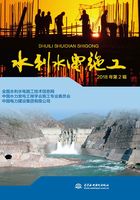
黄登水电站岩壁梁岩台双向控爆开挖施工
摘要:通过对多个地下厂房岩壁吊车梁施工的探索及总结,成功摸索出了一套岩壁吊车梁岩台开挖施工工法,并在黄登水电站成功实施,开挖成型效果较好。
关键词:吊车梁 开挖施工 双向控爆 黄登水电站 地下厂房
1 概述
地下厂房开挖施工中,岩壁梁岩台开挖是施工的重点及难点,开挖成型极为困难,精度要求又极高。通过科学的试验,选择适合的爆破参数、钻孔参数、孔间排距等。根据不同地质条件,在岩台开挖前采取一些针对性的加固措施,保证了岩台的完整性;在岩台的造孔精度控制上,采用了样架导向技术,保证了造孔质量;岩台开挖采取双向光面爆破法,保证了岩壁吊车梁开挖质量。
黄登水电站地下主厂房地层主要为变质火山角砾岩、变质火山细砾岩夹变质凝灰岩,其次是侏罗系中统花开左组板岩。洞室岩体呈次块状—块状,以Ⅱ、Ⅲ类围岩为主,岩体完整性好,局部受F230-14断层影响,围岩揭露呈水平向70°切割断层;地下洞室位于地下水位以下,洞室围岩均为微透水—极微透水岩体。主厂房开挖高度为80.5m,长度为247.3m,上拐点以上宽度为32m,下拐点以下宽度为29m。根据主厂房分层高度,岩台布置在主厂房Ⅲ层上下游边墙,上拐点高程为1496.27m,下拐点高程为1494.13m;岩台高为2.14m,宽为1.5m,斜面长2.62m,倾角为55°。
岩壁吊车梁开挖结合主厂房Ⅲ层结构特点,首先进行中部梯段拉槽开挖(宽度为20m),并预留4.5m保护层。中部拉槽开挖采用潜孔钻垂直钻孔,中部拉槽超前两侧岩台保护层开挖约30m。岩台部分采用手风钻双向光爆,施工过程中按Ⅲ①→Ⅲ②→Ⅲ③…Ⅲ⑤的顺序进行开挖。在中槽开挖前下直墙所在面采用YQ-100E改进型轻型潜孔钻钻孔,一次预裂到Ⅲ层底板1489.70m高程;岩壁梁上拐点以上直墙设计轮廓线光爆孔采用手风钻造孔,并预埋PVC管进行保护。下直墙以内的保护层采用手风钻分台阶垂直开挖,浅孔小药量爆破,开挖高度3.8m。最后进行岩壁梁小三角体岩台开挖,采用三角体斜墙面及上直墙面手风钻打斜孔和垂直孔双向光爆。岩台开挖采用高精度非电雷管,磁电雷管起爆。边墙预裂采用YQ-100E改进型轻型潜孔钻钻孔,中槽开挖采用手风钻水平钻孔。为确保岩壁吊车梁拐点安全,在1493.97m高程(拐点以下16cm)布置φ25@1m、L=3m、外露0.1m的砂浆锚杆,并采用∠160×100×10角钢与锚杆焊接。斜面孔造孔时采用1.5寸钢管架设样架造孔。
岩台开挖成型平整度控制较好,半孔率达到90%以上,平均超挖控制在8.9cm以内。
2 技术特点
岩壁吊车梁控制精度要求高,岩台不能受到大的扰动。为减少爆破振动对岩壁吊车梁的影响,该部位的开挖采用预留保护层的开挖方式,先离厂房边墙3~5m预留保护层进行施工预裂,再进行中部梯段拉槽开挖。中槽施工预裂采用轻型潜孔钻造孔,采用履带式潜孔钻D7进行梯段开挖,也可采用手风钻造水平孔开挖;岩台所在层设计边线预裂采用轻型潜孔钻造竖直孔,采取“一次预裂、薄层开挖、随层支护”的方法,减小对保留岩体的爆破振动影响,保证高边墙稳定。保护层开挖遵循“短进尺、弱爆破”的原则采用手风钻分层进行,斜岩台部位采用双向光爆,其余部位单向光爆。同时为了保证开挖质量,在岩台开挖前需选取一个部位进行生产性试验。
3 施工方法及要点
岩壁吊车梁双向光爆采用分段、分序施工,其施工程序和施工工艺主要根据生产性试验确定。
3.1 生产性试验
生产性试验的目的主要是通过试验不断摸索、确定岩壁吊车梁开挖的施工程序、爆破参数及钻孔精度控制方法。试验分为模拟试验及生产性试验,一般模拟试验进行1~2次,生产性试验进行3~4次。生产性试验选择在不同地质条件下进行,验证并确定开挖分序、爆破参数、钻孔精度控制方法及下拐点保护措施。
