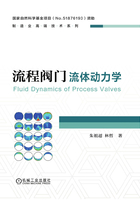
1.3 流程阀门研究现状
流程阀门的内部流动性能是其调控特性的内在表现,内部流动性能的变化将直接影响阀门的工作性能及工作可靠性。近几十年来国内外研究人员对流程阀门的流体动力学特性也开展了较多的研究工作,致力于提高阀门的使用性能。这些研究中,较多针对单相介质,并取得了一些研究成果。对于输送含固多相介质的阀门研究相对较少。下面将从单相和两相两个方面对国内外研究现状进行阐述和总结。
1.3.1 单相工况
对于流动介质为单相液体或气体的阀门,国内外学者分别从稳态和瞬态角度对其内部流动开展了大量的研究。
1.稳态分析
Chen等人[6,7]采用有限元方法编译了一套程序对带有圆盘阀的管道内部稳态流动性能进行二维数值模拟,分析了雷诺数、阀芯的位置以及阀芯的厚度等因素对流场内涡分布、压力分布、速度分布和湍流强度等参数的影响。Francis等人[8,9]采用有限元软件FIDAP对一个气体减压阀内部轴对称可压缩流场进行分析,同时开展实验对阀芯下表面的压力分布进行测量,研究了不同阀芯抬升高度对阀芯下表面压力分布及作用在阀芯上的气动力的影响。Moujaes[10]采用STAR-CD软件对3种开度的带法兰球阀进行三维数值模拟,研究不同进口雷诺数对流动损失系数及流量系数的影响。Sibilla[11]采用数值模拟技术对喷嘴止回阀内部流动特性进行研究。通过对不同湍流模型的稳态数值模拟结果和实验结果进行对比分析,认为RNG k-ε湍流模型能够更加精确地描述阀门内部的流动情况。An等人[12]采用CFD-ACE软件对LNG船舶系统中使用的防空化调节阀进行稳态数值模拟和改进优化,分别对带楔形阀芯的传统调节阀和带防空化节流孔阀芯的新型调节阀开展研究,分析阀门进出口压降,以及汽蚀和流量系数等阀门流动特性参数。Lee[13]采用CFD软件对圆盘止回阀的压力损失和流量系数进行计算,进而优化了支承梁的长度,并分析了不同流量下最优化结构的水头损失。
Morris等人[14]对流动介质为可压缩空气的蝶阀内部流动特性开展风洞实验研究,采用可视化技术拍摄流场的纹影图像,同时提取阀体壁面和阀芯表面的压力分布信息。实验研究了两种阀芯结构以及不同开启角度和工作压力比对流动特性的影响。Yi等人[15]采用CFD-FEM优化方法对止回式蝶阀的结构进行优化设计。通过流场分析确定旋转轴的高度,通过水锤分析获得作用在阀芯上的水锤压力,基于流场分析和水锤分析的结果,运用拓扑学优化和形状优化两种固体结构优化方式改进阀芯的结构。Leutwyler等人[16-18]采用不同湍流模型对中间开度的对称型蝶阀进行大量二维和三维数值模拟,分别研究不同气体压缩状态和不同气体流速对阀门内部气体流场、蝶板受力以及气动扭矩等阀门性能参数的影响。Song等人[19,20]采用CFD-FEM流固耦合计算技术结合正交实验与Kriging模型对一个传统蝶阀进行数值模拟优化分析;采用CFX软件对一个大型蝶阀在不同开度下的内部流场特性进行分析,并基于流场分析结果对阀门结构开展应力应变特性研究。
Chern等人[21]采用颗粒追踪方法对一个透明球阀进行流场可视化实验研究,重点分析阀门开度和进口速度对阀门内部以及阀后流动形态、空化性能等流动特征的影响。Ferrari等人[22]采用高速摄像技术对球形阀门在不同开度下的空化性能进行实验研究,并基于实验与数值模拟技术,对流体作用在阀芯上的径向力、轴向力以及压力分布进行分析。Palau-Salvador等人[23]采用CFD数值模拟和实验相结合的方式对调节阀开展研究,分析阀门阀芯出口结构对其内部的湍流性能和空化性能的影响。
袁新明等人[24,25]采用粒子成像流速仪(PIV)对弯型截止阀对称面模型进行了流场显示研究,并采用RNGk-ε湍流模型分别对弯型进口和斜进口截止阀对称面流场开展数值模拟研究,对比分析了弯型进口和斜进口截止阀流场特性。何世权等[26]采用CFD方法对角式调节阀进行了三维数值模拟,获得了其流量特性曲线、流道内压力分布和速度场分布等信息,并通过分析表明流闭型流向可提高阀门流量系数。张伟政[27]以套筒调节阀为对象,以数值模拟为研究方法,以降低能量损失和湍流耗散率为目标,对阀门内部能量损失严重的部位进行优化设计。冯卫民等[28]采用CFD方法对偏心球阀的内部流场进行了分析,分析了不同开度下偏心球阀内部流场结构及阀门流量特性、汽蚀特性和压力恢复系数等,并指出偏心球阀的阀体内部在小开度情况下,存在着较大尺度的三维流动。
2.瞬态分析
