连,即执行程序1时,可使输出B工作等。要改变程序与输出的关系,只要改变这里的竖线与横线间连接就可以了。
程序步进器的步进,或叫程序转换,由输出动作完成的应答信号,即输入信号控制。而执行某个程序后到底由那个应答信号控制步进,也通过逻辑方阵(图左上方)预选。如图所示,执行程序1时,输入X动作可使程序步进;执行程序2时,Z可使程序步进等。要改变这个关系,用改变横竖线的连接即可实现。
实现图0-9关系的具体电路很多,而且都用了集成电子电路,由于它是按程序顺序工作的,程序的动作又是可更改的,故称之为顺序控制器。
上述这两种控制器的出现,把控制电路发展成了电子控制器。它可由专门厂商成批生产,用户购置后,依需要设计好逻辑关系,稍做接线即可使用。这应该说是电气控制的一大进步。
不过,它们编程是靠硬件实现的,还是不大方便。同时,大规模集成电路也难使用。这使得这种控制器的进一步小型化、降低成本、降低功耗以及获得更高的可靠性都受到限制。也正是由于这个原因,这两种控制器虽然也风行过一时,但最后还是被淘汰了。
0.1.3 GM10条
20世纪60年代末期,由于电子计算机技术的发展,曾把小型电子计算机用作机械工作或生产过程的逻辑控制。计算机通过改变程序,更改控制,这比更改硬件接线方便得多。但它也存在一些缺陷:
1)编程复杂,要求有较高水平的编程与操作人员;
2)需要配备相应的外部接口;
3)对工作环境的条件要求较高;
4)功能“过剩”,机器资源未能充分利用;
5)造价昂贵。
所以,美国通用汽车(GM)公司为适应汽车工业发展的需要,于1968年提出设计新型电控制器的要求,并提出10点招标指标:
1)编程简单,可在现场修改程序;
2)维护方便,最好是插件式;
3)可靠性高于继电器控制柜;
4)体积小于继电器控制柜;
5)可将数据直接送入管理计算机;
6)在成本上可与继电器控制器竞争;
7)输入可以是交流115V;
8)输出为交流115V、2A以上,能直接驱动电磁阀;
9)在扩展时,原有系统只需很小变更;
10)用户程序存储器容量至少能扩展到4KB。
这就是著名的GM10条。如果说种种电控制器、电子计算机技术的发展是PLC出现的物质基础,那么GM10条则是PLC出现的直接原因。
0.1.4 PLC的诞生
GM10条提出后,Bedford联盟(Bedford,MA)向其提议制作模块化数字控制器(ModularDigital Controller,MODICON),即MODICON 084。它是世界上第一块成为商品的PLC。在美国GM公司的装配线上试用,取得了成功。也从此,有了著名的MODICON品牌PLC。其创始人,迪克·莫利(Dirk Morley)也为此被誉为PLC之父。
随后,这项技术在美国就迅速地发展起来。过了两年,日本人从美国引进了这项新技术,很快研制成类似的控制器,即DSC-8。又过了两年,即1973年,西欧国家也制成了这样的控制器。
有决定意义的进步还是在1975~1976年之间。这两年,美国、日本、德国等一些国家把微处理器(Microprocessor)用作可编程序控制器的中央处理单元(Center Processing Unit,CPU),用集成电路的存储器代替磁芯存储器,把微型计算机的技术与上述两种电控制器结合起来,使得可编程序控制器实现更大规模的集成化,工作更为可靠,更能适应工业环境,而且还更加灵活,功能也更加强。同时,成本也大幅度地降了下来,从而使PLC进入了实用阶段。
我国于1974年开始研制,1977年开始工业应用。
该种控制器出现后,其名称和定义不大统一。为此,美国电气制造商协会NEMA(NationalElectrical Manufacturers Association)于1980年正式将其命名为可编程序控制器(ProgrammableController,PC),并给它下了定义:“PC,是一种数字式电子装置,它使用了可编程序的记忆体以存储指令,用以执行诸如逻辑、顺序、计时、计数与演算等功能,并通过数字或类似的输入/输出模块,以控制各种机械或工作程序。”
1985年1月,国际电工委员会(IEC)在颁布可编程序控制器标准草案第二稿时,对它也下了定义。这个定义为:“可编程序控制器是一种数字运算操作的电子系统,专为在工业环境下应用而设计。它采用可编程序的存储器,用来在其内部执行逻辑运算、顺序控制、定时、计数和算术运算等操作指令,并通过数字式、模拟式的输入和输出,控制各种类型的机械或生产过程。”
可知,PLC这个电子系统,也是靠存储程序、执行指令,进行信息处理,实现输入到输出的变换。但它的目的是用以控制各种类型机械或生产过程。所以,从实质上讲,它是一台工业环境应用的、满足实时控制要求的专用计算机。与普通计算机所不同的主要是:
它没有键盘,代之为一个个输入电路,并用其获取控制命令或现场信号。同时,此输入电路具有滤波能力,与内部电路为电隔离,但可通过光耦合建立联系。
它没有显示器,取而代之的为一个个输出电路,并用其产生控制输出。由于此电路具有驱动能力,故可以驱动一般的工业控制元器件,如电磁阀、接触器等。同时,此电路与内部电路也是电隔离的,用光或磁耦合建立联系。
它没有硬盘,只有内存。但可配备存储卡,以为程序与数据建立备份;
它配置有外设或通信接口,可用以编程或下载程序、监控及连网通信;
它的结构为模块化,体积小,安装方便,比较坚固,具有很强的抗干扰、抗冲击、抗振动特性。
总之,PLC只是一台没有键盘、没有显示器、没有硬盘,但有很丰富的输入、输出(接口)电路并且具有较强的驱动能力、配有接口,可在工业现场实时使用的、模块化、小型化的、专为工业环境应用而设计制造的特殊计算机。而且,PLC还不针对某一具体工业应用,在实际应用时,其硬件可根据实际需要进行配置,其软件也可根据控制要求进行设计编制。
要指出的是,随着技术进步,PLC的功能在不断增强,性能在不断提高,应用在不断扩展,类型在不断增多。所以,它的概念也在不断更新。无疑的是,它已发展成为当今方方面面自动化、信息化的重要支柱。