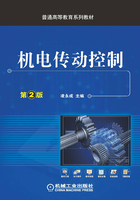
1.2 机电传动系统的动力学分析
1.2.1 机电传动系统的运动方程式
机电传动系统是一个由电动机驱动、通过传动机构带动生产机械运转的整体。尽管电动机种类繁多、性能各异,生产机械的负载特性多种多样,但从动力学的角度去分析,它们都应服从动力学的统一规律。
1.单轴驱动系统运动方程式
如图1-8所示,电动机通过联轴器直接与生产机械相连,由电动机M产生输出转矩TM,用来克服生产机械的负载转矩TL,带动生产机械以角速度ω(或转速n)进行运动。
图1-8 单轴驱动系统
a)系统组成 b)转矩方向
当电动机的输出转矩TM与负载转矩TL平衡时,转速n或角速度ω不变;加速度或角加速度
等于零,即TM=TL,这种运动状态称为静态(相对静止状态)或稳态(稳定运转状态)。
当TM≠TL时,转速或角速度就要发生变化,产生角加速度,速度变化的大小与传动系统的转动惯量J有关。
把上述各种参量的关系用方程式表示出来,则有
式中 TM——电动机的输出转矩(亦称驱动转矩,N·m);
TL——生产机械的负载转矩(N·m);
J——机电传动系统的转动惯量(kg·m2);
ω——机电传动系统的角速度(rad/s);
t——时间(s)。
式(1-1)就是机电传动系统的运动方程式。
在工程计算中,常用转速n代替角速度ω,用飞轮惯量(亦称飞轮转矩)GD2代替转动惯量J来进行系统的动力学分析。
由于
式中 G——机电传动系统的重力(N);
m——机电传动系统的质量(kg);
g——重力加速度(m/s2);
ρ——机电传动系统转动部分的转动惯性半径(m);
D——机电传动系统转动部分的转动惯性直径(m)。
据此,机电传动系统的运动方程式可以转化为更为常用的工程形式:
式中,常数375包含着g=9.81m/s2,因此,常数375具有加速度的量纲;而GD2是一个整体物理量。
工程形式的机电传动系统运动方程式是研究机电传动系统的最基本的方程式,它决定着机电传动系统的动力学特征。
二维码1-4
(1)静态
当TM=TL时,系统的加速度,n为常数。此时,机电传动系统以恒速n运转,机电传动系统处于静态(亦称稳态)。
(2)动态
当TM>TL时,系统的加速度,n不为常数。此时,机电传动系统加速运转,处于加速状态;当TM<TL时,系统的加速度
,n不为常数。此时,机电传动系统减速运转,处于减速状态。
机电传动系统处于加速状态或减速状态时,称系统处于动态(亦称非稳态)。系统处于动态时,系统中必然存在一个动态转矩Td
正是因为动态转矩Td的存在,才使得机电传动系统的运动状态发生了变化。因此,机电传动系统的运动方程式(1-1)和式(1-4)还可以转化为系统的转矩平衡方程式
或者
也就是说,在任何情况下,电动机所输出的驱动转矩TM总是被生产机械的负载转矩(即静态转矩)TL和系统动态转矩Td之和所平衡。
当TM=TL时,Td=0。此时,系统没有动态转矩,系统恒速运转,即系统处于稳态。系统处于稳态时,电动机输出转矩的大小仅由电动机所驱动的负载转矩决定。
2.转矩方向的确定
由于传动系统有多种运动状态,相应的运动方程式中的转速和转矩的方向就不同,因此需要约定方向的表达规则。
因为电动机和生产机械以共同的转速旋转,所以,一般以n(或ω)的转动方向为参考来确定转矩的正负。
(1)TM的符号与性质
当TM的实际作用方向与n的方向相同时(符号相同),TM取与n相同的符号,为驱动转矩;当TM的实际作用方向与n的方向相反时,TM取与n相反的符号,为制动转矩。驱动转矩促进运动;制动转矩阻碍运动。
