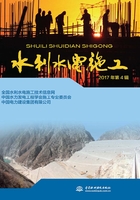
300m级高心墙堆石坝施工关键技术研究与应用
吴高见 樊 鹏 韩 兴/中国水利水电第五工程局有限公司
【摘 要】 随着高堆石坝向300m级跨越,所面临的防渗安全备受关注。对于深厚覆盖层、陡窄河谷条件下的高堆石坝,保证地基处理、防渗体系、坝体填筑的施工质量显得尤为重要。长河坝水电站大坝为砾石土心墙堆石坝,建于深厚覆盖层上,坝体高240m,覆盖层和坝体的总高度293m,坝体高度大,地震设防烈度高达Ⅸ度,河谷陡窄,坝体变形稳定和渗流稳定控制难度大,设计指标及施工质量标准高。项目开展了系统、深入的科学研究,取得了丰硕的创新成果。本文简要介绍长河坝水电站大坝工程特点与施工难点,叙述大坝填筑施工过程中采取的主要关键技术,对类似的工程施工具有很好的借鉴意义。
【关键词】 心墙堆石坝 施工 关键技术 新工艺
1 工程概况
长河坝水电站位于大渡河干流上游,是大渡河水电规划“三库22级”的第10级电站。工程枢纽建筑物由砾石土直心墙堆石坝、左岸引水发电系统和右岸泄洪洞系统组成。水库总库容10.75亿m3,有效库容4.15亿m3。电站总装机容量2600MW。
拦河大坝为砾石土直心墙堆石坝,坝顶高程1697.00m,最大坝高240.0m,大坝心墙底高程1457.00m,坝顶宽度16.0m,上、下游坝坡1∶2。大坝总填筑量3417万m3。坝基覆盖层设两道混凝土防渗墙,上游副墙厚1.2m,主墙厚1.4m。
2 工程特点与施工难点
2.1 工程特点
长河坝水电站大坝施工条件复杂,具有“两高、一大、一深、一窄”的工程特点。“两高”为:坝高240m,底部60~70m覆盖层,总高近300m;地震烈度高,大坝地处8级地震地区,抗震设防烈度为Ⅸ度。“一大”即填筑规模大,大坝填筑总量达3417万m3。“一深”为深覆盖层,坝基覆盖层厚度60~70m,局部达79.3m。“一窄”为陡窄河谷,河谷宽高比仅2.09,岸坡坡度70°以上。河谷拱效应和蓄水水位陡涨效应显著,水库初期蓄水期无控蓄能力,初导洞下闸后2d内坝前水位快速上升约72m。长河坝大坝是目前国内外建在深厚覆盖层上的最高心墙堆石坝,施工极具挑战性。
2.2 施工难点
1.设计指标及施工质量标准高
本工程是超现行设计及施工规范标准的大坝(现行的设计及施工规范中均明确对于高于200m以上的高坝应进行专项研究、专题论证),质量要求高。其中,砾石土心墙料压实度以全料压实度和细料压实度进行双控制,全料的压实度应不低于0.97(击实功2688kJ/m3);细料压实度不低于1.00(击实功592kJ/m3),经碾压试验获取了心墙土料碾压参数为:26t凸块碾,静碾2遍+振碾12遍。反滤料技术要求高,设计填筑4种反滤料,设计指标与要求各异,传统掺配工艺控制精度低,掺配质量不易保障。
2.天然砾石土料场成因复杂、均匀性差
心墙土料场土料天然含水率在1.7%~19.3%之间,平均为9.8%,粒径大于5mm颗粒(以下简称P5)含量变化范围7%~90%,平均为49.1%,小于0.075mm含量变化范围8%~64%,平均为30.4%,小于0.005mm变化范围1.6%~26.3%,平均为10.3%,料场超径(大于150mm)平均含量约5.6%,超径含量高。土料各项检测指标变化大、空间分布均一性差,料场天然土料级配指标大多难以满足设计要求,无法直接满足心墙填筑质量及规模化施工要求,需要进行土料超径剔除、不均匀土料的掺配及含水率的调整等多道制备工序,土料开采制备难度大,施工质量控制环节多。
3.堆石料场岩石坚硬、剥采困难
本工程规划了两个石料场,大坝上游的响水沟石料场供应大坝上游堆石、过渡料,下游江嘴石料场供应大坝下游堆石、过渡料及反滤料加工系统原料。料场岩性以花岗岩、闪长岩为主,岩石饱和抗压强度达190MPa,岩石强度高,工程前期进行了大量的过渡料爆破试验,在炸药单耗达2.5kg/m3的情况下,仍不能获得质量稳定的过渡料。
