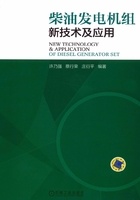
2.2 柴油机技术的发展
自第一台四冲程柴油机在1896年研制。100多年来,柴油机技术得以快速而全面的发展,在相关领域得到广泛应用。经过大量研究成果表明,柴油机是目前被产业化应用的各种动力机械中热效率最高、能量利用率最好、最节能的机型。装备了最先进技术的柴油机,升功率可达到30~50kWh/L,扭矩储备系数可达到0.35以上,最低油耗可达到198g/kW·h,标定功率油耗可达到204g/kW·h;柴油机被广泛应用于船舶动力、发电、灌溉、车辆动力等广阔的领域,尤其在车用动力方面的优势最为明显。全球车用动力“柴油化”趋势业已形成。在美国、日本以及欧洲100%的重型汽车使用柴油机为动力。在欧洲,90%的商用车及33%的轿车为柴油车。在美国,90%的商用车为柴油车。在日本,38%的商用车为柴油车,9.2%的轿车为柴油车。据专家预测,在不久的时间内柴油机将成为世界车用动力的主流。
现代的高性能柴油机由于热效率比汽油机高、污染物排放比汽油机少,应用日益广泛。西欧国家不但载货汽车和客车使用柴油发动机,而且轿车采用柴油机的比例也相当大。美国联邦政府能源部及美国三大汽车公司为代表的美国汽车研究所理事会研发新一代经济型轿车同样将柴油机作为动力配置。经过多年的研究、大量新技术的应用,柴油机最大的问题——排放和噪声取得重大突破,达到汽油机的水平。
1.柴油机发展方向的主要体现
(1)升功率和比质量
升功率和比质量是衡量柴油机性能的有效指标;现代发动机的技术发展体现在发动机的质量越来越轻,而功率越来越大,新材料和新结构的不断应用提高了发动机升功率,降低了比质量。
内燃机的发展水平取决于其零部件向高精尖的水平发展,而内燃机零部件的发展水平,是由生产材料及制造技术等因素来决定的。也就是说,内燃机零部件的制造技术水平对主机的性能、寿命及可靠性有决定性的影响。由于铸造技术水平的提高,气冲造型、静压造型、树脂自硬砂造型制芯、消失模铸造,使内燃机铸造的主要零件如机体、缸盖等可以制成形状复杂曲面及箱型结构的薄壁铸件。这不仅在很大程度上提高了机体刚度,降低了噪声辐射,提高了零部件之间的配合精度,而且使内燃机达到轻量化。
(2)柴油机的高压缩比
压缩比的提高,使热效率得到了提高。柴油机由于其压缩比大,最大功率点、单位功率的油耗低。在现代技术性能更好的发动机中,柴油机的油耗约为汽油机的70%,柴油机是目前热效率最高的内燃机。柴油机因为压缩比高,发动机结实,故经久耐用、寿命长。
(3)柴油机的增压及电控燃油系统
优良的燃烧系统;采用4气门技术、超高压喷射、增压和增压中冷、可控废气再循环和氧化催化器、降低噪声的双弹簧喷油器、全电子发动机管理等,集中体现在以采用电控共轨式燃油喷射系统为特征的新一代柴油机上。
柴油机增压技术的应用早在20世纪20年代就有人提出压缩空气提高进气密度的设想,直到1926年瑞士人A.J.伯玉希才第一次设计了一台带废气涡轮增压器的增压发动机。由于当时的技术水平、工艺和材料的限制,还难以制造出性能良好的涡轮增压器,加上二次大战的影响,增压技术未能迅速发展,直到大战结束后,增压技术的研究和应用才受到重视。1950年增压技术才开始在柴油机上使用并作为产品提供市场。50年代,增压度约为50%,四冲程机的平均有效压力约为0.7~0.8MPa。
70年代,增压度达200%以上,四冲程发动机已达2.0MPa以上,二冲程发动机已超过1.3MPa,普遍采用中冷,使高增压(>2.0MPa)四冲程发动机实用化。单级增压比接近5,并发展了两级增压和超高增压系统。
80年代,仍保持这种发展势头。进排气系统的优化设计,提高了充气效率,充分利用废气能量,出现谐振进气系统和MPC增压系统。可变截面涡轮增压器,使得单级涡轮增压比可达到5甚至更高。采用超高增压系统,压力比可达10以上,而发动机的压缩比可降至6以下,发动机的功率输出可提高2~3倍。进一步发展到与动力涡轮复合式二级涡轮增压系统。提高平均有效压力可以大幅度地提高效率,减轻质量。一台增压中冷柴油机可以使功率成倍提高,而造价仅提高15%~30%,即每马力造价可平均降低40%。
在20世纪60年代后期内燃机电子控制技术产生,通过70年代的发展,80年代趋于成熟。随着电子技术的进一步发展,燃机电子控制技术使其控制面会更宽,控制精度会更高,智能化水平也会更高。如燃烧室容积和形状变化的控制、压缩比变化控制、工作状态的机械磨损检测控制等较大难度的内燃机控制将成为现实并得到广泛应用。内燃机电子控制将由单独控制向综合、集中控制方向发展,是由控制的低效率及低精度向控制的高效率及高精度发展的。