(2)TL的符号与性质
当TL的实际作用方向与n的方向相同时,TL取与n相反的符号(符号相反),为驱动转矩;当TL的实际作用方向与n的方向相反时,TL取与n相同的符号(符号相同),为制动转矩。
举例:如图1-9所示,电动机拖动重物上升和下降。设重物上升时速度n的符号为正,下降时n的符号为负。
图1-9 TM和TL符号的判定
a)系统起动时 b)系统制动时 c)重物下降时
当重物上升时,TM为正,TL也为正。TM、TL、n的方向如图1-9a所示。此时,系统的运动方程式为
因此,重物上升时,TM为驱动转矩,TL为制动转矩。
当重物在上升过程中制动(图1-9b)时,TM为负,TL为正。此时,系统的运动方程式为
此时,动态转矩和加速度都是负的,它们使重物减速上升,直到停止为止,系统中由动能产生的动态转矩被电动机的制动转矩和负载转矩所平衡。
当重物下降时,TM为正,TL也为正。TM、TL、n的方向如图1-9c所示。此时,系统的运动方程式为
因此,重物下降时,TM为制动转矩,TL为驱动转矩。
3.多轴驱动系统的等效折算
由于许多生产机械都要求在低速状态下工作,而作为原动机的电动机,往往具有较高的额定转速。因此,多数生产机械在电动机与工作机构之间,都设有减速机构(齿轮减速器、蜗轮蜗杆减速器等)和变速机构(机床主轴箱变速器等),借此实现减速、增矩,以适应生产机械的工作要求。因此,在机电传动领域,绝大多数驱动系统实际上都是多轴驱动系统。
为了便于对多轴驱动系统进行运行状态的分析,一般是将多轴驱动系统等效折算为单轴驱动系统,即将多轴驱动系统中各转动部分的转矩和转动惯量或直线运动部分的质量折算到某一根轴(一般折算到电动机的输出轴)上,将其转化为等效的单轴驱动系统之后,再进行系统动力学分析。
负载转矩、转动惯量和飞轮转矩等效折算的基本原则:折算前的多轴系统和折算后的单轴系统在能量关系或功率关系上保持不变,即遵循能量守恒原则或功率守恒原则。
二维码1-5
1.2.2 机电传动系统的负载特性
前面讨论的机电传动系统运动方程中,负载转矩TL可能是常数,也可能是转速的函数。把同一轴上负载转矩与转速之间的函数关系称为机电传动系统的负载特性。
机电传动系统的负载特性就是生产机械的负载特性,有时也称为生产机械的机械特性。如无特别说明,在本书中,机电传动系统的负载特性均指折算到电动机输出轴上的负载特性。
不同类型的生产机械在运动中受阻的性质是不同的,其负载特性曲线的形状也有所不同,大致可分为恒转矩型负载特性、离心式通风机型负载特性、直线型负载特性和恒功率型负载特性等几种。
1.恒转矩型负载特性
这一类型负载特性的特点是负载转矩为常数,如图1-10和图1-11所示。依据负载转矩与运动方向的关系不同,恒转矩型负载特性可分为反抗性转矩和位能性转矩两种。
(1)反抗性转矩
由摩擦、非弹性体的压缩、拉伸与扭转等作用所产生的负载转矩称为反抗性转矩,又称为摩擦性转矩。反抗性转矩的方向恒与运动方向相反,阻碍运动;反抗性转矩的大小恒定不变。
图1-10 反抗性转矩的负载特性
图1-11 位能性转矩的负载特性
根据转矩正方向的约定可知,反抗性转矩与转速n的方向相反时取正号,即n为正方向时,TL为正,特性在第一象限;n为负方向时,TL为负,特性在第三象限(图1-10)。
(2)位能性转矩
位能性转矩是由物体的重力或弹性体的压缩、拉伸、扭转等作用所引起的负载转矩。位能性转矩的大小恒定不变,作用方向不变,与运动方向无关,即在某一方向阻碍运动而在另一方向促进运动(图1-11)。
