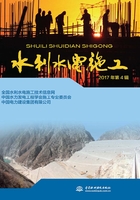
振动碾无人驾驶技术的研发与工程应用
韩 兴/中国水利水电第五工程局有限公司
【摘 要】 堆石坝碾压施工的常规做法是驾驶员在车上操作,施工中存在控制精度不高、施工效率低、质量难以保证、强烈振动环境影响操作人员健康等问题。为提高控制精度,确保施工质量,减小劳动强度及提高施工效率,本文依托长河坝大坝工程,论述了国内首次研制的无人驾驶振动碾技术,在施工中实现了无人驾驶振动碾机群的自动化、信息化与智能化一体控制的研发过程、原理及应用成果。
【关键词】 堆石坝 振动碾 无人驾驶 精确碾压 智能控制 应用成果
1 概述
长河坝水电站位于四川省甘孜藏族自治州康定县境内,为大渡河干流水电梯级开发的第10级电站。该电站水库正常蓄水位1690.00m,总库容为10.75亿m3,电站总装机容量为2600MW。拦河大坝为砾石土直心墙堆石坝,最大坝高240m,且修建在60~70m的深厚覆盖层之上,是国内外建在覆盖层上的最高坝。
大坝填筑总量约3417万m3,受“4·20”芦山地震等多种因素的影响,填筑开始时间较合同时间滞后3个月,工程首个度汛工期尤为紧张,而统计大坝度汛前单层最大碾压面积达17.23万m2,碾压设备投入量要求巨大。碾压设备配置与管理是确保施工质量与保障进度履约的关键。为确保施工质量,工程施工前通过生产性碾压试验最终确定的各种坝料的碾压参数见表1。
表1 长河坝水电站大坝各料种填筑碾压参数

长河坝大坝工程采用了GPG数字化大坝碾压实时监控,对施工全过程进行监测和预警控制,该系统具有全方位实时监控各项碾压参数(碾压遍数、速度、激振力、碾压厚度)的功能,能够有效避免漏碾、欠压现象。同时,系统设计有人工控制碾压超速行驶报警功能,使超速碾压可有效控制。但在施工中监测发现,人工驾驶控制振动碾碾压平均速度仅为2km/h,较设计行驶速度偏低20%,且人工控制搭接宽度控制精度较差,漏碾返工或搭接宽度过大等影响大坝施工质量和施工降效等问题。为使碾压施工实现精准控制,确保施工质量,提高施工效率,使振动碾驾驶员从单调、乏味、高强度的碾压作业中解脱出来,我们研究开发了振动碾机身电气及液压自动控制系统,集成应用卫星导航定位、状态监测与反馈控制、超声波环境感知等技术,实现了振动碾压机械的无人驾驶精确碾压机群作业。
2 振动碾自动控制系统方案
2.1 系统架构
振动碾自动控制系统是主要由工控机、遥控器、车载控制器形成的程序控制系统;以实现行驶、振动、转向、制动等自动控制的振动碾机身控制系统;以GPS定位、角度编码器、倾角传感器等形成的导航与姿态补偿系;以及加装在车身的超声波传感器形成的环境识别与自动避让系统等组成。系统设计架构如图1所示。
2.2 程序控制系统
工控机作为改造电控系统中的控制终端,主要负责振动碾工作状态的实时监控和系统工作参数的设定。车载控制器是振动碾改造电控系统的核心控制器,主要功能分为信号采集及处理功能、逻辑运算及路径控制功能和输出驱动功能。根据工控机和遥控器的指令实现振动碾的行驶与振动控制。同时,车载控制器还负责GPS数据和传感器数据的采集及处理,并结合工控机设定的工作参数进行作业路径的规划和自动路径跟踪。

图1 振动碾自动控制系统设计架构图
路径规划采用的方式为:设定工作区域的四个角点(如图2中A、B、C、D点所示),根据这四个角点来确定作业区域的边界;然后设定当前或最近的角点作为起点(图2中设定A为起点),再设定车身前进方向的角点来确定作业的方向(图2中设定从A至B)。完成设定后,控制器会自动根据设定的起点和方向来计算直线行驶的航向,并计算出所需碾压的轨迹数量(图2中轨迹数为④),待启动自动程序后控制器会根据所计算的航向完成设定区域内所需碾压轨迹的自动碾压作业。

