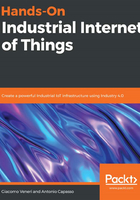
PLCs
PLCs originated in 1968, when General Motors United provided the desired features for a new generation of controllers to be used in their production facilities. Currently, a PLC is based on a multiprocessor system, with network integrated abilities that are able to perform very complex functions. It is based on almost the same technologies as a usual computer, but adapted to the control of industrial processes. A PLC consists of several main components—a processor, I/O, a power supply, a remote I/O, a fieldbus, PID, a servo, and an encoder. It also contains other components that are available for specific uses as independent modules. The cabinet or rack contains and encloses all of the modules, ensuring the first deep integration from the pure mechanic world and the electronic world. There are some PLCs that are not modular but instead contain all of the fundamental components in a single device. The standardization of PLC programming languages from the IEC 61131-3 standard has greatly contributed to making PLCs more open and less tied to a specific vendor. The IEC 61131 standard provides the following five PLC programming languages:
- Sequential Functional Chart (SFC)
- Ladder diagram
- Functional Block Diagram (FBD)
- Instruction list
- Structured text
The first three are graphical programming languages, while the last two are textual languages. The most common PLC vendors in the market are Siemens AG, Rockwell Automation, Mitsubishi Electric Corporation, Schneider Electric, and Omron Corporation. In the following sections, we will look at some of the main modules of a PLC.