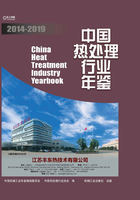
材料表面金属渗扩与渗镀技术发展概况
一、引言
材料表面金属渗扩与渗镀技术是利用不同的能量源(热能或机械能),使不同的金属或合金元素覆盖于钢铁材料表面或扩散进入金属基体,从而形成一层特殊的表面强化层,以提高构件的表面强度及耐腐蚀等性能。材料表面金属渗扩技术主要指渗硼、渗金属工艺,所渗入的金属元素主要有铬、钒、钛、铌、锰、铝和锌等,因渗硼与渗金属的处理方法非常相似,故而常归在一类。这些元素可单独渗入工件表面,或是采用多元共渗或复合渗的方式实现,以进一步提高产品的综合性能。渗镀技术具有“镀”与“渗”的特点,经渗镀工艺处理的构件,其表面既有完整的金属镀层,又有部分金属原子向内扩散形成的渗层,可大幅度提高产品表面的耐磨、耐腐蚀和抗疲劳性能。
钢铁材料零部件普遍存在腐蚀现象,特别是在户外暴露条件下腐蚀更为严重。据报道,全世界每年因金属腐蚀造成的直接经济损失约7000亿美元,我国每年因金属腐蚀造成的损失占当年国民生产总值的4%,而我国工业领域因摩擦磨损造成的损失约为当年GDP的4.5%。因此,钢铁腐蚀与磨损不仅造成外观损害,而且还严重地降低了钢铁材料制品的强度和使用寿命,常因个别零件表面损坏而引起严重的设备损毁和人员伤亡事故。所以,提高材料的表面性能是延长零部件使用寿命、保证系统稳定性的关键。更重要的是,通过表面性能的改善,提高零部件使用寿命和材料使用效率,可以大量节约资源和能源,减少优质材料消耗,降低生产成本,保护环境。
二、材料表面金属渗扩与渗镀技术特点
材料表面金属渗扩工艺是使材料表面强化的一项重要工艺技术,其基本工艺过程是:将工件放入含有渗入元素的活性介质中加热到一定温度,使活性介质分解并释放出欲渗元素的活性原子,活性原子被工件表面吸附并溶入表面,进而向工件表层扩散形成一定厚度的扩散层,辅以后续热处理,最终改变工件表层的成分、组织和性能。渗扩工艺不仅在制造业各个领域所需的表面耐磨、耐腐蚀零部件强化中得到广泛应用,而且在微电子工业和信息产业中也发挥着越来越重要的作用。根据渗剂种类及工艺手段的差异,金属渗扩工艺可分为渗硼、渗金属和TD处理等。
渗硼工艺包括固体粉末渗硼、气体渗硼、膏剂渗硼和盐浴渗硼等,其中固体渗硼因具有操作方便、使用设备简单和质量易控制等优点在生产中得到较广泛的应用。固体渗硼是把工件放入固体渗剂中或用固体渗剂包裹工件加热到一定温度保温,使工件表面渗入硼元素或多种元素的工艺过程。钢经渗硼后,表面有很高的硬度(1300~2300HV)和耐磨性,良好的耐蚀性、抗氧化性和热硬性。固体渗硼工艺简单且处理后工件表面无渗剂残留,具有局部渗硼易于实现等优点。但是,由于渗硼处理的温度较高,渗硼处理后零件的变形较大以及渗层较薄、渗层脆性较大等原因,限制了渗硼技术的推广应用。
利用化学热处理方法将金属(如铬、钒、铌和钛)原子渗入工件表面的工艺称为渗金属,其渗层称为渗金属层,也称为金属碳化物覆层。在渗金属工艺中,渗铬工艺常用于耐腐蚀、抗高温氧化、耐磨损和需提高疲劳强度的工件,适用于钢铁、耐热合金和难熔金属等材料的表面改性处理;渗钛可提高钢铁材料的耐蚀性、表面硬度和耐磨性,提高铜基合金或铝基合金的表面硬度、耐磨性、热稳定性;渗钒、铌工艺主要用于要求有更高硬度、高耐磨性的工件。