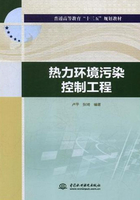
第一节 机械除尘器
机械除尘器通常指利用质量力(重力、惯性力和离心力等)的作用使颗粒物与气流分离的装置,包括重力沉降室、惯性除尘器和旋风分离器。
一、重力沉降室
1.工作机理
重力沉降室又称重力除尘器,是利用重力作用使尘粒从气流中分离出来的装置。含尘气流进入沉降室后,由于流动截面扩大而引起的气流速度降低,使得粉尘颗粒将在重力作用下垂直向下运动,最终落入灰斗。重力沉降室的设计模式有层流(laminar flow)式和紊流(turbulent flow)式两种。层流设计模式是假定沉降室内的气流为处于层流状态,气流流动为柱塞流(plug flow);湍流设计模式是假定沉降室内的气流处于湍流状态,在垂直于气流方向的每个横截面上各种粒径的粒子完全混合(perfect mixing flow)。前者称为层流式重力沉降室,后者称为湍流式重力沉降室。
2.设计模式
(1)层流式重力沉降室。层流式重力沉降室内的气流流速为v0(m/s),颗粒均匀分布在入口烟气中。颗粒的运动轨迹由两个分速度合成:在水平方向,颗粒与气流具有相同的速度;在垂直方向,忽略气体浮力,在重力和流体阻力的作用下,每个颗粒以其末端沉降速度us(m/s)独立沉降。图3-1为层流式重力沉降室及其纵断面的示意图。
根据图3-1,气流在沉降室内的停留时间t为

式中 L、W、H——沉降室的长、宽和高,m;
Q——处理烟气量,m3/s。
在时间t内,粒径为dp的粒子的沉降距离为


图3-1 层流式重力沉降室及其纵断面示意图
(a)简单的重力沉降室;(b) 层流式重力沉降室纵断面
因此,对于粒径为dp的粒子,只有在高度hc以下进入沉降室的粒子才能沉降到灰斗中。当hc<H时,粒子的分级除尘效率为

对于给定的重力沉降室,可按式(3-3)求出不同粒径粒子的分级除尘效率或作出分级效率曲线。根据沉降室入口粉尘的粒径分布,按式(2-85)或式(2-86)即可计算出沉降室的总除尘效率。
对于沉降运动处于斯托克斯区域的颗粒,将式(2-48b)代入式(3-3)可获得其分级效率:

重力沉降室能够100%捕集的最小粒子的粒径dmin为

若要使粒径为dp的粒子达到100%的捕集效率,重力沉降室的最小长度Lmin为

为简化计算和分析,除特别说明外,以后都采用斯托克斯沉降公式。实际上,在293K和101325Pa下,对于颗粒密度ρp=1g/cm3、粒径dp<100μm的粒子,按斯托克斯公式的末端速度的计算值和试验值相当一致。
由于沉降室内的各层速度分布的差别,不可避免地会出现扰动和返混现象,沉降到沉降室底部的粉尘颗粒也会重新扬起。工程上常用式(3-3)计算值的一半作为分级效率,用36代替式(3-4)~式(3-6)中的18,这样理论计算和实际就符合得更好。
从式(3-3)可以看出,提高沉降室除尘效率的主要途径为:降低沉降室气流速度,增加沉降室长度或降低沉降室高度。沉降室内气流速度要根据粉尘颗粒的密度和颗粒粒径来确定,一般采用0.3~2.0m/s。为使沉降室捕集粒径更小的粒子,降低沉降室高度是有效的方法。在沉降室内增设几层水平隔板,形成多层沉降室,此时沉降室的分级效率变为

式中 n——水平隔板层数。
考虑到多层沉降室清灰的困难,实际上一般限制隔板层数在3层以下。
(2)湍流式重力沉降室。当沉降室中的气流处于湍流状态时,各种粒径的颗粒在垂直于气流方向的各个横截面上完全混合,即各种粒径的粒子都均匀分布于气流中。图3-2为湍流式重力沉降室内粒子分离示意图。
在沉降室内取宽度为W、高度为H和长度为dx的捕集单元,假设dy代表边界层的厚度,气流以水平流速v0流动,在气流流过距离dx的时间dt=dx/v0内,边界层内粒径为dp的粒子将沉降到灰斗而从气流中除去,被除去的粒子分数可以简单表示为(Np为粒径为dp的粒子数目)。