(4)内燃机材料技术
内燃机使用的传统材料是钢、铸铁和有色金属及其合金。在内燃机发展过程中,人们不断对其经济性、动力性、排放等提出了更高的要求,从而对内燃机材料的要求相应提高。对内燃机材料的要求主要集中在绝热性、耐热性、耐磨性、减摩性、耐腐蚀性及热膨胀小、质量轻等方面。现代的陶瓷材料具有无可比拟的绝热性和耐热性,陶瓷材料和工程塑料(如纤维增强塑料)具有比传统材料优越的减摩性、耐磨性和耐腐蚀性,其比重与铝合金不相上下而比钢和铸铁轻得多。因此,陶瓷材料(高性能陶瓷)凭借其优良的综合性能,可用在许多内燃机零件上,如喷油点火零件、燃烧室、活塞顶等。若能克服脆性、成本等方面的弱点,在新世纪里将会得到广泛应用。工程塑料也可用于许多内燃机零件,如内燃机上的各种罩盖、活塞裙部、正时齿轮、推杆等,随着工艺水平的提高及价格的降低,未来工程塑料在内燃机上的应用将会与日俱增。
(5)柴油机技术的发展体现在节能、环保、动力强、维修方便等方面
柴油机具有较好的经济效益。虽然柴油机的初置费用较高,但其燃油经济性比汽油机高30%左右,同时柴油价格相对较低,经过一定运行小时的使用后,柴油机总的成本费用明显低于汽油机。因柴油机不用点火系统和分电器,其故障率大大降低,柴油机可靠性更高。
随着高压共轨喷油等一系列新技术和新装备的应用,同时结合柴油颗粒捕集器、稀氮氧化物捕集器、选择性催化还原系统等后处理装置技术,柴油机排放变得更为清洁,克服噪声大且冒黑烟的不良形象,成为更清洁、更省油、功率更强劲的动力装置。
柴油机排气后处理技术的现状和发展方向,柴油机尾气处理在于NOx(氮氧化物)和碳烟微粒,目前柴油机排气控制技术采取了一系列措施,而等离子体技术是未来柴油机排气后处理的发展趋势。
柴油机电子控制技术的发展状况,从20世纪70年代开始,进入20世纪80年代,英国卢卡斯公司、奔驰汽车公司、德国博世公司、美国康明斯公司、美国通用的底特律柴油机公司、卡特彼勒公司、日本五十铃汽车公司及小松制作所等都竞相开发新产品并投放市场,以满足日益严格的排放法规要求。
柴油机具备高扭矩、高寿命、低油耗、低排放等特点使其成为解决汽车及工程机械动力问题最现实和最可靠的手段。随着柴油机的数量及使用范围迅猛发展。对柴油机的经济性能、动力性能、废气排放及噪声污染控制的要求也越来越高。传统的机械控制喷油系统已无法满足喷油量、喷油压力和喷射正时完全按最佳工况运转的要求。近年来,随着信息技术、计算机技术及传感器技术的迅速发展,电子控制的电子产品在可靠性、体积、成本等各方面都能满足要求,使电子控制燃油喷射更加容易实现。
实际上,与汽油机相比柴油机排气中CO和HC少得多,NOx排放量相近,主要是排气微粒较多,与柴油机燃烧机理有关。柴油机是一种非均质燃烧,很短时间形成可燃混合气,而且可燃混合气形成与燃烧过程互相交错。对柴油机喷油规律分析得出:喷入燃料的雾化质量、气缸内气体的流动以及燃烧室形状等均直接影响燃烧过程的进展以及有害排放物的生成。有效地改善排放需提高喷油压力和柴油雾化效果,使用预喷射、分段喷射等。
深入研究和新技术的应用使柴油机的发展有了巨大变化。现代先进的柴油机一般采用电控喷射、高压共轨、涡轮增压和中冷等技术,在体积、重量、噪声、烟度等方面已接近了汽油机的水平。随着国际排放控制标准(如欧洲Ⅳ、Ⅴ标准)的颁布与实施,汽油机和柴油机都面临着严峻的挑战,采用电子控制燃油喷射的技术是解决办法之一。柴油机电子控制技术在发达国家的应用率已达到90%以上。
2.现代柴油机采用新型技术的主要特点
1)致密石墨铸铁的应用,使发动机轻便而小巧。而致密石墨铸铁天生的硬度同时也增加了发动机的耐用性并减少了噪声。
2)新一代高压共轨柴油直喷技术,有效实现低排,高效;部分柴油发动机的喷射燃油时的压力高达1,600Pa,产生压力极大。较高的喷射压力同时提高了发动机的效率并有助于降低其排放。
3)压电喷油器,控制喷油正时和喷油量。压电喷油器是燃油喷射的最前沿技术,它保证更大、更精确容量燃油能以比其他燃油喷射快两倍的速度进行喷射。大幅提升动力与扭矩。
4)双喷射,压电喷油器的高速运转允许在正式进行燃油传输前,先行输送小量的燃油-试喷射。试射保证了更流畅的动力传输同时增加了燃油的纯度。压电喷油器降低了其他柴油发动机上明显的噪声及振动的缺陷,同时提高了燃烧效率、增加输出功率,而排放与燃油消耗降低,其中柴油微粒催化过滤用来减少尾气排放等。同时,发动机配有涡轮增压器,优化了高低速扭矩,提高了可靠性及性能。