3 施工关键技术
结合长河坝水电站大坝工程实际特点和施工难点进行了大量现场试验、理论分析与实践应用研究,并注重新技术和新设备的研发,分别开展了复杂条件下心墙土料的改性制备工艺、土石坝精细化的系列新设备、基于信息技术的质量检测和控制新方法、生态环保的绿色施工等关键技术的研究,提升超高堆石坝施工技术能力。
3.1 心墙土料改性的成套施工新工艺
在传统料场勘察方法基础上,针对长河坝水电站汤坝砾石土料场空间分布极度不均匀的问题,采用基于P5含量等值线的料场勘察方法,将料场中同一地质成因的土料在空间上进行P5含量分区分级,查明了偏粗料、合格料、偏细料分布特征及其分区储量,为料场合理开采利用提供了充分的依据,取得了良好的效果。
为确保土料上坝填筑质量,通过工艺比选及试验,选择用于矿山及骨料生产系统的棒条式振动给料机经调整筛条长度、间距作为超径(大于150mm)剔除设备,并根据工程强度要求配套建设了5套钢筋混凝土结构的筛分楼。筛分楼设有箱式结构的受料斗、筛分设备安装层以及满足装载机出料的出料层,该筛分系统筛余料中有用料平均比例仅为0.2%,透筛率高,单台产能可达670t/h。
对于粗细料,以P5作为控制指标进行掺配,以提高土料利用率。研究应用公路工程的稳定土搅拌系统作为土料掺混的机械制备系统,通过定量给料、计量输送和强制搅拌掺混,实现掺配土料的自动配料、均匀掺混的生产工艺。在设备选型基础上,针对本工程土料粒径大、黏性高、含水高的特点对成套设备进行了改进,调整了搅拌叶片间距、配料仓的仓壁坡度,并完成了一定场次的测试试验。应用表明掺拌生产均匀性好,可有效解决传统工艺掺配存在的掺配均匀性差、黏土结块等问题,实际产能可达700t/h。
依托毛尔盖大坝工程,通过跟踪检测与计算,研发了均匀布坑、畦田灌水、渗透扩散、计时闷存的砾石土料含水量调整方法,保证了大坝心墙土料最优含水率要求。研制了移动式自动加水装置,可实现土料连续定量均匀加水。针对长河坝工程高含水的土料,研究采用分层翻晒工艺调整含水率,并研制了适用于推土机的快速翻晒装置。
在长河坝工程中,应用上述技术,综合利用69.5万m3的料场偏粗、偏细料及31.6万m3高含水土料,料场开采与坝面填筑数量比为1.41,远小于规范推荐的料场规划与坝料填筑的数量比例(2~2.5),土料开采利用率大幅提高,从而取消了新联料场,减少耕地占用51万m2,同时保证了心墙料物理力学性能的均一性。
3.2 反滤料精确掺配工艺研究
依托人工骨料系统,通过进行反滤料掺配工艺试验、基本技术参数采集、自动化控制系统编程等确定了反滤料精确掺配生产工艺,工艺原理为:砂、小石、中石、大石在胶带运输机上依次下料平铺,根据反滤料设计级配对各粒径骨料掺配含量确定下料流量,通过首先调整电动弧门开口大小的方式控制下料流量范围,再由中控室远程控制变频器振动给料机精确控制,由给料机下的皮带秤在线反馈流量,通过工艺性试验现场采集参数进行自动化数据编程,从而实现反滤料的自动化掺配。
利用电子皮带秤针对反滤料在指定频率的下料速度稳定性行了测试,评价振动给料机变频精度,给料变频技术能将精度控制在1%~3%,较传统工艺控制精度提高3%~5%以上。
3.3 高标准过渡料机械破碎加工技术
过渡料机械破碎加工技术是通过对合理单耗的爆破原料再进行二级破碎,粗碎控制最大粒径、中碎调整级配的过渡料制备工艺。该技术较爆破直采法产出的过渡料级配更稳定,并可有效解决硬岩、偏硬岩条件下过渡料爆破直采难度大、利用率低等问题。
长河坝工程料场岩石强度高,通过应用过渡料机械破碎加工技术对料场爆破的堆石料进行二级破碎加工,经过颚式破碎机粗碎后,可有效控制最大粒径,50%的破碎料再经圆锥式破碎机中碎后经胶带机混合获得了质量稳定的过渡料。
