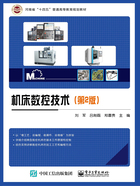
1.2 数控机床的组成及工作原理
1.2.1 数控机床的组成
数控机床一般由输入/输出装置、数控装置、伺服系统、机床本体和检测反馈装置组成,如图1-3所示。图中实线箭头所指部分为开环系统,虚线箭头所指部分包含检测反馈装置,构成闭环系统。

图1-3 数控机床的组成
1.输入/输出装置
输入/输出装置是CNC系统与外部设备进行信息交互的“桥梁”,主要用于零件数控程序的编译、存储、打印和显示等。早期的数控机床常用的信息(程序)载体有标准穿孔带(见图1-4)、磁盘和U盘等。现代数控机床常用的信息载体有硬盘和CF卡等,信息载体上记载的加工信息由按一定规则排列的文字、数字和代码所组成。目前,国际上通常使用EIA(Electronic Industries Association)代码以及ISO(International Organization For Standardization)代码,这些代码经输入装置(MDI键盘和CF卡接口等)输送到数控装置。现代数控机床一般都具有利用通信方式进行信息交换的能力,这种通信方式是实现 CAD/CAM、FMS和CIMS的基本技术。在CAD/CAM集成系统中,加工程序可不需要任何载体而直接由个人计算机通过机床传输线输入数控系统。目前,在数控机床上常采用的通信方式有以下几种。
(1)串行通信(RS232、RS422、RS485等通信接口)。
(2)自动控制专用接口和规范(DNC接口,MAP协议等)。
(3)网络通信(Internet、LAN等)。
(4)无线通信(无线AP和智能终端等)。

图1-4 穿孔带(单位:mm)
2.数控装置
数控装置是数控机床的核心,也是区别于普通机床的最重要特征之一。数控装置通常由一台通用或专用微型计算机组成,包括输入装置、内部处理器、中央处理器、输出接口和控制电路等,如图1-5所示。数控装置用来接收并处理控制介质的信息,将代码加以识别、存储、运算,输出相应的命令脉冲,经过功率放大驱动伺服机构,使数控机床按规定要求动作。它能完成加工程序的输入、编辑及修改,实现信息存储、数据交换、代码转换、插补运算及各种控制功能。因此,数控机床功能的强弱主要取决于数控装置。图1-6所示的车床、铣床/加工中心数控装置是我国自主研发生产的华中8型数控装置(中高端系列产品)。

图1-5 数控装置的组成

图1-6 华中8型数控装置
3.伺服系统
伺服系统是数控机床工作的动力装置,主要由伺服单元和驱动装置两部分组成。伺服单元是CNC和机床本体的联系环节,它把来自数控装置的微弱信号放大成控制驱动装置的大功率信号。根据接收指令的不同,伺服单元分脉冲式伺服单元和模拟式伺服单元,而模拟式伺服单元按电源种类又可分为直流伺服单元和交流伺服单元。
驱动装置是把经伺服单元放大的指令信号变为机械运动的部件,通过简单的机械连接部件驱动机床,使工作台(或刀架)精确定位或按规定的轨迹作严格的相对运动,最后加工出图样所要求的零件。和伺服单元向对应,常用的驱动装置有步进电动机、直流伺服电动机和交流伺服电动机等。
伺服系统是数控系统的执行部分,数控装置发出的指令依靠伺服系统实施,因此伺服系统是数控机床的重要组成部分。伺服系统分开环伺服系统、半闭环伺服系统和闭环伺服系统。在半闭环伺服系统和闭环伺服系统中,需要使用位置检测反馈装置,间接或直接测量执行部件的实际位移值,并与指令位移值进行比较,按闭环原理,将其误差转换并放大后控制运动部件的进给。伺服系统性能的好坏直接影响数控机床的加工精度和生产效率,因此要求伺服系统具有良好的快速响应性能,能准确而迅速地跟踪数控装置的指令信号。
4.检测反馈装置
检测反馈装置由检测元件和相应的检测与反馈电路组成,其作用是检测运动部件的位移、速度和方向,并将其转化为电信号反馈给数控装置,构成闭环控制系统。常用的检测元件有脉冲编码器、旋转变压器、感应同步器、光栅和磁尺等。开环控制系统没有检测反馈装置。
5.机床本体
机床本体是指数控机床的机械结构实体部分。和普通机床相比,数控机床同样包括机床的主运动部件、进给运动部件、执行部件和基础部件,如底座、立柱、工作台(刀架)、滑鞍和导轨等,不同的是数控机床的主运动和进给运动都是由单独的伺服电动机驱动的,因此其传动链短、结构比较简单。图1-7所示为数控车床的本体结构。为了保证数控机床的快速响应特性,在数控机床上普遍采用精密滚珠丝杠副和直线滚动导轨副;为了保证数控机床的高精度、高效率和高自动化加工,数控机床的机械结构具有较高的动态特性、动态刚度、阻尼精度、耐磨性和抗热变形等性能。除此之外,数控机床还配套一些良好的辅助控制装置,如自动换刀装置(ATC)、工件自动交换装置(APC)、冷却装置、润滑装置、排屑装置、防护装置及对刀/测量装置等,以便最大限度地发挥数控机床的功能。由于可编程序控制器(PLC)具有响应快、性能可靠、易于编程和修改等优点,并可直接驱动机床电器。因此,目前辅助控制装置普遍采用PLC进行控制。

