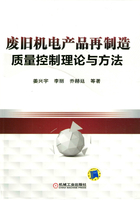
1.3.3 废旧机电产品的再制造质量控制方法的研究进展
综合国内、外再制造研究现状可知,再制造的研究多集中在再制造工艺、再制造工程技术、加工设备、逆向物流等方面,而作为再制造工程的核心——再制造过程中的质量控制方面的研究却相对较少[55-61],这也是严重制约我国再制造发展的重要因素之一。因此,开展本课题的研究,对于我国科学发展再制造具有极其重要的理论意义。
与传统制造相比,再制造是以废旧产品为起点的,由于服役时间和工况、失效形式和失效程度、剩余寿命等的不同,使得再制造系统具有高度的不确定性。Guide归纳了再制造系统的七项不确定性[41]:①回收时间和质量不确定;②回收与需求平衡不确定;③回收产品的拆卸不确定;④逆向物流不确定;⑤物料匹配复杂性;⑥再制造工艺路线的随机性;⑦加工时间的多变性。
由于再制造系统具有多种不确定性,这为其运营过程中的质量管理与控制提出了巨大挑战,因此传统制造模式的质量管理与控制方法已很难适应再制造系统。再制造的对象是情况复杂的废旧产品,不同的再制造产品质量具有更大的波动性,即不同的再制造产品质量可能各不相同,同一装备在不同时期进行再制造也会使得再制造产品质量有所差异。所以,废旧产品(或零件)的质量直接影响再制造系统的性能和其产品质量,这在客观上也要求对废旧产品(或零件)进行质量检测与控制。
瑞典的Youngseok Kim和Hong-Bae Jun提出了一种嵌入质量再制造系统建模方法,以对废旧产品(或零件)进行质量控制[62]。但该方法受到废旧品(或零件)质量特性的限制,具有一定的局限性。目前对废旧产品(或零件)质量控制研究主要集中在外部几何形状、内部质量特性的检测及再制造性的评价,基本上实现了再制造产品质量的前期控制。但由于没有考虑环保和用户需求的因素,对实际的再制造存在一定的制约。
同时,由于再制造采用的是具有不确定性性能和质量的废旧机电产品,这使再制造过程比原产品制造过程更为复杂。而在这一过程中,再制造过程质量控制是保证再制造产品质量的核心。过程质量控制是根据再制造产品的工艺要求,研究出再制造产品的波动规律,判断造成异常波动的工艺因素,并采取各种控制措施使波动保持在技术要求的范围内,其目的是使再制造过程长期处于稳定运行状态。然而废旧品再制造性具有高度的不确定性,如再制造产品需要经过加工、改进等环节才能使用,并不能立即满足某些需要,这一系列过程需要较长的时间,即加工时间的高度不确定性。这些致使影响再制造产品质量的因素大大增多,极大地增加了工序质量控制的难度。
西北工业大学的张晶、梁工谦提出对于多工序、多指标的生产模式运用T2控制图的方法进行质量控制,该方法对检测数据做标准变换创造出利用休哈特控制图的条件,从而利用T2控制图结合相关的统计方法实现多元控制图的诊断,提高了再制造产品质量[63]。但该方法对再制造过程质量的诊断缺乏智能性、自适应性,很难实现实时的动态过程质量控制和预测。这也源自传统的过程质量控制方法,即通过序后生产检验和质量统计报表等形式进行静态质量管理和控制[64,65],且没有实现实时的动态生产质量控制和质量预测,其控制效果和效益受到很大限制,从而也影响了再制造产品的最终质量。因此,如何加强过程质量控制,提高再制造的生产效率成为再制造急需解决的一大难题。
另外,在再制造产品质量管理与控制过程中,再制造产品质量评价是提高和改进再制造产品质量的重要手段。再制造产品质量的形成涉及废旧产品的回收、拆解、清洗、检测、再制造加工、组装、检验、包装直至再制造产品出厂等一系列的过程。因此,再制造产品质量评价应贯穿于产品全生命周期的整个过程,针对一定的质量目标,在相应的产品集成信息、评价技术方法及人员组织保证的支持下,就产品质量的技术性、经济性、市场性等方面所进行的系统性评价活动[66]。
西安建筑科技大学的李菲、沈虹提出基于质量功能配置(QFD)方法将产品再制造质量特性与用户满意度相结合,构建了产品再制造质量特性评价质量屋,以此评价出相对重要的质量特性,在满足用户需求的基础上为确定再制造产品“质量突破特性”和提高再制造产品质量提供了数据参考[67]。该方法由于在再制造环境下,原料返回在时间和质量上的不确定性、材料的不确定性、再制造加工路线和加工时间的不确定性、生产计划和控制的动态性,很难解决这种动态性质量评价问题,因此本项目通过构建基于再制造过程的动态质量评价模型,采用动态性的评价方法来实现再制造产品质量评价,从而实现再制造产品质量的持续改进。