Kioni等人[29]提出了一个二维轴对称管道瞬变流动的数值模拟运算算法,并对瞬态关闭工况下阀门内部的速度场和压力场结构进行了模拟分析。Li等人[30]将作用在旋转止回阀阀芯上的水力矩分成静止水力矩和旋转水力矩,并通过实验测量和数值模拟对这两个分力矩进行分析研究。Cho等人[31]通过稳态和非稳态实验对一个球阀的力平衡性能开展研究,并基于CFD技术对该阀门进行流动分析,进而考察阀芯上下表面的压力分布和受力状况。Wang等人[32]采用CFX软件对单阀芯蝶阀在开启过程中的非定常流动进行三维数值模拟,对中间对称截面的速度分布和压力分布进行了分析,并考察了流量系数、动态转矩系数以及拖曳系数等性能参数随阀门开度的变化规律。Scheffermann等人[33]采用STAR-CD模拟软件对水坝锁紧阀开启过程进行非定常数值模拟,计算过程通过Hite的物理模型实验进行验证。文章研究了不同开启时间下,阀门下游压力随时间的变化规律,并分析了阀门流量系数随阀门开启角度的变化规律。Song等人[34]采用CFX软件对弹簧压力安全阀的内部流场性能及动态特性开展非定常CFD数值模拟。
李哲等人[35]采用动网格技术对固体燃气发生器调压阀进行三维数值模拟,分析了阀门内部收敛-扩张结构内的瞬态流动分布及特性参数的波动变化规律,并研究了进口压力对阀门动态特性的影响。冯卫民等人[36]以特大口径水轮机进水球阀为对象,研究动态关闭过程阀门前后压力及机组流量的变化规律,结果表明二阶段关闭能够有效地降低球阀的最大水击压力,并指出球阀内部涡区分布与水击压力最大值之间存在内在关联。钱锦远等人[37-39]采用数值模拟的方法对截止阀进行研究,分析讨论了结构变化及开启时间等参数的变化对阀门内部流场结构、阀门空化规律及阀芯受力特性等的影响,并在此基础上提出阀门的优化措施。崔宝玲等人[40]采用滑移网格技术分析了阀门启闭过程中的压差和流阻特性随着启闭时间的变化规律,并分析了阀门内部流场在开启和关闭过程中的差异性。
可以看出,国内外研究人员从稳态和非稳态等角度对单相介质阀门开展了大量的流体动力学特性研究,分析了阀门的受力特性、流动性能等,并获得了丰硕的研究成果。但是由于阀门使用领域的多样化以及阀门种类的多样化,流程阀门内部流体动力学特性研究还需要进一步深入开展,从而更好地为阀门的设计开发以及应用控制服务。
1.3.2 含固两相工况
含固两相是流程阀门在实际使用中常碰到的工况条件,包括气固两相和液固两相。由于介质中含有颗粒,流程阀门内部极易磨损,然而针对流程阀门两相流体动力学特性以及颗粒运动所导致的磨损特性研究还是普遍偏少。而当阀门处于固定开度下时,其内部流道近似为一种曲折的管道结构,因此含固两相工况下曲折管道的研究成果也可以为阀门的研究提供参考。同时,国内外研究人员针对颗粒与壁面的碰撞磨损也开展了大量的研究工作,并提出了一系列的磨损计算模型,为含固两相工况下阀门流道的磨损数值计算提供了理论支撑。下面将对颗粒与壁面的碰撞磨损研究、阀门内部两相流动及磨损研究,以及曲折管道内两相流动及磨损研究三个方面的研究现状进行分析。
1.颗粒与壁面的碰撞磨损研究
颗粒与壁面的碰撞磨损研究主要是通过理论和实验分析碰撞磨损机理,并提出相对应的碰撞磨损模型。由于颗粒属性、壁面材料属性、颗粒运动参数以及研究分析方法的差异,磨损模型多种多样。早在1995年,Meng和Ludema[41]就通过查阅大量文献,归纳总结了较为合理、较为完善的28种磨损模型,共涉及33个影响磨损的变量。平均每个模型包含5个不同的变量值,且不存在一个模型将所有影响磨损的因素都涵盖。随着磨损研究的发展,近20年来研究人员也提出了一些新的磨损模型。
目前,已存在的磨损模型主要可以分为两大类:①基于理论机理假设、分析推导和实验研究相结合的半经验磨损模型;②根据实验分析所获得的经验磨损模型。其中根据磨损材料性质的不同,半经验磨损模型又可以分为塑性材料磨损模型和脆性材料磨损模型。由于课题研究中使用的皆为塑性材料,因此下面分别对具有代表性的塑性材料磨损模型进行介绍。
(1)半经验磨损模型
塑性材料的磨损过程极其复杂,该过程中包含了颗粒对表面的切削作用、材料表面的塑性变形、颗粒破碎的二次冲蚀磨损等不同的磨损破坏部分,因此目前对塑性材料的磨损机理并未有一个统一的论断。但是在塑性材料的磨损研究中,为了深入了解磨损的本质,研究人员基于一些磨损机理假设推导出了大量磨损计算模型。
Finnie[42]基于塑性材料的微切削原理提出了塑性材料磨损的首个计算模型,对壁面材料损失的体积进行计算。随后,他结合实验结果[43],对该模型进行了改进[43]。具体公式如下:

