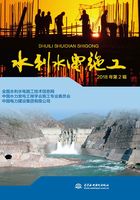
黄登水电站主厂房开挖施工技术措施综述
摘要:本文主要围绕黄登水电站主厂房开挖施工进行阐述,对施工技术方案进行总结,可为类似工程提供借鉴。
关键词:黄登水电站 主厂房开挖 施工技术措施 综述
1 工程概况
黄登水电站引水发电系统地下主、副厂房按一字形布置,从右至左依次布置右端副厂房、安装间、机组段、左端副厂房,相应长度分别为25.15m、60m、141m、21.15m,总长247.3m,高度80.5m,岩壁梁以上宽度32m,以下29.3m。
2 地质条件
地下主厂房段地层主要为变质火山角砾岩、变质火山细砾岩夹变质凝灰岩,变质凝灰岩岩体较破碎,劈理和顺层积压面发育。侏罗系中统花开左组板岩岩体较破碎,呈薄层状结构。
洞室岩体呈次块状—块状,以Ⅱ、Ⅲ类围岩为主,岩体完整性好;断层破碎带及较大劈理发育或挤压面发育的变质凝灰岩夹层为Ⅳ、Ⅴ类围岩。洞室在局部可能会出现的变形破坏形式主要为由结构面组合形成的楔体塌滑或崩塌破坏及断层带的坍塌破坏。
3 开挖方法
3.1 分层
主厂房从上至下共分10层进行爆破开挖。具体分层见图1。
主厂房Ⅰ、Ⅱ层开挖以空调机室为施工通道,Ⅲ层及部分Ⅳ层以主厂房运输洞为主要运输通道,Ⅳ层、Ⅴ层及部分Ⅵ层以母线洞为通道,Ⅶ、Ⅷ层以引水下平洞作为通道。下部Ⅸ、Ⅹ层石渣从溜渣井下至后延段,以尾水支洞为施工通道。

图1 主厂房开挖分层横剖面图
主厂房开挖采用钻孔爆破法进行施工,主要施工技术有预裂爆破、光面爆破、掏槽等,主要施工工艺有导洞法、导井法、先洞后墙法等。
3.2 岩锚梁开挖
综合厂房各层开挖特点及复杂程度,岩锚梁的开挖汇集了组织水平、技术水平以及施工人员个人素质等各要素,将直接关系到岩锚梁的成型质量。另外,岩锚梁开挖成型质量与地质条件息息相关。
岩锚梁具体开挖过程及成果描述如下:
(1)地下厂房岩锚梁范围开挖高度8.8m,岩台坡比为1∶0.7。
(2)开挖总体程序:①吊顶小牛腿浇筑基本完成后,进行Ⅲ层开挖支护;②Ⅲ层中部拉槽先进行施工,预裂待Ⅱ层锚索施工完成后紧跟施工。
(3)施工方法简述。岩锚梁采取中部拉槽水平开挖,两侧边墙预留保护层,岩台部分采用手风钻双向光爆。施工过程中首先采取在上游侧从空调机室修建施工便道的方式进入工作面,进行Ⅲ①层开挖支护施工;Ⅲ①层施工完成后利用主厂房运输洞(局部区域垫渣)升坡进行上游侧施工便道拆除,并进行占压部分的Ⅲ①层开挖施工及Ⅲ②层开挖及支护施工。Ⅲ②层开挖时,上、下游边墙留2.5m保护层,YT-28手风钻造竖直孔,浅孔小药量光爆。为此,需增加一道施工预裂,孔距60cm。考虑无自由面,施工预裂线装药密度初拟170g/m,可根据爆破试验和现场实际地质条件优化。施工预裂超前于Ⅲ②层中槽开挖,上、下游侧保护层开挖适时跟进,掌子面错开30m左右。
Ⅲ层岩锚梁岩台采用双向控爆法开挖。Ⅲ层中槽开挖超前岩台保护层30m,岩台上部直墙面光爆孔造孔与预裂孔可同时施工。导向钢管采用φ48钢管,钻孔样架全部采用φ38钢管搭设,孔位定位钢管间距35cm,孔深控制钢管全长布置。外侧保护层开挖结束后,从下部搭设钢管样架,采用手风钻从下部钻岩台斜面光爆孔。斜面光爆孔与预先施工的上部直墙面光爆孔组成双向光爆网,同步起爆挖除岩台三角体。根据项目部多座地下厂房岩台施工的成功经验,优选岩台三角体双向光爆参数,并根据岩层不同地质结构调整装药参数是保证岩台成型质量的关键。岩锚梁岩台双向控爆开挖方法见图2。

