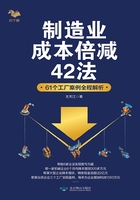
【案例5】落实外协检验减少品质支出
一、竟然没有品质部
笔者在长三角辅导某企业时遇到了一个问题:这家年销售额8000万元、200多人的企业竟然没有品质部,品质管理的功能散落在仓库、车间、跟单员之间。
没有品质部的制造型企业有两种:一种品质非常好,不需要设置这个部门;另一种是品质较差,设置不了品质部。实地调研后发现,这家企业显然属于后者。
设置不了品质部的原因有以下几种:
第一种原因,企业老板观念上不同意设置,认为设置品质部会额外增加人工成本,殊不知这些减少的人工成本与隐形的品质成本比起来是“小巫见大巫”。
第二种原因,同样是企业老板不同意设置,原因是原来设置过品质部没有发挥出应有的作用,厂里的不良品没有减少,返工、报废、退货、客诉和原来一样多,有些企业甚至是增多了,并且事情处理起来更加麻烦,最后认定这个部门多半是摆设,再次设置只会是“重复昨天的故事”。
第三种原因,是利益交织造成的,品质部成为多方利益博弈的交会点,品质部自身不具备良好的博弈能力,反而成了品质关联各部门之间推诿的靶子。采购部门抱怨品质部验收标准不统一,生产部抱怨来料不良多影响效率品质部没有拦截住,销售部抱怨成品经过品质部的检验还是有大量不良、退货、客诉等。最主要的是,一些具体事务涉及品质判定背后带来的利益变动所产生的压力。这些变动直接带来的就是博弈和冲突,品质部的人员承受不了这些压力,解决不了这些博弈和冲突,最终选择黯然离开这个企业或品质部,导致企业老板同意设置这个部门却没有人愿意来这个部门工作的尴尬局面。
这家企业没有品质部主要是第三种原因造成的。之前企业老板同意设置了品质部,由于放任不管,成立不到两个月就宣告夭折。后来企业老板主动暂停了一些外部事务,决定再次成立品质部,并亲自挂帅管理品质部。这个部门在企业老板的推动下,第1个月的确发挥了作用,品质状况开始好转;第2个月,随着企业老板事务增多,经常出差不在公司,品质部的人员陆续提出辞职;第4个月,品质部的人员全部离开,品质部宣告解散。从此以后,再也没有人提出成立品质部。
二、重新成立品质部
这家企业的品质部就是在这种情况下重新成立的,在咨询团队的带领和推动下,品质部在企业里站稳了脚跟,企业内部各项品质管理动作、流程、表单、会议得到落地,企业各级人员品质意识得到提高,品质管理氛围开始形成。
通过建立1个月的品质数据发现,内部的检验合格率比之前有所提高,但是没有持续提高,原因是受来料检验外协厂影响较大,来料检验部分外协厂的合格率不足80%。如果品质部要求退货会使外协厂产生额外费用,个别外协厂在拉走退货之后干脆不再交货,等着企业着急出货柜时再原封不动地把退货拉过来。如果品质部提出一些品质要求,他们都回复做不到。如果这些有问题的半成品被接收,会影响公司内部生产效率和成品品质,外协厂处于一种退不得、严不得的状态,成了这个阶段品质管理的瓶颈。
那么,能不能管理好这些供应商,或者换掉一部分供应商呢?