卷扬机起吊重物(图1-12)时,由于重力的作用方向永远向着地心,所以,由它产生的负载转矩永远作用在使重物下降的方向。当电动机驱动重物上升时,TL与n的方向相反;当重物下降时,TL和n的方向相同(图1-11)。
图1-12 卷扬机起吊重物
假设n为正,TL阻碍运动;则n为负时,TL一定促进运动,其特性在第一、四象限。
不难理解,在运动方程式中,反抗性转矩TL的符号总是与n相同;位能性转矩TL的符号则有时与n相同,有时与n相反。
2.离心式通风机型负载特性
离心式通风机型机械是按离心力原理工作的,如离心式鼓风机、水泵等,其负载转矩TL的大小与转速n的二次方成正比(因此,这类负载特性又称为二次方特性),即
式中 T0——摩擦阻力矩;
C——常数。
离心式通风机型机械的负载特性曲线(最初是沿着虚线变化的)如图1-13所示。
3.直线型负载特性
直线型负载的负载转矩TL的大小与转速n的大小成正比,即
式中 C——常数。
直线型负载的特性曲线如图1-14所示。
图1-13 离心式通风机型负载特性曲线
图1-14 直线型负载特性曲线
4.恒功率型负载特性
恒功率型负载的负载转矩TL的大小与转速n的大小成反比,即
式中 C——常数。
例如,机床在进行金属切削加工过程中,粗加工时,切削量大,吃刀量大,负载转矩TL大,机床主轴低速运转,转速n低;精加工时,切削量小,吃刀量小,负载转矩TL小,机床主轴高速运转,转速n高。但不管是粗加工还是精加工,负载转矩TL与转速n的乘积为常数,即功率恒定不变。
恒功率型负载的特性曲线如图1-15所示。
在实际的生产机械中,负载特性可以是单一类型的,也可以是几种类型的复合。
图1-15 恒功率型负载特性曲线
1.2.3 机电传动系统的稳定运行
在机电传动系统中,电动机与生产机械连成一体,为了使整个系统运行合理,就要使电动机的机械特性与生产机械的负载特性尽量相匹配。特性配合的基本要求是系统能够稳定运行。
1.机电传动系统稳定运行的含义
1)机电传动系统应能以一定速度匀速运行。
2)机电传动系统受某种外部干扰作用(如电压波动、负载转矩波动等)而使运行速度发生变化,应保证系统在干扰消除后能恢复到原来的运行速度。
2.机电传动系统稳定运行的条件
(1)必要条件
如图1-16所示,电动机的输出转矩TM和负载转矩TL大小相等,方向相反。从T-n坐标上看,就是电动机的机械特性曲线n=f(TM)和生产机械的机械特性曲线n=f(TL)必须有交点,其交点称为平衡点。
(2)充分条件
机电传动系统受到干扰后,要具有自动恢复到原平衡状态的能力,即:当干扰使速度上升时,有TM<TL;当干扰使速度下降时,有TM>TL。这是机电传动系统稳定运行的充分条件。符合稳定运行条件的平衡点称为稳定平衡点。
图1-16 稳定工作点的判别
机电传动系统稳定运行的充分必要条件也可表述如下。
1)电动机的机械特性曲线n=f(TM)和生产机械的机械特性曲线n=f(TL)有交点。
2)。
分析举例:在图1-16中,曲线ABC是三相异步电动机的机械特性曲线,铅垂线2-TL和是负载的机械特性曲线。下面分析a、b两点是否为稳定平衡点。
对于a点,有TM-TL=0。当负载突然增加后,有,转速会由先前的na下降到
,系统工作点会由先前的a点漂移到a′点。在a′点,系统建立起新的转矩平衡关系,有
,因此,系统会在a′点稳定运行。当负载波动消除后,有
,系统会自动加速,转速由
上升到na,并在a点建立起新的转矩平衡关系,即TM-TL=0,因此,系统会重新在a点稳定运行,故a点为系统的稳定平衡点。
按照同样的分析方法,依据特性曲线的变化关系进行分析,可知b点不是稳定平衡点。对此,读者可自行分析。提示一点:重点观察负载波动后,系统能否自动建立起新的转矩平衡关系。