图2 岩锚梁岩台双向控爆开挖方法示意图(单位:cm)
岩锚梁岩台的开挖,严格控制光面爆破孔的钻孔方向、孔距、装药量,并根据地质条件的变化、爆破效果及时修正孔距和装药量。爆破孔装药采用间隔装药,严格控制装药量。斜面孔装药结构图见图3、图4。
根据岩锚梁爆破试验成果,推荐光面爆破参数见表1。

图3 奇数斜面孔装药结构图(单位:cm)

图4 偶数斜面孔装药结构图(单位:cm)
表1 推荐光面爆破试验参数表

岩锚梁部位的岩壁及岩台面不允许欠挖,局部超挖不得大于10cm,不允许产生爆破裂隙。岩壁开挖后,清除爆破产生的裂隙及松动岩石,清洁岩壁面,及时进行岩壁斜面修整。
厂房Ⅲ层主要采用YT-28手风钻钻水平孔开挖,分左、右幅开挖。手风钻水平抬动开挖时,为保证具有良好临空面,采用毫秒雷管微差起爆网络。边墙采用手风钻分两次进行超前预裂,在设计开挖边线上形成一条贯穿裂缝,以缓冲、反射开挖爆破的振动波,减小对保留岩体的爆破振动破坏,使之获得较平整的开挖轮廓。
3.3 开挖工艺流程
(1)施工准备。洞内风、水、电就绪,施工人员、机具准备就位。技术员对各班操作手进行技术交底。
(2)测量放线。洞内导线控制网采用全站仪进行测量。每排炮后进行洞室中心线、设计开挖规格线及控制点测放,并根据爆破设计参数点布孔位。
(3)钻孔作业。采用YT-28手风钻钻孔,由合格钻工严格按照测量定出的中心线、开挖规格线、控制点、尾线和测量布孔进行钻孔作业。在已经造好的孔上插上PVC管进行定向。
在钻孔作业过程中,技术人员现场旁站,便于及时发现和解决现场技术问题。每排炮由值班技术员按“平、直、齐”的要求进行检查,做到炮孔的孔底落在爆破规定的同一个铅直断面上;为了减少超挖,周边孔的外偏角控制在设备所能达到的最小角度。炮孔装药之前,质检员对掌子面上的炮孔进行检查,如有遗漏,则要补钻。对炮孔的各项指标检验合格后,方可装药。
(4)装药、连线、起爆。装药前用高压风冲扫孔内,炮孔经检查合格后,方可进行装药爆破;炮孔的装药、堵塞和引爆线路的连接,由专业的炮工严格按批准的钻爆设计进行施作,装药严格遵守爆破安全操作规程。
掏槽孔由熟练的炮工负责装药,光爆孔、预裂孔用小药卷捆绑于竹片上间隔装药。水平开挖利用自制平台架装药,炸药装好之后,理顺导爆管,先进行同段炮非电雷管的并联,再进行不同段的串联,然后用黏土进行炮孔的封堵,要求连线、封堵良好,封堵长度不小于炸药的最小抵抗线。再由技术员和专业炮工分片分区查看,并进行网络接线检查。撤退工作面其他工作人员、设备、材料至安全位置。炮工负责引爆。
(5)开挖前,完成超前支护。超前支护形式主要采用超前锚杆。超前支护完成后,确保洞室能满足开挖爆破施工要求时,才能钻进爆破开挖,并在开挖结束后系统支护跟进。对层间错动带、小断层及节理裂隙较为突出的部位进行随机支护或加强支护。同时,开挖进尺控制在1~1.5m,遵循“短进尺,弱爆破”的原则。
3.4 关键及特殊部位开挖技术
