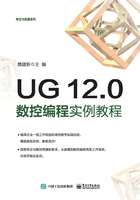
4.数控编程过程
1)进入UG加工环境
(1)在横向菜单中先单击“应用模块”选项卡,再单击“加工”命令。
(2)在【加工环境】对话框中选择“cam_general”选项和“mill_contour”选项,单击“确定”按钮,进入UG加工环境。此时,实体上出现两个坐标系:基准坐标系和工件坐标系,这两个坐标系重合在一起。
(3)在屏幕左上方的工具条中单击“几何视图”按钮,如图3-21所示。

图3-21 单击“几何视图”按钮
(4)在“工序导航器”中展开的下级目录,双击“
WORKPIECE”选项。
(5)在【工件】对话框中单击“指定部件”按钮,在绘图区选择整个实体,单击“确定”按钮。单击“指定毛坯”按钮
,在【毛坯几何体】对话框中,对“类型”选择“包容块”选项,把“XM-”、“YM-”、“XM+”、“YM+”、“ZM+”值都设为1mm。
2)创建ϕ12mm立铣刀与ϕ6mm立铣刀
(1)单击“创建刀具”按钮,在【创建刀具】对话框中,对“刀具子类型”选择“MILL”图标
、“名称”选择“D12R0(铣刀-5参数)”选项,单击“确定”按钮。
(2)在【铣刀-5参数】对话框中,把“直径”值设为12mm、“下半径”值设为0mm。
(3)按照上述方法,创建D6R0立铣刀,把“直径”值设为6mm、“下半径”值设为0mm。
3)创建边界面铣刀路(粗加工程序)
(1)单击“创建工序”按钮,在弹出的【创建工序】对话框中,对“类型”选择“mill_planar”选项。在“工序子类型”列表中单击“带边界面铣”按钮
,对“程序”选择“NC_PROGRAM”选项、“刀具”选择“D12R0(铣刀-5参数)”选项、“几何体”选择“WORKPIECE”选项、“方法”选择“METHOD”选项,如图3-22所示。设置完毕,单击“确定”按钮。
(2)在【面铣】对话框中单击“指定面边界”按钮,在【毛坯边界】对话框中,对“选择方法”选择“面”,在实体上选择台阶面,如图3-23所示。

图3-22 设置【创建工序】对话框参数

图3-23 在实体上选择台阶面
(3)在【毛坯边界】对话框中,对“刀具侧”选择“内侧”选项、“平面”选择“指定”选项,选择实体最高位,在【毛坯边界】对话框中勾选“余量”复选框。在“列表”栏中选择“Inside”(内侧)选项,把“余量”值设为3.0000(单位:mm),如图3-24所示;在“列表”栏中选择“Outside”(外侧)选项,把“余量”值设为5.0000(单位:mm),如图3-25所示。设置完毕,单击“确定”按钮。
提示:这里的余量是指加工轮廓的范围放大还是缩小。

图3-24 在【毛坯边界】对话框中设置“Inside”余量

图3-25 在【毛坯边界】对话框中设置“Outside”余量
(4)在【面铣】对话框中设置“刀轨设置”选项卡参数,对“方法”选择“METHOD”选项,对“切削模式”选择“往复”选项、“步距”选择“刀具平直百分比”选项;把“平面直径百分比”值设为75.0000(%)、“毛坯距离”值设为3.0000(单位:mm)、“每刀切削深度”值设为0.5000(单位:mm)、“最终底面余量”值设为1.0000(单位:mm),如图3-26所示。
(5)单击“切削参数”按钮,在弹出的【切削参数】对话框中,单击“策略”选项卡,对“切削角”选择“指定”选项、把“与XC的夹角”值设为0。单击“余量”选项卡,把“部件余量”值设为0.2mm,单击“确定”按钮。
(6)单击“非切削移动”按钮,在弹出的【非切削移动】对话框中单击“进刀”选项卡,在“开放区域”列表中,对“进刀类型”选择“线性”选项,把“长度”值设为5mm,“高度”值设为3mm、“最小安全距离”值设为8mm。
(7)单击“进给率和速度”按钮,在弹出的【进给率和速度】对话框中,把主轴速度值设为1000 r/min、切削速度值设为1200 mm/min。
(8)单击“生成”按钮,生成的面铣刀路如图3-27所示。

