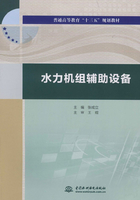
第二节 进水阀的型式及其主要构件
常用的水轮机进水阀主要有蝴蝶阀、球阀、筒形阀和闸阀四种。
一、蝴蝶阀(简称蝶阀)

图1-1 活门绕流示意图
1.工作原理
蝶阀主要是由圆筒形的阀体和可在其中绕轴转动的活门及其他部件组成。蝶阀关闭时,活门四周与阀体接触,切断和封闭水流通路;蝶阀开启时,水流绕活门两侧流过,如图1-1所示。
2.主要类型
根据蝶阀阀轴的布置型式,可把蝶阀分为立轴和卧轴两种,如图1-2、图1-3所示。这两种蝶阀水力性能没有明显差别,均有广泛应用。其各自的特点如下:
(1)立轴蝶阀的阀体组合面一般在水平位置,可就地逐件装拆。而卧轴蝶阀的阀体组合面大多在垂直位置,需要在安装场装配好后,整体吊装就位,故安装和检修复杂一些。
(2)立轴蝶阀的下部轴承容易沉积泥沙,需要定期清洗,否则下部轴承容易磨损,甚至引起活门下沉,影响密封性能。而卧轴蝶阀则无此问题。
(3)立轴蝶阀的操作机构位于阀体的顶部,有利于防潮和运行人员维护检修,但阀体需要一个刚度很大的支座来固定,为支承活门的重量,在下端需装设推力轴承,故结构较为复杂。卧轴蝶阀的操作机构可布置在阀体的一侧或两侧,并可利用混凝土地基做基础,不需支承活门的推力轴承,故结构较简单。

图1-2 立轴蝶阀

图1-3 卧轴蝶阀
(4)立轴蝶阀与卧轴蝶阀相比,布置相对较为紧凑,所占厂房面积要略小一些。
(5)作用在卧轴蝶阀活门上的水压力合力位于阀轴中心线以下,其水力矩有利于活门的动水关闭。部分卧轴蝶阀利用这一水力特性,适当上移阀轴,使活门的下部面积比上部大8%~10%,从而减少操作力矩,缩小操作机构。
由于立轴蝶阀下部轴承容易沉积泥沙,造成的磨损问题很难防止,因此在一般情况下,特别是多泥沙电站,宜优先选用卧轴蝶阀。
重锤式蝶阀在全开位置时,重锤被举至最高点蓄能,并被锁锭,在事故紧急关闭时,重锤释放重力能,迅速关闭截断水流,常用于中小型电站。
3.主要部件
蝶阀的主要部件有阀体、活门、阀轴、轴承、密封装置、锁锭装置和操作机构等。
(1)阀体:为蝶阀的主要部件,呈圆筒形,水流由其中通过,既要承受水压力,支承蝶阀的全部部件,又要承受操作力和力矩,故要有足够的刚度和强度。直径较小、工作水头不高的阀体可采用铸铁铸造,中型阀体多采用铸钢结构,大型阀体则一般采用钢板焊接结构。阀体分瓣与否决定于运输、制造和安装条件。当活门与阀轴为整体结构或不易装拆时,则可采用两瓣组合。直径大于4m的阀体,一般采用两瓣或四瓣组合,分瓣面布置在与阀轴垂直的平面或偏离一个角度。阀体下部设有地脚螺栓,用来承受蝶阀的重量、操作力和力矩,而作用在活门上的水推力则由上游或下游侧的连接钢管传到基础上。因此,在地脚螺栓和孔的配合处,应按水流方向留有30~50mm的间隙,以便于安装和拆卸蝶阀。
(2)活门:活门装于阀体内,在全关位置时要承受全部水压力,在全开位置时处在水流中心且平行于水流,因此不仅要有足够的强度和刚度,而且要有良好的水力性能。图1-4所示为活门的常用形状。菱形活门阻力系数最小,但强度较弱,适用于水头较低的电站;铁饼形活门的断面外形由圆弧或抛物线构成,其阻力系数较菱形和平斜形大,但强度较好,适用于高水头电站;平斜形活门的断面中间部分为矩形,两侧为三角形,其阻力系数介于菱形和铁饼形之间,适用于直径大于4m的分瓣组合蝶阀;双平板形活门两侧各有一块圆形平板,两平板间由若干沿水流方向的筋板连接,在活门全开时两平板之间也能通过水流,故阻力系数小,活门全关时呈箱形结构,密封性能好,刚度大,能承受较大的水压力,但不便做成分瓣组合式结构,一般用于直径小于4m的蝶阀。根据水头高低,活门一般采用铸铁或铸钢结构,大型活门则采用焊接结构,为一中空壳体。
(3)阀轴和轴承:活门在阀体内绕阀轴转动,阀轴大多与活门直径重合,卧轴蝶阀有时也采用偏心结构,以利于动水快速关闭。阀轴与活门的连接方式一般有三种:当直径较小、水头较低时阀轴贯穿整个活门;当水头较高时阀轴分别用螺钉固定在活门上;当活门直径大于4m时,多采用分件组合方式。轴承用于支承阀轴,卧轴蝶阀有左、右两个导轴承,立轴蝶阀除上、下两个导轴承外,在阀轴下端还设有推力轴承,以支承活门重量。轴瓦材料常用铸锡青铜,轴瓦压装在钢套上,钢套用螺钉固定在阀体上,以便于检修轴瓦。

