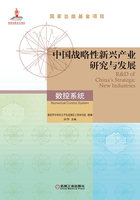
2.2 多轴联动、多通道控制技术
2.2.1 多轴联动
为了满足复杂曲面的加工需求,必须采用多轴联动数控系统。多轴联动加工可利用刀具的最佳几何形状进行切削,产品的加工效率、加工质量和加工精度大幅提升。一般认为,2~3台三轴机床的加工效率仅能和1台五轴联动机床的加工效率相媲美。多轴联动数控系统集计算机控制、高性能伺服驱动和精密加工技术于一体,对于一个国家的军工、航空航天、精密仪器等行业有着举足轻重的影响力。五轴联动数控机床已成为航空航天、精密仪器加工等领域重要的加工工具,五轴联动是技术难度最大、应用范围最广的数控机床技术之一。五轴机床一般采用“3+2”结构,即三个进给轴和两个回转轴结构,不仅可以实现X/Y/Z三个轴的直线运动,还可同时实现另外两个轴的回转运动。这种机床主要有立式加工中心、卧式加工中心、摇篮式加工中心及龙门加工中心等。以立式加工中心为例,立式五轴加工中心的回转轴有两种运作方式:一是工作台回转,二是依靠主轴头的回转。除此以外,卧式加工中心还有工作台旋转和主轴头摆动相结合的五轴联动运作方式等。
多轴联动控制技术是指由数控系统控制多个坐标轴同步协调运动。多轴联动控制系统由多轴联动控制器和执行机构组成,其关键技术就是对执行机构运动部件的速度、加速度等进行实时控制和调节,控制执行机构按照算法设定的速度、路径运行。
三轴联动、五轴联动的显著特点是,在G代码指令上联动轴的关系都是显式表达的,如G01三轴联动的X、Y、Z的运动关系,在G代码指令上都必须予以显式定义。而切线跟随控制、斜轴控制技术有时并不是显式地定义某个伺服轴(比如C轴)与X、Y轴及运动轨迹的关系。斜轴控制技术机床,为了满足某种加工工艺需求,将数控机床的X、Y两个伺服轴有意布置成不垂直的状态。但是在G代码编程时,需要操作者根据机床X、Y两个伺服轴的实际夹角,生成实轴坐标系下的G代码指令,不仅难度大,同时编制出来的G代码程序没有通用性。斜轴控制不仅需要在解释器、插补器中进行处理,同时需要解决手轮、步进、点动等PLC运动控制的问题。在五轴联动数控机床进行RTCP功能开发时,需要解释器接口与插补器接口,才能实现从虚轴编程到实轴的运动控制,因为此时G代码程序中输入的数据中所包含的轨迹信息不是实轴的运动轨迹信息,而是刀触点的位置及该刀触点位置处的法矢量。对于刀位信息,不通过G代码解释器的解释,不可能获得五轴中的各个实轴的运动轨迹,也不能实现RTCP功能。
插补技术是多轴联动控制器实现轨迹控制的核心,对数控系统的精度和效率有直接的影响。现代数控技术采用的插补方法通常是将给定的加工曲线离散成一系列微小直线段、圆弧线段等基本线段,并根据进给速度和插补周期将这些线段离散成大量的插补指令点,然后将这些线段转换成在各轴上的位移增量,再将这些脉冲增量换算成具体的脉冲数驱动电动机运动,实现多轴的联动控制,数据表插补法包括脉冲增量法和数据采样法。
数据表插补控制有两种用途,一种用于耦合轴之间有明确轨迹联动要求,且所有耦合轴为伺服轴,比如电子齿轮、电子凸轮等的运动控制;另一种用于耦合轴之间至少有一个轴为非伺服轴,比如工件主轴或者刀具主轴,其他轴是伺服轴,并且伺服轴中有一个轴或者几个轴需要根据当前时刻非伺服轴及其他伺服轴的位置决定其位置的运动控制。比如交错轴斜齿轮的加工,工件的回转速度必须根据刀具(非伺服轴)的速度进行计算,同时附加的工件回转角速度也必须根据滚刀的Z轴位置进行计算。
数据表插补法主要用在计算量很大的情形。比如在活塞车削中,刀具运动频率高达450Hz,没有办法完成一个控制周期中每一个时刻刀尖点位置的计算。此时,必须事先将每个控制周期中的每一个时刻的刀尖点位置计算出来,存入数据表中,在每个插补周期中直接通过查询数据表,获得被控制轴的运动位置。由此可见,数据表插补法一般用于周期性的、封闭的、复杂曲线的加工,比如凸轮轴的高速磨削加工。若要求工件凸轮的回转速度小于20r/min,可不用数据表插补法。若要求工件凸轮的转速高达120r/min甚至500r/min时,不采用数据表插补法。在20μs左右的控制周期中,现有数控装置的CPU很难计算出刀尖点的准确位置。