3.4 精细化的土石坝施工新设备、新技术
1.高陡边坡盖板混凝土反轨液压爬模的研制
针对高陡、薄层混凝土盖板施工困难问题,研发了边坡混凝浇筑反轨液压爬模及自动控制系统;通过研制的轨道实现液压爬模的着力与支撑;以反向托轮控制混凝土的浮托力;实现侧向模板的自动升降和模板长度方向的调节。自爬式反轨液压爬模在长河坝工程边坡盖板混凝土施工中投入了生产应用,爬模能够实现自动爬升,速度可达80cm/h。利用反轨系统完全能够克服混凝土浮托力,混凝土浇筑质量良好,仓面平整度控制在±5mm以内。
2.盖板混凝土基面高塑性黏土机械化喷涂技术
为保证高塑性黏土和混凝土压板结合效果,需在压板表面涂刷3~5mm泥浆。在类似工程中,泥浆通常采用人工涂刷,施工效率低,且厚度不易保证,均匀性差。
为了改善传统工艺的不足,研究开发了机械喷涂工艺,泥浆在压缩空气作用下,经过滤输送至喷头形成有压流达到喷涂黏附的效果。以德国制造的瓦格纳尔PC喷涂机作为喷涂设备,结合多次现场工艺试验,确定了泥浆可喷配比及浆液相对密度。制定的喷涂工艺流程为:泥浆制备→润管→注浆→试喷→正式喷涂至设计厚度。
盖板泥浆喷涂工艺是土石坝高塑性黏土填筑中混凝土盖板基面传统泥浆涂刷工艺的革新,工艺设备安装简便、快捷,操作方便,施工效率高,质量效果好。检测机械喷涂厚度分布3.7~4.0mm,平均厚度3.87mm,离散系数仅为0.01。统计机械喷涂作业效率可达1m2/min,较人工涂刷工艺提高工效2倍以上。
3.双料摊铺工艺
为解决常规土石坝土-砂分界面“先砂后土”法施工存在的料种相互侵占、填筑尺寸不规范、施工效率低等问题。研发了心墙区界面双料摊铺器,实现了大坝心墙料与反滤料、不同反滤料分界面摊铺一次精确成型,该装置结构合理、操作简单,界面坡比可调,形体准确,有效提高了施工效率和摊铺质量。摊铺器是采用型钢和钢板加工而成的无底箱式结构。摊铺器中间设置料仓分隔钢板,分隔板在出料口以下的倾角与心墙设计坡比一致。双料铺后侧的出料口高度根据对应料种的碾压试验沉降率确定,出料口高度即为两种料的摊铺成型厚度。双料摊铺工艺可有效解决常规土石坝土-砂分界面“先砂后土”法施工存在的料种相互侵占、混杂、填筑尺寸不规范、施工效率低等问题。避免了传统工艺带来的分界区物料分离,提高了界面接合质量。
4.振动碾无人驾驶技术
在长河坝水电站大坝工程中,对碾压机械作业技术进行进一步深入系统研究,研发了振动碾压机械无人驾驶技术。开发了振动碾机身电气及液压控制系统、集成应用卫星导航定位、状态监测与反馈控制、超声波环境感知等技术,首次实现了振动碾的无人驾驶作业,精确控制碾压作业,提高了碾压质量和施工效率。
研发的振动碾机身电气及液压控制系统,由电气主控制器完成参数设定,就地控制器控制行走、转向、振动等状态,实现振动碾工作状态的自动控制。利用卫星定位导航技术实现机身位置、方向定位和路径控制,根据指定施工区域建仓规划,进行碾压路径自动设定及差异化调整。利用角度编码器、倾斜传感器等进行振动碾行驶状态、姿态的检测,实现了机身自动控制系统的补偿控制,提高作业精度。研发了振动碾显示控制器,进行碾压参数设定,实现作业区域、作业环境、施工参数及行驶状态等的实时显示。研究采用超声波环境感知系统,实现自动障碍避让,开发了低频段无线遥控应急装置,进一步提高了振动碾应急制动的可靠性。
首批5台无人驾驶的振动碾已成功应用于长河坝大坝施工,总运行时间超过5000h。应用成效:在质量控制上,可避免漏压、欠压,直线行走偏差±10cm以内,行走速度偏差0.1km/h,并有效控制超压现象,确保一次碾压合格率(均值约97.1%);在施工效率上,对比人工驾驶作业施工效率提高约10.6%,同时可缩短间歇时间,延长工作时间约20%;在安全风险控制上,可降低人为影响和夜间施工安全风险;在劳动保护上,可有效减少振动环境下对人体损伤,减少了人力资源的浪费。
