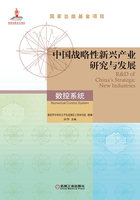
2.2.2 多通道控制
数控系统多通道技术是指每个通道独立完成各自的工序,多轴间相互协作,最终共同完成一项任务。该项技术可有效减少设备投入,缩短加工时间,提高加工效率。
多通道数控系统基本模式如图2-24所示。

图2-24 多通道数控系统基本模式
在数控系统开发中,为简化程序编制,一般一个通道最多包含9个轴,可以只有一个伺服轴,也可以有一个或多个伺服轴和一个伺服主轴。不属于伺服主轴的主轴,一般不纳入通道的插补管理范畴。
在传统的单通道数控系统中,NC程序的加工流程是串行化的,即用户输入G代码后,数控装置对其进行解析与解释,求解出刀具补偿量和刀位点,以及插补方式和进给速度等,一直到整个加工程序完成,都在一个通道中进行。多通道数控系统的加工流程为多个上述单通道NC程序运行的并行化,即用户输入G代码文件,从分配每个通道需要执行的部分NC程序块开始,一直到整个加工工序完成,是在所有通道的共同协作下完成的。多通道数控系统NC程序加工流程如图2-25所示。
多通道控制系统并行控制技术能使数控机床的操作者在同一时间指定多个NC程序运行,也可在并行执行NC程序间进行信号的传递与交互,完成多种任务。
HNC8型数控系统最多有32个通道,每个通道最多有9个轴(伺服轴+主轴),从数控系统的宏观运行来看,通道是并行运行的。HNC8型数控系统中的工位与西门子840D的工作方式原理基本类似,主要是便于PLC编程及G代码程序编制,方便数控机床的操作及加工代码的编制。

图2-25 多通道数控系统NC程序加工流程
工位由通道组成,一个工位最多可以管理8个通道,属于同一个工位的通道在运行的时间关系上是按照G代码指令给定的顺序运行的,不存在工作运行间的协同问题。因此,一个工位只有一个G代码程序,即可满足顺序运行的要求,可较为方便地编制PLC程序。一个工位虽然有多个通道,但是对应于一个操作面板。
数控系统中与运动控制有关的结构体可定义为:
Struct
{
工位数组sWork[4];//一个数控系统最多有4个工位;工位指针*pWork=&sWork[0];
}
属于同一个工位的通道,在运行时一般为顺序运行,各通道共享G代码程序空间,同一个工位的通道只需要一个G代码程序进行顺序控制。
除了属于某个工位的通道,还有独立运行通道,即不属于某个已定义的工位的通道,其有独立G代码程序和对应的机床操作面板。
一个多通道机床数控系统的动作协同,是发生在工位与工位之间、工位与通道之间、通道与通道之间的。当然还有独立PLC轴与工位、独立通道之间的动作协同要求。
HNC8型数控系统多通道功能包括通道间耦合动作协同、PLC编程、控制中信息双向或者多向传递、HMI界面操作按钮与通道之间的关联等。