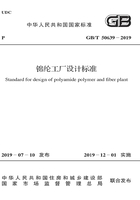
3.4 工艺计算
3.4.1 聚合装置的工艺计算应以装置的设计生产能力为基准,并应进行物料衡算和热量衡算。
3.4.2 聚酰胺6的聚合、萃取、干燥、单体回收和低聚物全回用等主要设备的生产能力应按照装置的操作弹性、设备运转效率、物料停留时间以及产品质量特性等进行计算,并应符合下列规定:
1 当无备台、无液态CPL供应时,固态CPL熔融运转效率宜取70%;
2 助剂调配系统应按产品方案中需加入比例最高助剂量为基准,每批调配量不应小于16h使用量;
3 聚合反应器停留时间应根据典型品种确定,同时应对高负荷、高黏度产品工艺条件进行核算;
4 萃取和干燥系统负荷率宜取85%;
5 回收系统运转效率宜取85%,同时应对非正常工况进行核算。
3.4.3 聚酰胺66和聚酰胺56的反应器、闪蒸器、预聚合器、后聚合器等主要设备的生产能力应按照装置的操作弹性、设备运转效率、物料停留时间以及产品质量特性进行计算。
3.4.4 泵、风机、压缩机等动力设备的流量、扬程和设备台数应根据聚合装置的操作特性、弹性范围和压力降等因素计算确定。
3.4.5 换热器的换热面积和设备的规格应根据工艺操作参数和热量平衡数据计算确定。
3.4.6 二次热媒的换热量和循环量应根据装置的设计生产能力和聚合反应的各段热量平衡计算确定,再计算一次热媒的加热量和循环量。
3.4.7 纺丝和熔体输送设备及熔体夹套管应进行热量衡算。
3.4.8 下列管道应进行应力计算:
1 聚合装置中温度不小于200℃、管径不小于DN65的热媒管道;
2 不小于DN100的干燥切片用循环热氮气管道;
3 聚合反应器顶部排放热气管道;
4 聚合物熔体输送管道。
3.4.9 管道应力计算应核算不同工况聚合反应器的端点附加位移对管道系统的影响,并应充分利用管道走向的自然补偿。
3.4.10 切片输送、干燥,纺丝及后处理的工艺设备配置应以单台(套)设备的生产能力为基本依据,并应结合产品方案中的产量、设备运转效率计算所需台(套)数。
3.4.11 纺丝熔体管道设计应进行下列计算:
1 熔体管道的管径分配和长度应通过计算确定,应保证到达生产相同产品的每个纺丝箱体的熔体输送管道内的熔体压力降和熔体停留时间相等,且熔体黏度应在纺丝允许范围内;
2 纺丝熔体管道系统设计的热应力分析计算应在满足安全性的前提下,使管道长度最短;
3 纺丝熔体管道设计应进行管道系统熔体压力降、熔体停留时间和黏度降计算。
3.4.12 每条纺丝生产线的热媒加热设备的能力应根据工艺参数和装置生产能力计算。
3.4.13 纺丝冷却风的风量和风速应以产品方案中小时产量最大的品种为依据计算确定。
3.4.14 油剂调配系统的能力及配置应根据产品方案计算确定。
3.4.15 组件清洗设备配置应根据设备清洗能力和清洗周期,以及需清洗的纺丝组件、计量泵、过滤芯的数量,计算所需台(套)数。