图3-26 设置“刀轨设置”选项卡参数

图3-27 生成的面铣刀路
(9)在辅助工具条中单击“前视图”按钮,切换视图方向。从前视图中可以看出刀路与实体相距1mm,如图3-28所示。
提示:这里出现的1mm就是“最终底面余量”。

图3-28 前视图所示刀路
(10)在“工序导航器”中双击选项,在【面铣】对话框中把“最终底面余量”值设为0.1mm。重新生成的刀路与实体贴在一起,如图3-29所示。
(11)在“工序导航器”中双击选项,在【面铣】对话框中单击“指定面边界”按钮
,在【毛坯边界】对话框中,删除“列表”栏Outside所在的行,重新生成的刀路如图3-30所示,这是因为已经删除了内边界。

图3-29 刀路与实体贴在一起
(12)如果在图3-24中把“余量”值改为30mm,那么重新生成的刀路如图3-31所示(改变加工范围)。这里的余量是指范围,正值代表扩大,负值代表缩小。

图3-30 重新生成的刀路

图3-31 把“余量”值改为30mm后重新生成的刀路
4)创建外形铣削刀路(粗加工程序)
(1)单击“菜单|插入|工序”命令,在【创建工序】对话框中,对“类型”选择“mill_planar”选项;在“工序子类型”列表中单击“平面铣”按钮,对“程序”选择“NC_PROGRAM”选项、“刀具”选择“D12R0(铣刀-5参数)”选项、“几何体”选择“WORKPIECE”选项、“方法”选择“METHOD”选项,如图3-32所示。设置完毕,单击“确定”按钮。
(2)在【平面铣】对话框中单击“指定部件边界”按钮,在【部件边界】对话框中,对“选择方法”选择“曲线”选项、“边界类型”选择“封闭”选项、“刀具侧”选择“外侧”选项,如图3-33所示。

图3-32 设置【创建工序】对话框参数

图3-33 设置【部件边界】对话框参数
(3)选择实体台阶面的内边线,如图3-34所示。
(4)在【部件边界】对话框中,对“平面”选择“指定”选项,选择实体的顶面,把“偏移距离”值设为0mm。设置完毕,单击“确定”按钮。
(5)在【平面铣】对话框中单击“指定底面”按钮,选择实体的台阶面。
(6)在【平面铣】对话框中,对“方法”选择“METHOD”选项,对“切削模式”选择“轮廓”选项、“步距”选择“恒定”选项,把“最大距离”值设为10.0000mm、“附加刀路”值设为1,如图3-35所示。

图3-34 内边线被加强显示

图3-35 设置“刀轨设置”选项卡
(7)单击“切削层”按钮,在弹出的【切削层】对话框中,对“类型”选择“恒定”选项,把“公共”值设为0.5mm。
(8)单击“切削参数”按钮,在弹出的【切削参数】对话框中,单击“策略”选项卡,对“切削方向”选择“顺铣”选项、“切削顺序”选择“深度优先”选项。单击“余量”选项卡,把“部件余量”值设为0.3mm、“最终底面余量”值设为0.2mm,把“内公差”值和“外公差”值都设为0.01mm。
(9)单击“非切削移动”按钮,在弹出的【非切削移动】对话框中,单击“转移/快速”选项卡。在“区域之间”列表中,对“转移类型”选择“安全距离-刀轴”选项;在“区域内”列表中,对“转移方式”选择“进刀/退刀”选项、“转移类型”选择“直接”选项。单击“进刀”选项卡,在“开放区域”列表中,对“进刀类型”选择“圆弧”选项,把“半径”值设为3.0000mm、“圆弧角度”值设为90.0000(单位:°)、“高度”值设为0.0000mm、“最小安全距离”值设为10.0000 mm。单击“退刀”选项卡,对“退刀类型”选择“与进刀相同”选项,如图3-36所示。
(10)单击“起点/钻点”选项卡,把“重叠距离”值设为3.0000mm,对“指定点”选择“控制点”图标,如图3-37所示。选择实体左下角1条边的中点作为起点。
(11)单击“进给率和速度”按钮,在弹出的【进给率和速度】对话框中,把主轴速度值设为1000 r/min、切削速度值设为1200mm/min。
(12)单击“生成”按钮,生成的加工台阶面刀路如图3-38所示。
(13)在“工序导航器”中选择选项,单击鼠标右键,在快捷菜单中单击“复制”命令。再次选择
选项,单击鼠标右键,在快捷菜单中单击“粘贴”命令。