渗金属技术较多地用于钢铁件,主要是利用铬、钒、铌、钛与碳的亲和力比铁强,能从铁中获得碳原子的能力,形成金属碳化物覆层,在渗入金属向内扩散和基体碳原子向外扩散的双向扩散作用下,渗层厚度比低温渗金属显著增加。通过在金属表面进行钒、铬和铌等渗扩处理,形成的金属碳化物覆层具有超高硬度和很高的耐磨性。TD处理是一种特殊的渗金属技术,它是将工件浸渍在以硼砂熔盐为载体的熔融液体中,使表面渗入一种或几种金属元素的热扩渗工艺方法。经该方法处理后所形成的覆层在常温下具有良好的稳定性、优异的抗磨损能力,在冷作模具和其他一些耐磨零件的表面强化中效果良好。但该方法存在盐浴寿命不高、盐浴腐蚀严重、工件变形大以及表面黏附的盐清理困难等一系列缺点,限制了该工艺的推广应用。
对一些原子半径较小的弱碳化物形成元素的金属渗扩处理,原子的渗入与扩散方式以及渗层结构类似于渗碳(氮)处理工艺。以渗铝、渗锌为例,其最表层为铝(锌)铁合金,次表层为铝(锌)扩散层。渗锌、渗铝层具有比钢铁材料更负的电极电位,在工件上形成一种良好的阴极保护层,该工艺多用于要求有较高耐蚀性的工件。渗锌处理方法与电镀锌方法相比,能够使工件具有更高的表面硬度和耐磨性,是提高金属材料抗大气、水、硫化氢及一些有机介质(如苯、油类)腐蚀能力的经济实用且应用广泛的一种保护方法,如对水管、铁塔型材和螺栓等的处理。渗锌还可提高铜、铝及其合金的表面性能。渗铝工件的耐大气腐蚀性能比渗锌工件更好,是一种既可以保持工件基体韧性,又可以提高工件表面的抗氧化和耐腐蚀能力的化学热处理方法。渗铝还可改善铁基粉末合金、铜合金和钛合金的力学性能。
在渗镀技术中,按照镀层形成过程的界面反应和原子扩散方式可分为机械镀和热浸镀。机械镀是在室温下的液体介质中,依靠冲击载荷、金属粉末的团聚与吸附作用,使金属粉末在基体表面形成沉积成层(镀层)的工艺,镀层的形成过程没有热浸镀过程的界面反应和原子扩散,没有热喷涂过程中的金属粉末烧损、氧化和相变,也没有电镀过程的电解沉积结晶。与传统的电镀、热浸镀和热喷涂等技术相比,机械镀的工艺原理尚不清楚,工艺控制尚不精确,导致其应用领域较为狭窄,成熟应用的镀种单一,在实际生产中仍然存在一些突出问题。
热浸镀是将金属工件浸入熔融金属中获得金属镀层的一种方法。在热浸镀过程中,被镀金属基体与镀层金属之间通过熔解、化学反应和扩散等方式形成冶金结合的合金层。由于热浸镀要求镀层金属熔点低于金属工件熔点,因此常选用钢铁材料作为基材,如钢件的热浸锌和热浸铝。热浸锌是各国公认的一种经济实惠的材料表面保护工艺,其防腐蚀作用是因处于腐蚀环境中的锌可在表面形成致密的保护薄膜,它既减少了锌的腐蚀,又保护了镀锌层下的基材免受损坏。热浸铝层还具有很高的抗高温氧化与抗燃气腐蚀能力,广泛应用于大气、硫化氢、碱、海水以及高温介质中工件的表面防护。
三、国内外材料表面金属渗扩与渗镀技术发展概况
1.渗硼
(1)渗硼发展概况。渗硼工艺有着悠久的历史,1895年,从第一篇渗硼的论文问世,到现在已过去125年。20世纪20年代以前,因人们还未完全认识渗硼的特点,具体操作工艺还存在很多难题需要解决,致使渗硼工艺发展缓慢,几乎没有实际的应用价值。20世纪20~60年代,固体渗硼技术因为一些新渗硼剂的发明而取得了一些进展,在工艺上可以保证所需的渗层厚度,但渗硼剂的价格昂贵,且所需的处理温度高、时间长,迫使人们开始寻找其他的方法。