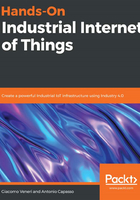
Automation in the industrial process
Factory automation can be defined as a discipline that studies the methods and technologies that allow the control of flows of energy, materials, and information needed for the realization of production processes.
The importance of automation in a modern production process derives from a multiplicity of factors, not just economic ones, among which are the following:
- The improvement of the quality of the products
- The opportunity to use the same production system for different products in a concept known as flexibility of the plant
- Shorter production times
- The opportunity to reduce the number of incoming and outgoing warehouses
- The drastic reduction of processing waste
- Lowering the cost of production
- The need to comply with laws or regulations
- The opportunity to reduce the environmental impact and save energy
- The improvement of the competitiveness of the company as a whole
In an automated system, we can identify the physical processes and the control system, as shown in the following diagram:
Physical processes can be defined as the sum of the operations that act on entities belonging to the physical world and which change some of their characteristics. Operations that fit this definition include material or part movements, mechanical processing, or chemical reactions. These physical processes can be considered objects of automation. Pure and simple information, on the other hand, does not make changes to the real world, and so cannot be considered a physical process.
A physical process receives raw materials and energy as inputs. It also receives information, which can be in the form of electric voltage, current values, or fluid pressure, or which can be coded in sequences of binary values. It produces output materials in the form of finished products and waste, and also sends information. The noises coming from the environment that act on the process can also be considered as inputs to the process itself.
The outgoing information is provided by appropriate devices made by the following:
- Sensor: Transforms the variable to be measured into the type necessary for measurement
- Transducer: Accepts information in the form of a physical or chemical variable, and converts it into a magnitude of a different nature—typically electric
Very often, sensors and transducers coincide in the same physical component. We generally call a device a sensor (or a transducer) if it measures a magnitude and gives an output as a signal, typically an electrical one. The incoming information is used by the actuators to set the value of the control variables for the process. Usually, the real actuator is built by a pre-actuator, which processes the information to convert it into a power signal. Sensors, actuators, and pre-actuators carry out part of the physical process and act as interfaces to the control system.
A control system receives information on the status of the process from the sensors and processes them according to the specified algorithms. It then sends to the actuators information related to actions that provide the desired control of the physical process. The control system also receives information from one or more external entities, such as human operators or other control systems that are hierarchically higher. It is also able to provide information about its own status and the controlled process to the external entities.