图3-2 湍流式重力沉降室内粒子分离示意图
在时间dt=dx/v0内,粒径为dp的粒子以其末端沉降速度us沉降,在垂直方向上沉降的最大距离为,即存在
的关系。对于粒子完全混合系统,比率dy/H是进入边界层且被从气流中除去粒子所占的分数,因此存在以下关系:

式中负号表示随着x的增加粒子数目减少。对式(3-8)积分得

对式(3-9)存在两个边界条件,即在沉降室入口处x=0,Np=Np,0;在沉降室出口处x=L,Np=Np,L,因此有

最后,粒径为dp的粒子的分级除尘效率为

根据分级除尘效率和粒径分布,可以很容易地求得沉降室的总除尘效率。
3.设计和应用
设计重力沉降室时,首先确定气流速度v0,然后根据尘粒的真密度和欲100%捕集尘粒的粒径计算出沉降速度us,再根据确定的沉降室内的气流水平流速v0和沉降室高度H(或宽度W),最后求出沉降室的长度L和宽度W(或高度H),具体步骤如下:
(1)气流水平流速v0的确定。含尘气体在沉降室断面上的水平流速v0可根据含尘气流的临界速度vL来确定,其中vL可按下式计算:

式中 k——流线系数,取值范围为10~20,k值随尘粒直径的减小而递增。
气流水平流速v0一般为临界速度vL的0.5~0.75倍,其值通常在0.3~2.0m/s,不宜大于3m/s。
(2)尘粒末端沉降速度的计算。根据欲捕集粉尘的粒径利用斯托克斯公式(2-48a)计算粒子dp的末端沉降速度us,并结合实际情况进行us的修正和气流流动状态的校核。
(3)确定重力沉降室的尺寸。根据烟气流量和水平流速,计算沉降室的有效截面积A:

再按下列公式依次计算沉降室的高度H、宽度W和长度L,并根据沉降室的长度L决定是否需要设置隔板以及所需设置隔板的层数,并最终确定重力沉降室的结构尺寸。

(4)校核。根据计算出沉降室的结构尺寸进行取整后,利用式(3-5)计算出该沉降室所能捕集的最小尘粒粒径,要求该粒径数值小于等于沉降室需100%去除的最小尘粒粒径。
【例3-1】 设计一锅炉烟气除尘用的沉降室,拟100%去除50μm以上的粉尘。已知烟气量为0.778m3/s,烟气温度为150℃,粉尘密度为2100kg/m3。
解:烟气温度为150℃时,其动力黏度为μ=2.4×10-5Pa·s,密度ρ=0.84kg/m3。
(1)气体流速的确定:

取v0=0.6vL=0.6×1.75=1.05(m/s)。
(2)利用斯托克斯公式计算尘粒的末端沉降速度。

经校验,,属层流区。
考虑到尘粒通过沉降室截面时速度的不均匀性,对上式求得的us进行校正,实际选用:

(3)确定重力沉降室的结构尺寸,其中有效截面积:
高度:

宽度:

长度:

沉降室长度过长,应设置一层水平隔板,即构成两层沉降室,则每层高度为0.3m,此时沉降室长度为

最终沉降室尺寸为:L×W×H=3.21×1.23×0.60(m×m×m)
(4)校核:该沉降室所能捕集的最小尘粒粒径为

45.4μm<50μm,故满足设计要求。
重力沉降室的结构简单,投资少,压力损失小(一般50~130Pa),维修管理容易。一般除尘效率在40%~70%,仅适用于粒径在50μm以上的粉尘,可作为气体的初级净化装置,用于去除气流中最大和最重的尘粒。
二、惯性除尘器
1.除尘机理
惯性除尘器是利用惯性力使尘粒从气流中分离出来的装置。当含尘气流急剧转向或与挡板、百叶窗等障碍物碰撞时,由于粉尘颗粒与气体的密度不同,导致颗粒和气体受到的惯性力不同,颗粒和气流的运动轨迹也将发生偏离,从而使得颗粒从含尘气流中分离出来。图3-3为含尘气流冲击两块挡板时尘粒分离的机理。当含尘气流冲击到挡板B1上时,惯性大的粗尘粒d1首先被分离下来。挡板B2的设置又使得气流方向发生了改变,细尘粒d2将借助离心力的作用被分离下来。若设该点的旋转半径为R2,切向速度为ut,则尘粒d2所受的离心力与成正比。