主厂房开挖成型质量的关键部位在于岩锚梁、洞室交叉部位的施工。
(1)地下洞室及岩锚梁对爆破质点振动速度要求非常严格(小于7cm/s),每层拉槽开挖前必须进行周边设计轮廓线预裂,加快地震波的衰减速度,从而尽可能减小爆破振动对围岩及支护结构的影响;由于第Ⅳ层离岩锚梁比较近,为减少第Ⅳ层开挖爆破对岩锚梁的振动影响,岩锚梁锚杆需在第Ⅳ层边墙预裂完成后方可进行安装,然后进行岩锚梁混凝土浇筑。在厂房第Ⅳ层开挖时必须进行爆破振动测试,控制单响药量和质点振动速度,求得本区实测的K、a值。
(2)引水压力管道、母线洞、尾水管扩散段、主变运输洞、主变交通洞等都必须在高边墙上开洞口,高边墙稳定问题突出。因此,施工中采取以下措施,确保施工质量:第一,测量放线认真准确,岩锚梁等关键部位由上级测量单位复核;第二,由经验丰富的钻手施钻,技术员跟班指导,岩锚梁等重要部位组织质量跟踪小组,对每道工序进行质量跟踪;第三,在技术人员指导下,由经验丰富的炮工进行装药连线,严防用错雷管段数;第四,严格控制最大单响装药量,以防止爆破振动对厂房高边墙,特别是岩锚梁造成损坏;第五,为保证边墙开挖轮廓,厂房除Ⅰ层外,其余每层开挖前均对上下游边墙及端墙进行预裂;第六,高边墙上开洞口时,尽可能采用小洞贯大洞的方式并预先做好洞口的锁口支护,并按“先洞后墙”的原则进行施工,做好各洞口与厂房相交处的环向预裂。
(3)岩锚梁施工技术要点。
1)岩锚梁位于厂房第Ⅲ开挖层内,为保证岩锚梁岩台成型,开挖时采用控制爆破技术,采用高精度非电雷管。开挖前精心进行爆破设计与试验,试验选择在先施工段进行,爆破工艺性试验通过后才能大量展开施工。岩锚梁部位的开挖采用预留保护层的开挖方式,保护层与中部槽挖之间采取预裂爆破分开。中部槽挖先行,用液压潜孔钻垂直钻孔,梯段爆破,超前两侧保护层开挖约30~50m,保护层厚度初拟4.0m,施工中根据爆破试验优化参数。
2)岩锚梁保护层必须按爆破振动试验确定的爆破参数严格控制下直墙外侧垂直钻爆的单响药量,钻孔时采用三次钻杆校杆法和加扶正器法保证下直墙面预裂孔垂直,孔与孔之间平行,孔底偏差小于10cm,保证预裂孔钻孔精度。岩台三角体上直墙面及斜面光爆孔间距30~35cm,钻孔深度及角度用测量仪器严格控制。岩石三角体双向光爆采用高精度非电毫秒雷管,磁电雷管起爆。
3)岩锚梁施工中,采用激光定位技术放样,精确测放轮廓线。钻孔方位角采用地质罗盘控制,水平钻孔用水平尺控制水平度,斜面倾斜孔仰(倾)角及深度用几何法控制。开孔前用全站仪测定每一孔位应钻深度。
4)岩锚梁三排深孔受力锚杆设置钻孔样架。锚杆孔深根据超挖情况重新计算,并用全站仪准确测量定位。受拉锚杆采用凿岩台车造孔,受压锚杆采用潜孔钻造孔。锚杆孔上、下偏差不大于±3cm,左右偏差不大于±10cm,孔深偏差不大于5cm,角度偏差不大于+2°。岩锚梁锚杆安装在Ⅳ层边墙预裂完成后进行,以减小爆破对岩锚梁锚杆的扰动。
3.5 钻爆设计
3.5.1 钻爆设计原则
根据主厂房地质条件及相关技术规范要求、开挖方法及以往施工经验,隧洞开挖爆破设计按“短进尺、弱爆破”的原则进行;严格控制最大单响药量,减小对围岩的扰动,并按规范和设计要求的质点振速等要求对爆破参数进行测验,根据实测参数进行爆破设计。
3.5.2 爆破参数选择