图1-4 活门

图1-5 周圈密封
(4)密封装置:包含活门外圆处的周圈密封和阀体与阀轴连接处的端部密封两种。周圈密封的型式又分为两种,如图1-5所示,一种是依靠阀门关闭的操作力将活门压紧在阀体上的压紧式,常用于小型蝶阀,其活门由全开至全关的转角为80°~85°,密封环采用硬橡胶板或青铜板制成,在与活门密封接触处的阀体上加不锈钢衬板;另一种是空气围带式,常用于直径较大的蝶阀,当活门关闭后,密封环充气膨胀,封住间隙,其活门由全开至全关的转角为90°。常用橡胶围带,一般装在阀体上,当活门关闭后,围带内充入压缩空气而膨胀,封住周围间隙。活门开启前应先排气,待围带缩回后方可开启。充入围带内的压缩空气压力应大于最高水头(不包括水锤升压值)0.2~0.4MPa,在不充气时,围带与活门的间隙为0.5~1.0mm。端部密封的型式很多,效果较好的有青铜涨圈式和橡胶围带式,前者适用于直径较小的蝶阀,后者适用于直径较大的蝶阀。双平板形活门的周圈密封移到阀轴外部,形成一个整圈,并取消了端部密封,所以漏水小,密封性能好。
(5)锁锭装置:蝶阀活门在稍微偏离全开位置时就会产生自关闭的水力矩,为防止因漏油或液压系统事故以及水流冲击作用而引起蝶阀误开或误关,必须装设可靠的锁锭装置,在全开或全关位置时投入该装置,以锁锭阀门位置。
(6)附属部件。
1)旁通管和旁通阀:进水阀一般要求动水关闭,但不要求动水开启,所以一般在蝶阀上均装有旁通管和旁通阀,在蝶阀开启前,先开启旁通阀,对阀后充水,当蝶阀两侧的压力相等后,再在静水中平压开启蝶阀,以减小开启力矩和消除开启振动。旁通管的断面面积一般取蝶阀过流面积的1%~2%,但旁通流量必须大于导叶漏水量。旁通阀一般采用闸阀或针形阀,用液压、电动或手动操作,液压操作用于大直径旁通阀。由于旁通闸阀是在两侧压差较大的动水情况下开启的,在开启的初始阶段闸板振动强烈,故应快速开启旁通闸阀至全开位置,以尽快避开闸板振动区域。
2)空气阀:为了在蝶阀关闭时向阀后补充空气,防止产生真空而破坏钢管,同时,为了在向阀后充水时排出空气,必须在蝶阀下游侧压力钢管的顶部设置空气阀。图1-6所示为空气阀的原理图,空气阀由导向活塞、通气孔和空心浮筒等组成。当蝶阀后水面降低时,空心浮筒下降,使引水管经通气孔与大气相通,实现补气。当蝶阀后充满水时,空心浮筒上浮至极限位置,引水管与大气隔绝,防止水流溢出。

