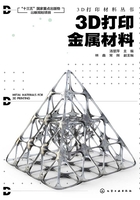
1.2 金属3D打印的发展历史和现状
1.2.1 国外金属3D打印技术发展历史
(1)思想萌芽阶段
DED是最早出现的一类金属3D打印技术,其思想萌芽可追溯到二十世纪二三十年代。1922年,Baker在其专利[14]中描述了一种通过焊接沉积成形装饰性焊接制品的方法,其技术原理与后来发展起来的基于同步送丝的电弧/电子束/等离子定向能量沉积(分别简称DED-A,DED-E,DED-P)技术类似,如图1-7所示。在此后的三四十年内,全球范围内出现了多个源于焊接思想的DED工艺。1972年,Ciraud发明了一种将金属粉末直接送入局部热源熔化沉积成形金属零件的方法,并申请了专利[15](图1-8)。从原理上看Ciraud发明的技术与目前广泛应用的基于同轴送粉的激光定向能量沉积(简称DED-L)技术已经十分接近。除上述技术外,1979年Housholder提出了通过分层铺粉、选区成形三维零件的制造思想[6],这为后来发展起来的激光/电子束PBF工艺提供了技术雏形。然而,受困于当时计算机技术的限制,复杂零件的三维建模及分层切片等数字化模型处理技术在当时还比较困难,上述技术还只能实现简单形状零件的成形。

图1-7 采用焊接沉积法在平板上制备的金属构件(US 42364720A)

图1-8 Ciraud发明的定向能量沉积工艺示意图(Ger.Patent Appl.DE 22 63 777 A1)
1—成形底板;2—粉末;3,3a—局部热源;4—聚焦点;5—成形仓;6,6a—热源发生器;7—送粉器;8—粉仓;9—粉末输送管道;10—泵;11—角度控制器;12—电源;13—电源控制阀
(2)快速成形阶段
20世纪80年代以来,随着计算机技术的进步,现代意义上的金属3D打印技术开始出现。1986年,Deckard在其专利中提出了激光选区烧结(selective laser sintering,SLS)的概念,成形的材料既可以是高分子材料也可以是金属材料。1989年,美国麻省理工学院发明了一类选择性喷射沉积液态黏结剂黏结粉末材料的3D打印工艺,即黏结剂喷射(materials jetting,MJ)技术[16],成形的材料同样既可以是高分子材料也可以是金属材料。然而,受激光、电子束等能量密度低的限制,这一时期的金属3D打印技术还无法实现金属构件的直接制造,成形的零件需要进行脱脂、烧结固化等后续处理。
(3)快速制造阶段
20世纪90年代中期以来,激光、电子束等高能束技术取得飞速发展,能量密度不断提高,金属3D打印逐渐步入高性能复杂金属构件直接快速制造阶段。1995年,德国Fraunhofer激光研究所提出了激光选区熔化(selective laser melting,SLM)成形的技术思想。同年,美国麻省理工学院Dave等提出了利用电子束做能量源将金属丝熔化进行三维制造的设想。2000年,White在Feygin提出的薄材叠层(sheet lamination,SL)制造思想基础上,发明了适用于金属薄材叠层制造的超声波固结成形技术。2001年,瑞典Arcam AB公司申请了利用电子束在粉末床上逐层制造三维零件的专利,即电子束选区熔化(selective electron beam melting,SEBM)技术。2002年,德国EOS公司和瑞典Arcam公司分别推出了SLM和SEBM商业化装备,可成形接近全致密的精细金属零件和模具,其性能可达到同质锻件水平,这标志着金属3D打印由快速成形进入快速制造阶段。
(4)产业化初级阶段
近十年,特别是2012年以来,随着工艺、材料和装备的日益成熟,金属3D打印技术在航空航天、生物医疗等领域的应用逐渐增多,基本进入了产业化的初级阶段。此外,国内外在3D打印的经典理论和方法基础上,又发展了一些新的金属3D打印工艺和方法,如喷墨液态金属3D打印、金属微滴3D打印、冷喷涂沉积、喷射沉积-激光重熔复合成形等,极大丰富和扩大了金属3D打印的材料种类和应用范围。