图3-3 含尘气流冲击两块挡板时尘粒分离的机理
回旋气流的曲率半径越小越能分离捕集细小的粒子。显然,这种惯性除尘器除借助惯性力作用外,还利用了离心力和重力的作用。
2.结构类型
惯性除尘器结构类型多样,可分为以气流中粒子冲击挡板捕集较粗颗粒的冲击式和通过改变气流方向而捕集较细粒子的反转式。冲击式惯性除尘器又可分为单级型和多级型。反转式惯性除尘器则可分为弯管型、百叶窗型和多层隔板型等。图3-4为冲击式惯性除尘装置的示意图。在冲击式惯性除尘器中,沿气流方向设置一级或多级挡板,使气流中的尘粒冲撞挡板而被分离。

图3-4 冲击式惯性除尘装置示意图
(a)单级型;(b)多级型
图3-5为反转式惯性除尘装置的示意图。弯管型和百叶窗型反转式除尘装置与冲击式惯性除尘装置一样,均适用于烟道除尘,多层隔板型的塔式除尘装置主要用于烟雾的分离。

图3-5 反转式惯性除尘装置示意图
(a)弯管型;(b) 百叶窗型;(c) 多层隔板型
3.应用
一般惯性除尘器的气流速度越高,气流转向的曲率半径越小,转变次数越多,则除尘效率就越高,同时阻力也增大。惯性除尘器对于密度和粒径较大的金属或矿物性粉尘具有较高的除尘效率,但对于黏结性和纤维性粉尘,因易堵塞而不宜采用。由于惯性除尘器的净化效率不高,一般用于多级除尘中的第一级除尘,用来捕集10~20μm以上的粗尘粒。惯性除尘器的压力损失一般为100~1000Pa。
三、旋风除尘器
1.工作机理
(1)旋风除尘器内气流与尘粒的运动。旋风除尘器是利用旋转气流产生的离心力使尘粒从气流中分离出来的装置。普通旋风除尘器多数采用切向进气、轴向排气的形式,该除尘器由进气管、筒体、锥体、排出管(内筒)和灰斗组成,其结构形式和内部气流如图3-6所示。
除尘时,含尘气流由进气管切向进入除尘器,气流在旋风筒内沿筒体外层作自上而下的旋转运动,同时少量气体沿径向运动到轴心区域。当旋转气流到达锥体底部后,转而沿轴心向上旋转,最后经排出管排出。通常将旋转向下的外圈气流称为外涡旋,旋转向上的中心气流称为内涡旋,外涡旋与内涡旋的旋转方向相同。
气流做旋转运动时,粉尘颗粒在离心力的作用下移向筒体边壁,并在重力的作用下沿边壁滑落入灰斗,最终通过专用卸灰阀将尘粒排出分离器。
气流从除尘器顶部向下做高速旋转时,顶部压力下降,一般分气流带着细小颗粒沿筒壁旋转向上,到达顶部后,再沿排出管外壁旋转向下,最后到达排出管下端附近被上升的内涡旋带走并从排出管排出,这股旋转气流称为上涡旋。
(2)旋风除尘器内气流的速度分布和压力分布。旋风除尘器内的气流运动很复杂,除了切向和轴向运动外,还存在径向运动。为了研究方便,通常将内、外涡旋气体的运动分解成切向速度、径向速度和轴向速度3个速度分量。
切向速度是决定气流速度大小的主要速度分量,也是决定气流质点离心力大小的主要因素。旋风除尘器内气流的切向速度和压力分布如图3-7所示。

图3-6 普通旋风除尘器的结构及内部气流

图3-7 旋风除尘器内气流的切向速度和压力分布
根据涡流定律,外涡旋的切向速度vT反比于旋转半径R的n次方,即

式中 n——涡流指数,通常n≤1。
实验表明,n值可以由下式进行估算:

式中 D——旋风除尘器直径,m;
T——气体的热力学温度,K。
内涡旋的切向速度vT正比于旋转半径R,比例常数等于气流的旋转角速度ω(rad/s),即

因此,在内、外涡旋的交界圆柱面上,气流的切向速度最大,作用在粉尘颗粒上的离心力也最大。实验测得交界圆柱面直径di可由下式估算:

