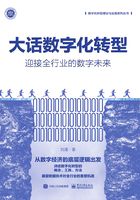
工业互联网:设备像人一样沟通
接下来,我们聊聊在工业互联网场景下的数字化是如何帮助企业提高业务效率并获得竞争优势的。工业互联网这个概念最早是由美国通用电气公司在2012年提出的,定义其是一种开放、全球化的网络,将人、数据和机器连接起来。由此可看出,工业互联网的使命就是让工业生产更加智慧、有效率。
提到工业互联网,就不得不提到物联网,这两个名词经常会被混着用。工业互联网是依托于物联网的,但不同的地方在于:物联网强调的是构建物和物之间的连接,比如计算机和遥控器之间的连接,或者传感器和加工机床之间的连接;工业互联网则具有更加宽泛的含义,它不只连接工业设备,还强调对工业生产线上的人员、设备、物料,以及管理系统进行全面连接,是用互联网把生产环境中的全部人、事、物都串联起来,以支撑各个环节的业务活动。
基于工业互联网的“数字化”业务,对工业生产数据进行智能分析,从而对整个生产制造过程进行智能化的管理和运营,我们给这个模式起了个更加响亮的名字,叫“智能制造”。
简单地说,原先每个工厂,甚至每个设备,都需要一个值班人员边盯着机器参数边不断抄录的费事环节,现在都可以靠机器设备自动完成了。机器自动记录的数据可以支持加工设备的自动生产,同时,也能够实现对工厂中生产事故的提前预警。
这样“智能化”的操作,不仅能让整个生产过程更快、更准,还节约了非常多的人力成本。于是,工业互联网在工业生产行业的大规模应用,催化了整个信息技术概念对工业活动的全价值链和全供应链的深度整合,完全重塑了以生产部门为中心的工业信息网络。
在过去的几十年中,制造企业利用信息技术提高自己的运营能力,大量引入信息系统来进行生产和管理。这里面就包括解决制造企业资源管理问题的ERP系统和针对车间运营监控的MES系统。这些系统在工厂长期的运作中积累了大量的生产制造数据,为实现制造业的全面智能化打下了坚实的基础。
类比消费领域产生数据的“用户点击”动作,在工厂车间里,数据产生环节就变成了设备在生产制造过程中的规定操作活动,比如某个机械手臂摇摆幅度和力度,或者某个待加工零件从前一个工位被移动到了其他工位。这些小的生产线状态“情报”都会被自动记录在各个工业系统中,最终构成企业巨大的工业数据体系。
而当我们把这些工业系统接入互联网中,让这些系统利用各自存储的有价值的数据进行协同工作时,就可以收获很多非常直接的“好处”。这些系统通过网络直接与生产控制设备进行连接,当发现需要做什么时,会马上通过工业互联网通知到相应的生产设备,来进行下一个步骤的加工操作。
在这个模式下,机器自己会配合“干活儿”,再也不用“工人”手把手带着做了。而每个机器系统里存储的数据,则可以发挥“工人”大脑的作用,指挥生产线上的工业活动。
当然,能够接入工业互联网的不仅可以是信息系统,还可以是生产设备,甚至可以是生产线上“流转”的一个个待加工的零件,如螺钉、半导体、轴承、芯片。每个生产线上的零件都可以看作一个独立的“数据单元”,而这个“数据单元”既承载了它在整个生产线上的经历,也记录着当下的生产状态:这个零件正在被加工、等待、查看温度是否正常、查看硬度是否达标、查看是否正在被从一个工位拿到另一个工位的“旅途”中……
把一个零件“变成”一个“数据单元”,关键在于智能传感器。传感器是用来检测环境中各种物理参数的,比如温度、湿度、力度、光照强度、音量等。说白了,就是模拟人的感觉器官,让生产工件也能有感觉,能够感知生产环境的变化。传感器越多,工件的感受能力越强,就越能够变成一个更精密的“数据单元”。
以前传感器很贵,所以用得少,但是现在传感器的成本越来越低,而且尺寸也越来越小。我们可以像“撒胡椒面”一样尽可能地在生产线上布满传感器,甚至我们会非常自然地想在每个生产设备和被加工的物品上都尽可能地配上传感器。
传感器越多的生产线就越聪明,因为生产环境的每个细微变化都被尽收眼底,从而变得“可控”。如果一杯可乐在车间最末端突然洒了,或者瓶子变形了,工人就能马上知道是拧瓶盖环节没拧紧,还是玻璃融化塑形阶段温度不够,或者是灌装可乐的时候每杯的定量出现了偏差。
信息从传感器产生,通过工业互联网被收集,然后在工业系统中被加工、分析,最后再通过工业互联网对生产设备进行控制,甚至指导生产设备之间通过网络通信密切地配合协作。互联网连接了设备,连接了人,连接了生产物料,整个生产制造过程因此变得非常聪明!

智能制造是工业数字化场景中的热门概念,在一些高级的智能化工厂中,工人只需要一个平板电脑就可以管理操控整个车间的生产运营。