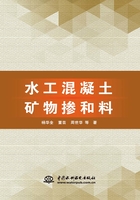
2.4 磷渣粉
2.4.1 磷渣粉的定义
磷渣是电炉法炼磷工业的副产品。GB/T 6645—2008《用于水泥中的粒化电炉磷渣》中定义,凡用电炉法制黄磷时,所得到的以硅酸钙为主要成分的熔融物,经淬冷成粒,即粒化电炉磷渣,简称磷渣。水淬粒化电炉磷渣的粒径在0.5~5mm之间,堆积密度为800~1000kg/m3,通常为黄白色或灰白色,如含磷量较高时,则呈灰黑色。磷渣经磨细加工制成的粉末即为磷渣粉。
天然磷矿石可分为磷灰石和磷块岩两种,主要成分都是氟磷酸钙[Ca5F(PO4)3]。电炉法炼磷时,在密封式电弧炉中,用焦炭和硅石分别作还原剂和成渣剂,在1400~1600℃的高温下磷矿石发生熔融、分解、还原反应。焦炭在与磷矿石中的氧结合后将气态磷释放出来,磷矿石中分解的CaO和硅石中的SiO2结合,形成熔融炉渣从电炉排出,在炉前经高压水淬冷形成粒化电炉磷渣,其主要化学反应见式(2.4-1)。

20世纪80年代以来,我国黄磷工业得到了迅速发展。据统计,我国2008年黄磷生产能力就超过200万t,占世界总生产能力的80%以上,是世界上最大的黄磷生产、消费和出口国家。每生产1t黄磷将产生8~10t磷渣,但我国磷渣年处理量仅占产渣量的20%不到,每年的磷工业排放出大量的磷渣,除少量作为建材原料和生产农用硅肥外,大量磷渣只能露天堆放,既占用了大量的土地资源,其内所含的磷和氟还会造成环境污染,污染地表和地下水资源,危及径流地区人畜的安全。因此,磷渣的排放和综合利用成为磷工业面临的首要问题。
我国于1986年发布的GB/T 6645—1986《用于水泥中的粒化电炉磷渣》规定了磷渣用作水泥混合材的品质要求。1988年发布的JC/T 740—1988《磷渣硅酸盐水泥》规定采用粒化电炉磷渣作为混合材生产磷渣水泥,允许掺量可达20%~40%。除做水泥混合材外,由于主要成分为CaO和SiO,并含有磷、氟,磷渣还可以用作水泥生产的钙质、硅质原料或矿化剂,降低水泥生产能耗。苏联将磷渣作为矿化剂大量用于制造抗硫酸盐水泥以及白色水泥,并以磷渣为主要原材料、掺加主要成分为水泥、石灰、水泥二次粉尘、氯化镁和苛性钠的2%~12%的少量外加剂,研制出无需焙烧的磷渣胶凝材料,批量生产砌块、人行道板及流槽。长江科学院与湖北兴山县水泥厂于1985年合作研制了低熟料型磷渣水泥,磷渣粉掺量达到70%~75%。
磷渣粉是一种很好的混凝土掺和料,可大幅度降低混凝土水化热和绝热温升,提高混凝土的抗拉强度、极限拉伸值和抗裂性能,改善混凝土耐久性能,其特有的缓凝性能可以满足大体积混凝土的施工需要,尤其适合应用于大体积的水工混凝土中。随着西部水利资源的深入开发,大型水利水电工程相继启动,充分利用区域磷渣资源优势,可以弥补部分地区的粉煤灰掺和料资源短缺问题,推动水电建设的可持续发展。
2.4.2 矿物组成
淬冷后的粒状磷渣主要为玻璃体结构,其玻璃体含量高达83%~98%,含有一定量的假硅灰石(α-CaO·SiO2、β-2CaO·SiO2、5CaO·3Al2O3)、硅钙石(3CaO·2SiO2)和枪晶石(3CaO·2SiO2·CaF2)等矿物,一般还会残留少量的五氧化二磷(P2O5)。若将高温熔融炉渣自然慢冷(气冷),则成为块状磷渣,它的主要结晶化合物为CaO·SiO2,气冷磷渣活性很低,一般只能作为铺路石或混凝土骨料。
2.4.3 化学成分
磷渣主要化学成分为CaO和SiO2。CaO含量在40%~50%,SiO2含量在25%~42%,CaO和SiO2总量达86%~95%,SiO2/CaO值通常在0.8~1.2。理论上,硅灰石的SiO2/CaO值为1.075,SiO2/CaO值的变化是决定黄磷渣硅灰石矿物相组成的重要因素。磷渣中还含有少量的Al2O3、Fe2O3、P2O5、MgO、TiO2、F、K2O、Na2O等,通常Al2O3含量为2.5%~5.0%,Fe2O3为0.2%~2.5%,MgO为0.5%~3.0%,P2O5为1.0%~5.0%,F为0~2.5%。受黄磷生产工艺水平制约,我国磷渣中的P2O5一般小于3.5%,但难于小于1.0%。
不同产地磷渣的化学组成不同,主要取决于生产黄磷时所用磷矿石的品质,以及磷矿石和硅石、焦炭的配比关系,磷矿石中的CaO含量高低直接决定了磷渣的CaO含量,硅石和磷矿石的配比量主要影响磷渣的SiO2和SiO2/CaO值。
黄磷生产过程中的物质分异作用,使得几乎所有焦炭被氧化成一氧化碳进入炉气,绝大部分高价磷被还原成磷蒸汽进入冷凝吸收塔,原料中约90%的Fe2O3与P4化合成磷铁,从电炉底部排出,并带走部分Mn、Ti、S等成分。上述工艺特性使得磷渣组成以CaO和SiO2为主,Fe、P含量较低,并且进一步降低了Mn、Ti、S等成分。受黄磷生产工艺的影响,国内外不同产地的磷渣化学组成有很好的相似性,有利于磷渣的开发利用。
国外磷渣的主要化学成分见表2.4-1,我国云南、贵州、广西等地的磷渣化学成分见表2.4-2。全国23家黄磷厂产生的磷渣的化学成分统计见表2.4-3,可以看到不同厂家磷渣的化学成分相对稳定。
表2.4-1 国外磷渣的主要化学成分%

