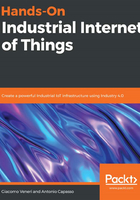
Actuators
In typical process control applications, the acquisition of the process variables to be controlled and the processing of the control laws is carried out through analogical or numerical controllers that work on a low power signal level. The variable that is processed by the controller and sent to the process to carry out the necessary corrective actions is handled in the same low power representation. The process, on the other hand, may require high levels of power to be controlled. Examples of processes that require high levels of energy include thousands of cubic meters of a liquid or the forces of hundreds of thousands of Newton, such as in a metallurgical rolling process.
The function of the actuator is to convert low energy control signals into actions of a power level that is suitable to the process to be controlled. This function can be considered as an amplification of the actuation signal generated by the controller. In many cases, the signal is also converted and then transduced into a completely different physical dimension.
A final control element carries out the necessary steps to convert the control signal generated by the controller into actions performed on the process. To change the flow rate of a fluid from 10 to 50 cubic meters per second, for example, a typical control signal of between 4 and 20 mA requires some intermediate operations. The necessary operations may depend on the process and the controller, but they can be summarized in the following diagram:
The preceding diagram can be explained as follows:
- The first operation is the Signal Conversion. This represents the modifications that must be implemented on the control signal so that it is compatible with the actuator. If, for example, the controller is numeric, and the final control element is a valve, the actuator may be a direct current motor. In this case, the signal conversion will be performed by a DAC and a power amplifier. The output of the conversion produces a transduced and amplified signal, which establishes the control variable of the process. This effect on the control variable is usually carried out by a physical device that is related to the process, such as a valve or a conveyor belt.
- The Actuator can be defined as a device that converts the control signal into an action on the control component, not on the process.
- Finally, we arrive at the Final Control Component. This device has a direct influence on the dynamic variables of the process and is an integral part of the process. If a flow rate must be controlled, for example, the last control element might be a valve that is part of the fluid transport system. If a temperature must be controlled, the last control device will have a direct influence on the temperature.