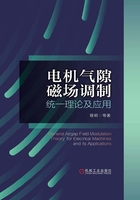
2.1 磁场调制式磁齿轮
机械式齿轮和齿轮箱被广泛用于变速传动系统,虽然机械齿轮具有很高的转矩传递能力,但是其自身也存在一些固有的问题:
(1)运行噪声大,存在振动和摩擦,热损耗较大。
(2)需要润滑和定期维护,运行成本较高。
(3)过载时存在不可逆损坏的风险。
(4)可靠性较差,是变速传动系统故障率较高的部件之一。
与机械齿轮相比,基于磁场耦合实现能量传递的磁齿轮则具有很多优势:
(1)振动小、噪声低。
(2)无机械接触,不存在摩擦损耗。
(3)无需润滑,免维护,运行成本低。
(4)具有过载保护能力,可靠性高。
(5)输入和输出轴之间能够实现物理隔离。
虽然磁齿轮已经提出很长时间,但是早期传统转换型磁齿轮由于转矩传递能力较差,并未得到广泛关注和应用。近年来,随着高性能磁场调制式磁齿轮的提出和永磁体性能的不断提高,磁齿轮的研究再次引起了国内外专家学者的兴趣。
磁齿轮概念最早于1916年提出,当时美国学者Neuland在其申请的发明专利中描述了一种电磁齿轮拓扑结构[1],该电磁齿轮采用电励磁线圈产生磁场,已具磁齿轮的雏形,由于其结构较为复杂且转矩密度和效率较低,提出后并未得到太多关注。1941年,美国学者Faus借鉴直齿圆柱型机械齿轮结构提出了一种简化的磁齿轮形式,即用永磁体的N极、S极分别代替圆柱机械齿轮的齿和槽,利用磁场耦合实现转矩的传递[2]。20世纪80年代以后,随着高性能钕铁硼永磁材料的出现,该类磁齿轮因其结构简单,再次成为研究的热点。这一时期提出的磁齿轮多数是根据机械齿轮演变而来,结构形式基本保持不变,仅是简单地用磁极代替机械齿槽,磁场耦合代替齿槽啮合,所以可将此类磁齿轮统称为传统转换型磁齿轮,图2-1所示为一种径向外耦合平行轴转换型磁齿轮。虽然转换型磁齿轮具有简单的结构,但是永磁体利用率低,导致转矩传递能力弱,一直未得到广泛应用。
2.1.1 基本结构与工作原理
2001年,英国学者K.Atallah和D.Howe提出了一种具有高转矩密度的高性能同轴磁齿轮。与转换型磁齿轮相比,该同轴磁齿轮结构具有如下特性:静止于高速转子和低速转子之间的调磁环,能够对高、低速转子永磁体产生的磁场进行调制,从而使所有永磁体产生的磁场能够同时相互耦合产生转矩,改善了永磁体利用率,大大提高了磁齿轮的转矩传递能力[3,4]。该同轴磁齿轮结构被提出后便得到了广泛关注和研究,通过改变转子永磁体的布置和充磁方式,国内外学者又相继提出了多种不同的磁齿轮拓扑结构[5-9]。由于此类磁齿轮均基于磁场调制原理工作,所以可将其统称为磁场调制式磁齿轮。
如图2-2所示,FMMG包括由外至内、同轴心排列的外转子、调磁环、内转子,调磁环静止放置在内、外转子之间,三者由内、外气隙隔开,转子能够自由旋转。调磁环由导磁铁块和非导磁块沿圆周交替排布组成,导磁铁块由硅钢片叠压而成,内转子铁心外表面和外转子铁心内表面贴永磁体,相邻永磁体沿径向交替反向充磁。其工作原理是,内(外)转子产生的永磁磁场经导磁铁块的磁场调制作用后,能够在外(内)气隙产生一系列空间谐波磁场,只需根据其中幅值最大的异步空间谐波磁场的极对数来选择外(内)转子永磁体极对数,就能通过磁场耦合实现稳定的转矩传递。此时,导磁铁块的个数等于内、外转子永磁体极对数之和,内、外转子的旋转速度比等于内、外转子永磁体极对数比的倒数。根据能量守恒原理,内、外转子传递的转矩比则等于内、外转子永磁体极对数比,即实现了齿轮变速传动的效果[3,4]。
与传统转换型磁齿轮不同,上述FMMG的内、外转子永磁体产生的磁场,经过调磁环的磁场调制作用,能够共同耦合进行转矩的传递。仿真和实验分析表明,该径向充磁表贴式同轴磁齿轮的转矩密度可达100kN·m/m3,其转矩传递能力可以与普通机械齿轮相媲美。参考Atallah和Howe教授在文献[4]中报道的径向充磁表贴式FMMG的相关实验结果,对比与其转速、传动比和输出转矩相近的商业化机械齿轮,分析结果见表2-1[10,11]。对比分析表明,径向充磁表贴式FMMG在体积、质量和效率等方面均具有明显优势。由于非接触、无摩擦,不存在机械损耗,所以FMMG具有较长的使用寿命。受永磁体价格影响,FMMG的成本比机械齿轮高很多,但其免维护特性节省的维护费用在一定程度上能够弥补成本差价。