式中 de——排气管直径,m。
旋转气流的径向速度。因内、外涡旋流的性质不同,导致内、外涡径向速度的矢量方向不同。近似认为外涡旋气流均匀经过内、外涡旋交界圆柱面进入内涡旋,即将外涡旋通过内、外涡旋交界圆柱面的速度视为外涡旋的平均径向速度vr,即

式中 Q——旋风除尘器的处理气量,m3/s;
r0、h0——交界圆柱面上的半径和高度,m。
旋转气流的轴向速度。与径向速度类似,视内、外涡旋而定。外涡旋轴向速度向下,内涡旋向上。内涡旋中,随着气流逐渐上升,轴向速度不断增大,在排出管的底部达到最大值。
图3-7也给出了旋风除尘器内的压力分布。旋风除尘器内,全压和静压的径向变化很显著。全压和静压由外壁向轴向逐渐降低。轴心附近,静压处于负压状态。
2.性能参数
(1)旋风除尘器的分离理论。旋风除尘器从1885年摩尔斯(Morse)申请发明专利投入工业应用至今已有100多年的历史。长期以来,人们对旋风除尘器的分离机理进行了大量的理论和实验研究,概括起来主要包括沉降分离理论(转圈理论)、平衡分离理论(筛分理论)、紊流连续径向混合的分离理论等。
沉降分离理论(转圈理论)是20世纪30年代通过类比平流重力沉降原理而发展起来的。该理论认为,含尘气流进入旋风除尘器后,气流做旋转运动,粉尘颗粒在离心力的作用下抛向边壁,尘粒沉降到除尘器边壁所需的时间和尘粒在分离区间气体停留时间相平衡。旋转圈数越多,气流在旋风除尘器内的停留时间越长,则粉尘到达边壁的数量越多,除尘效率也越高。
平衡分离理论(筛分理论)是斯台尔曼(Stairmand)等人在旋风除尘器内部流场测试和内部流动规律分析的基础上于1956年提出的。该理论认为,在旋风除尘器内,粒子沉降主要取决于尘粒的离心力和向心运动气流作用于尘粒上的流体阻力,并假想在旋风除尘器内部有一张无形的筛网,大于筛网粒径的粉尘被捕集分离出来,而小于筛网粒径的粉尘被气流夹带出去。
紊流连续径向混合的分离理论是雷思(Leith)和利希特(Licht)于1972年通过类比电除尘器的分离机理而提出的。
(2)旋风除尘器的除尘效率。计算分割粒径是确定除尘效率的基础。因假设条件和选用系数不同,所得计算分割粒径的公式也不同。下面以筛分理论为基础介绍一种分割粒径的计算方法。
在旋风除尘器内,粉尘粒子的沉降主要取决于离心力FC和向心运动气流作用于尘粒上的阻力FD。在内、外涡旋界面上,如果FC<FD,粒子在向心气流的作用下进入内涡旋,最后排出除尘器;如果FC>FD,粒子在离心力推动下移向筒体壁面而被捕集。如果FC=FD,作用在粒子上的外力之和等于零,粒子在交界面上不停地旋转。实际上由于各种随机因素的影响,处于这种平衡状态的粉尘颗粒有50%的可能进入内涡旋,50%的可能向筒体壁面运动。可认为其除尘效率为50%,此时的颗粒粒径称为分割粒径,用dc表示。对于处于斯托克斯区域的球形颗粒:

式中 vT0——交界面处气流的切向速度,m/s。
vT可根据式(3-17)计算,vr可由式(3-21)估算,则

dc越小,说明除尘效率越高,除尘性能越好。
当dc确定后,可以根据雷思-利希特(Leith-Licht)模式计算其他粒子的分级效率:

其中涡流指数n可根据式(3-18)确定。最终根据分级效率和粒径分布计算旋风除尘的总除尘效率。
(3)旋风除尘器的压力损失。旋风分离器的压力损失是评价旋风除尘器设计和性能的主要指标,亦称压力降。它与旋风除尘器的结构和运行条件等有关,很难通过理论计算获得,主要靠实验确定。实验表明,旋风除尘器压力损失ΔP一般与气体入口速度的平方成正比,即

