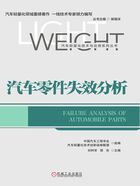
1.1 汽车零部件失效分析技术的发展过程
伴随着中国汽车工业的发展,汽车金属零部件的失效分析技术也经历了相同的发展过程。总体讲,在20世纪50年代到80年代,国有计划经济体制下,国产汽车以中型商用车为主体,产量有限,产品及相关技术开发不多,而且汽车产品性能较低,使用工况稳定,其材料工艺技术进步比较缓慢,因此在行业内产品或结构件失效不多,这方面的工作主要集中在“废品分析”的范畴,应对的主要是材料工艺的一些问题,这些问题主要来自材料和工艺技术的相对落后和不稳定等原因。
20世纪80年代中后期,随着改革开放的深入,汽车工业开始迅猛发展,但直到2000年左右,主要还是集中在以轻、中、重型的载货商用车为主体的产品发展过程中,乘用车的起步主要是在引进技术的国产化和技术消化阶段。其中,在公路运输车辆、工程机械及矿山用车等领域的应用,汽车产品的动力性及载货能力逐步提高,依据整车的各方面需求,各种总成的性能和水平也在不断地应对新的需求。这其中因恶劣的工况和超载等问题,带来了汽车零部件的大批量和多种多样的失效问题。在应对这种大量的失效问题的过程中,汽车金属零部件失效分析技术应运而生,并取得了持续的发展。最初,失效分析工作主要是针对产品质量和售后服务展开的,伴随着失效分析技术及认知的逐步深入,也逐步地体会到失效分析工作绝不仅仅是材料工艺的问题,它涵盖了整个汽车技术、汽车产品与市场需求的适应性问题。
为满足汽车产品的技术需求,20世纪80年代末,“汽车理化检测及失效分析专业学组”在中国汽车工程学会材料分会的领导下成立了,多年来一直在行业内坚持组织相关的技术交流和培训活动,取得了一定的效果。同时也积极参与、组织本行业内的相关人员参加中国机械工程学会失效分会的活动和技术交流,促进了汽车行业失效分析工作的进步。
到2000年以后,以乘用车进入寻常百姓家庭为标志,国内汽车工业迅猛发展。这个阶段对于汽车行业来讲的另一个重要标志,就是大规模的产品技术开发,这其中包括各种技术的引进消化和自主开发,相关总成和整车性能的提高,如为满足减重和节能减排而采用的新技术、新结构、新材料和新能源等。这不仅仅包括产品的性能设计开发及材料工艺应用,还包括产品的试制及性能和可靠性试验等。为此各大汽车公司或主机厂,以及零部件及材料供应企业,将失效分析相关工作的重点从质量改进和售后服务逐步地向产品开发方面发生偏移,进一步加深了各环节企业对于失效工作的认识和需求。同时,也使得失效分析工程师得以更多地了解和掌握相关的汽车产品技术,为进一步实现业务技术提高提供了条件。
而在企业中,从事失效分析的工程技术人员主要构成是材料工程师或金相检验技术人员,他们从材料工艺内在质量检验开始,逐步地延伸到废品分析,更进一步地发展到失效模式的分析方面,逐步积累经验,提高认知水平,形成了一门跨专业工程技术。在20世纪90年代以前,国内的汽车产业还是以一汽、东风、重汽及工程机械等一些大的国有企业为主体,这些企业基本上是大而全的企业模式,连一个螺钉都自己生产。因此刚开始起步的失效分析工作也主要集中在这些企业内。在20世纪90年代以后一批新的汽车企业加入进来,汽车零部件和总成的生产越来越走向专业化和社会化,且伴随着大规模的产品开发工作,这些专业化生产企业连同钢铁企业等,也越来越关注汽车零部件失效分析工作和相关技术。可以说汽车行业有着机械装备产品中最大的且门类相对齐全的失效模式样本。这些都促进了行业内失效分析专业技术队伍的壮大、技术的深入发展,并对失效分析工作提出了更高的要求。
但在汽车业内经常性的技术交流中,大家也普遍感觉到目前的汽车零件失效分析技术仍存在着一些问题,如技术环境不佳,失效分析技术的一些基本理念、原则、思维方式等方面存在不合理的问题,使得分析工作技术偏离较为严重,很大程度上影响了这项技术的发展,有时也带来了一些负面影响。