5.坝料自动加水系统的研制
坝壳料加水采用坝外加水,利用已获国家专利的智能加水系统向运料车内自动加水。该系统与坝料计量称重系统有效绑定使用。系统能够有效保证加水量,且实现自动控制,结构简单、安全可靠、经济。系统通过检测车载无线射频卡自动识别地泵系统测得的该车坝料重量,计算出适宜加水量,并利用液体流量传感器及电磁阀控制水流开关,实现智能化加水。长河坝工程高峰监控车辆达272辆,系统能够有效保证加水量,且实现自动控制,结构简单、安全可靠。
3.5 基于信息技术的质量检测和控制新方法
1.车载移动实验室和砾石土含水率快速检测技术
研制了用于砾石土快速烘干的大型红外微波设备,在不破坏土体本身结构的情况下,实现了土样快速加热烘干,大幅度缩短了含水率检测时间。研发了由红外微波烘干设备、高精度流量计和其他测试计算设备组成的车载移动试验室,可在20min内完成土料含水率的快速测定,不仅使干密度的检测时间缩短了近7h,而且提高了试验检测的准确性。
根据大量的试验数据,论证确定砾石饱和面干含水率相对固定,据此提出了砾石饱和面干含水率测定替代法,通过对细料含水率的测定与加权计算,快速获得砾石土心墙料的含水率,检测时间比传统方法缩短了6~8h,效率提高了4倍。
2.基于三维激光扫描的堆石坝填筑体碾压密实质量检测技术
提出了基于三维扫描的堆石坝填筑压实度检测技术,通过采用改进ICP迭代法处理点云配准问题,比传统的ICP法迭代的精度和迭代效率均有所提高,精度提高10%~20%,时间缩短到10min左右;采用地面Delaunay三角网法对点云进行建模,其网格最接近真实地面起伏情况;采用碾压区域的栅格化检测技术,实现了对填筑面任意区域的质量检测,并且标记不合格区域并反馈给监测中心,用于指导及时的补充碾压。
3.图像筛级配检测技术
针对堆石坝坝料级配检验工作难度大、效率低及误差大等弊端,基于当代先进的无损检测理念,将数字图像处理技术融入坝料颗粒级配检验之中,同时结合人工智能和大数据等先进手段,开拓性地摸索出了一整套方便、快速且精准的坝料颗粒级配检验技术。基于坝料颗粒的分形尺度特征,以各种图像处理技术的运行可行性、效率及精度为标准,探究了以Matlab为平台,集小波去噪、对比度增强和Ostu阈值分割等于一体的坝料数字图像处理技术。通过颗粒尺寸分布数学模型描述坝料的级配分布特征,利用模型中的特征参数来反映坝料级配特征,实现了坝料级配的多维描述。基于大数据统计思想,通过叠加数个单位小尺度实现对大尺度的检验。同时,从侧面上实现了对坝料微米级别颗粒的检验,大大减少了工作量并提高了技术的可操作性。基于一系列人工智能算法,“迂回式”地对误差进行了规避,保证了检验的精度。此外,基于一定的软件平台,开发了坝料颗粒智能识别系统,进一步简化了操作,实现了级配检测程序化、自动化。
4.基于地基反力测试的车载压实质量检测方法
开展了基于地基反力测试的车载压实质量检测方法研究,在充分研究国际现有指标体系的基础上,从地基反力测试的原理和机制出发,结合信号分析处理方法确定实时检测指标,通过系列现场试验,验证了用峰值因素CF值来表征堆石坝粗粒料常规压实检测参数(干密度、相对密度、孔隙率等)的适用性。建立了CF在粗粒料上与碾压参数的多元回归模型,对回归模型精度进行对比,发现CF指标的预测模型误差较小,作为堆石坝不同坝料压实状态的表征指标更为科学与合理。
5.GPS碾压实时监控系统的应用
长河坝大坝施工全过程应用数字化大坝监控系统,通过在碾压设备安装高精度GPS移动终端,经基站将碾压信息进行处理和传送,实现现场分控室对设备的碾压过程实时监控。GPS数字化监控系统具有全方位实时监控各项碾压参数(碾压遍数、速度、激振力、碾压厚度)的特点,能够有效避免漏压、欠压现象,严格控制压实厚度,真正实现了过程可控。
6.基于无线微波传输的信息管理平台的开发
