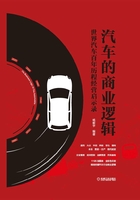
7.1 削减成本,提升企业运营效率
7.1.1 精益生产提高生产效率
精益生产在库存管理和团队合作方面优于大规模生产。精益生产之所以库存较低,是因为采用了准时化生产方式(JIT),即根据需要的时间和数量进行生产。另外,组装厂在生产过程中,如果发现零件有瑕疵,就马上停止生产,解决问题后才会流到下一道工序,降低了废品率,也减少了维修场地和维修工人的数量,企业无需再保持大量的库存。精益生产和大规模生产的对比见表3-8。团队合作在生产过程中非常重要。当生产出现问题时,整个团队的员工群策群力,合作解决问题。这体现了精益生产重视员工参与性的思想。
表3-8 精益生产VS大规模生产

资料来源:搜狐网
按照精益生产方式重组的生产系统缩短了产品的单位生产时间。20世纪90年代初大众建造的工厂是精益生产的范例,位于德国东部的Mosel工厂和位于Martorell的西亚特工厂都移植了日本的工厂模式,生产流程得到了系统的改进。重组后的生产系统帮助大众提高了生产效率。1997年,POLO系列的单位生产时间从24h降至15h,帕萨特系列从31h降至22h。
大众在推动精益生产的过程中进行了如下改革:
引入分散化、扁平化管理的等级制度。通过引入分散化的生产管理,将精益生产的原则融进工作过程中。自1992年以来,大众一直在推进团队合作,并辅以更扁平化的层级制度。1993年大众将决策能力转移到执行部门,从而鼓励了员工的自我责任和积极性。
同步工程方法缩短项目时间。同步工程即在产品的设计开发期间,将概念设计、结构设计、工艺设计、最终需求等结合起来,成立对应的项目小组。1993年大众将车辆的开发过程从一般顺序方法转变为同步工程法,缩短了项目时间,当客户的需求发生变化时,大众可以以更快的速度对市场需求做出反应。
持续改进的管理思想鼓励了员工创新。大众采用了日本人的持续改进理念,鼓励员工参与优化工作场所,以提高所有生产过程的质量和生产效率。工厂的经理直接接受、快速检查和执行由员工提出的新点子。
7.1.2“转盘”概念和模块化思想实现柔性生产
20世纪90年代末大众引入了“转盘”的概念,允许在工厂内部和不同工厂之间进行短时的应急性的产量调整。不同国家的工厂可以在各自的生产线上生产各种车型,调整生产计划,以应对不同车型需求的短期变化。“转盘”的概念后来被2000年的模块化策略所取代。
“呼吸工厂”的概念帮助大众实现柔性生产。大规模生产的特点之一是按照工作时间安排生产,而以市场为导向的生产则是基于企业收到的客户订单来安排时间和班次,这就是所谓的“呼吸工厂”的概念。面对季节性波动的需求,新车型的启动和车型升级计划,工厂提前计划需求周期比较困难。“呼吸工厂”的重点是要匹配生产和在手的订单之间的关系,在不同生产基地间灵活生产,以及为柔性生产设立了各种工作时间模型。
大众利用平台和“主”生产站点策略来平衡产量失衡。一个生产站点只能在一个平台上生产是常态,而能够在一个平台或跨越不同平台上灵活生产的生产站点是所谓的“主”站点,比如大众在德国东部的Mosel工厂。大众可以利用这一套体系在各生产站点之间来平衡短期的产量失衡。“主”生产站点和平台策略使生产站点之间在成本、质量和交付标准上的内部竞争,从而优化了集团产能。
根据“相同零部件”原则,模块可以跨品牌、跨车型使用,节约了开发成本和降低采购价格,从而产生协同效应。例如,高尔夫、奥迪A3、新甲壳虫、斯柯达明锐和奥迪TT都是建立在一个共同的平台之上。
关于大众平台化、模块化的发展后续有专门章节阐述。
7.1.3 充分利用国际分工,进行全球化的生产和采购
全球化的生产充分利用了低成本优势。在费迪南德·皮耶希的领导下,大众集团的全球化进一步发展。通过建立灵活的全球生产网络,加强了大众集团的国际竞争力。大众在全球有50多个生产地点,例如,墨西哥工厂生产新款甲壳虫和捷达,斯洛伐克工厂生产途锐,充分利用了在低成本国家生产的优势。
市场化的采购政策创造了竞争环境。采购政策向以市场为导向的采购政策过渡,这种政策不再以稳定的产能利用率为主导,而是对客户需求波动迅速反应。20世纪90年代,大众在德国生产时更广泛地依靠外部供应商,给集团内部供应商创造了竞争环境,降低了集团生产成本。
采购由单个部件向复杂部件和模块的交付转变。平台化战略的推行也改变了大众零部件的采购政策,逐渐由单一组件转为复杂部件和模块的采购,同质化、比较独立的零部件越来越多地采取外包的政策。1995年,大众阿根廷工厂开始采用模块组装原则,供应商对组装好的零部件进行现场安装。
精益生产、协同生产和国际分工大大提升了大众的运营效率。从1993年起大众的存货周转率和固定资产周转率有明显的上升(见图3-94,图3-95)。

图3-94 1989~2000年大众存货周转率
资料来源:大众公司

图3-95 1987~2000年大众固定资产周转率
资料来源:大众公司