表2.4-2 我国部分地区磷渣化学成分%

续表

表2.4-3 全国23家黄磷厂磷渣化学成分统计%

2.4.4 磷渣粉的加工与制备
2.4.4.1 采用试验球磨机粉磨
通常采用球磨机对磷渣进行加工粉磨。没有充分干燥的磷渣很难磨细,粉磨前必须将磷渣进行干燥处理。采用φ500mm×500mm小型试验球磨机,加料量5kg,球料比20:1,对磷渣进行粉磨加工。粉磨前先将磷渣在100℃烘干2h,使其含水量不大于0.3%,研究磷渣粉的细度(45μm筛筛余)、比表面积以及粉磨电耗的相对关系,见表2.4-4。不同粉磨时间,磷渣粉的颗粒粒度分布见表2.4-5。
表2.4-4 磷渣粉的细度(45μm筛筛余)、比表面积和粉磨电耗

表2.4-5 磷渣粉颗粒粒度分布

粉磨15min的磷渣粉中,45μm筛筛余达到42.1%。其粒度分布主要集中在10~60μm之间,占到了将近60%;1μm以下的仅占了1.97%,1~10μm也仅占到20%左右,60μm以上的仍有20%左右。但粉磨时间超过15min后,粉磨效率大幅提高。随着粉磨时间的延长,磷渣粉的比表面积不断提高。其中粉磨时间在45~90min,比表面积增幅相对平缓;小于45min或大于90min阶段,比表面积的增速很快。用球磨机粉磨磷渣的粉料粒度主要集中在1~30μm之间,各料粉完全符合罗辛-拉姆勒-本尼特(RRB)粒度分布规律。
磷渣粉的球磨机粉磨电耗与比表面积的关系见图2.4-1。粉磨时间小于45min,磷渣粉比表面小于441m2/kg时,相对球磨效率较高、能耗较低。比表面积超过500m2/kg,粉磨能耗急剧上升。因此,球磨工艺不适合加工细度要求较高的磷渣粉。

图2.4-1 比表面积S与能耗的关系
2.4.4.2 采用生产性球磨机粉磨
在贵州省瓮福磷肥厂利用磷肥磨细加工的球磨机对贵州瓮福黄磷厂生产的电炉磷渣和贵州泡沫山黄磷厂生产的电炉磷渣分别进行了加工。加工前对磷渣进行烘干处理,将含水量控制在1%以内,通过控制送料速度控制磷渣粉的细度(一般水泥厂的球磨机可通过调整磨机中的球弹比例或回料系统反复粉磨使细度达到规定的要求),最终以5车/h磨出的磷渣粉细度达到200目(80μm筛筛余10%以内)。按1车/150kg计算,1h能生产750kg磷渣粉,1d可加工18t磷渣粉。按10车/h、6车/h、5车/h分别对两个料源的磷渣进行加工,实际获得磷渣粉样品的情况如表2.4-6所示。
表2.4-6 磷渣粉加工参数表