3.2 开挖分层分区
岩壁吊车梁开挖按照图1所示进行分层、分区。

图1 岩壁吊车梁开挖分层图(单位:m)
①、②、③—保护层及岩台开挖顺序
3.3 开挖施工
3.3.1 岩壁吊车梁开挖施工程序
岩壁吊车梁开挖施工程序如下(不包括上层开挖及本层中部拉槽开挖):上层边墙欠挖检查及处理→岩台保护层①区开挖及③区垂直光爆孔造孔→岩台保护层②区开挖→地质素描及岩面基础验收→岩台下拐点加固处理(锁口锚杆、角钢防护施工等)→下拐点以下系统支护→岩台③区开挖。保护层也可根据岩台所在层分层高度调整,分三层开挖。
其中锁口锚杆、角钢(或槽钢)防护施工及下拐点以下1m范围喷混凝土支护用于有地质缺陷的部位,地质条件较好的部位可以省去此工序。
3.3.2 施工程序中需注意的问题
(1)保护层及中部拉槽开挖宽度控制。预留保护层宽度按照3~5m控制,这样才能保证在中槽开挖完成后保护层还有足够的宽度供手风钻造孔施工。中槽开挖的宽度需注意满足出渣装车及会车需要。
(2)开挖高度。岩壁吊车梁上面一层开挖底板距离岩壁吊车梁上拐点一般在1.5~2.5m,岩壁吊车梁所在层的开挖底板距离岩壁吊车梁层下拐点3.5~4m。岩壁吊车梁保护层开挖层高控制在2.5~3m。
保护层开挖分层高度按照2.5~3m考虑是因为手风钻造孔施工在孔深不大于3m时造孔相对容易并比较容易控制造孔精度。岩壁吊车梁上层开挖底板与岩壁吊车梁上拐点距离主要考虑③区开挖(岩台斜面开挖)一般只有150cm左右的厚度,如果岩壁吊车梁上层开挖底板与岩壁吊车梁上拐点之间距离过大,爆破过程中可能会对岩壁吊车梁建基面造成损伤,因此其距离按照1.5~2m控制。岩壁吊车梁所在层的开挖底板与岩壁吊车梁层下拐点的距离主要考虑手风钻进行岩壁吊车梁斜面孔施工的空间;并综合考虑岩壁吊车梁受拉、受压锚杆的设计参数,留出足够的空间保证锚杆造孔及安装不会受到限制。
3.3.3 开挖分段及控制措施
(1)分段长度。岩壁吊车梁开挖分段长度原则上按20m一段,根据现场中部拉槽揭露出的实际地质情况,若遇到岩石破碎带、块体或断层部位,可对分段长度适当调整。
(2)开挖顺序。厂房Ⅲ层施工工序较多,必须按照“平面多工序,立体多层次”的原则,作业时间存在搭接,进行开挖支护流水作业。厂房上、下游边墙超前预裂100m后,岩台竖直光爆孔造孔开始;Ⅲ①层中槽超前30~50m以上,两侧保护层错距开挖跟进,错开距离15~30m;Ⅲ②层分左、右半幅开挖,在Ⅲ①层开挖全部完成后进行;Ⅲ②层开挖完成后,边墙支护及时跟进,确保高边墙稳定及工期目标顺利实现。
3.4 施工工艺流程
各区开挖施工工艺流程如下:测量放线→样架施工→样架检查验收→造孔施工→验孔→样架拆除→爆破参数设计及装药爆破→出渣清底→爆破效果检查。
3.5 施工操作要点及控制措施
3.5.1 测量放线
测量由专业人员进行,放样内容包括样架导向定位点、所有周边孔开孔点,所放点位须在现场进行明显标识,放线过程现场技术员全程参与。
3.5.2 样架搭设及检查验收
导向样架采用1.5英寸钢管排架搭设,管扣件连接。边墙及底板开挖面采用手风钻先造直径50mm的孔,深50cm,再用钢管插入孔内加固样架,定位导向管长1.2m,具体根据孔位要求布置。样架搭设参见图2。
样架搭设完毕后需经过专业测量人员进行校核及质量管理部门验收方能投入使用。
3.5.3 造孔控制
岩壁吊车梁岩台开挖采用样架进行钻孔精度控制。
(1)开挖布孔。岩台(③区)竖直、斜面光爆孔均按35cm孔距布孔,若遇到岩石破碎带、块体或断层部位,可适当调整孔距(可调整为30cm孔距布孔)。每个光爆孔均按照爆破设计由专业人员通过测量放线定出孔位。

图2 导向样架搭设示意图