图1-7 数控车床的本体结构
1.2.2 数控机床的工作原理
数控机床在加工工艺与表面成形方法上与普通机床基本相同,但在实现自动控制的原理和方法上区别很大。数控机床是用数字化信息实现自动控制的。在数控机床上加工零件时,要事先根据加工图样的要求确定零件的加工路线、工艺参数和刀具数据,再按数控机床编程手册的有关规定编写零件数控加工程序,然后通过输入装置将数控加工程序输入数控系统。在数控系统控制软件的支持下,这些加工程序经过处理与计算后,发出相应的控制指令,通过伺服系统使数控机床按预定的轨迹运动,从而进行零件的切削加工。数控机床加工零件的过程如图1-8所示。

图1-8 数控机床加工零件的过程
(1)加工程序编制。首先,根据图样对工件的形状、尺寸、位置关系、技术要求等进行工艺分析。然后,确定合理的加工方案、加工路线、装夹方式、刀具及切削参数和图形轮廓的坐标值计算(数学处理)等。最后,根据加工路线、工艺参数、图形轮廓的坐标值及数控系统规定的功能指令代码及程序段格式,编写加工程序。对编写好的加工程序进行程序仿真检验。
(2)加工程序输入。加工程序通过输入装置输入数控系统。目前,采用的输入方式主要有软驱、USB接口、RS232C通信接口、分布式数字控制(Direct Numerical Control,DNC)接口、网络接口等。数控系统一般有两种不同的输入方式:一种是边输入边加工,DNC属于此类输入方式;另一种是一次性把零件加工程序输入数控系统内部的存储器,加工时再由存储器一段一段地读出,软驱、USB接口属于此类输入方式。
(3)译码。数控系统接收的程序是由程序段组成的,程序段中包含零件轮廓信息、进给速度等加工工艺信息和其他辅助信息,计算机不能直接识别这些信息。译码就是按照一定的语法规则将上述信息解释成计算机能够识别的数据形式,并按一定的数据格式存放在指定的内存专用区域。在译码过程中对程序段还要进行语法检查,发现错误立即报警。
(4)数据处理。数据处理一般包括刀具补偿、速度计算及辅助功能的处理。刀具补偿包括刀具半径补偿和刀具长度补偿。刀具半径补偿的任务是根据刀具半径补偿值和零件轮廓轨迹计算出刀具中心轨迹。刀具长度补偿的任务是根据刀具长度补偿值和程序值计算出刀具轴向实际移动值。速度计算是指根据程序中所给的合成进给速度,计算出各坐标轴运动方向的分速度。辅助功能的处理主要指完成指令的识别、存储和设定标志,这些指令大都是开关量信号,现代数控机床可由PLC控制。
(5)插补计算。加工程序提供了刀具运动的起始点、终点和运动轨迹,而刀具从起始点沿直线或圆弧运动轨迹走向终点的过程则要通过数控系统的插补软件控制。插补软件的任务就是通过插补计算程序,根据程序规定的进给速度要求,完成在轮廓起始点和终点之间的中间点的坐标值计算,即数据点的密化工作。
(6)伺服控制和零件加工。伺服系统接收插补计算后的脉冲指令信号或插补周期内的位置增量信号,这些信号经放大器放大后驱动伺服电动机,带动机床的执行部件运动,从而将毛坯加工成零件。