从表2.4-6的数据可以看出,磷渣粉的粉磨细度和加工速度基本成正比,即加工速度越快,其细度越大,颗粒粒径越大,比表面积越小。对于不同厂家的磷渣,相同的加工速度对应的磷渣粉细度和比表面积相近。
2.4.5 颗粒形态
粒化磷渣肉眼下呈白色至淡灰色,玻璃光泽,形态有球状、扁球状、纹状、棒状、不规则状等。偏光镜下,呈明显的碎粒结构,碎粒内部广泛发育多种收缩裂理,碎粒具有光学均质性,全消光,未发育任何明显的结晶相。显然,高温熔融磷渣经水淬骤冷,体积快速收缩,破裂形成碎粒状结构,快速冷却固化使结晶作用缺乏足够的发育时间,使粒化磷渣呈非晶玻璃态结构。
磨细后的磷渣粉颗粒大小不均,粒径在n~n×10μm之间,颗粒表面光滑,呈棱角分明的多面体形状,少量呈片状,基本不含杂质。图2.4-2为比表面积250m2/kg、350m2/kg、450m2/kg的磨细磷渣粉颗粒SEM照片。
2.4.6 品质指标
2.4.6.1 磷渣粉的品质要求
近年来,磷渣粉作为混凝土掺和料在大中型水电水利工程中得到了成功应用,积累了较多的工程经验。2007年制定的电力行业标准DL/T 5387—2007《水工混凝土掺用磷渣粉技术规范》,对用于水工混凝土的磷渣粉的品质指标做出了具体规定,要求其质量系数不得小于1.10,比表面积、需水量比、三氧化硫含量、含水量、安定性、五氧化二磷含量、烧失量、活性指数均应符合要求。DL/T 5387—2007《水工混凝土掺用石类渣粉技术规范》磷渣粉的品质指标列于表2.4-7中。
表2.4-7 磷渣粉的品质指标

2.4.6.2 质量系数
磷渣的质量系数是指主要碱性氧化物和酸性氧化物的质量比,即钙、镁、铝元素氧化物质量之和与硅、磷元素氧化物质量之和的比值,见式(2.4-2)。


图2.4-2 磨细磷渣粉颗粒SEM照片
磷渣的质量系数反映了磷渣主要化学成分的关系,是评定磷渣粉活性的重要指标。质量系数越大,磷渣粉的活性越高。但是仅仅根据质量系数来判断磷渣粉的活性是不全面的,磷渣粉的活性还与其内部结构和比表面积等因素相关。
在中国和苏联的标准中,规定用于水泥混合材的磷渣要求其质量系数不得小于1.10,P2O5含量不得大于2.5%。
2.4.6.3 比表面积
比表面积是影响磷渣粉性能的重要指标。淬冷成粒的磷渣必须磨成具有较高比表面积的磷渣粉,才具备潜在的水化活性,能用作混凝土的掺和料。磷渣粉的颗粒大小也可采用以筛余量来表示,但采用比表面积作为磷渣粉细度指标,更适于反映磷渣粉的颗粒级配和磨细程度。不同比表面积磷渣粉的胶砂强度和活性指数对比见表2.4-8。从表2.4-8可以看到,磷渣粉比表面积小于300m2/kg时,活性指数较低。
表2.4-8 不同比表面积磷渣粉的活性指数

2.4.6.4 需水量比
影响磷渣粉需水量比的主要因素包括比表面积、粒形和杂质等。比表面积在200~450m2/kg范围内的磷渣,一般需水量比在96%~105%之间,对混凝土拌和物的流动性或用水量影响较小。磷渣粉的需水量比与粉磨方式及比表面积的关系见表2.4-9。
表2.4-9 磷渣粉的需水量比

图2.4-3所示的不同细度的瓮福磷渣粉掺量与需水量比的关系。磷渣粉比表面积增大并未带来需水量比的明显规律性变化,相同细度的磷渣粉在不同掺量下,需水量比变化也没有明显规律性,即磷渣粉颗粒细度及掺量对胶凝材料需水量没有明显影响。在试验掺量和细度范围内,磷渣粉的需水量比基本在96%~100%之间变化。

