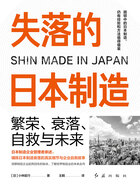
中小微制造企业挑起了“Made in Japan”的大梁
前述情况虽然只是我所知道的案例的一部分,但恐怕出海的多数品牌厂商都存在这样的情况。
品牌厂商是甲方,比我们下包公司的地位高。所以理所当然地认为自己在制造方面的水平比我们更高,但我不这么认为。
当时的日本,是由中小微制造企业制造出精确度出类拔萃的零部件,再发送给品牌厂商组装的。品牌厂商们据此生产的品牌产品才被称为“Made in Japan”。
那时候的品牌厂商接连不断地开发出富有魅力的产品,并将大多数相关零部件的制造工作都派单给了日本的中小微下包公司,从而获取了在严格的品控下,以低廉的成本制造出的毫无差错的零部件。
现如今,没有全部转移到海外而是在日本保留了制造体系的行业,如汽车、精密仪器、机床等,这些行业使用的大量零部件,仍然由我们这些中小微制造企业提供。
日本制造业的核心,说是我们中小微制造企业一点也不为过。虽说“Made in Japan”是“授予日本各个品牌的荣誉”,但持续提供高精度零部件的中小微制造企业才是真正的幕后英雄。
话虽如此,实际上,我们中小微制造企业却遭受了大量派单骤然停止的剧烈打击,经受了倒闭、破产、业务缩水等困难。
在这里,我想跟大家聊聊“Made in Japan”这曾经风靡世界的“制造力”的源泉。
日本在二战后的高度发展期,形成了以大企业(核心企业)为中心,下包企业层层环绕的结构。从一次下包开始,到二次、三次、四次下包……下包公司层层分包,最后甚至连接到家庭兼职。
当然,越往下分包,接单单位的成本就越低廉,生产车间和设备也就越简陋。
乍一看,这样的作业方式是不规范的,大品牌厂商恐怕会认为这种作业方式会产生大量的不合格品。但实际上正是像这样的下包公司和制造体制支撑起了日本品质即“Made in Japan”。
泡沫经济崩溃前,我们公司属于二次下包公司,分包母公司对我们的要求十分严格,近乎“PPM管理”100万个制品中不合格品不得超过1个的要求。
当然,由于成本原因,我们一直处于一个“半死不活”的状态,就像各位在前言图表中所见的那样,通常利润率在3%左右,最多不过5%。
这种分包模式的优势在于,当我们陷于困境时,分包母公司会给我们增加单量,也会融资给我们周转,同时还会对我们进行品质管理方面的指导。总而言之,就像亲子关系那样作为“母公司”给予我们照顾。
但对品质、交期,分包母公司会非常严格。每个月都会召开品质会议,在所有下包公司面前公布本月合格率最低的下包公司的名字。为了避免遭受这种羞辱,将品质保持在事前决定好的范围内成了理所当然的管理目标。
这种做法,在海外通常被称为“品质过剩”。但只有这种被认为是过剩的品质,才能够使产品的品质长期保持稳定,是日本得意的“磨合技术”的命门。
所谓磨合技术,是指“通过对构成产品的零件、材料进行微调整,完美展现产品性能”,磨合技术是日本的强项,也是日本产品品质优良不易损坏的主要原因。
当时的各大品牌厂商靠着优秀的设计、严格的品质体系(TQC, Total Quality Control),自上而下集合了几百家、几千家公司的优秀零部件,再组装出库。
除了这种自上而下铺开的品质控制管理制度,还有各家公司为了按期缴纳高品质零部件而绞尽脑汁优化生产流程的努力,和长期脚踏实地的工作精神。
这些公司的员工对品质的意识,对公司的归属感,都很强。他们不仅对自己的工作非常认真,对他人的不合格品也绝不放过。
之前,有个大型品牌厂商的人曾这样强调在海外开厂的优势:“每三年就可以更换一批从小地方出来打工的工人,可以一直聘用年轻的工人工作……”但在我们这些专注制造的人看来,这可真是胡说八道。
因为经验是制造的命根子。
经验老到的优秀工人清楚地记得曾经出现过的问题,就能在产品的生产制造过程中提前发现情况,预防问题再度出现。
无论生产指南的小册子写得多好,都赶不上人类的感性和熟练度。
如果有品牌厂商认为,3年左右就替换掉刚开始熟稔自己的工作并建立起工作信心的工人是理所当然的,那他们可真是大错特错了。
在终身雇佣制下长期工作于同一家公司的日本人,齐心协力打造了高品质的产品,向世界发出了振聋发聩的声音,那就是我理解的日本被全世界所期待,被全世界所赞叹的“Made in Japan”的真实内在。