式中 EV——表面材料损失的体积;
mp——单个颗粒质量;
σf——流动应力;
Up——颗粒碰撞速度;
hc——切削深度;
θ1——碰撞角度。
虽然模型的预测结果与一些实验结果相吻合,但是该模型还是存在较大的不足之处。它不适用于颗粒碰撞角度为90°的工况,低估了大角度碰撞时材料的磨损,高估了小角度碰撞时材料的磨损。同时,在该模型中Finnie将颗粒速度的指数值预测为2,这与很多实验结果不是很一致。
Bitter[44,45]基于颗粒冲蚀的微切削机理和变形磨损理论,提出了一种适合所有碰撞角度的磨损模型。他认为材料的磨损主要由切削磨损和变形磨损共同作用导致,当碰撞角度较小时,切削磨损占主导,而当碰撞角度较大时,变形磨损起决定作用。虽然他的模型与实验结果符合很好,但是由于公式的复杂性限制了其使用。
变形磨损:

切削磨损:

式中 Mp——颗粒总质量;
ξ1——变形磨损因子;
ξ2——切削磨损因子;
K、K1、K2和K3——常数。
随后,Neilson等人[46]通过开展一系列气固两相流实验对该模型进行了简化,提高了其实用性。简化模型如下:

式中 Etotal——总磨损量;
up1——碰撞前颗粒速度的法向分量;
vp1——碰撞前颗粒速度的切向分量;
θa ——vp1为0时的碰撞角度。
Sheldon等人[47]基于单个颗粒碰撞的压痕损伤理论和能量平衡理论,提出了一个包含变形磨损和切削磨损的磨损模型,如下所示:

式中 dp——颗粒直径;
ρp——颗粒密度;
HVw——目标材料的维氏硬度。
Tilly[48]基于高速摄影技术和电子显微技术对颗粒的碰撞磨损开展研究,提出了双阶段碰撞磨损理论。第一阶段为颗粒碰撞材料表面并对其产生切削磨损;第二阶段为第一阶段碰撞过程中颗粒破裂出的碎片对材料表面造成的二次碰撞磨损。材料表面的总磨损量为两个阶段磨损之和。如

式中 E1,E2——第一阶段和第二阶段的碰撞磨损量;
,
——第一阶段和第二阶段的磨损最大值;
Ur——相对速度;
Up0——起始碰撞速度;
dp0——产生磨损的最小颗粒直径;
Fdv——一定条件下的颗粒破裂程度。
Huchings等人[49]基于薄片式磨损机理提出了球形颗粒法向碰撞的磨损模型。该模型引入临界塑性应变来判断材料的磨损程度,具体如下:

式中 ER——单个颗粒的碰撞磨损率(表面材料磨损量/碰撞颗粒质量);
a——塑性变形压痕的体积分数;
ρw——目标材料的密度;
σpf——塑性流动应力常量;
δc——临界应变;
HBw——目标材料的布氏硬度。
(2)经验磨损模型
由于磨损机理的复杂性,越来越多的研究人员致力于从实验中总结归纳出颗粒碰撞的磨损模型,而不是从机理出发对磨损的细节进行分析。
Tabakoff等人[50]开展了大量煤灰颗粒对金属壁面的碰撞磨损实验,提出了包含碰撞速度和角度等参数的磨损经验方程,如下所示:

式中 θb——发生最大磨损时的碰撞角度;
C——常数(当θ1≤3θb时,值为1;当θ1>3θb时,值为0)。
美国磨损与腐蚀研究中心(E/CRC)学者[51]通过对碳钢和铝的大量磨损测试,提出了包括碰撞速度、碰撞角度、材料的布氏硬度以及颗粒的形状等多参数的磨损方程。该磨损方程是目前使用最为广泛的磨损模型之一,很多国内外研究者都采用它来计算颗粒对壁面的磨损。

式中 C——常数,取决于目标材料的布氏硬度,表达式为:

Fs——颗粒形状因子,当颗粒为圆形时取0.2,半圆形时取0.5,尖锐形时取1;
θ0,a1,a2,a3,a4,a5和w——磨损公式的经验常数,具体数值见表1-1。
表1-1 Mclauary磨损模型的经验常数值

该中心人员[52,53]在上述磨损模型的基础上,通过实验分析对碰撞角度函数以及速度指数进行了修改(改为2.41),以适用于铬镍铁合金718等材料的磨损预测。

挪威商立恩威验证公司(DNV)的研究人员[54]基于一系列的实验和一个磨损模型基本形式提出了一个适合于多种常用材料的磨损模型,见式(1-23)和式(1-24)。

式中 EM——目标材料损失的质量;
K和n——常数,取决于表面材料,见表1-2;
ai——经验参数,见表1-3。
表1-2 式(1-23)中的常数值

表1-3 式(1-24)中的经验常数值

Oka等人[55,56]以大量磨损实验和几个重要参数(颗粒的碰撞速度、碰撞角度、目标材料硬度、颗粒粒性)为基础,也提出了一个磨损预测方程用于铝、铜、碳钢等材料的磨损分析。