二维码1-6
1.2.4 机电传动系统的过渡过程
在实际工作中,机电传动系统具有两种运行状态,即静态(稳态)和动态(暂态)。处于静态时,系统的动态转矩为0,电动机以恒速运转;处于动态时,系统的动态转矩非0,电动机速度处于变化之中。
当机电传动系统中电动机的驱动转矩TM或负载转矩TL发生变化时,系统就要由一个稳定运行状态变化到另外一个稳定运行状态,这个变化过程称为过渡过程。
在过渡过程中,电动机的转速、转矩和电流都会按照一定的规律变化,它们都是时间的函数。
1.过渡过程的影响
生产机械对机电传动系统的过渡过程都有各自的、多样化的要求。
如龙门刨床的工作台、可逆式轧钢机、轧钢机的辅助机械等,它们在工作中需要经常进行起动、制动、反转和调速。因此,都要求过渡过程尽量快,以缩短非生产时间,提高生产率。
升降机、载人电梯、地铁、铁路机车、有轨电车等生产机械和运输设备,则要求起动、制动过程平稳、顺滑,加减速度变化不能过大,以保证安全生产和乘坐舒适性。
而造纸机、印刷机等生产机械,则必须限制其加速度的大小,以确保产品质量。如果加速度超过允许值,则可能损坏机器部件或造成产品质量下降。
在过渡过程中,能量损耗的大小、系统的准确停车与各部分协调运转等方面,都对机电传动系统的过渡过程提出了不同的要求。
为满足上述要求,必须研究过渡过程的基本规律,研究系统各参量对时间的变化规律,如转速、转矩、电流等对时间的变化规律。这样,才能正确地设计、选择机电传动系统,为机电传动系统的自动控制提出控制原则,设计出完善的起动、制动等自动控制电路,以求改善产品质量,提高生产效率和减轻劳动强度。这就是研究机电传动系统过渡过程的目的和意义所在。
二维码1-7
2.过渡过程分析
机电传动系统之所以存在过渡过程,是因为存在以下惯性。
(1)机械惯性
机械惯性反映在转动惯量J或飞轮转矩GD2上,机械惯性的存在使转速n不能发生突变。
(2)电磁惯性
电磁惯性反映在电枢回路电感和励磁绕组电感上,电磁惯性的存在使电枢回路电流Ia和励磁磁通Φ不能突变。
(3)热惯性
热惯性反映在温度上,热惯性的存在使温度不能突变。
这三种惯性在机电传动系统中是互相影响的。如电动机运行发热时,电枢绕组和励磁绕组的电阻都会变化,从而会引起电枢电流Ia和磁通Φ的变化。
由于热惯性较大,温度变化较转速、电流等参量变化要慢得多,一般可不考虑,而只考虑机械惯性和电磁惯性。
由于存在机械惯性和电磁惯性,当对机电传动系统进行控制(如起动、制动、反向和调速)、系统的电气参数(如电压、电阻、频率)突然发生变化、传动系统的负载突然发生变化时,传动系统的转速、转矩、电流、磁通等不能马上跟着变化,其变化都要经历一定的时间,因而形成机电传动系统的电气机械过渡过程。
在有些情况下,如直流他励电动机电枢回路不串接电感,电磁惯性影响也不大,则只考虑机械惯性。在这种过渡过程中,仅转速n不能突变,电枢电流Ia和转矩TM是可以突变的。
研究过渡过程的方法,一般是先列出反映变化规律的基本方程式,在此基础上使用数学解析法,或者使用图解法及实验方法来求得过渡过程的解答。
3.机电时间常数
深入的理论研究和数学分析表明,机电传动系统过渡过程的时间长短,与系统的飞轮转矩GD2和速度变化量成正比,而与动态转矩成反比。在这里,要引入一个反映机电传动系统机械惯性的物理量——机电传动系统的机电时间常数τm。
τm是反映机电传动系统机械惯性的物理量,通常称为机电传动系统的机电时间常数。τm是指系统转速达到稳态值的63.2%所经历的时间。
式中 τm——机电时间常数(s);
n0——理想空载转速(r/min);