通过构建以无线微波技术作为数据传输链路媒介的无线传输网络,建成综合性的数字化信息管理中心,利用无线微波传输技术实时收集传输坝区各施工作业面、交通运输、防汛及危险山体监控的相关信息,从而实现后方管理中心进行坝料称重计量监控、车载加油信息监控、实时碾压监控、拌和作业信息监控、边坡危岩体监控、洪汛监控等系统的集中管理。研究开发建立一套适应快速施工节奏的以移动平板及PC端为终端的施工信息管理平台,包含地磅称重数据实时反算填筑方量的进度曲线与测量收方统计图的施工进度管理系统;包括试验检测数据统计及反映数据波动曲线、填筑厚度与质量验收评定的质量管理系统;包括油料消耗与设备数量统计的材料物资管理系统;包括交通超速抓拍与防洪、危岩体监控的安全管理系统;包括施工日志、现场照片、测量、试验等基础数据录入的移动平板办公管理系统等。完全实现质量、安全、进度、物资、文档及计量的动态智能管理,大幅度缩短了管理路径,提高管理效率。
3.6 绿色施工技术
1.筑坝料混装炸药开采爆破技术
石料场开采规模大,应用混装炸药爆破技术具有完全耦合装药、炮孔利用率高、有利于级配控制、装药效率高等优点。通过大量的爆破试验获得了满足坝料级配要求的可靠参数、防渗漏措施等。两种爆破对比分析:堆石超径率降低0.5%,过渡料半成品利用率提高8%~10%,装药效率达240kg/min,提高约40%,可节约劳动力约50%。
2.LNG环保汽车的应用
液化天然气被公认是现在地球上最干净的燃料。为减小长河坝工程长隧道运输产生烟尘带来的安全隐患,降低长隧道通风排烟难度,以达到节能目的,同时保障能源供给,避免“柴油荒”对施工运输作业进度的影响,本工程引进数十辆LNG自卸汽车作为下游江嘴堆石料料场的运输车辆,并完成加气系统的配套建设。实践证明,LNG车辆完全能够适应水利水电工程大坝填筑运输条件,并可节约约20%的燃料费用,经济和社会效益显著。
3.箱型承压板跨心墙技术
基于心墙土料静动力非线性特性、弹塑性理论和有限单元法,揭示了不同跨心墙道路型式及运输车辆作用力下的心墙应力变形分布规律与影响范围,进行了心墙抗剪强度分析,为跨心墙道路型式提供了理论依据。通过系统的理论分析和现场试验,同时开展了大量的现场测试,获得了行车过程中车辆荷载对土体的作用模式,论证并确定了合理的跨心墙运输道路方案和运行参数,研发了可拆装式箱型承压板跨心墙技术,均化了车辆荷载,有效控制了对心墙土体的影响;在60t载重汽车通行条件下,实测减压板方案的表层最大附加压力为69.2kPa,为轮压值的9.5%。跨心墙技术的应用,极大程度上促进了料源平衡优化,避免了长距离绕坝运输,取得了良好的节能减排效果。
同时,通过土料改性研究,合理规划开采料场,取消了第二土料场,节约耕地765亩,减少了移民搬迁;采用振动碾无人驾驶技术,避免了强烈振动环境对操作人员的伤害;研究采用的机械化成套设备和高效施工技术,计算减少耗油量33万L,减少CO2排放831t、SO2排放1.32t、NOx排放6.7t、CO排放3t。节能减排效果明显,有效保护了环境,实现了绿色施工。
4 结语
长河坝大坝系列新技术和新工艺的应用,有效保证了施工质量。2016年9月10日,大坝比合同工期提前4个月填筑到顶。工程先后经过13次质量监督总站质量巡检,大坝填筑全过程处于受控状态,得到质量专家好评。并多次被评为“优秀工作面”“质量示范区”。目前大坝渗控及变形均满足设计要求,大坝运行状况良好。
通过对长河坝大坝施工关键技术研究与工程实践形成了系统的施工与质量控制技术,解决了深厚覆盖层上300m级高心墙堆石坝建设的一系列工程技术难题,保证了深厚覆盖层上筑坝的工程质量和防渗安全。研究成果形成3项行业标准,取得50余项国家专利,形成多项国家及省部级施工工法,相关技术已在两河口、双江口等大型水电工程应用,经济社会与环境效益显著,具有广泛的推广应用前景。