式中 ERV——体积磨损率(表面材料磨损体积/碰撞颗粒质量);
ERV(90)——碰撞角度为90°时的体积磨损率;
n1和n2——取决于颗粒材料的硬度和其他颗粒碰撞条件,n1,,b1和b2值见表1-4;
K,k1,k3——由颗粒的特性决定,具体参数值见表1-5;
k2——由材料的硬度和特性决定,具体参数值见表1-5;
U0——参考速度,具体参数值见表1-5;
d0——参考颗粒直径,具体参数值见表1-5;
a1和a2——表面材料的载荷松弛系数。
表1-4 n1和n2中的常数值

表1-5 式(1-27)中的常数值

在磨损模型的研究领域,还有很多研究者分别针对影响磨损的各个因素开展大量的实验研究。Smeltzer[57,58]、Laitone[59,60]和Burnet[61]等人针对碰撞磨损与颗粒速度之间的指数关系值进行了研究分析;Sheldon[62]分析了不同目标材料下,颗粒的碰撞角度与碰撞磨损之间的关系;Finnie[63]、Levy[64]和Foley[65]等人研究了目标材料对颗粒碰撞磨损的影响;Liebhard[66]、Finnie[67]等人研究了颗粒的属性等因素对颗粒碰撞磨损的影响。
各磨损模型的对比见表1-6,虽然磨损模型都或多或少地存在一些局限性,但是在实际工业过程设备的磨损研究过程中,合适的磨损模型不仅能够精确预测磨损信息,同时还能够减少时间和资源的消耗。
表1-6 各磨损模型的对比

(续)