图1-6 空气阀原理图

图1-7 伸缩节
3)伸缩节:在蝶阀的上游侧或下游侧,通常装有伸缩节,使蝶阀能沿水平方向移动一定距离,既可补偿钢管的轴向温度变形,又便于蝶阀的安装和检修。图1-7所示为一种常见的伸缩节结构,伸缩节与蝶阀以法兰螺栓连接,伸缩缝中装有3~4层石棉盘根或橡胶盘根,用压环压紧,以阻止伸缩缝漏水。对岔管输水系统,如岔管外露部分不长,伸缩节最好装设在蝶阀下游侧,以便在不影响其他机组正常运行情况下检修伸缩节。
4.主要特点
(1)结构简单,尺寸较小,重量较轻,造价便宜,操作方便。
(2)能动水关闭,可用作机组快速关闭的保护阀门。
(3)活门对水流流态有一定影响,引起水力损失和空蚀,特别是在高水头下使用时,因活门厚度增大和流速增加而更为明显。
(4)封水性能不如其他阀门,有一定漏水,围带在阀门启闭过程中容易擦伤,会使漏水量增加。
对于重锤式蝶阀,在事故紧急关闭时,还具有先快后慢的关闭特性,能有效控制机组的转速上升和压力钢管的水锤压力上升,是中小型机组安全可靠的后备保护装置。
5.应用范围
蝶阀一般适用在水头250m以下、管道直径1~6m的水电站,更高水头时应和球阀作选型比较。目前已制成的蝶阀最大直径达8.23m,最高水头达300m。
二、球阀
1.工作原理
球阀通常采用卧轴结构,如图1-8所示,在球阀全开时,圆筒形活门的过水断面与压力引水管道直通,相当于一段钢管,对水流几乎不产生阻力,此时工作密封盖位于上部,如图1-8(a)和(b)上半部所示;在球阀全关时,活门旋转90°,由密封装置截断水流,如图1-8(b)的下半部所示。

图1-8 球阀
2.主要部件
球阀的主要部件有阀体、活门、阀轴、轴承、密封装置、操作机构等。
(1)阀体:阀体通常由两件组成,分为偏心分瓣和对称分瓣两种,偏心分瓣的组合面靠近下游侧,阀体地脚螺栓布置在靠上游侧的大半个阀体上,特点是分瓣面螺栓受力均匀,但阀轴与活门必须为装配式,否则活门无法装入阀体;对称分瓣的组合面位于阀轴中线上,如图1-8所示,阀轴与活门可采用整体结构,以减轻重量。阀体多为铸钢件。
(2)活门:活门呈圆筒形,上有一块可移动的球面圆板密封盖,在由其间隙进入的压力水作用下,推动密封盖封住出口侧的孔口,随着阀后水压力的降低,形成严密的密封。由于承受水压的工作面是一球面,改善了受力条件,不仅使球阀能承受更大的水压力,而且还节省了材料,减轻了重量。活门和阀轴为整体结构时,可采用铸钢整铸或铸焊方式。
(3)密封装置:球阀的密封装置有工作密封和检修密封两种,其结构如图1-9所示。工作密封:位于球阀出流侧,由密封环、密封盖等组成,其动作程序为:球阀开启前,先由旁通阀向下游侧充水,同时打开卸压阀,将密封盖2内腔的压力水从孔c排出,随着下游侧水压力的逐渐升高,在弹簧和阀后水压力的作用下,密封盖2逐渐脱离密封环1,这时即可开启活门。相反,当活门关闭后,孔c被卸压阀关闭,上游侧压力水由活门和密封盖护圈4之间的间隙流进密封盖2的内腔,随着下游水压力的下降,密封盖2逐渐突出,直至与密封环1压紧为止。
早期的球阀仅设有工作密封,这样在一些重要的高水头电站通常需设置两个球阀,一个为工作球阀;另一个为检修球阀。现在的球阀一般在上游侧均设有检修密封,用于检修工作密封、阀轴密封和接力器。检修密封有机械操作和水压操作两种,图1-9左上侧所示为机械操作结构,利用螺母6和螺杆5调整密封环7,使其压紧或脱开密封面。由于零件多,操作不方便,易因周围螺杆作用力不均而造成偏卡或动作不灵,故已淘汰。图1-9左下侧所示为水压操作结构,当投入检修密封时,孔a充入压力水,孔b排水,在水压力作用下密封环9向右伸出,紧压在密封面8上;退出检修密封时,孔b充入压力水,孔a排水,密封环9左移,与密封面8脱离。
为了防止生锈,密封装置的活动零件和相应的滑动面一般采用不锈钢材料或加不锈钢保护层。
(4)附属部件:液压操作的球阀一般设有三个液压阀,分别是旁通阀、卸压阀和排污阀,并设有空气阀和伸缩节等部件。卸压阀的作用是在启闭活门时,把密封盖内腔的压力水排至下游,避免密封盖与密封环摩擦。排污阀用来排除积存在球阀壳体内下部的污水。
3.主要特点
(1)承受水压高,关闭严密,漏水极少。
(2)全开时水流条件良好,几乎没有水力损失,密封装置不易磨损。
(3)活门刚性好,动水关闭时振动小,阀门操作力小,动水操作时水阻力只有摩擦力的5%左右,有利于动水紧急事故关闭。

