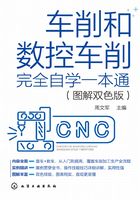
第四节 数控车刀和刀具系统
数控车床加工时,能根据程序指令实现全自动换刀。为了缩短数控车床的准备时间,适应柔性加工要求,数控车床对刀具提出了更高的要求,不仅要求刀具耐磨损、寿命长、可靠性好、精度高、刚性好、耐用度高,而且要求安装、调整、刃磨方便,断屑及排屑性能好。在全功能数控车床上,可预先安装8~12把刀具,当被加工工件改变后,一般不需要更换刀具就能完成工件的全部车削加工,为了满足要求,刀具配备时应注意以下几个问题。
① 在可能的范围内,使被加工工件的形状、尺寸标准化,从而减少刀具的种类,实现不换刀或少换刀,以缩短准备和调整时间。
② 使刀具规格化和通用化,以减少刀具的种类,便于刀具管理。
③ 尽可能采用可转位刀片,磨损后只需更换刀片,增加了刀具的互换性。
④ 在设计或选择刀具时,应尽量采用高效率、断屑及排屑性能好的刀具。
一、数控车削对刀具的要求
1.刀具性能
数控车削对刀具性能的具体要求见表2-22。
2.刀具材料
刀具材料的选择对刀具寿命、加工效率、加工质量和加工成本等的影响很大。刀具切削时,要承受高压、高温、摩擦、冲击和振动等作用。因此,刀具材料应具备以下一些基本性能。
表2-22 数控车削对刀具性能的具体要求

① 硬度和耐磨性 刀具材料的硬度必须高于工件材料的硬度,一般要求在60HRC以上。刀具材料的硬度越高,耐磨性就越好。
② 强度和韧性 刀具材料应具备较高的强度和韧性,以便承受切削力、冲击和振动,以防刀具脆性断裂和崩刃。
③ 耐热性 刀具材料的耐热性要好,能承受高的切削温度,具备良好的抗氧化能力。
④ 工艺性能和经济性 刀具材料应具备好的锻造性能、热处理性能、焊接性能、磨削加工性能等,而且要追求高的性价比。
二、数控车刀的种类及其选用
1.常用数控车刀的种类和用途
常用数控车刀一般分为尖形车刀、圆弧形车刀和成形车刀三类,其说明见表2-23。
2.机夹可转位车刀的选用
机夹可转位车刀是使用可转位刀片的机夹刀具,如图2-29所示。它是由刀垫、刀片和套装在刀杆的夹紧元件(图2-30)组成。夹紧元件将刀片压向支承面而紧固,车刀的前、后角靠刀片在刀杆槽中安装后获得。一条切削刃用钝后可迅速转位换成相邻的新切削刃继续切削,直到刀片上所有的切削刃均已用钝,刀片才报废回收。更换新刀片后,车刀又可继续切削工作。
表2-23 常用数控车刀的种类和用途



图2-29 机夹可转位车刀结构形式

图2-30 可转位车刀的内部结构
可转位刀片是各种可转位刀具最关键的部分。正确选择和使用可转位刀片是使用可转位刀具的重要内容。
① 刀片材质的选择 常见的刀片材料有高速钢、硬质合金、涂层硬质合金、陶瓷、立方氮化硼和金刚石等,其中,应用最多的是硬质合金和涂层硬质合金刀片。选择刀片材料的主要依据是被加工工件的材料、被加工表面的精度、表面质量要求、切削载荷的大小以及切削过程有无冲击和振动等。
② 刀片尺寸的选择 刀片尺寸的大小取决于必要的有效切削刃长度L。有效切削刃长度与背吃刀量ap和车刀的主偏角κr有关,使用时可查阅有关刀具手册选取。
可转位刀片的型号及意义如图2-31所示,代码的具体含义可查阅GB/T 2076—2007《切削刀具用可转位刀片型号表示规则》。
③ 刀片形状的选择 刀片形状主要依据被加工工件的表面形状、切削方法、刀具寿命和刀片的转位次数等因素选择。被加工表面形状及其适用的刀片可参考图2-32选取,图中刀片的型号组成见国家标准GB/T 2076—2007《切削刀具用可转位刀片型号表示规则》。