从20世纪60年代开始,盐浴渗硼和电解渗硼引起了人们的极大关注,技术人员开展了大量的研究,相继研究出多种盐浴成分的配比方案和工艺,获得工业应用,并且成功地应用于一些模具和部分易磨损件上,但在实际应用过程中,人们发现用于盐浴渗硼的硼砂熔盐会强烈腐蚀坩埚,且工件表面黏附的残盐不易清洗;此外,盐浴渗硼和电解渗硼后存在工件易变形、渗层厚度不均匀等缺点,促使人们寻找新的工艺解决方案。为寻求既能保证渗硼质量,又符合经济实用要求的新渗硼剂和渗硼工艺,固体渗硼再次得到重视,最早取得成功的是西德的布莱梅硬化技术研究所。在此基础上,美国、日本和苏联等国家相继发表了不少文章,20世纪80年代以后我国在固体渗硼方面的研究也取得了很大成功,现在工业上主要应用的是固体渗硼工艺。
(2)渗硼工艺。依据渗剂介质的物理状态不同,可以将渗硼工艺分为气体渗硼、液体渗硼和固体渗硼三大类。气体渗硼采用的气源为三氯化硼、乙硼烷和三甲基硼,采用850~1000℃工艺处理,一般生成Fe2B单相层。这种工艺的优点是渗层均匀、致密和表面质量好,工艺结束后不必清理。缺点是乙硼烷不稳定,不易控制,并具有爆炸性,三氯化硼易水解,另外,上述气体价格昂贵。因此,气体渗硼基本上用于实验室进行研究,难以实现工业化生产。
液体渗硼包括电解渗硼和盐浴渗硼,但以盐浴渗硼为主。盐浴渗硼常用的渗硼剂是以硼砂为基,加入碳化硅、硅钙合金、硅粉和铅粉等作为还原剂,以碳酸钠、氯化钾、氟化钠和氟硅酸钠等为改善流动性的添加剂,共同组成盐浴渗剂。这种配方具有成本低、盐浴流动性好、有较好的供硼能力,以及便于利用渗剂成分调整控制渗硼层组织等优点。但盐浴渗硼也存在一些缺点,如盐浴的活性差、工件清洗困难、坩埚寿命短,以及在大量生产中很难保证盐浴温度和成分的均匀性等,限制了此方法的应用。
固体渗硼是将工件直接埋入粉末状或粒状的渗硼剂中,或者在零件表面涂上膏状渗硼剂,然后装入渗硼箱中进行适当的密封处理,最后加热到渗硼温度保温,实现表面渗硼处理。固体渗硼主要由供硼剂、催渗剂和填充剂组成,粒状和膏状渗硼剂还含一定比例的黏结剂。常用的供硼剂有碳化硼、硼铁、三氧化二硼和硼砂等;催渗剂一般为卤化物、碳酸盐、稀土化合物或稀土合金,常用的催渗剂有氯化铵、氟硼酸钾、氟硼酸钠、碳酸钠、稀土氯化物等;填充剂一般用碳化硅或氧化铝,其作用主要是防止渗剂板结和渗剂与工件粘结,方便工件取出,并可降低成本。膏体渗硼剂中黏结剂是一些具有不与工件和渗剂发生化学反应的黏性材料,常用的有桃胶水溶液、羧甲基纤维素水溶液等。
2.渗金属
(1)渗锌和渗铝。渗锌和渗铝应用较多的处理方法是粉末法,其处理方法与固体渗硼类似,将经表面清洁处理的工件放入装有粉末渗剂的密封容器中进行加热保温即可,其生产成本低、效率高、操作简单和生产工艺可靠;也可将工件放入装有粉末渗剂的密封旋转炉中进行处理,效率更高,适合批量生产。粉末渗剂一般由供渗剂、催渗剂和填充剂三部分组成。
粉末渗锌的供锌剂主要成分是纯锌粉,加入惰性物质(如氧化铝)以防止渗剂与零件或锌粉之间黏结、改善零件受热状态和渗剂分布的均匀性、提高工件表面质量;催渗剂一般用卤盐,其中用氯化铵的最多。钢铁材料经340~440℃保温2~8h,表面可获得15~100μm的渗锌层。
粉末渗铝的供铝剂为铝粉或铝铁合金粉,供铝剂提供渗铝所需的活性铝原子;催渗剂常用氯化铵;可用氧化铝或高岭土粉末作为填充剂,防止金属粉末黏结、调节渗剂活性。钢铁材料经750~1000℃保温6~10h,表面可获得40~600μm的渗铝层。
