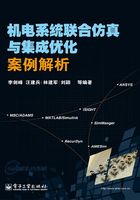
第1章 绪论
1.1 机电系统
1.1.1 机电系统的组成
机电系统又称为机电一体化系统,是一门交叉学科,它所涉及的主要技术科学领域包括传统的机械设计、电子技术、经典控制理论等内容,同时又包括现代信息处理技术、现代设计方法、软件工程,以及自适应控制、模糊识别、系统仿真、人工智能等现代控制技术,而且随着现代科学技术的发展,这些学科之间的相互渗透会越来越多,它们之间的界限将越来越模糊。
机电系统一般含有控制部分,因此往往将机电系统称为机电控制系统,如图1.1所示,通常由以下几部分组成:传感器、控制器、驱动装置、执行机构等。

图1.1 机电控制系统的组成
1.传感器
传感器主要用来从被测对象中提取各种信息,检测机电控制系统工作时所要监测的各种物理量,大多数传感器要将被测的非电信号转换为电信号。被测得的物理量一般有位移、速度、加速度、力、力矩、转角、流量、温度等。
2.执行机构
执行机构指的是直接推动被控对象,完成控制任务的机构,包括以电、气压、液压等为动力源的各种元器件及装置,如以电为动力源的直流电动机、三相交流异步电动机、交流永磁伺服电动机、步进电动机,以气压作为动力源的气动电动机和汽缸,以液压作为动力源的液压缸、液压电动机等。
3.驱动装置
驱动装置与执行机构相连接,给执行机构提供动力,驱动装置一般按不同的动力源分为三类:电动、气动、液压,主要功能是驱动各种执行机构。
4.控制器
机电控制系统的核心是控制器,机电控制系统的各部分均要由控制器实现协调与匹配,控制器测试传感部分的信息及外部直接输入的指令,进行集中、存储、分析、加工处理后,按照信息处理结果和规定的程序与节奏发出相应的指令,控制整个系统有目的地运行。
典型的机电一体化系统有数控机床、机器人、汽车电子化产品、智能化仪器仪表、电子排版印刷系统、CAD/CAM系统等。
1.1.2 机电系统的发展
现代机电产品正朝着智能化、模块化、网络化的方向发展。智能化主要体现在目前的机电产品在控制理论的基础上,吸收了人工智能、模糊数学、心理学、生理学和混沌动力学等新思想、新方法,模拟人类智能,使产品具有判断推理、逻辑思维、自主决策、故障诊断等能力,如具有模糊控制功能的全自动洗衣机、电冰箱等。
模块化主要体现在目前的一些机电产品已经具有标准机械接口、电气接口、动力接口、环境接口、机电一体化产品模块,这些模块化的设计为机电产品的选用、互相之间的连接提供了极大的方便。
机电产品的另一发展趋势是网络化,基于网络的各种远程控制和监视技术迅速发展,现场总线和局域网技术已在众多机电产品中得到了广泛的应用。
我国从20世纪80年代初开始进行机电一体化的研究和应用,国务院成立了机电一体化领导小组并将其列为“863计划”,许多大专院校、研究机构及一些大中型企业对这一技术的发展及应用做了大量的工作。数控技术起步于1958年,到“九五”末期,国产数控机床的国内市场占有率达50%。工业机器人方面,我国1986年将机器人的研究开发列入国家科技计划,现已掌握了机器人操作机的设计制造技术、控制系统和软件编程技术、运动学和轨迹规划技术,生产了部分机器人的关键元器件,并进入实用化阶段,已开发出可用于装配、能前后行走、爬墙、水下作业的多种机器人。目前,国内相关科研机构和企业已掌握了工业机器人操作机的优化制造技术,机器人软件的设计和编程等关键技术,还掌握了弧焊、点焊及大型机器人自动生产线(工作站)与周边配套设备的开发和制备技术。
在计算机集成制造系统(CIMS)方面,我国经过多年的理论和技术准备,CIMS已经有了较快发展。目前,已在清华大学建成了国家CIMS工程研究中心,在著名高校和研究单位建立了7个CIMS单元技术实验室和8个CIMS培训中心。当前,CIMS的进一步试点推广应用已经扩展到机械、电子、航空、航天、轻工、纺织、冶金、石油化工等诸多领域,正得到各行各业越来越多的关注和投入。
随着我国对外贸易持续快速增长,机电产品出口也步入了世界前列,但我国机电产品出口增长的质量还不高,尤其缺乏自主出口品牌。目前我国自主品牌出口所占比例较低,而机电产品名牌更是少之又少,绝大部分出口是使用外方品牌的加工贸易和以贴牌为主的订单贸易。
总的来说,我国机电产品设计水平与国际先进水平相比还有相当大的差距,主要表现在产品设计水平的落后导致产品性能、质量的落后,且设计基础数据缺乏,设计规范、手册陈旧,设计方法落后,对不少先进产品的设计还没有掌握。
1.1.3 机电系统的现代设计方法
在市场发展越来越成熟的今天,现代机电产品所涉及的学科和工业门类众多,用传统的设计方法很难达到设计的要求。因此,对现代的机电产品来说,其设计思想和设计方法都会有一些全新的内容。
现代设计方法包括计算机设计计算、优化设计、反求工程、现代设计方法学、工业艺术设计、价值工程等。
机电产品现代设计理论与方法领域有待重点解决的科学问题包括仿真与虚拟设计,建模/仿真方法学,分布式仿真系统,虚拟制造产品数字化设计、功能仿真、性能模拟及工艺设计技术,实现虚拟加工、装配、拆卸、工艺评估及决策支持的系统工具。
与传统设计理论与方法相比,现代设计理论与方法具有创新性,数字化、网络化、协同化、智能化、虚拟化等是其主要特点。设计理论与方法从“传统”走向“现代”,体现了现代设计理论与方法的科学性、前沿性。
传统的产品开发流程如图1.2所示,主要经过方案设计、工程图、样机制作、试验评估及生产几个步骤。

图1.2 传统的产品设计流程
可以看出,传统的产品开发过程主要依靠产品开发人员的经验,而且产品的性能只有在样机制造完成后才能够通过产品一系列的性能试验对设计结果进行评判。试验中发现的问题,必须等到下一次设计才可能修改,因此传统的设计过程一般需要通过反复多次才能最终满足设计要求,所以,开发周期较长、质量差,开发流程已越来越难以满足产品开发的要求。
采用多软件联合仿真的现代产品设计流程如图1.3所示。

图1.3 现代产品设计流程
从流程图可以很明显看出,与传统的产品开发流程相比,采用多软件联合仿真的产品开发流程由于在设计阶段就可以对各种方案进行分析、对比和优化,可以在物理样机制造之前预测产品的各项性能指标,从而大大减少了生产与试验评估的次数,提高了开发效率,节约了开发经费。