图2-31 可转位刀片的型号及意义

图2-32 被加工表面形状及其适用的刀片
三、装夹刀具的工具系统选择
数控车床的刀具系统,常用的有两种形式:一种是刀块形式,用凸键定位,螺钉夹紧,该结构定位可靠,夹紧牢固,刚性好,但换装费时,不能自动夹紧,如图2-33所示。另一种是圆柱柄上铣齿条的结构,可实现自动夹紧,换装也快捷,刚性较刀块形式的稍差,如图2-34所示。

图2-33 刀块式车刀系统

图2-34 圆柱柄上铣齿条式车刀系统
四、装刀与对刀
装刀与对刀是数控机床加工中极其重要并十分棘手的一项基本工作。对刀的好与差,将直接影响到加工程序的编制及零件的尺寸精度。通过对刀或刀具预调,还可同时测定各号刀的刀位偏差,有利于设定刀具补偿量。
(一)车刀的安装
在实际切削中,车刀安装得高低,车刀刀杆轴线是否垂直,对车刀角度有很大影响。以车削外圆(或横车)为例,当车刀刀尖高于工件轴线时,因其车削平面与基面的位置发生变化,使前角增大,后角减小;反之,则前角减小,后角增大。车刀安装得歪斜,对主偏角、副偏角影响较大,特别是在车螺纹时,会使牙形半角产生误差。因此,正确地安装车刀,是保证加工质量、减小刀具磨损、提高刀具使用寿命的重要步骤。
如图2-35所示为车刀安装角度示意。图2-35(a)为“-”的倾斜角度,增大刀具切削力;图2-35(b)所示为“+”的倾斜角度,减小刀具切削力。

图2-35 车刀的安装角度
(二)数控车床对刀
对刀是数控机床加工中极其重要和复杂的工作。对刀精度的高低将直接影响到零件的加工精度。
在数控车床车削加工过程中,首先应确定零件的加工原点,以建立准确的工件坐标系;其次要考虑刀具的不同尺寸对加工的影响,这些都需要通过对刀来解决。
1.刀位点
刀位点是指程序编制中,用于表示刀具特征的点,也是对刀和加工的基准点。对于各类车刀,其刀位点如图2-36所示。
2.刀补的设置与测量(表2-24)
表2-24 刀补的设置与测量


3.试切法对刀的步骤
设1号刀为90°外圆车刀,并作为基准刀;2号刀为切槽刀;3号刀为螺纹刀,4号刀为内孔镗刀。其对刀的步骤见表2-25。
表2-25 试切法对刀的步骤

4.工件坐标系建立的步骤
假定程序中工件坐标系设定指令为:G50(G92) X100.0 Z100.0,工件坐标系设置在工件轴线和右端面的交点处。
(1)方法一
① 用1号刀(基准刀)车削工件右端面和工件外圆。
② 让基准刀尖退到工件右端面和外圆母线的交点A,见图2-39所示。
③ 让刀尖向Z轴正向退100mm。
④ 停止主轴转动。
⑤ 用外径千分尺测量工件外径尺寸d。
⑥ 让刀尖向Z轴正向退100-d。
⑦ 则刀尖现在的位置就为程序中G50(G92)规定的X100.0,Z100.0的位置。
(2)方法二
① 让1号刀(基准刀)车削工件外圆,X向不动,刀具沿Z轴正向退出后置零。
② 停止主轴转动。
③ 用外径千分尺测量工件外径尺寸d。
④ 让基准刀刀尖和工件右端面对齐或车削右端面,让刀尖向工件中心运动d数值(若测得工件外径为38mm,刀尖向工件中心运动时,在手动状态下注意CRT显示器上X轴坐标值向工件中心增量进给-38mm时,停止进给)。
⑤ 然后再次将当前X、Z坐标数值置零。
⑥ 将刀尖运动到程序G50(G92)规定的X、Z坐标值。如主程序中编制G50(G92)X100.0 Z100.0,则将刀尖运动到CRT显示器上X、Z轴的坐标值均为100处,当前点即为程序的起始点。
当程序运行加工工件时,执行G50(G92)程序后,系统内部即对当前刀具点(X、Z)进行记忆并显示在显示器上,这就相当于在系统内部建立了一个工件原点为坐标原点的工件坐标系,当前刀具点位于工件坐标系的X100.0,Z100.0处。