(2)TD(Toyota Diffusion)处理。实现金属碳化物覆层,其工艺手段可分为固体法、液体法、气体法和离子轰击法等,离子轰击法受处理装备和技术特性的限制,目前少有规模化应用。固体法和气体法渗金属发明得较早,也有不少工业应用,但影响最大、应用最广的是液体法(即TD处理)。
TD处理是日本丰田中央研究所20世纪60年代末发明的一种表面强化方法。TD处理是将钢铁材料放入含有活性金属原子的高温硼砂熔盐中保温,在材料表面形成几微米到数十微米的碳化物层,也称为硼砂熔盐金属覆层技术。它是一种以提高耐磨性能为主的表面强化技术。目前实际应用最广泛、效果最好的是在工件表面形成VC、NbC、Cr7C3等碳化物覆层。TD处理所得到的碳化物覆层有很高的硬度和耐磨性,其处理设备简单,价格便宜,操作方便,渗层质量稳定,处理后可直接淬火,广泛应用于处理各种模具、剪板刀片、卡盘爪和挤压辊等零件。
TD处理的基本步骤为:零件表面脱脂→预热→盐浴渗金属→淬火、回火→清洗残盐。具体做法是将欲处理的工件置于含有碳化物形成元素(如铬、钒、铌和钛)的高温盐浴中,在850~1050℃保温1~8h,此时基材中所含的碳会向外扩散至表面,与盐浴中的碳化物形成元素结合为碳化物,表面形成碳化物后,出现内外碳浓度的梯度,随着涂覆过程的进行,碳不断向外扩散,使碳化物覆层加厚。
3.机械镀
(1)机械镀发展概况。机械镀是20世纪40~50年代由美国Tainton公司发明的一种涂镀工艺,在该技术刚开始应用时,施镀工件需要用几个小时才能达到期望的镀层厚度,并且金属粉末利用率较低,后来经过一系列技术改进,缩短了施镀时间,提高了金属粉末的利用率,在20世纪70年代以后,机械镀逐步进入发达国家工业生产中,近20年,该技术趋于成熟,逐步在各领域得到认可并应用,取得了一定的经济效益和社会效益。
(2)机械镀工艺。机械镀是将活化剂、金属粉末、冲击介质和一定量的水混合为浆料,与工件一起放入滚筒中,借助于滚筒转动产生的机械能的作用,在活化剂及冲击介质机械碰撞的共同作用下,在铁基表面逐渐形成锌镀层。
典型的机械镀工艺大至可归纳为四个阶段:①表面预处理阶段,去除工件表面油污及氧化物,使工件裸露出金属基体,以利镀覆;②闪镀阶段,为防止铁基体氧化,促进镀层与基体的紧密结合,在镀覆之前,往往要在经预处理的工件表面形成一层较薄的金属层,一般为铜层,而此过程仅需30~90s,习惯上称为“闪铜”;③镀覆阶段,镀覆过程所需金属粉末和活化剂的数量主要取决于工件表面积及镀层厚度;④后处理阶段,镀覆后需进行分离、漂洗、干燥、钝化和密封等处理。镀后工件与介质等的分离通常借助于振动筛与磁分离器进行,分离出的介质可返回滚筒重复使用,而工件则经漂洗、干燥后装箱。如需要,工件可进一步进行钝化处理或用有机物封膜,以提高耐蚀性。
机械镀层是一种由均匀的扁平状金属颗粒组成的镀层。按镀层厚度可分为两类:一类厚度为25.4~88.9μm,称为MG(Mechanical Galvanizing),可代替热镀产品;另一类厚度小于25.4μm,称为MP(Mechanical Plating),可代替电镀产品。这两类镀层除厚度及用途上有所区别外,其他性能基本相同。机械镀层外观为均匀的银白色,但色泽不如电镀层,并有微小的凹凸点;镀层的均匀性、附着力和涂覆能力均较好,这一点对一些具有深洞、沟槽和螺纹的工件尤为重要;镀层耐蚀性良好,高性能的镀层在野外、工业和海洋环境中可提供牺牲阳极保护,可保护构件10~30年或更长时间免于腐蚀。