(2)孔深控制。严格控制垂直孔的孔深,在样架上面专门搭设一根横向钢管,从钢管的上口到每区的设计孔底长度取为定值,并且将所用钻杆全部截成这个长度值(包括钻头长度),钻工用定长(包括钻头长度)钻杆施工至横向钢管上口处时,钻机被此钢管挡住无法向下施钻,从而保证所造孔在孔深要求上满足规范要求。
(3)倾角控制。严格控制造孔的倾角,每个光爆孔都采用导向管(1.5英寸钢管)进行施工,并且为了保证钻杆的居中,在每个导向管的上口处都加了对中夹片,这样就保证了所造的孔在方向上满足设计要求。造孔倾角控制见图3。

图3 造孔倾角控制示意图
3.5.4 样架拆除
爆破孔经过检查验收合格后,可拆除样架。拆除过程中需对爆破孔进行有效的保护,防止出现堵孔等现象。
3.5.5 爆破参数控制
根据生产性试验取得的成果,初步拟定各区开挖装药爆破参数,实际开挖过程中根据揭露的地质情况及时对爆破参数进行个性化设计,及时优化调整,调整时线装药密度按10g/m进行增减。为了提高岩壁梁岩台面的成型质量,用斜面和垂直面的“面装药密度”控制线装药密度。
所有光爆孔药卷均事先按照爆破设计确定的装药结构采用竹片绑扎好,光爆孔插药入孔时还应注意药卷的方向,竹片靠洞室轮廓线一侧,药卷朝向最小抵抗线方向。相邻孔的间隔装药错开,尽量减小因间隔药之间围岩裂隙发育造成的局部突起现象。爆破孔采用黏土或细砂袋进行炮孔的堵塞,堵塞长度不小于最小抵抗线。
(1)完整岩石。垂直光爆孔线装药密度按55g/m控制,垂直孔面装药密度154.3g/m2;斜面光爆孔线装药密度按86.2g/m控制,斜面孔面装药密度246.3g/m2。
(2)节理裂隙发育岩石。垂直光爆孔线装药密度35g/m,垂直孔面装药密度98.2g/m2;斜面光爆孔线装药密度62.3g/m,斜面孔面装药密度178.0g/m2。
3.5.6 爆破效果检查
排炮结束后,现场技术人员、专职质检人员及专职安全人员必须及时到现场检查爆破效果,收集相关数据。测量人员采用全站仪对岩面超欠挖情况进行检查,形成测量体型图。另外检查下拐点的破坏情况、上拐点成型是否在一条直线上,以及炮孔间是否出现“八”字孔现象,检查并统计残孔率及半孔率,炮孔间岩面的平整度,垂直孔与斜面孔对应是否整齐。根据检查结果及收集的数据,及时与质量标准相比较,得出评价结论及改进方法。
3.6 岩台下拐点加固措施
当岩台下拐点部位岩体较为破碎,节理、裂隙等较发育时,系统锚杆支护只能把体积稍大的不利岩体锁住保证岩体的整体性,对体积稍小的岩体或相对破碎的岩体还需在进行③区爆破施工前采取加固措施,从而保证岩台的成型质量。
(1)在岩台下拐点以下10cm位置布置一排φ25@75cm,L=3m砂浆锚杆锁口,外露15cm;采用∠50×50×3角钢对锁口锚杆进行通长焊接加固。
(2)在锁口锚杆和角钢的基础上,采用C30钢纤维混凝土对下拐点以下1m范围喷6~8cm厚混凝土加固。
(3)对于岩石破碎带、块体或断层部位,除采用上述两种方案外,可视情况进行随机锚杆或挂钢筋网多重加固。
岩壁吊车梁下拐点加固参见图4。

图4 岩壁吊车梁下拐点加固示意图(单位:mm)
4 结语
(1)通过增加岩台保护层分序、采用样架进行周边孔控制,以及对不同岩石、部位采用“个性化装药”和“面装药密度”控制线密度等方法,整体岩台成型完整,爆破半孔率达到90%以上,平均超挖控制在3.2cm以内,有效控制了质点爆破振动速度,减小了边墙变形,保证了高边墙围岩的安全稳定;同时也为以后地下厂房高边墙岩台施工提供了技术指标和新的技术方法,新颖的工法将促进地下工程施工技术的进步,社会效益明显。
(2)与同类岩台开挖工法相比,通过精确控制,减小超挖量,减少岩壁梁混凝土施工时混凝土的超填量以及处理欠挖的时间和费用,降低了消耗,节省了时间,产生了较好的经济效益。
(3)岩台开挖采用了双向光爆工艺,可保证不同区段岩台平行施工,加快施工进度。
(4)在造孔中采用了标准化样架导向技术,减少了人为因素影响,保证了施工质量的稳定性。