图2-1 径向外耦合平行轴转换型磁齿轮

图2-2 径向充磁表贴式FMMG拓扑结构
表2-1 径向充磁表贴式FMMG与商业化机械齿轮比较

为了进一步改善FMMG的性能,基于磁场调制原理,通过改变永磁体的布置或充磁方式,国内外学者又提出了多种MMG拓扑结构,如图2-3所示。图2-3a为内、外转子永磁体采用Halbach方式充磁的同轴磁齿轮,Halbach永磁体排布不但可以使气隙磁通密度波形更接近正弦波,而且能够改善气隙磁场强度,从而有效提高磁齿轮的转矩传递能力[8]。但是,永磁体Halbach充磁过程复杂,且加工制作成本较高。为了防止内转子高速旋转时表贴的永磁体脱落,提高机械可靠性,图2-3b所示FMMG内转子采用了辐条嵌入式永磁体安排,该结构同时还可以产生一定的聚磁效应,能够帮助改善磁齿轮转矩传递能力[5]。为了提高外转子机械完整性,图2-3c所示FMMG的外转子采用同极性永磁体表面内嵌结构,将磁化方向相同的永磁体沿外转子内表面均匀间隔排列,在保持转矩传递能力不变的情况下,该结构能够节省永磁体用量,而且简化了外转子机械加工工艺,降低了成本[7]。

图2-3 不同同轴式FMMG拓扑结构
2.1.2 磁场调制效应的定性分析
同轴磁齿轮的关键是在内外转子之间设置了由铁磁材料和非铁磁材料间隔排列构成的调磁环,正是它实现了内外转子上不同极对数永磁磁场之间的有效耦合。下面以一同轴磁齿轮为例,通过磁场分布定性分析调磁环对内、外转子永磁磁场的调制效应,从而说明磁齿轮的工作原理[12,13]。
为一般起见,设内转子的角速度为ω1,极对数为p1;外转子的角速度为ω2,极对数为p2;调磁环的角速度为ωFe,铁磁导磁块数为NFe。
为简单起见,假设内、外转子永磁体磁动势沿圆周方向呈正弦分布,即

式中,F1m和F2m分别为内、外转子永磁体磁动势幅值;φ1和φ2分别为内、外转子永磁体磁动势的初相角;θ为机械角度;c1和c2分别为内、外转子转向系数,顺时针方向取+1,逆时针方向取-1。
1.无调磁环时的气隙磁场
首先观察没有调磁环时的情况,此时内、外转子之间的气隙均匀,磁导恒定不变,气隙磁通密度与磁动势相差一个系数,因此很容易得到由内、外转子永磁体产生的磁通密度为

式中,B1m和B2m分别为内、外转子永磁体所产生的磁通密度幅值。
如图2-4所示,与永磁磁极对数相对应,内转子磁场在一个完整圆周内具有4个周期,而外转子磁场呈现出22个周期。显然,由于两个磁场具有不同的周期数,它们不可能有效耦合,因此也就无法产生稳定的电磁力矩。
2.有调磁环时的气隙磁场
设调磁环由NFe块铁磁材料和非铁磁材料间隔组成,其磁导波如图2-5所示。略去高次谐波,调磁环的磁导可表示为

式中,Λ0为磁导平均分量;Λm为磁导交变分量的幅值;cFe为调磁环转向系数,cFe=1表示顺时针方向,cFe=-1表示逆时针方向;φFe为磁导交变分量的初相角。

图2-4 无调磁环时内、外转子永磁体产生的基波磁场示意图

图2-5 磁环磁导波(局部)
由式(2-1)和式(2-5)可得内转子永磁体所产生的气隙磁通密度为

式中

由此可见,内转子永磁体产生的气隙磁场包含三个分量:第一个分量B11为基波分量,其极对数和转速与内转子相同;而第二、三分量则是由于调磁环的调制作用所产生的。
类似地,外转子永磁体所产生的气隙磁通密度为

式中

外转子永磁体产生的气隙磁场包含三个分量:第一个分量B21为基波分量,其极对数和转速与外转子相同;而第二个、第三个分量则是由于调磁环的调制作用所产生的。
对于图2-2所示的同轴磁齿轮,调磁环静止不动,转速ωFe=0。为简化起见,设φFe=φ1=0,则式(2-8)和式(2-9)变为

可见,内转子永磁体产生的磁场分量B12极对数为NFe-p1,转速为,转向与内转子相反,磁场分量B13极对数为NFe+p1,转速为
,转向与内转子相同。
如果设计磁齿轮的参数使其满足

则B12变为

其极对数为p2,与外转子基波永磁磁场B21极对数相同。只要使二者的转速相同,即可实现B12与B21的稳定耦合,从而产生转矩,如图2-6a所示。取c2=-c1,则转速关系为