4.热浸镀
(1)热浸镀发展概况。钢带热浸镀是对钢带进行表面强化和防护处理的一种工艺方法。早在1893年,德国人就发表了关于钢材热镀铝的技术论文,随后,法国、美国也公布了热镀铝的技术专利,但早期的热镀铝工艺过程比较复杂,很难适用于工业化生产。20世纪40~50年代,是钢带热镀铝技术的开发与试生产时期,当时,基本上只有美国在进行工业化生产。50年代,日本开始进行热镀铝钢带的技术研究,英国、法国和联邦德国等也开展了镀铝钢带的技术研究。进入70年代,热镀铝钢带广泛应用于海水及海洋大气环境,结果表明,镀铝钢带具有优良的耐蚀性,因此,其产量急剧增加。从80年代开始,森吉米尔法连续热镀铝工艺向改良森吉米尔法发展,改良的森吉米尔法将原来处理方法的氧化炉加热改为无氧化加热,且加热炉的炉温由原来的400~500℃提高到了1150~1250℃,使得钢带可在短时间内迅速加热至700℃,很快烧掉和挥发掉钢带表面的油污,并在表面形成微氧化膜,缩短了还原退火时间,保证了钢带的前处理表面质量,从而大大提高了机组速度和机组的生产能力。进入21世纪,美钢联法具有电解脱脂、刷洗等前处理和全辐射加热退火工艺等特点,使得热镀铝工艺由改良森吉米尔法向美钢联法发展。
(2)热浸镀工艺。目前,钢管、钢丝和零部件的热浸镀锌一般采用溶剂法。溶剂法的工艺流程为:预镀件→前处理→热浸镀→后处理→成品。在440~470℃热浸锌1~5min,可获得20~100μm的浸锌层;而在700~790℃热浸铝1~5min,可获得80μm左右的浸铝层。浸镀的前处理环节是将镀件表面的油污、氧化物等彻底清除干净,同时还须使制件表面活化,以便制件在浴锅中很快与被镀金属反应,从而获得满意的热浸镀层。镀后处理包括镀层在融化状态下除去多余的锌(铝)液,迅速水冷以防出现灰暗镀层并进行钝化处理与涂防护层。
四、材料表面金属渗扩与渗镀技术的工业应用
在金属的腐蚀与防护领域中,金属渗扩和渗镀工艺处理后的工件表面获得了良好的耐磨、耐蚀性能,因此获得广泛应用。
渗硼技术主要应用在工作条件恶劣的工模具和易磨损的零部件上,其目的是为了提高零部件的耐磨性和使用寿命,降低生产成本,提高经济效益。冷作模具主要的要求是抗磨损,故渗硼非常适合因磨损而失效的模具的处理。对压制耐火砖模具、Cr15钢制硅钢片冲模、5CrMnMo钢热锻模可进行渗硼处理,特别是热冲压冲头、热引伸冲头,经渗硼回火后使用寿命可提高3~6倍。另外,在压铸模方面,用普通碳素钢渗硼替代高合金钢取得了成功。其中,渗层的脆性及渗剂价格昂贵是制约固体渗硼在工业中应用的主要因素。尽可能地获得单一的渗硼层来降低渗层脆性,采用廉价原料配制渗硼剂,并选用最佳的渗剂用量和合理的渗硼工艺,在大幅提高零部件的使用寿命的同时,可大大降低成本。
TD处理的应用范围也很广。在冷锻模方面,比较分别用SKH9钢、硬质合金和具有碳化物覆层的SKD11钢制造的某修边冲头的使用寿命,可以发现:SKH9钢仅使用5000~10000次即发生了显著的黏附现象,硬质合金使用10000~50000次同样显著黏附,而SKD11钢的碳化物覆层冲头的平均使用寿命为54000次,而且很少黏附,制品光洁。用不同材质和工艺制造10号钢正反挤压凸模的使用寿命不同,用SKH9钢的使用寿命为25000次,用超硬合金的为25000次,用超硬合金经碳化物覆层处理后达461000次。