式中 ρ——气体的密度,kg/m3;
v1——气体的入口速度,m/s;
ξ——局部阻力系数。
表3-1给出了几种旋风除尘器的局部阻力系数值,可供设计和计算时参考。
表3-1 几种旋风除尘器的局部阻力系数值

需要说明的是,国产旋风除尘器的命名采用拼音字母表示。如XLP/B-4.2型旋风除尘器,X表示旋风除尘器,L表示立式,P表示旁路式,A和B表示产品型号,4.2表示简体直径的分米数值。
在缺少实验数据时,局部阻力系数可用下式估算:

式中 A——旋风除尘器进口面积,m2。
式(3-26)表明,除尘器的相对尺寸对压力损失有较大影响,当除尘器结构形式相同时,几何相似放大或缩小,压力损失基本不变。
应该指出的是,运行操作因素对旋风除尘器的压力损失也有影响。随着入口含尘的增加,除尘器压力损失明显下降,这是因为旋转气流与粉尘的摩擦作用导致旋转速度降低的缘故。除尘器内有叶片、突起和支撑物时,同样可使得气流的旋转速度降低,进而导致压力损失下降。在运行过程中,旋风除尘器可接受的压力损失一般低于2kPa,通常在0.8~1.0kPa左右。
【例3-2】 某型号旋风除尘器筒体直径为0.9m,排气管直径为0.45m,排气管下缘至锥顶的高度为2.58m,入口速度v1=13m/s时的处理气体量Q=1.37m3/s。试确定净化工业锅炉烟气时的分割直径和压力损失(假设烟气温度为423K,烟尘真密度为2.1g/cm3,423K时烟气的黏度μ=2.4×10-5Pa·s)。
解:取内外涡旋交界圆柱的直径di=0.7de=0.7×0.45=0.315m;根据式(3-18),则

假设接近圆筒壁处的气流切向速度近似等于气流的入口速度,由式(3-17),得v1(D/2)n=vTRn=常数,即

由式(3-21)计算径向速度为

根据式(3-23)可得该旋风分离器的切割直径dc为

根据式(3-25)计算旋风除尘器操作条件下的压力损失:

3.影响除尘效率的因素
影响旋风除尘器效率的因素有:二次效应、结构尺寸、气体和烟尘的物理性质和操作变量。
(1)二次效应。图3-8为旋风除尘器分级效率曲线。在旋风除尘过程中,由于被捕集的粒子重新进入气流,即所谓的二次效应,导致实际的分级效率曲线与理论曲线的不一致。在较小粒径区间,理应逸出的粒子由于聚集或被较大粒子撞向壁面而脱离气流获得捕集,实际效率高于理论效率。在较大粒径区间,理应沉入灰斗的颗粒却因反弹或被重新吹起而随净化后的气流一起排走,实际效率低于理论效率。通过环状雾化器将水喷淋在旋风除尘器内壁,可以有效控制二次效应。
(2)结构尺寸。基于大量的实验研究和工程实践,旋风除尘器的各个部件都有一定的尺寸比例,某个比例关系的变动,就会影响除尘效率和压力损失。

图3-8 旋风除尘器分级效率曲线
在同样的切向速度下,筒体直径越小,粉尘颗粒受到的离心力越大,除尘效率也越高。当风量大时,可将多个旋风除尘器并联使用,如多管旋风除尘器,可以保持较高的除尘效率。但筒体直径过小,粒子容易逃逸,使得效率下降。
随着排出筒直径de的减小,内涡旋的范围也随着减小,有利于提高除尘效率。但de太小会造成阻力过大,一般取de=(0.4~0.65)D。
根据测量,气流在除尘器内下降的最低点并不一定能达到除尘器的底部。从排出管下部到气流下降的最低点之间的距离称为旋风除尘器的特征长度l,根据亚历山大(Alexander)公式:

值得注意的是,l与气体流量无关。实际旋风除尘器排出管以下部分的高度应当接近或等于l。增加旋风除尘器的筒体和锥体高度,从直观上看,增加了气流在除尘器内旋转的圈数,有利于提高除尘效率。但实际上由于外涡旋有向心的径向运动,当外涡旋气流自上而下旋转时,气流也会不断进入内涡旋,因此筒体和锥体的总高度过大已没有实际意义。研究数据表明,一般筒体高度以不大于5倍筒体直径为宜。
在锥体部分,由于断面不断减小,气流切向速度不断增大,尘粒到达边壁的距离也在逐渐减小,这些都有利于除尘器的除尘。因此锥体直径可加长一些,有的除尘器其锥体长度为简体长度的2.8~2.85倍。
从除尘器中的压力分布来看,除尘器锥体底部呈负压状态,如果除尘器底部尤其是排灰阀密封不严,渗入外部空气,会把正在落入灰斗的粉尘吸入内涡旋气流,并从除尘器的出口排出,使除尘效率下降。通过测试,当旋风除尘器底部进入10%的空气时,其除尘效率降低到50%以下。因此在不漏风的情况下进行正常排灰是旋风除尘器运行中必须注意的问题。收尘量不大的除尘器,可以在下部设置固定灰斗,定期除灰。收尘量较大的则要求连续排灰,可设双翻板阀或回旋式(星型)锁气器(图3-9)。
(3)气流和烟尘的物理性质。气体的温度和黏度、尘粒的大小和相对密度、烟气含尘浓度等,都影响旋风除尘器的效率。气体温度越低、黏度越小,尘粒粒径越大、密度越大,烟气含尘浓度越高,除尘效率越高。在流量不变的情况下,可以采用下式来估算它们之间的影响。


图3-9 锁气器
(a)双翻板阀;(b) 回旋式(星型)

压力损失与含尘量之间的关系可表示为

式中 ΔPd——随含尘浓度而变化的压力损失,Pa;
ΔPc——干净空气的压力损失,Pa;
C1——入口含尘浓度,g/m3。
(4)操作变量。式(3-23)表明,提高含尘气流入口流速,可减小分割直径dc,进而改善除尘器性能。除尘效率和处理气体量之间的关系可用下式估算:

若入口流速过大,二次效应可能会增强,使得已经沉积的尘粒再次被吹起,重新卷入到气流中。另外,压降与入口流速的平方成正比,入口流速过大,压降损失会急剧上升。卡伦(Kalen)和曾斯(Zens)提出了一个除尘效率最高时的入口速度的经验公式:

实际情况下,旋风除尘器最适宜的入口流速为12~25m/s,与上述结果基本一致。
4.旋风除尘器的结构形式
(1)按进气方式,可将旋风除尘器分为切向进入式和轴向进入式两类,如图3-10所示。切向进入式又分为直入式和蜗壳式。直入式进气管外壁与筒体相切,设计制造方便,性能稳定。蜗壳式进气管内壁与筒体相切,进气管外壁采用渐开线形式,渐开角有180°、270°和360° 3种。蜗壳入口形式易于增大进口面积,减少尘粒向器壁的沉降距离,有利于粒子分离,另外,蜗壳入口还减少进气流与内涡旋气流的相互干扰,降低进口压降。轴向进入式是利用固定的导流叶片促进气流旋转,在压力损失不变的前提下,能够处理的气体流量大,且气流分布均匀,主要用于夺冠旋风除尘器和处理气体量大的场合。

图3-10 旋风除尘器进口形式示意图
(a)直入式;(b)蜗壳式;(c)逆转型;(d)正交式
(2)按气流组织方式,可将旋风分离器分为回流式、直流式、平旋式和旋流式等多种形式,工业锅炉中使用较多的是回流式和直流式两种,这两类除尘器性能也较好,下面作简单介绍。
1)回流式旋风除尘器。在回流式旋风除尘器内,含尘气流由一端进入做旋转运动把尘粒分离,净化后的气流又旋转返回至和进气口相同端排出。它有筒式、旁路式和扩散式等几种形式。
筒式。它是最普通的旋风除尘器,其结构形式如图3-6所示。这种旋风除尘器制造方便,阻力较小,但除尘效率较低。对于10μm左右的粒子的分离效率一般低于60%~70%,虽然曾经应用较为广泛,但已逐渐被其他高效的旋风除尘器所取代。
旁路式。如图3-11(a)所示,这种除尘器采用180°蜗壳进气结构,并在筒体上部设置了旁路隔离室,使得上部灰环中的尘粒(包括部分较细的粒子)得到隔离,直接进入下涡旋而得到清除。这不仅提高了除尘总效率,而且也提高了除尘器对不同尘粒浓度的适应性。但是由于灰尘隔离室容易堵塞,因此要求被处理烟尘中的尘粒要求较好的流动性。