图3-36 设置“进刀”选项卡参数

图3-37 设置“起点/钻点”选项卡参数
(14)在“工序导航器”中双击选项,在【平面铣】对话框中单击“指定部件边界”按钮
。
(15)在【部件边界】对话框中,单击“移除”按钮。
(16)选择实体台阶面,单击“确定”按钮,选择台阶面的外边线。
(17)在【部件边界】对话框中,对“平面”选择“指定”选项,选择实体的台阶面,单击“确定”按钮。
(18)在【平面铣】对话框中单击“指定底面”按钮,选择实体的下底面,把“距离”值设为0mm,单击“确定”按钮。
(19)在【平面铣】对话框中,把“附加刀路”值设为0。
(20)单击“生成”按钮,生成的加工台阶外形刀路如图3-39所示。

图3-38 生成的加工台阶面刀路

图3-39 生成的加工台阶外形刀路
(21)在“工序导航器”中选择选项,单击鼠标右键,在快捷菜单中单击“复制”命令。再次选择
选项,单击鼠标右键,在快捷菜单中单击“粘贴”命令。
(22)在“工序导航器”中双击选项,在【平面铣】对话框中单击“指定部件边界”按钮
,在弹出【部件边界】对话框中,单击“移除”按钮
。
(23)在【部件边界】对话框中,对“选择方法”选择“面”选项,对“刀具侧”选择“内侧”选项,如图3-40所示。
(24)选择实体的底面,单击“确定”按钮,系统自动选择实体底面的边线。
(25)在【部件边界】对话框中,对“平面”选择“指定”选项,选择实体的上表面,把“距离”值设为0mm,单击“确定”按钮。
(26)在【平面铣】对话框中单击“指定底面”按钮,选择实体的底面,把“距离”值设为0mm,单击“确定”按钮。
(27)在【平面铣】对话框中,对“切削模式”选择选项、“步距”选择“恒定”选项,把“最大距离”值设为10.0000mm,如图3-41所示。

图3-40 对“刀具侧”选择“内侧”

图3-41 设置刀轨参数
(28)单击“非切削移动”按钮,在弹出的【非切削移动】对话框中单击“进刀”选项卡,在“封闭区域”列表中,对“进刀类型”选择“螺旋”选项,把“直径”值设为10.0000 mm、“斜坡角”值设为1.0000(单位:°)、“高度”值设为1.0000mm,对“高度起点”选择“当前层”选项,把“最小安全距离”值设为1.0000 mm、“最小斜面长度”值设为10.0000mm,如图3-42所示。单击“退刀”选项卡,对“退刀类型”选择“与进刀相同”选项。
(29)单击“生成”按钮,生成挖槽刀路,如图3-43所示。
(30)在工作区上方的工具条中单击“程序顺序视图”按钮,如图3-44所示。
(31)在“工序导航器”中把“PROGRAM”名称改为A1,并把所创建的程序移到A1程序组中。修改后的“工序导航器”如图3-45所示。

图3-42 设置“进刀”选项卡参数

图3-43 挖槽刀路

图3-44 单击“程序顺序视图”按钮

图3-45 修改后的“工序导航器”
5)创建精加工刀路
(1)单击“菜单|插入|程序”命令,在【创建程序】对话框中,对“类型”选择“mill_planar”选项,对“程序”选择“NC_PROGRAM”选项,把“名称”设为A2。
(2)单击“确定”按钮,创建A2程序组。此时,A2和A1都在NC_PROGRAM的下级目录中,如图3-46所示。
(3)在“工序导航器”中选择和
两个刀路程序,单击鼠标右键,在快捷菜单中单击“复制”命令。再选择A2,单击鼠标右键,在快捷菜单中单击“内部粘贴”命令,把上述两个刀路程序粘贴到A2程序组中,如图3-47所示。

图3-46 创建A2程序组

图3-47 复制程序
(4)在“工序导航器”中双击选项,在【平面铣】对话框中,把“最大距离”改为0.1mm,“附加刀路”改为2。单击“切削层”按钮
,在弹出的【切削层】对话框中选择“仅底面”选项。单击“切削参数”按钮
,在弹出的【切削参数】对话框中把“余量”改为0mm。单击“进给率和速度”按钮
,在弹出的【进给率和速度】对话框中,把主轴速度值设为1200 r/min、切削速度值设为500 mm/min。
(5)单击“生成”按钮,生成的精加工台阶刀路如图3-48所示。
(6)采用相同的方法,修改刀路程序,生成的精加工外形刀路如图3-49所示。