2.阀门内部两相流动及磨损研究
Tong等人[68]基于两相流理论和颗粒动力学理论提出了一种L型阀门的流体动力学模型。该模型能够基于气体和颗粒的性质、阀门的结构尺寸以及工况条件求得颗粒流量、气体压降、气体流量等流场信息。Yang等人[69]采用多分辨率小波变换对L型阀门直管段和水平管段的压力信号进行实验分析,研究了充气速率、充气位置、气体速度和颗粒粒径分布等参数对压力波动以及两相流态的影响。Chan[70]首次采用正电子发射粒子跟踪技术对L型阀门的流动性能进行实验研究,分析了阀门下游有无负载对颗粒的运动轨迹及质量流量的影响。
颜海霞[71]对气力输送系统出料阀前后三维管道中的气固两相流动进行了数值模拟,研究不同阀门开度、颗粒粒径及颗粒进入流场位置对颗粒运动轨迹的影响,并获得了不同阀门开度情况下管道壁面的磨损分布规律。王蓓[72]通过数值模拟软件Fluent分析了不同开度、不同流速和不同颗粒大小工况下,调节阀内部携沙天然气两相流动状态,提出了冲蚀角、流动速度、颗粒大小三个主要因素对调节阀受携沙天然气冲蚀的影响规律。林哲等人[73]对平行双闸板闸阀内颗粒碰撞所导致的磨损开展了数值计算分析,提出了阀门关键密封面磨损预测公式。王国荣等[74]采用CFD方法对MPD节流阀中液固两相流湍流流动进行了研究,结果表明,MPD节流阀内壁的冲蚀磨损主要发生在阀芯末端,阀门内壁面磨损主要取决于钻井液的流速及固体质量流量。朱红钧等人[75]采用数值模拟方法研究了针型阀在气固两相工况下的磨损特性,考察了入口速度、阀门开度和阀门口径、颗粒浓度、颗粒直径和颗粒相浓度的影响,指出阀芯尖端部位为高磨损区域,且颗粒粒径对磨损影响显著。刘波等人[76]采用数值计算方法对蝶阀内部磨损开展了研究,详细讨论了入口压力和阀门开启角度等因素的影响。结果表明,随着入口压力的增加,湍流强度和冲蚀磨损都会增加;湍流强度和颗粒冲蚀磨损随着阀门开度的减小而减小。
Nokleberg等[77]采用CFD和磨损实验相结合的方法研究了减压阀的磨损,结果表明,模拟预测值和实验值具有很好的一致性。Wallace等人[78]采用CFD和实验相结合的方法研究了水泥浆对阀门部件的磨损,研究中分别对阀门结构的简化模型和原模型(节流阀)的磨损进行了分析,指出数值模拟方法能够得到合理的磨损分布,但是磨损程度较实验值小很多。Mazur等人[79]采用CFD技术对蒸汽轮机的旁通阀内颗粒磨损进行了研究,结果表明,通过改进阀门结构改变了颗粒的轨迹和碰撞角度,能够使阀门的磨损急剧减小。Wang等人[80]采用CFD-DPM数值模拟方法对压力钻井中的节流阀磨损进行了计算,分析了节流阀内部磨损分布特性,在此基础上使用响应面方法对阀门结构进行了优化设计,降低了节流阀内部30.2%的磨损量。
3.曲折管道内两相流动及磨损研究