对于热锻模,碳化物耐热疲劳性好,使用中很少发生热裂。虽然碳化钒覆层的抗氧化性能不高,但对于钢铁热锻模来说已足够,例如30号钢热锻模用4Cr5MoV钢淬火、回火处理后,使用寿命为20000~30000次,与用SKD61钢淬火回火处理后的寿命相当,而SKD61钢采用TD处理后,使用80000次没有坏。对于压铸模,由于VC、NbC覆层不易粘铝,故适用于铝、锌合金压铸模,特别是对于在浇口附近受高速铝熔液冲刷的芯棒,效果尤为显著,一般可提高寿命几倍到几十倍。
机械镀是为防止金属基体遭受腐蚀而进行的一种涂镀工艺,适合机械镀的产品包括垫片、螺栓、螺母、射钉、膨胀钉和紧固件等,工件的材料可为结构钢、铸铁和粉末冶金等。机械镀已经从在钢铁工件表面形成Zn、Cu、Al和Sn等单一镀层,发展到形成Zn-Al、Zn-Sn、Zn-Al-Sn、Zn-Re、Zn-Ni和Zn-Ti等多元合金镀层。机械镀层对基体材料有防护性、装饰性和提高耐蚀性的作用,并且镀层厚度能根据材料的防腐蚀要求进行调整,以实现防腐蚀与成本的合理控制。机械镀在机械、电力、交通、建筑和五金等行业得到了广泛应用。
热浸镀锌是当今世界上应用最广泛、性能价格比最优的钢材表面处理方法。热浸镀锌产品对钢铁的减缓腐蚀、节能节材起着不可估量和不可替代的作用。热镀钢板具有优良的耐大气腐蚀性、耐热抗氧化性、良好的涂装性和加工成形性,故被作为外壳材料、包装材料和轻型结构材料广泛地应用在建筑、汽车、家电、化工、电力、通信、能源、交通、农牧、水利、军工和民用五金等众多领域。目前,发达国家用于汽车行业的热镀锌板占其总产量的40%以上。随着国内经济的不断发展,尤其是汽车、家电和建筑业的发展,对镀锌带钢的需求也将不断增加。
五、材料表面金属渗扩与渗镀技术的发展趋势
近年来,除了进一步优化工艺、提高产品质量的稳定性外,已开始运用计算机控制和数值模拟方法来研究金属渗扩与渗镀工艺,它们主要是针对以下几个方面开展工作:一是计算机化的质量管理系统应用于金属渗扩与渗镀工艺技术的实际生产运行中,建立系统化、标准化流程及化学表面热处理工艺数据库将是今后工艺研究的方向,这必将具有巨大的研究和经济价值;二是对已有的定性结果建立量化数学模型,系统地描述冶金过程;三是从宏观模拟向微观模拟发展,模拟渗层组织的形成(镀层凝固)以及组织生长过程。
在机械镀方面,其工艺的改进与发展方向主要是金属粉末合金化匹配,寻找高效分散剂,提高覆层的致密性、光亮度和镀覆生产效率,降低成本,实现清洁化生产,进一步延长材料表面的耐腐蚀时间。当然,机械镀的镀层形成机理研究、合金镀层开发、无铬钝化技术研究,仍是工作重点。机械镀具有高效率、低成本、无污染和无氢脆的特点,随着表面处理工业的发展和环保对电镀工艺的限制,作为一种新型的表面处理技术将有较大的发展空间。
节能环保是当今社会所倡导的主题。对热浸镀技术而言,如何适应日趋严格的环境保护政策要求,防止废水、废气、废渣及重金属离子无序排放,是目前需要尽快解决的问题。建立系统、集中和规模化的解决方案,开发新型环保处理助剂迫在眉睫;对渗硼渗金属而言,应向无公害、节能等方向发展,可通过多种形式的复合热处理技术、新型渗剂和催渗技术的开发,有效降低工艺温度,缩短处理周期,减少能耗,解决耗能高和盐浴污染等问题,促进渗硼渗金属技术稳定发展。
〔撰稿人:武汉材料保护研究所有限公司潘邻吴勉〕