图3-48 生成的精加工台阶刀路

图3-49 生成的精加工外形刀路
6)创建ϕ6mm立铣刀的刀路
(1)单击“菜单|插入|程序”命令,在【创建程序】对话框中,对“类型”选择“mill_planar”选项,对“程序”选择“NC_PROGRAM”选项,把“名称”设为A3。
(2)在“工序导航器”中选择刀路程序,单击鼠标右键,在快捷菜单中单击“复制”命令。再选择A3,单击鼠标右键,在快捷菜单中单击“内部粘贴”命令,把
刀路程序粘贴到A3程序组,如图3-50所示。
(3)在“工序导航器”中双击选项,在【平面铣】对话框的“工具”列表中对“工具”选择“D6R0(铣刀-5参数)”铣刀选项,如图3-51所示。

图3-50 复制刀路

图3-51 选择“D6R0(铣刀-5参数)”铣刀
(4)在【平面铣】对话框中,对“切削模式”选择“轮廓”选项,单击“切削层”按钮
,在弹出的【切削层】对话框中把“每刀切削深度”值设为0.3mm。单击“切削参数”按钮
,在弹出的【切削参数】对话框中单击“空间范围”选项卡,对“过程工件”选择“使用参考刀具”选项,对“参考刀具”选择“D12R0(铣刀-5参数)”选项,把“重叠距离”值设为2.0000(单位:mm),如图3-52所示。
(5)在【平面铣】对话框中,单击“非切削移动”按钮,在弹出的【非切削移动】对话框中单击“进刀”选项卡。在“封闭区域”列表中,对“进刀类型”选择“与开放区域相同”;在“开放区域”列表中,对“进刀类型”选择“圆弧”选项,把“半径”值设为1.0000mm,“圆弧角度”值设为90.0000(单位:°)、“最小安全距离”值设为2.0000mm,如图3-53所示。

图3-52 设置“空间范围”选项卡参数

图3-53 设置“进刀”选项卡参数
(6)单击“生成”按钮,生成的清角刀路如图3-54所示。
(7)在“工序导航器”中选择选项,单击鼠标右键,在快捷菜单中单击“复制”命令。再选择中A3,单击鼠标右键,在快捷菜单中单击“内部粘贴”命令,把
刀路程序粘贴到A3程序组。
(8)双击选项,在【平面铣】对话框中,把“最大距离”改为0.1mm、“附加刀路”改为2。单击“切削层”按钮
,在【切削区】对话框中,把“类型”改为“仅底面”。单击“切削参数”按钮
,在【切削参数】对话框中选择“空间范围”选项卡,对“过程工件”选择“无”选项。单击“余量”选项卡,把“部件余量”值和“最终底面余量”值都设为0mm。
(9)单击“生成”按钮,生成的精加工刀路如图3-55所示。

图3-54 生成的清角刀路

图3-55 生成的精加工刀路
(10)在“工序导航器”中选择选项,单击鼠标右键,在快捷菜单中单击“复制”命令。再选择A3,单击鼠标右键,在快捷菜单中单击“内部粘贴”命令,把
刀路程序粘贴到A3程序组。
(11)双击选项,在【平面铣】对话框中,把“切削模式”改为“跟随周边”、“最大距离”值改为2mm。单击“进给率和速度”按钮
,在弹出的【进给率和速度】对话框中,把主轴速度值设为1200 r/min、切削速度值设为500 mm/min。
(12)单击“生成”按钮,生成的精加工底面的刀路如图3-56所示。

图3-56 生成的精加工底面的刀路
(13)单击“创建工序”按钮,在【创建工序】对话框中,对“类型”选择“mill_planar”选项,把“子类型”设为“底壁铣”按钮
,对“程序”选择A3,对“刀具”选择“D6R0(铣刀-5参数)”选项,对“几何体”选择“WORKPIECE”选项,如图3-57所示。
(14)单击“确定”按钮,在【底壁铣】对话框中单击“指定切削区底面”按钮,选择实体的上表面,单击“确定”按钮。
(15)在【底壁铣】对话框中单击“指定修剪边界”按钮,在【修剪边界】对话框中选择“曲线”选项、“修剪侧”选择“内部”选项,如图3-58所示。