厂房Ⅰ层采用手风钻造水平孔开挖,钻孔直径为50mm,循环进尺根据不同围岩类别暂定为:Ⅱ、Ⅲ类围岩洞段3m,Ⅳ类围岩洞段1.0~1.5m,周边光爆孔间距50cm,爆破效率按 91%考虑。
3.5.3 爆破器材选用
(1)炸药:采用塑料膜包装的卷状乳化炸药,水位线以下开挖可采用4#岩石抗水炸药。成品卷状乳化炸药密度为0.95~1.3g/cm3,爆速不小于4500m/s,作功能力不小于320mL,猛度不小于16mm,殉爆距离不小于4cm。
(2)雷管:采用普通非电毫秒雷管,塑料导爆管雷管的单发准确率应在99.9%以上,延时精度符合出厂质量要求。
(3)导爆索:浸水前导爆索爆速不低于6500m/s,能可靠传爆和起爆炸药,导爆索爆速不低于6000m/s。
(4)起爆装置:采用磁电起爆。
3.5.4 爆破允许质点振速
按照招标文件技术条款,厂房高边墙等部位最大允许质点振速应不超过7cm/s,其余应满足《水工建筑物地下工程开挖施工技术规范》和《引水发电系统地下洞室开挖与支护施工技术要求(A版)》的要求。
4 开挖质量控制
(1)严格按照设计图纸、施工技术规范、监理批复的措施施工。
(2)建立和完善 “三检”质量管理制度,执行质量一票否决制。
(3)施工用原材料必须有出厂合格证、材质证明书,需要抽检的必须及时通知试验室取样,检查合格后方可使用。
(4)严格控制开挖边界尺寸,尽量避免超欠挖,有结构要求的不允许欠挖,超挖不大于15cm(不良地质段除外)。
(5)光面爆破须达到以下要求:
1)残留炮孔痕迹应在开挖轮廓面上均匀分布。
2)炮孔痕迹保存率:完整岩石在80%以上,较完整和完整性差的岩石不少于50%,较破碎和破碎岩石不少于20%。
相邻两孔间的岩面平整,孔壁不应有明显的爆震裂隙。
(6)严格按爆破设计进行布孔装药爆破。
(7)开挖要求四点一线(底线点、中线点、起拱点、顶点)的孔位在同一直线上。
(8)QC(全面质量管理)小组定期召开厂房开挖质量和工艺讨论会,并经常到作业现场收集实际资料(围岩地质条件、钻爆参数等),对数据进行分析整理,为不断提高厂房开挖质量提供依据。
5 结语
黄登水电站地下厂房系统洞室群施工除具有常规地下厂房施工难度外,还受到特殊地质条件的影响,洞室开挖后围岩会产生较强烈的变形破坏。尤其是在下游边墙部位,开挖形成的洞室交叉段、岩柱等应力集中部位变形破坏更为严重。开挖过程中对应不同结构及地质情况选择了适应性的措施:
(1)根据地下厂房及临近洞室施工顺序及进度计划安排,周密规划施工通道,并考虑由于地质条件变化而导致施工顺序发生变化的情况,编制多种切实可行的方案。
(2)对于临近交叉洞室开挖,高边墙上开洞口时,尽可能采用小洞贯大洞的方式并预先做好洞口的锁口支护,并按“先洞后墙”的原则进行施工,做好各洞口与厂房相交处的环向预裂。
(3)岩锚梁开挖控制要点:
1)爆破质点振速要求不超过7cm/s。每层拉槽开挖前必须进行周边设计轮廓线预裂。
2)采用预留保护层的开挖方式,保护层与中部槽挖之间采取预裂爆破分开。
3)严格控制钻孔精度。
(4)尾水管后延伸段部位由于挖空率高,加上地质条件差,开挖过程中风险极大,对结构突变位置先进行环向辐射孔预裂,采取导洞、分层开挖的方式,并随层进行一次衬砌支护。