图3-11 回流式旋风除尘器
(a)旁路式;(b) 扩散式
扩散式。如图3-11(b)所示,其主要结构特点是将原来的圆锥改为倒置圆锥体,并在倒置圆锥体下部设置一表面光滑的圆锥形反射屏,反射屏中心开设有小孔。由于反射屏的作用,防止了返回气流重新卷起粉尘,提高了除尘效率。反射屏中心孔径在(0.05~0.1)D时除尘效率最高。
2)直流式旋风除尘器。该种除尘器的特点是,含尘气流由除尘器一端进入,做旋转运动,把粉尘从气流中分离出来,净化后的气体则继续旋转,并从除尘器的另一端排出。这类除尘器内没有上升的内旋气流,减少了返混和二次飞扬,除尘器阻力损失较小,但效率有所下降。
(3)多管旋风除尘器由多个相同构造形状和尺寸的小型旋风除尘器(又称旋风子,直径D为100mm、150mm和250mm)组合在一个壳体内并联使用。当处理烟气量大时,可采用这种组合形式,能够有效捕集5~10μm的粉尘。多管旋风除尘器可用耐磨铸铁铸成,因而可以处理含尘浓度较高(100g/m3)的气体。常见的多管除尘器有回流式和直流式两种。图3-12为回流式多管旋风除尘器,其中每个旋风子都是轴向进气,并需设置等压风箱以保证旋风子进口的气流分布均匀。

图3-12 回流式多管旋风除尘器
5.旋风除尘器的设计选型
目前多采用经验法来选择旋风除尘器的型号和规格,其具体步骤如下:
(1)旋风除尘器选型。根据含尘浓度、粒度分布、密度等烟气特征以及除尘要求、允许的压力损失和制造条件等因素全面分析,合理选择旋风除尘器的类型。在选用旋风除尘器时,应使烟气流量的变化与旋风除尘器适宜的烟气气流速度相适应,以期在工况变化情况下均能满足除尘效率的要求。
(2)确定进口气速v1。根据使用时允许的压力降,确定进口气速:

一般旋风除尘器进口气流速度为12~25m/s。
(3)确定旋风除尘器进口截面积A和矩形尺寸(入口宽度b和高度h)。根据处理气体量Q,由下式确定进口截面积:

(4)确定除尘器规格。依据选定旋风除尘器类型系数,确定除尘器筒体直径D。根据筒体直径D,从国家标准图、产品样本或手册中查到该型除尘器的规格。通常标准图、产品尺寸和手册会给出某一入口气速下的处理气体量,这时可免去步骤(3)的计算过程,直接确定除尘器规格。常用旋风除尘器的主要尺寸比例列于表3-2。
表3-2 几种常用旋风除尘器的主要尺寸比例

① 括号内的数字为出口无蜗壳式的压力损失。
② 进口速度为16m/s时的压力损失。
③ 进口速度为20m/s时的压力损失。
设计者可按要求选择其他的结构,但应遵循以下原则:
(1)为避免粒子短路漏到出口管,h≤s,s为排气管插入深度。
(2)为避免过高的压力损失,b≤(D-de)/2。
(3)为保证涡流的终端在锥体内部,(H+L)≥3D。
(4)为利于粉体滑动,锥角=7°~8°。
(5)为获得最大的除尘效率,de/D≈0.4~0.5,(H+L)/de≈8~10;s/de≈1。
【例3-3】 已知烟气处理量Q=5000m3/h,烟气密度ρ=1.2kg/m3,允许压力损失为900Pa,若选用XLP/B型旋风除尘器,试求该旋风除尘器的主要尺寸。
解:(1)由式(3-32),并按表3-1,取ξ=5.8,则进口气速为

v1的计算值与表3-2的气速与压力降数据基本一致。
(2)根据式(3-33)和表3-2中选定型号旋风除尘器的系数,分别确定除尘器的尺寸。

(3)参考XLP/B产品系列,选取旋风除尘器筒体直径D=700mm,具体型号为XLP/B-7.0,其中7.0表示除尘器筒体直径D的分米数,该除尘器其他主要尺寸为