图3-57 设置【创建工序】对话框参数

图3-58 设置【修剪边界】对话框参数
(16)在工作区上方的工具条中选择“相切曲线”选项,如图3-59所示。

图3-59 选择“相切曲线”选项
(17)选择实体口部内侧曲线,如图3-60所示。
(18)在【底壁铣】对话框中,对“切削区域空间范围”选择“底面”选项、“切削模式”选择“往复”选项、“步距”选择“刀具平直百分比”选项,把“平面直径百分比”值设为75%。
(19)单击“切削参数”按钮,在弹出的【切削参数】对话框中把“余量”值设为0mm。
(20)单击“进给率和速度”按钮,在弹出的【进给率和速度】对话框中,把主轴速度值设为1200 r/min、切削速度值设为500 mm/min。
(21)单击“生成”按钮,生成加工口部的刀路如图3-61所示。

图3-60 选择实体口部内侧曲线

图3-61 生成加工口部的刀路
7)创建加工斜面的刀路
(1)在“工序导航器”中选择选项,单击鼠标右键,在快捷菜单中单击“复制”命令。再选择A3程序组,单击鼠标右键,在快捷菜单中单击“内部粘贴”命令。
(2)双击选项,在【平面铣】对话框中单击“指定部件边界”按钮
,在【部件边界】对话框中单击“移除”按钮
。
(3)在【部件边界】对话框中,对“选择方法”选择“面”选项、“刀具侧”选择“外侧”选项。
(4)选择实体的上表面,在【部件边界】对话框中的“列表”栏中删除Inside所在的行(删除内环),只保留Outside所在的行,即选择实体上表面的外边线(此时,外边线呈棕色),如图3-62所示。设置完毕,单击“确定”按钮。
(5)在【平面铣】对话框中单击“指定底面”按钮,在【平面】对话框中,对“类型”选择“通过对象”选项,如图3-63所示。

图3-62 选择实体上表面的外边线

图3-63 选择“通过对象”选项
(6)选择实体侧面的圆弧边线(见图3-64),显示圆弧所在的平面,如图3-65所示。设置完毕,单击“确定”按钮。

图3-64 选择实体侧面的圆弧边线

图3-65 显示圆弧所在的平面
(7)在【平面铣】对话框中、“附加刀路”值设为0。
(8)单击“切削层”,在弹出的【切削层】对话框中对“类型”选择“恒定”选项,把“公共”值设为0.1000(单位:mm)、“增量侧面余量”值设为0.1*tan(5)(应在英文输入法下输入“()”,否则,被视为非法字符,系统会报警),如图3-66所示。
(9)单击“切削参数”按钮,在弹出的【切削参数】对话框中,单击“余量”选项卡,把“部件余量”值、“最终底面余量”值、“内公差”值和“外公差”值都设为0.01mm。
(10)单击“进给率和速度”按钮,在弹出的【进给率和速度】对话框中,把主轴速度值设为1200r/min、切削速度值设为500mm/min。
(11)单击“生成”按钮,生成刀路。单击“前视图”按钮
,切换视图方向。平面铣刀路如图3-67所示。从图中可以看出,生成的刀路有斜度。

图3-66 设置【切削层】对话框参数

图3-67 平面铣刀路
(12)单击“菜单|插入|工序”命令,在【创建工序】对话框中对“类型”选择“mill_contour”选项。在“工序子类型”列表中单击“深度轮廓铣”按钮,对“程序”选择A3,对“刀具”选择“D6R0(铣刀-5参数)”选项、“几何体”选择“WORKPIECE”选项、“方法”选择“METHOD”选项,如图3-68所示。设置完毕,单击“确定”按钮。
(13)在【深度轮廓铣】对话框中单击“指定切削区域”按钮,在实体上选择方形凹坑周围的4个斜面和圆弧面,如图3-69所示。

图3-68 单击“深度轮廓铣”按钮

图3-69 在实体上选择方形凹坑周围的4个斜面和圆弧面
(14)在【深度轮廓铣】对话框中,把“最大距离”值设为0.1mm。
(15)对“切削参数”、“非切削移动”和“进给率和速度”,按前面的方式进行设置。
(16)单击“生成”按钮,生成刀路,即用“深度轮廓铣”方式加工斜度,如图3-70所示。

图3-70 用“深度轮廓铣”方式加工斜度