图2.4-3 不同细度磷渣粉掺量与需水量比的关系
2.4.6.5 含水量
虽然磷渣中含有较高的玻璃质含量,但由于磷渣中的Al2O3含量较低,因此在无碱的条件下,磷渣基本没有水硬活性。不过,磷渣具有较高的比表面积和表面能,因此易受潮结块,当受潮的磷渣掺入混凝土中,会影响混凝土拌和物的均匀性。此外,当磷渣中含有较多水分时,磷渣难以磨细,会降低磷渣粉的比表面积及其均匀性。通常,出磨磷渣粉含水量一般在0.5%以下。
2.4.6.6 安定性
安定性主要与材料中的游离氧化钙相关。熔融磷渣在冷却过程中,可能会有游离氧化钙分相析出,当其含量超过一定限度时,可能会导致混凝土膨胀开裂,对混凝土质量产生不利的严重影响。不过,现有资料证实磷渣中基本不含游离氧化钙。不同磷渣粉掺量下,水泥的安定性试验结果见表2.4-10。试验结果表明,经过4次沸煮,掺磷渣粉水泥净浆试件的膨胀值(雷氏法)均小于5.0mm。
表2.4-10 掺磷渣粉水泥的安定性试验结果

2.4.6.7 烧失量
黄磷生产过程中,采用焦炭作为还原剂,因此磷渣中可能会含有未燃尽的炭粒。如前所述,多孔炭粒,不仅增加需水量比,而且具有较强的表面活性作用,对引气剂吸附强烈,且会破坏混凝土内部结构,造成内部缺陷,降低混凝土的性能,因此需要严格控制其含量。
2.4.6.8 SO3
磷渣中一般含有1%~3%的三氧化硫,过多的SO3可能会使混凝土产生延滞性硫铝酸钙,导致体积膨胀破坏。磷渣粉中SO3含量多少,主要与生产黄磷的磷矿石品质相关。磷矿石中通常都含有一些杂志,如氟酸盐、磷化石灰石、砂以及黏土等,这些没有被还原的物质就会存在于磷渣中。
2.4.6.9 P2O5
P2O5在磷渣中可以同时以正磷酸盐和多聚磷酸盐的形式存在。正磷酸盐易溶,阻碍六方形水化铝酸钙进一步水化,导致水泥的缓凝,会延长硅酸盐水泥的凝结时间。此外,由于P—O键的键能高于Si—O键和Al—O键,因此多聚磷酸盐成为网络形成体也会降低粒化磷渣的早期活性,延长混凝土的凝结时间。
2.4.6.10 氟含量
磷渣粉中的氟(F)含量对混凝土凝结时间和强度均有影响。在碱性条件下玻璃相解体时析出的氟离子与水化产物氢氧化钙形成的氟化钙会延缓水泥凝结;另外,氟还可能引起钢筋锈蚀。尽管DL/T 5387—2007《水工混凝土掺用磷渣粉技术规范》没有对磷渣粉中的氟含量进行具体规定,但当掺入磷渣粉的水泥出现严重缓凝现象时,应检测其氟含量,并根据试验结果作出相应限制。
2.4.6.11 活性指数
粒化磷渣具有与粒化高炉矿渣相似的玻璃体结构。从化学组成来看,粒化磷渣是一种具有潜在活性(胶凝性)的材料。由于磷渣中的Al2O3含量较低,以及存在P2O5和F,使磷渣的早期活性低于粒化高炉矿渣。
与矿渣相似,磷渣的活性不仅与化学成分相关,而且在很大程度上取决于黄磷生产工艺、成粒条件及其结构形态。经过水淬处理的磷渣,在骤冷成粒的过程中,形成了高玻璃质含量的结构,储备了大量的化学内能,在粉磨过程中,机械能转化成磷渣粉的表面能,因此磷渣粉具有一定的活性。一般情况下,比表面积在300kg/m2以上时,磷渣粉的活性指数,即28d龄期抗压强度比可达到60%以上,90d龄期抗压强度比可达到85%以上。
2.4.6.12 放射性
近年来人们越来越关注建筑材料的放射性,通常磷渣中的放射性核素比活度符合GB 6763—1986《建筑材料产品及建材用工业废渣放射性物质控制要求》限制规定:ARa/200≤0.1;ARa/350+ATh/260+AK/4000≤1.0,且放射性活度低于粉煤灰。典型的磷渣放射性核素比活度见表2.4-11。磷渣与粉煤灰的放射性对比见表2.4-12。
表2.4-11 磷渣放射性核素比活度

表2.4-12 磷渣与粉煤灰放射性比较试验结果
