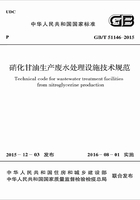
4.2 废水安全处理
4.2.1 废水收集应符合下列规定:
1 硝化甘油生产单元与安全处理单元布置应相对独立,在保证安全的前提下宜靠近布置,生产废水不宜远距离输送;
2 生产废水应统一收集,并应通过专用管路输送至废水安全处理工序;
3 生产废水安全处理前,废水管路坡度宜为2%~5%;
4 生产废水安全处理单元及管路宜进行保温。
4.2.2 废水输送及管路设计应符合下列规定:
1 硝化甘油废水至安全处理装置的排放管道宜使用明铺不锈钢管。安全处理后的废水可采用不锈钢管或其他耐腐蚀管线。
2 硝化甘油废水管道焊接或法兰连接应光滑平整,接口处密封应牢固可靠。
3 硝化甘油废水管道基础应平稳、坚固。
4 铺设在地下的硝化甘油废水管道应在冻土层以下,管路上面不得建造其他建筑和设施。
5 硝化甘油废水管道明铺时宜安装在便于检查的保温廊道中,明铺的硝化甘油废水管道较长时,保温廊道应至少每隔30m设一个检查窗,并应设置热胀冷缩补偿装置。
4.2.3 硝化甘油废水贮存应符合下列规定:
1 收集的硝化甘油废水应贮存在不锈钢容器内;
2 未经安全处理的硝化甘油废水储存时间不应超过24h。
4.2.4 曲道器单元设置应符合下列规定:
1 曲道器不应少于2台,数量及大小应根据废水的水量确定;
2 废水在每台曲道器内的停留时间不应小于0.5h;
3 曲道器宜选用不锈钢材质,曲道器底部应装设胶管阀;
4 曲道器应定期检查,底部的硝化甘油应每天从曲道器底部胶管阀排出,并应用胶皮桶回收处理,每次不应超过5kg。
4.2.5 皂化单元设置应符合下列规定:
1 碱液宜选用氢氧化钠配制,浓度宜为10%~15%;
2 废水经曲道器排出后宜自流进入皂化装置,并应加入碱液进行皂化,中和后的废水可通过蛇形管夹套以蒸汽间接加热或在蒸煮器内进一步皂化;
3 中和皂化装置应设置搅拌装置,宜采用pH自动控制加药系统;
4 中和皂化装置中废水pH值应控制在10~12,蒸煮时间不应少于3h,蒸煮温度应控制在95℃以上;
5 中和皂化装置应设置自来水冲洗和碳酸钠溶液冲洗系统,冲洗后废水应排入废水处理站。