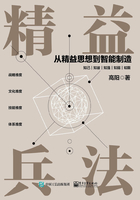
上QQ阅读APP看本书,新人免费读10天
设备和账号都新为新人
1.3 精益体系的完善
1950年,进入丰田管理层的丰田英二(见图1.5)考察了美国底特律的福特公司轿车厂。当时这个工厂每天能生产7000辆轿车,比日本丰田公司一年的产量还要多,但丰田英二在他的考察报告中却自信地写道:“那里的生产体制还有改进的可能。”

图1.5 丰田英二
“二战”后的日本经济萧条,缺少资金和外汇,经济和技术基础与美国相距甚远,没有可能利用巨额资金全面引进美国的成套设备和大量的原材料来生产汽车。面对这一现实,丰田英二和他的伙伴大野耐一在丰田公司历史沿革下来的一些优秀做法的基础上,进行了大量的探索和实验,并根据日本的国情提出了一系列具有创新性的方法。
大野耐一先在自己负责的工厂试验一些现场管理方法(见图1.6),如目视管理法、一人多机、U 形设备布置法等,这是丰田生产方式的萌芽。随着大野耐一式的管理方法取得初步实效,他的地位也得到了逐步提升,大野耐一式的管理在更大的范围内得到了应用,同时他的周围也聚集了一些人。通过对生产现场的观察和思考,大家又提出了一系列革新方案,如单分钟换模法、防错法、五问法、拉动式生产等。经过30多年的磨合与完善,一套适合快速变换市场需求的丰田公司的生产模式最终成型。

图1.6 大野耐一在丰田车间现场
可见,精益生产并非一两种简单的管理工具,而是通过不断创新、不断传承而形成的一套与环境、文化高度融合的现代化管理体系。