定义

为磁齿轮变速比。
类似地,可得外转子磁通密度分量为

其极对数为p1,与内转子基波永磁磁场B11极对数相同。当转速满足式(2-18)时,B22的转速与B11相同,二者实现稳定耦合,从而产生转矩,如图2-6b所示。

图2-6 调磁环的磁场调制效应
综上所述,同轴磁齿轮参数在满足式(2-16)的前提下,内转子永磁体在内气隙中产生极对数为p1的基波磁场,其转速与内转子相同;经调磁环调制之后,内转子永磁体还在外气隙中产生极对数为p2的谐波磁场,其转速恰好与外转子的基波磁场转速相同,构成耦合谐波对。同样,外转子永磁体一方面在外气隙中产生极对数为p2的基波磁场,其转速与外转子相同;另一方面,经调磁环调制后,外转子永磁体还在内气隙中产生极对数p1的谐波磁场,其转速与内转子的基波磁场转速相同,构成另一谐波对。正是在这些谐波对的相互作用下,实现内、外转子之间的转矩传递,内、外转子的转向相反,转速大小与极对数成反比。这便是同轴磁齿轮中调磁环的“磁场调制效应”或同轴磁齿轮的基本工作原理。
2.1.3 其他类型的磁齿轮
与传统转换型磁齿轮不同,FMMG利用磁场调制原理能够实现较高的转矩传递能力,所以成为目前研究较多的磁齿轮类型。
一方面,为适应不同形式的传动需求,国内外学者提出了基于磁场调制原理的多种直线、轴向和横向磁通FMMG。图2-7所示为圆筒形直线FMMG结构,文献[14]分析指出,该直线FMMG传递的力密度高达1.7MN/m3,与直线永磁无刷电机结合,可方便地实现低速大推力操作,非常适合于诸如海浪发电、铁路牵引等直驱应用场合[15,16]。图2-8所示为轴向磁齿轮结构,文献[17]报道指出,图2-8a所示盘式轴向磁通式FMMG的转矩密度可达70kN·m/m3,而且高速转子、低速转子和调磁环之间的轴向应力非常低。文献[18]提出如图2-8b所示的同轴式轴向磁通式FMMG,通过将调磁块安装在磁齿轮轴向端盖上,有效减少了机械结构的复杂程度,其转矩密度达77kN·m/m3,略高于盘式轴向磁通式FMMG。文献[19]提出了一种横向磁通式FMMG,如图2-9所示,两个转子均采用永磁体与铁心间隔排列的结构,且永磁体切向充磁,相邻永磁体充磁方向相反,其最显著的特征是两个永磁转子轴向并排设置,而调磁环则位于两个转子轴向外侧,形成横向磁通路径。在此基础上,文献[20]将调磁环设置为T形,如图2-10所示,通过在两个轴向并排的转子之间增加一条有效磁路的方式,使该类FMMG的转矩密度增加到282. 56kN·m/m3。

图2-7 直线FMMG结构

图2-8 轴向磁通式FMMG结构

图2-9 横向磁通式FMMG结构[19]

图2-10 轴向—横向磁通复合式FMMG结构[20]
另一方面,为降低永磁体之间的极间漏磁,现有文献通常将具有多极对数的低速转子安排为具有较大直径的外转子,而将具有少极对数的高速转子设置为内转子,这种安排方式虽然可以为外转子永磁体提供较多的安装空间,从而提高永磁体利用率,但高速转子上的永磁体却承受着高速运行所带来的巨大离心力,为永磁体(特别是采用表贴方式安装的永磁体)的机械稳定性带来巨大挑战。文献[21]提出了一种高速转子采用内置式永磁体的安装方式,试图增加高速侧转子机械结构强度,以适应其高速运转的需求,但这一方案中的导磁桥无疑会受到很高的应力,从而增加了FMMG的设计难度。此外,由于FMMG基于磁场调制原理运行,气隙中存在大量的同步和异步运行的谐波磁场,通常会导致高速运行的高速侧转子永磁体涡流损耗十分突出,严重降低了FMMG的传动效率。
鉴于上述两个原因,文献[22]提出一种高速转子磁阻式FMMG,如图2-11所示,该方案中的低速转子与中间调磁环和传统FMMG完全一样,但其高速内转子侧采用凸极磁阻式,有效简化了高速转子机械结构,增加了其机械强度。因此,该磁阻式FMMG更能胜任高速和超高速运行,从而有望提高整个传动系统的功率密度。研究表明,当高速转子铁心采用型号为2605SA1的非晶合金时,磁阻式FMMG的传动效率将比传统FMMG高,然而,该FMMG的转矩密度仅为传统FMMG的1/3左右,且转矩脉动较大。

图2-11 磁阻式FMMG结构
综合上述分析,对比传统转换型磁齿轮和磁场调制型磁齿轮,可以概括出未来高性能磁齿轮应具有如下特点:①转矩/力密度高,能与普通机械齿轮相媲美;②结构简单,加工制作方便;③可靠性高,稳定性强;④加工成本低。由于同轴磁齿轮具有较高的转矩密度,且可以方便地与现在的永磁无刷电机相结合实现变速传动,所以磁场调制型同轴磁齿轮无疑是未来磁齿轮研究和发展的趋势。