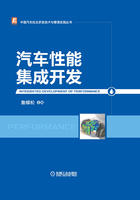
5.2.3.1 乘员舱热管理性能的目标分解及方案设计
1.乘员舱热管理系统设计参数的确定
汽车空调系统的任务是为乘员舱提供一个热舒适的环境,是现代车辆中最重要的辅助设备之一。乘员舱热管理系统的目标由乘员舱热管理系统的负荷确定,乘员舱热管理系统的负荷则由车内外的设计参数确定。目前,大部分主机厂的车内外设计参数是依据5.1节中设定的整车性能目标和相应试验方法选取的某个设计工况点来确定的,部分主机厂的典型设计参数见表5-14。
表5-14 乘员舱热管理系统的主要设计参数

2.乘员舱热管理系统性能目标的确定
为了维持乘员舱内的舒适温度,乘员舱热管理系统在制冷时提供冷量,在采暖时提供热量,乘员舱与外界环境的热交换情况如图5-27所示,主要包括3部分负荷:乘员舱的冷/热负荷、乘员舱内乘员的热湿负荷、新风和漏风负荷。

图5-27 乘员舱与外界环境的热交换
(1)乘员舱的冷/热负荷 设计参数确定后,乘员舱的冷/热负荷主要由乘员舱各部分面积、厚度等结构参数和材料的辐射、导热等热力性能决定,主要参数见表5-15。
乘员舱冷/热负荷主要包括以下几部分:QB通过车身(车顶、车门)与乘员舱交换的热量(W),QC通过车身(地板、行李舱)与乘员舱交换的热量(W),QG通过玻璃表面以对流方式与乘员舱交换的热量(W),QBi通过玻璃表面以辐射方式直接进入乘员舱的热量(W),QE从发动机舱前壁板与乘员舱交换的热量(W),QM车内电器造成的热量(W)。具体的计算公式和相关经验参数可参考汽车空调设计的书籍,本书中不再详述。
表5-15 乘员舱的主要参数

(2)乘员舱内乘员的热湿负荷QP 乘员舱内乘员的热湿负荷分为两部分:一是由传导、对流、辐射方式散发的显热量;二是由人体呼吸和皮肤水分蒸发所散发的潜热量。通常采用经验数据进行计算,显热量按驾驶人70~100W/m2,乘客55W/m2取值;潜热量按24°C环境下人体的散湿量50~80g/h取值。
(3)新风和漏风负荷QV 新风和漏风负荷来源于由于车身密封性导致的漏风和为了改善车内空气质量引入的新风,通常新风+漏风量按人均11m3/h计算。
综上,根据制冷、采暖和除霜除雾不同的工况,对以上负荷求和即为乘员舱热管理系统的总负荷Q,考虑一定的余量,放大系数取1~1.2,即乘员舱热管理系统的性能目标

3.主要零部件的性能目标分解
(1)暖通空调总成的制冷/热量、风量 乘员舱热管理系统的性能目标即暖通空调总成需要提供的制冷/热量,车内外空气的设计参数确定了暖通空调总成的进出口焓值,由此可以得到乘员舱热管理系统的送风量:

式中,VE为暖通空调送风量(m3/h);ρ为蒸发器入口的空气密度(kg/m3);iin、iout为蒸发器入口、出口空气焓值(kJ/kg)。
(2)压缩机和冷凝器的性能目标分解 首先需要确定制冷剂的设计工况,主要包括冷凝温度、蒸发温度、过冷度和过热度,如图5-28所示。通常汽车空调冷凝器采用的是风冷式,为了保证冷凝效果,冷凝温度应高于车外的温度12~15°C,考虑一定的余量,冷凝温度可取50~60°C。另一方面,理论上蒸发温度越低,空调的制冷效果越好,但是当蒸发器表面的温度低于0°C时容易造成蒸发器的表面结霜导致故障,因此,通常选择0°C作为汽车空调蒸发器的蒸发温度。为了保障到达节流装置的制冷剂是液态的,通常要求冷凝器出口的过冷度为5~8°C。为了保证制冷剂在蒸发器中完全蒸发,不出现压缩机液击,同时又不因过热度太大而造成蒸发能力浪费,通常选择5~10°C作为蒸发器出口的过热度。

图5-28 制冷循环压焓图
于是,可按如下公式计算压缩机排量:

式中,VC为压缩机排量(cm3),ν为压缩机进口制冷剂比容(m3/kg),Ncomp为压缩机转速(r/min),h2、h3分别为2、3点的制冷剂比焓(kJ/kg),ηv为压缩机的容积效率。
冷凝器的换热需求可按下式计算:

式中,Qcond为冷凝器的换热量(kW);h1、h5分别为1、5点的制冷剂比焓(kJ/kg)。
考虑到实车上冷凝器进风条件的恶化,冷凝器的换热性能目标可按1.1~1.3倍计算。