经详细了解,更换供应商的想法是行不通的。这些外协供应商中绝大部分是企业老板的亲戚、朋友、同学、老乡,个别外协厂甚至是唯一供应商。笔者还了解到,受多种因素制约,大部分外协供应商在这个地区很难开发出来新的外协厂商。也就是说,只能将现有的外协供应商用好才能解决来料合格率的问题。
其实,这也是大量中小企业品质管理中客观存在的真实状况,大型企业对供应商有绝对的品质控制权,整改不达标就可以更换,而中小企业由于资源有限,品质部对供应商的品质控制权干涉有限,这也就不难理解为什么有的企业没有品质部,有的企业品质部的人总是在变动,有的企业品质部发挥不了应有的作用。
有关系的供应商品质水平一直不高、难以管理是品质管理的难点之一。
三、第一个难题,解决外协供应商的品质问题
对于这些外协供应商的品质问题,咨询老师提出了以下措施:
第一项措施:书面通知所有的外协供应商,要求他们在交货之前必须自行检查品质状况,各种加工过的材料、零部件检查结果均需要记录在《外协加工交货检查表》(见表1-2)上,否则仓库不予收货。如果私自收货处罚仓管员,如果因私自收货造成返工由仓管员承担损失,请企业老板签字,同时也要求企业老板不得在没有填写《外协加工交货检查表》的情况下越权要求放行。
表1-2 外协加工交货检查表(木制品)REV:01

接下来,由采购部召集所有外协供应商到厂里讨论《外协加工交货检查表》的内容,仓管人员全部参加,品质部逐条讲解检查事项并询问外协供应商是否认可。实际上,这些是最基本的产品质量要求,没有人提出异议,品质部还对各外协供应商培训了表单的填写方式,为每家外协供应商下发一张填写完成的表单样板,最后请各外协供应商在通知上签字确认。
开完这次会议的第1周,执行情况良好,每家交货的外协供应商每次交货都能填好《外协加工交货检查表》交给仓管员。
第2周,有的供应商交货开始忘记填写,仓库一律不收货,品质部就在仓库收货处放置了一部分空表,让没有填表的供应商可以随时补填。这样的事情慢慢增多,一些供应商开始抱怨,填这个表有什么用,纯粹是在走形式,浪费时间和纸张,对品质提升没有任何帮助。
第3周,品质部经理开始动摇了,接受了一些供应商的观点,认为填这份检查表没有用。笔者提示他,这个检查表一开始就是个形式,每次交货都要填写,的确很麻烦。我们也知道有的供应商就是在对付,品质部人员要耐得住性子,一年有300多天,供应商每天每次交货前填表都得做“假”,他们不累吗?把第1周到现在的《外协加工交货检查表》拿出来仔细查看,按供应商名称分开,看一下哪些供应商是认真填写的、哪些供应商是对付着随便填写的。结合来料检验统计数据,给填表有问题的供应商指出问题,对于没有问题的供应商给予表扬,形成统计排名。这样做下去,这些《外协加工交货检查表》有一天就会变成真实的内容,就成了有约束力的品质管理措施。
品质部经理按这个思路找出了几家供应商的问题,如产品有洞眼不良高达50%仍然打√、产品100%变形也打√,有的供应商在检验结果“是”这一栏位竟然全部打√。品质部经理一一找到这些供应商的负责人,约他们到厂里进行面对面地沟通,批评他们是“闭着眼睛做事”。
从这一天起,品质部经理结合品管员提供来料检验数据,每天审核供应商填写的每一份《外协加工交货检查表》,有问题立刻指出,每天对填表状况进行公布、排名。1周以后,这份表和来料检验数据相符了。一个月后,外协来料检验合格率顺利达到90%以上,外协品质逐渐好转。
第二项措施:笔者要求采购部、品质部与外协供应商签订《品质保证协议》,主要是针对两方面的内容:一方面要求外协供应商必须保证合格率在90%以上;另一方面外协品质人员需要经过品质部培训、考试、认证,不得随意更换外协品质人员,外协供应商最终全部签订。接下来,品质部开始介入每一家外协厂品质的辅导,提高了对外协厂的巡查频率,为外协厂现场讲解产品各项品质要求,这些措施的执行促使外协来料检验合格率平均值在95%以上。
第三项措施:由品质部修订《品质保证协议》,将外协来料检验合格率与货款支付挂钩:
·外协来料检验合格率高于95%(含)在原有交易条件下优先付款优先下达采购订单。
·外协来料检验合格率低于90%(含)在原有交易条件下延期1个月支付货款。
·外协来料检验合格率低于80%(含)在原有交易条件下延期2个月支付货款。
·外协来料检验合格率低于70%(含)在原有交易条件下延期3个月支付货款。
每月月底品质部将优先付款、延期付款的外协厂名单直接交由企业老板批准,然后转交财务部,财务部按规则付款。此后,这家企业的外协来料合格率有了质的进步,稳定在95%以上。
经统计,由于外协来料合格率提升,该企业每月直接节约2400个工时。
品质部,是一个说起来很重要、做起来不重要、忙起来不要、出了品质问题跑不掉的部门。多年咨询实践观察发现,品质经理是制造型企业里流失率最高的中层管理岗位,这种局面与企业规范程度无关,无论是民营企业、台资企业还是外资企业大都一样,这个岗位在本企业里基本保持流失速度最快、流失率最高。
上面叙述的这家企业品质架构从无到有,那么对于品质架构完善的企业有哪些品质成本可以降低呢?请看下一个案例。