图1-9 球阀的密封装置
1—密封环;2—密封盖;3—密封面;4—护圈;5—螺杆;6—调整螺母;7—密封环;8—密封面;9—密封环
(4)体积大,结构复杂,重量大,造价高,直径较大时尤为显著。为节省投资,可通过采用较高的流速来缩小球阀尺寸。
4.应用范围
球阀一般适用于水头在200m以上、管道直径在2~3m以下的水电站。目前已制成的球阀最大直径为4.96m,最高水头已超过1000m。
三、筒形阀
筒形阀由法国Neyrpid公司1947年提出,1962年首次应用于Monteynard水电站,经过不断的改进与完善,逐步得到越来越多的应用,1993年在我国漫湾电站成功投运。筒形阀在结构、布置和作用等方面均与常规进水阀有一定差异。
1.工作原理
筒形阀主要由筒体、操动机构和同步控制机构组成。筒体安装在水轮机活动导叶与固定导叶之间,其布置如图1-10所示,阀门关闭时,筒体沿环状阀槽落下,与顶盖和底环构成密封面截断水流;开启时筒体被提升到座环与顶盖之间的空腔内,其底部和顶盖下端齐平,不干扰水流的正常流动。筒形阀由多套液压操作机构同时进行操作,并用同步控制机构来保证操作同步性。
2.主要部件
筒形阀的主要部件有筒体、操动机构、同步控制机构和密封装置等。
(1)筒体:筒体是一薄而短的大直径圆筒,常用20号锅炉钢板卷焊制成,其内圆必须略大于剪断销剪断后导叶与限位销相碰时的最大外圆,厚度应满足在关闭行程末端被异物卡住时所产生的不平衡操作力与周围水压力联合作用下的强度和刚度要求。当筒体尺寸较大时,可分瓣制造、运输和现场组装。
在筒体与固定导叶之间一般装有青铜导向板,以对筒体移动进行导向。当筒体被卡住时,应及时切除操作机构的油源,使筒体停止移动。
(2)操动机构:操动机构用于控制筒体上下运动,以启闭筒形阀,一般采用多套操动机构来保证筒体受力均匀,但由于受顶盖上方空间位置的限制,通常对称布置四套操动机构,当筒体直径较大时,可适当增加操动机构数量。
早期的筒形阀,操动机构普遍采用大力矩的低速油压马达作为动力,带动丝杠完成启闭动作,其结构如图1-11(a)所示。由于丝杠和螺母具有自锁功能,故筒形阀可停留在任意位置上。现在的筒形阀,均采用直缸接力器进行操作。
(3)同步控制机构:用于协调各操动机构的操作同步性,使各操动机构动作一致,确保筒形阀启闭平稳,避免在动水关闭时受水流冲击而引起筒体晃动,如图1-11(b)为同步链条方式。

图1-10 筒形阀的布置

图1-11 筒形阀传动原理图
(4)密封装置:为减少漏水量,在筒体与顶盖、底环之间设有密封装置,如图1-12所示。筒体与顶盖之间的密封称为上密封,筒体与底环之间的密封称为下密封。上密封由顶盖底部外缘处带凸缘的环形橡胶板和压板组成,下密封由底环外缘处的环形橡胶条和压板组成。当筒形阀关闭后,上、下缘与密封橡胶压紧,实现止水。压板和内六角螺钉均为不锈钢材质,密封件长度应留有余量,在装配时可按实际情况切割。实践证明这种密封装置止水性能好,使用寿命也较长。
筒形阀的操作力矩、零部件的结构强度和刚度必须满足动水关闭的要求。在动水关闭中,当筒形阀关到约90%行程时,筒体下端面开始脱流,而上端面仍承受动水压力,上下端面的压差即为作用于操作机构上的下拉力,该力可达阀门重量的10倍左右。实验表明,筒体下端面存在一定的倾斜角时,下拉力可显著降低。下拉力随倾斜角的增大而减小,但倾斜角越大,则筒形阀全开时,筒体下端面与顶盖、座环之间过流面的平滑性越差,对水流的影响也就越大。实际应用中倾斜角一般为2°~6°,如漫湾水电站采用4°。
3.主要特点
(1)结构简单,造价便宜,成本仅为蝶阀的1/3~1/2、球阀的1/4,不占用压力引水管道,无伸缩节、连接管、旁通阀和空气阀等附属设备,布置方便,可有效减小厂房宽度和地下电站的土建开挖量,降低电站投资。
(2)全开时不阻碍水流,水力损失小,关闭后封水严密,可有效减轻导叶的间隙空蚀和泥沙磨损,延长导叶的检修周期,对高水头、多泥沙电站或承担调峰调频任务的机组效果尤为明显。