图2 程序控制系统完成的路径规划图(碾压2遍)
设计的无线遥控器采用主副配置形式。主遥控器为智能化程度较高的集成遥控器,该遥控器能实现对至少4台振动碾机群的自动控制。副遥控器是非智能的人工控制遥控器,用以避免智能程度系统故障对作业过程的安全风险,可实现振动碾的紧急制动功能。
2.3 机身控制系统
振动碾机身控制系统的主要工作原理为:对原车的液压转向系统进行改造,在原车转向器部分增加电磁截止阀来实现原车转向液压系统与改造转向液压系统的切换。截止阀不通电时,转向泵输出油液经液压转向器到转向油缸,即为原车的人工转向方式。截止阀通电时,转向泵输出油液经比例节流阀和电磁换向阀与平衡阀后到转向油缸。通过控制比例节流阀线圈的电流,可以改变比例阀的开度,实现转向速度的调节。通过控制电磁换向阀两端不同的线圈通电,控制转向油缸的伸缩,实现转向方向的自动控制。转向角度由安装在车身铰接点的角度编码器进行采集,实现前后车架之间车身转角的反馈。
将原来的手动操纵手柄改为电控手柄。自动控制器采集手柄不同位置输出的模拟量值来进行前进/后退的判断与行驶速度的控制。通过控制加装的行驶电控比例阀两端线圈的电流,改变比例阀的开度,改变泵的斜盘角度和泵的输出排量,实现了振动碾自动行驶速度的控制。通过控制比例阀两端不同的线圈通电,改变了泵的液流输出方向,从而实现了振动碾行驶方向的控制。
2.4 导航与姿态补偿系统
导航与姿态补偿系统是实现振动碾自动行驶和自动转向以及控制精度的关键。要实现自动导航,振动碾的位置和行驶方向这两个信息的获取需要借助于GPS位置接收机和GPS航向接收机。
角度编码器:由于振动碾为铰接转向形式,在实现振动碾自动作业路线跟踪控制的过程中,需要采集钢轮与车身之间的转角信息来检测车身的位姿。转角由安装在车身铰接点的角度编码器进行采集,角度编码器输出信号通过CAN总线输入到控制器。
倾斜传感器:为解决振动碾自动作业过程中,工作路面状况恶劣,车身倾斜导致的GPS定位位置与车身实际位置偏移。在振动钢轮一侧增加设计安装了倾角传感器,提高了振动碾自动作业的精度。
2.5 环境识别与自动避让系统
系统设计了环境识别与自动避让系统,利用超声波传感器检测车身周围是否有人或物体靠近,当在一定范围内检测到有人或物体靠近时,振动碾能自动停止作业,待物体远离后继续完成作业。在振动碾前后方各均匀布置了三个超声波传感器。
3 现场的技术改进
振动碾经过首次改造完成后,经生产试验,发现的问题如下:
(1)振动碾在静碾状态,可基本完成完整的行驶、转向功能,一般偏差值可控制在50cm内,精度尚不能满足生产要求。
(2)静碾行驶试验过程中最大直线偏差达197cm,振动碾在行驶过程中位置出现偏差时,存在纠偏不及时甚至不能纠偏回位的情况。
(3)振动碾在激振状态行驶过程偏差过大,不能完成完整的碾压作业。
通过现场试验,验证了振动碾技改的自动控制系统基本实现了振动碾自动行驶、转向的自动控制,但应用的控制精度及纠偏方式亟待解决,经讨论研究提出的解决方案如下。
3.1 定位设备的安装位置调整
1.原方案定位设备的安装及程序计算方式
原方案GPS导航定位系统安装于振动碾驾驶室顶部,在其顶部一前一后布置,两个定位设备的点径距124cm。自动控制程序的定位及航向是以振轮为基准的,原方案定位设备测量的定位坐标为驾驶室坐标需转换为钢轮坐标,转换公式见式(1),对应振轮的航向也许利用驾驶室航向进行转换。

式中:x0,y0为定位设备测量的原始坐标值;x1,y1为转换后的钢轮坐标值;W为车身宽度的1/2;L为从铰接点到钢轮中心的直线距离;ϕ为钢轮的侧倾角;θ为钢轮的俯仰角;Ψ为钢轮的航向角。
2.定位设备的安装及程序调整方案
为进一步提高设备碾压精度,对定位设备的安装位置进行调整改进,直接将定位设备安装于振动碾的振轮框架上。
方案调整后两套定位设备安装于振动碾振轮框架平台两侧,水平径距180cm相比原驾驶室顶的安装距离增长近60cm,可有效降低定位系统本身偏差对航向定位的影响,从而提高作业精度。改进后定位设备测量的航向角直接为钢轮航向角,所以不需要进行转换。测量的定位坐标只需进行倾角补偿即可。较原方案更直接减少了中间影响因素,提高了反应时间。
3.2 定位设备的选型
考虑到定位设备的精度会影响自动作业的控制精度,分别选取N71J型和SPS型两套定位设备进行测试。对比两套定位设备输出的坐标曲线,可以看出虽然两套设备输出坐标都趋近于线性,而SPS型设备输出坐标其线性度明显比N71J型设备输出坐标的线性度要好,如图3和图4所示。