Tst——系统的起动转矩(N·m);
GD2——系统的飞轮转矩(N·m2)。
对于既定的机电传动系统而言,其Tst和GD2值为常数。
机电时间常数τm直接影响机电传动系统过渡过程的快慢。τm大,则过渡过程进行得缓慢,过渡过程历时时间长;反之,τm小,则过渡过程进行得快捷,过渡过程历时时间短。所以,τm是机电传动系统中一个非常重要的动态参数。
4.加快过渡过程的方法
由式(1-13)可知,要想有效地缩短机电传动系统的过渡过程,应设法降低GD2值和提高动态转矩Td值(在系统起动过程中,系统的起动转矩Tst实际上就是系统的驱动转矩TM与负载转矩TL的差值,亦即系统的动态转矩Td)。
(1)降低系统的GD2值
机电传动系统的飞轮转矩GD2值中,大部分是电动机转子的GD2,因此,降低电动机GD2值,就成为加快过渡过程的关键措施之一。
在系统结构和条件允许的情况下,采用两台电动机同轴驱动系统生产机械,或者直接采用小惯量电动机,均可有效降低机电传动系统的GD2值。
1)两台电动机同轴驱动。例如,龙门刨床采用两台电动机同轴驱动工作台,其目的之一就在于此。如用一台46kW、转速为580r/min的直流电动机驱动工作台,则GD2为216N·m2;但采用两台23kW、转速为600r/min的直流电动机同轴驱动工作台,则GD2仅为184N·m2。与采用一台电动机相比,系统的GD2值减小了15%,使过渡过程得以显著加快。
2)采用小惯量电动机。小惯量电动机的电枢轴做得细而长,转动惯量小,且起动转矩大,起动快,从而能够加速过渡过程,提高系统的快速响应性能。
(2)提高动态转矩Td值
提高系统的动态转矩Td值,可以从电动机的选择和控制系统的设计两方面采取措施。
1)合理选择电动机。目前,大惯量直流电动机(亦称宽调速直流力矩电动机)已在很多场合下取代小惯量直流电动机。大惯量直流电动机的电枢做得短而粗,GD2值较大(缺点),但其最大转矩Tmax为额定转矩TN的5~10倍(优点),因此,大惯量直流电动机的快速响应性指标Tmax/GD2仍然很好,并不比小惯量电动机差。
大惯量直流电动机低速时转矩大,可以不用齿轮减速机构,直接驱动生产机械,也更容易与生产机械匹配。由于大惯量直流电动机省掉了齿轮减速机构,结构大大简化,没有齿隙的存在,使系统传动精度得以显著提高。
另外,因电枢粗短,散热良好,大惯量直流电动机的过载持续时间可以很长,性能好的大惯量直流电动机可在3倍于额定转矩(或电流)的过载条件下持续工作30min以上而不发生损坏。因此,大惯量直流电动机在快速直流驱动系统中已得到广泛应用。
2)优化控制系统的设计。动态转矩Td越大,系统的加速度也越大,过渡过程的时间也就越短,系统的响应性也就越好。所以,希望在整个过渡过程中,电流(或转矩)大,以加快系统的过渡过程,但又要限制其最大值,使其不超过电动机所允许的最大电流Imax(或最大转矩Tmax)。
为此,引入充满系数的概念——充满系数K表征在过渡过程中,电动机的起动电流与最大电流的接近程度。
充满系数K越接近于1越好。若K=1,则说明在整个动态过程中,电动机的工作电流保持在最大值不变,亦即动态转矩保持最大值不变,从而可以获得最短的过渡过程。在机电传动控制系统中,将在充满系数K=1的条件下完成的过渡过程称为最优过渡过程。
例如,采用电枢串电阻多级起动的方法,其目的就是获得较大的平均起动转矩。起动电阻的级数越多,充满系数K值越大,起动就越快。
再如,在晶闸管供电的直流驱动控制系统中,电流调节器的整定原则是尽量保证电枢电流波形在起动和制动过程中近似为矩形,从而使过渡过程最短,以接近最优过程。