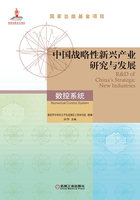
第1章 数控系统发展历程
1.1 数控系统技术演进
数控机床是以数控系统为代表的新技术对传统机械制造产业渗透而形成的机电一体化产品,它显著提高了零件加工的精度、速度和效率,是国家工业现代化的重要物质基础之一,也是制造业的“工业母机”,其技术水平代表着一个国家的综合竞争力,是国际装备制造业竞争的热点领域。
数控系统作为数控机床的控制核心,是机械制造和控制技术相结合的产物,为当今高端装备制造业的核心产品之一。作为控制机床的大脑,数控系统的功能、控制精度和可靠性直接影响着机床整体性能、性价比和市场竞争力。
1952年,美国麻省理工学院与帕森斯公司进行合作,发明了世界上第一台三坐标数控铣床。该数控铣床的控制装置由2000多个电子管组成,约一个普通实验室大小。其伺服机构采用一台小伺服电动机改变液压马达斜盘角度以控制液压马达速度,插补装置采用脉冲乘法器。该台数控铣床的研制成功标志着数控技术的创立和机械制造开始进入数控时代。
经过近70年的发展,数控系统技术得到了显著提升。最初由2000多个电子管起步,经历了分立式晶体管式、小规模集成电路式、大规模集成电路式、小型计算机式、微型计算机式数控系统等阶段。数控系统技术正向着高速化和高精度化、多轴联动与功能复合化、自动化与柔性化、开放化与平台化、网络化和智能化等方向发展。数控系统技术发展历程见表1-1。
表1-1 数控系统技术发展历程

(续)

数控技术是在多学科交叉、多领域技术融合基础上发展起来的,关键技术主要如下:
1)电子元件技术。微电子技术的发展对数控技术发展起着极大的推动作用。日本发那科公司于1963年采用硅晶体管研制出FS220、FS240等系统,1969年又采用中小规模集成电路(IC)更新了FS220、FS240等系统,20世纪70年代开始采用3SI,推出了FS5、FS7、FS3、FS6、FS0、FS18、FS16、FS20、FS21、FS15等一系列计算机数控(CNC)系统,从4位位片机(FS7)到16位8086微处理器(FS6)和32位80486微处理器(FS0)。1996年采用专用芯片微处理器,推出了小型化、高性能的i系列数控系统,大小为原系统的1/4,系统的性能及可靠性显著提升。
2)计算机应用软件技术。1970年芝加哥国际机床展览会上首次展出由小型机组成的数控系统,其采用半导体存储器存储零件加工程序,代替打孔的零件纸带程序进行加工,程序便于显示、检查、修改和编辑。译码、刀具补偿、速度处理、插补、位置控制等控制功能由软件实现,可减少系统的硬件配置,提高系统可靠性及柔性,降低了制造成本。
3)数控标准。在数控技术发展中,形成了国际标准化组织(ISO)标准、国际电工委员会(IEC)标准和美国电子工业协会(EIA)标准等多个国际通用标准体系,规定了数控机床的坐标轴和运动方向、编码字符、程序段格式、准备功能和辅助功能、数控纸带的尺寸、数控的名词术语等,行业标准对数控技术的发展起到了规范和推动作用。
4)伺服技术。伺服装置是数控系统的重要组成部分。20世纪50年代初,世界第一台数控(NC)机床的进给驱动采用液压驱动。液压系统单位面积产生的力大于电气系统所产生的力,惯性小、反应快;20世纪70年代初期,由于石油危机,加上液压系统对环境造成污染以及系统笨重、效率低等原因,美国GETTYS公司开发出了直流大惯量伺服电动机,静力矩和起动力矩大,性能良好,日本发那科公司于1974年引进并应用于数控机床上。随着伺服技术的发展,开环控制系统被闭环控制系统取代,液压伺服系统逐渐被电气伺服系统取代。同时交流驱动取代直流驱动,数字控制取代模拟控制,软件控制取代硬件控制。
5)自动编程技术。据统计分析,采用手工编程,一个零件编程时间与机床加工时间之比,平均约为30∶1。20世纪70年代出现的图像数控编程技术有效地解决了几何造型、零件几何形状的显示、交互设计、修改及刀具轨迹生成、走刀过程的仿真显示、验证等,推动了自动编程技术的发展。
6)分布式数控(DNC)。机械加工从单机自动化扩展到柔性生产线及计算机集成制造系统。从通信功能而言,在数控系统中增加DNC接口,可形成制造通信网络。网络最大特点为资源共享,通过DNC功能形成的网络可以实现零件加工程序的上传或下传,读、写CNC数据,可编程序控制器(PLC)数据传送,存储器操作控制,系统状态采集和远程控制等。
7)可编程序控制器(PLC)。在20世纪70年代以前,数控系统与机床强电顺序控制主要靠继电器进行。1969年,美国DEC公司研制出世界上第一台PLC,具有诸多优点,可直接应用在数控机床上。使用PLC减少了数控系统的占用空间,提高了系统的快速性和可靠性。
8)传感器技术。在数控系统控制下,零件加工的几何精度除受机械因素影响外,主要取决于所采用的位置和速度传感器。当前测量直线位移和旋转角度的传感器包括直线感应同步器和圆感应同步器、直线和圆光栅、磁尺、利用磁阻的传感器等,一般分辨率为0.01~0.001mm,测量精度为±(0.02~0.002)mm/m。随着机床精度的不断提高,对传感器的分辨率和精度也提出了更高的要求。
9)开放体系架构。当前市场上的数控系统开放体系架构主要有两种:①CNC+计算机(PC)主板。将PC主板插入传统的CNC机器中,PC主板主要进行非实时控制,CNC主要进行以坐标轴运动为主的实时控制。②PC+运动控制板。开放体系架构工作可靠,界面开放,越来越受到机床制造商的欢迎,成为数控技术发展趋势之一。