图3 SPS型定位设备输出坐标曲线

图4 N71J型定位设备输出坐标曲线
自动控制程序控制静碾手工测量偏差试验获得N71J型定位设备直线偏差可控制在±30cm以内,而SPS型设备偏差可控制在±20cm以内;在振碾状态下N71J型定位设备直线偏差达±40~50cm,而SPS型设备偏差可控制在±30cm以内。采用SPS型设备具有更高的作业精度。
3.3 纠偏程序的调整
1.原方案纠偏控制原理
为确保碾压过程及时进行纠偏,原方案程序中设计有路径跟踪控制程序,其纠偏原理为:根据GPS设备反馈的位置坐标来计算振动碾的横向偏差,并结合当前航向与直线航向的航向偏差来动态调整振动碾的转向角度,实现对设定直线的跟踪。
2.调整后纠偏控制程序
新的路径控制方案采用基于航向的直线跟踪控制算法:根据GPS设备反馈的位置坐标来预估振动碾所需要的航向,并与测得的车身实时航向进行比较,计算航向误差。根据航向误差来动态调整振动碾的转向角度,实现对设定直线的跟踪。
基于航向的直线跟踪算法没有直接计算横向误差,而是将横向误差的计算转换为所需航向的计算,降低了算法的误差敏感度,提高了自动作业的控制精度。
4 工程应用
首台振动碾完成技术改造后,现场进行了应用试验,典型的试验场地为25m×8m的长方形区域,场地表面平整度±30cm,振动碾分4条轨迹碾压,沿每条轨迹标准线每5m布置一个偏差测点,偏差值偏向上游为负,偏向下游为正。试验设定碾压速度2.7km/h,静碾2遍+振碾4遍,主要试验偏差值记录见表2。
表2 无人驾驶振动碾自动碾压偏差值记录表单位:cm

续表

试验结果如图5所示。

图5 振动碾前进作业速度-时间关系曲线图
实践证明,振动碾自动控制碾压直线偏差值基本控制在±10cm,最大偏差值不超过30cm,碾压速度偏差控制在±0.1km/h,考虑一定的搭接宽度,一次碾压合格率完全能够满足质量要求。首台振动碾在长河坝电站进行了长达7个月的实践应用,在运行过程中,对振动碾的程序又进行了系列改进:
(1)新增了自动寻址功能。振动碾可在自动记录自当前位置到作业起点的作业情况。
(2)作业区域新增坐标系选择功能。通过程序设定建立世界坐标系与施工坐标系的换算关系,可实现不同工地坐标的录入。
(3)新增循环次数的设定功能。可实现对各条碾压车道的连续碾压遍数设定。
(4)系统增设了安全自锁功能。当振动碾机身出现油料不足或机械故障故障时,振动碾会自动停止作业。
为进一步扩大实用效果,后续又改造了4台振动碾,实现了5台无人驾驶振动碾的机群化作业。通过近5000h的应用,成效如下:
1)质量控制:避免漏压、欠压、超压,确保一次碾压合格率(均值97.1%)。
2)施工效率:对比人工驾驶作业施工效率提高约10.6%,同时可缩短间歇时间约20%。
3)安全风险:可降低人为影响和夜间施工安全风险。
4)劳动保护:可有效减少振动环境下对人体损伤。
5 结语
振动碾无人驾驶技术首次实现了施工机械无人驾驶,实现了振动碾行驶速度、碾压遍数、搭接宽度等的精确控制,可采用导入测量坐标或机身定位完成作业区域的设定,通过显示控制器实现作业区域、作业环境、施工参数及行驶状态等的实时显示与数据记录。无人驾驶系统充分考虑到振动碾机身(油料不足或机械故障)及外部环境影响等影响作业安全因素,实现了环境自动识别与自动制动、避让。振动碾无人驾驶技术的实现,避免了强烈振动环境对操作人员的伤害,保护了操作人员的健康。该技术目前已获得相应专利,具有大中型土石方工程碾压的通用性,推动了施工机械装备的技术进步,经济和社会效益显著,具有较广阔的推广应用前景。