樊建人等人[81-84]提出了几种新型的弯管抗磨结构,并通过开展数值模拟和实验研究,分析新结构的抗磨机理。兰惠清等人[85]提出了一种考虑了气固两相混合速度和气体压力的磨损模型,开展了不同工况情况下弯管的磨损模拟,对比分析了高压和低压工况下颗粒速度对磨损速率的影响规律。林哲等[86,87]以前后壁面不等高的凹槽结构为研究对象,开展了内部流道磨损数值模拟和实验研究,考察了高度差及放置倾斜度的变化对凹槽结构后壁面的磨损形貌和最大磨损率的影响。赵永志等人[88]采用CFD-DEM数值模拟方法对三维弯管气固两相流致磨损开展了研究,指出了颗粒体积分数大于1%时应当考虑气体和颗粒间的双相耦合效应。
Tolle[89]等通过大量实验研究了沙粒速度、颗粒大小以及质量流量对管道部件磨损的影响,并且还分析了管道部件的结构、材料、内涂层对磨损的影响。Mills[90,91]针对弯管开展了大量的实验研究,考察了不同工况条件下的磨损分布演化规律。Bourgoyne[92]分析了沙粒对管道部件磨损失效作用机理,他对比了不同管道部件结构的磨损剧烈程度,同时还研究了流体速度、流体性质以及沙粒的浓度对磨损的作用效果。E/CRC的研究者[93-98]等采用欧拉-拉格朗日两相耦合技术,结合CFD磨损预测程序分析计算了180°弯管、90°弯管、三通管、突扩管以及突缩管等结构的磨损情况,并与大量实验结果进行对比分析。Russell[99]等人对不同材质的90°直角弯管开展了大量磨损测试,实验中考察了两种颗粒浓度和多种流量条件的影响,测试了整体重量损失以及样品表面的壁面磨损深度。Habib等人[100]采用CFD方法研究了稀气固两相流动对突缩管内磨损的影响,结果表明两段管道的结合位置磨损最为严重,同时也提出了不同粒径下磨损的临界速度。Wong等人[101]采用数值模拟和实验相结合的方法对竖直放置理想凹槽结构的磨损状况进行了研究分析,结果表明凹槽下游前缘部分的磨损最为严重。Duarte等人[102]采用了单相耦合、双相耦合和多相耦合的数值模拟方法对弯管磨损开展研究,指出在低质量流量工况条件下,不可忽略颗粒间碰撞对磨损的影响。
由上述可知,国内外已在磨损机理、阀门及一些曲折流道结构内部含固两相流动及流致磨损等方面开展了大量的研究工作,并得到了一些有益的结果。但同时也可以看到,针对流程阀门的研究仍然较少,研究对象、研究内容和研究方法等方面都有待于进一步深入拓展,从而更全面地揭示流程阀门在含固两相工况下的流体动力学特性以及流致磨损机理,进而为流程输送工程服务。
综上所述,本书以流程阀门为对象,围绕单相及含固两相等不同介质的要求,建立了适宜的流程阀门流体动力学特性及含固两相流致磨损计算方法,在此基础上,针对多种流程阀门结构开展了内部流动分析、调控性能预测及流致磨损分析,获得了大量有价值的成果,为流程阀门的设计以及可靠运行提供了理论和技术支撑。