图1-12 筒形阀的密封
(3)操作程序简单,启闭迅速,开启或关闭时间一般不超过60s,事故停机时能提供有效的过速保护,可实现调峰机组的快速启停。
(4)部分零部件加工精度要求高,安装难度大,座环和顶盖等部件需进行适当改造,目前还没有相关的设计、制造和安装标准规范,应用经验也相对较少。
(5)关闭后顶盖处于承压状态,不能用作检修阀门,检修时需要关闭进水闸门,一般不适用于岔管引水电站。
4.应用范围
筒形阀一般适用于水头在60~400m的水电站,特别是水头在150~300m的单元引水式电站,对多泥沙电站或承担调峰调频任务的机组尤为适合。
四、闸阀
1.工作原理
闸阀主要由阀体、阀盖和闸板等组成。关闭时,闸板下移到最低位置,其侧面与阀体接触,切断水流通路,同时,闸板上的密封面依靠操作力和闸板两侧流体的压差实现密封。全开时,闸板沿阀体中的闸槽向上移动至阀盖空腔内,水流通道全部打开,流道直通,水流平顺,水力损失很小。当闸板处于部分开度时,水力损失较大,易引起闸门振动,并可能损伤闸板和阀体的密封面,因此闸阀不宜用作调节或节流,一般只有全开和全关两种工作位置。
2.主要类型
闸阀按操作方式有液压操作、电动操作和手动操作三种,电动和手动操作的闸阀,阀杆上通常设有螺纹,按螺母所处位置不同可分为明杆式和暗杆式两种,如图1-13所示。明杆式的螺母在阀盖外,不与水接触,阀门启闭时,操作机构驱动螺母旋转,使阀杆向上或向下移动,从而使与阀杆连接在一起的闸板也随之启闭。暗杆式的螺母在阀盖内,与水接触,阀门启闭时,操作机构驱动阀杆旋转,使螺母向上或向下移动,从而使与螺母连在一起的闸板也随之启闭。

图1-13 闸阀类型
明杆式闸阀阀杆螺纹和螺母的工作条件较好,但阀杆上下移动,阀门全开时的总高度较大;暗杆式闸阀全开时总高度不变,但阀杆螺纹与螺母受水侵蚀,工作条件较差。作为进水阀使用的闸阀,一般为立式安装。
3.主要部件
闸阀的主要部件有阀体、阀盖、闸板、阀杆和操作机构等。
(1)阀体:阀体是闸阀的承重部件,呈圆筒形,其中通过水流,要求具有足够的强度和刚度,一般采用铸造结构。在阀体上部开有供闸板升降的孔口,内壁上设有与闸板密封的闸槽。
(2)阀盖:阀盖一般为铸造件,其下部与阀体连接,共同构成闸阀开启时容纳闸板的空腔,顶部装有阀杆密封装置,通常采用石棉盘根密封。
(3)闸板:闸板按结构型式分为楔式和平行式两类,如图1-14所示。楔式闸板落于阀体中楔形闸槽内,靠操作力压紧来密封。楔式单闸板结构简单,尺寸小,但配合精度要求高;楔式双闸板楔角精度要求低,容易密封,但结构较复杂;平行式双闸板落于阀体中平行闸槽内,在操作力作用下,通过中心顶锥将两块闸板压紧两侧面来密封,该结构密封面之间相对移动小,不易擦伤,制造维修方便,但结构复杂,将逐渐被楔式闸板取代。大型闸板上一般设有滚轮,以减少闸板移动时的摩擦力,并可设置旁通阀来实现平压启闭。闸板与闸槽接触的部位,通常设铜合金的密封条以改善止水效果。双闸板的闸阀宜直立安装,单闸板的闸阀可任意安装,而且用于水电站的闸阀不宜倒装,以免泥沙沉积。

图1-14 闸板结构
4.主要特点
(1)结构简单,制造工艺成熟,运行维护方便,结构长度较短,便于布置。
(2)全开时,水力损失很小,全关时具有良好的密封性能,漏水量少。
(3)能自锁,不会由于水流冲击而自行开启或关闭。
(4)外形尺寸高,重量大,闸板下部的闸槽易淤积泥沙而导致关闭不严,密封件容易磨损或脱落。
(5)动水关闭时振动较大,操作力矩大,采用手动和电动操作的闸阀启闭时间长,一般仅作为检修阀门,用于截断水流。
5.应用范围
闸阀的适用水头在400m以下,广泛用于压力引水管直径小于1m的小型电站,特别是卧式机组中。