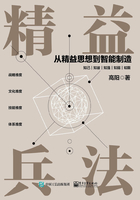
第2章 为什么成功推行“精益”的企业这么少
在全球化的背景下,不少企业都想引进国际上先进的管理手段来提升企业竞争力,最典型的便是丰田生产制造系统。但往往请了专家、做了培训,得到了部分改善,一阵风过去,一切又回到了原样。
有的公司听说“看板拉动”是个好东西,企业可以通过这个模式节省大量的资源投入,增加现金流,于是就轰轰烈烈地开展起了拉动生产改造。大量原来工位中的半成品库存被清空,然后替换成计算出来的可控数量半成品超市,接着上下道之间采用看板进行信号传递。这种心血来潮的“搞运功”式精益生产改进项目很多,刚开始确实会有一些效果,但是时间一长,一些当初预料不到的问题就会逐渐浮现出来。例如,某台关键设备损坏了,而设置的超市库存不足以支撑客户需求;看板遗失或放错看板,后道物料紧缺导致的停工,前道接不到需求而停机等待;客户每日需求发生变化,却没有及时更改看板数量,导致物料拉动时缺乏看板而无法传递信息等。每当这个时候,很多领导者就会打退堂鼓,觉得“看板拉动”是一个华而不实的东西,不但无法真正帮助企业,还平添了很多麻烦。
上述案例可以反映出很多问题,其中最明显的就是很多时候我们在行动之前,并没有理解精益改善的逻辑和具体的知识细节。就以看板拉动为例,千万不要觉得看板拉动系统是“伽马刀”,哪里出问题一旦上了看板就会变好。其实看板更像“X 光机”,它的作用是探测出企业到底哪里有问题,然后运用具体的改善策略去解决这个问题,以保证看板拉动模式的正常进行。我们感觉到的那些“麻烦”其实是看板这个“X 光机”探测出来的企业存在的问题。不能因为做了体检,查到了问题,就觉得是体检仪器导致的问题。问题一直在那里,X 光机只是告诉你指标不对,而你却觉得如果不用 X 光机检查,身体就没问题了,这个逻辑就太可笑了。
如果从大量的精益推行失败的案例中去一一探究原因,会得到一份几乎没有尽头的长卷。如果反其道而行之,看一看那些成功的企业是如何推行精益的,那么可以展开一条清晰的成功路径。到底推行精益生产的诀窍在哪里?为什么我国制造业领域直到现在也很少听说谁真的把自己做成丰田的样子了呢?下面就来讨论这个问题:为什么成功推行精益的企业这么少。
本章将从战略、文化、技能、体系4个维度探讨丰田公司的精益生产到底有何不同,看一看应该如何去推进精益生产。