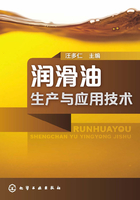
1.2 稀土纳米聚烯烃
聚烯烃以聚丙烯为例,英文名称:polypropylene,CAS号:9003-07-0,MDL号:UD1842000,Pub Chem号:24866797。分子式(C3H6)n,白色粉末,密度(25℃)0.9g/cm3,熔点189℃。溶解性:溶于二甲基甲酰胺或硫氰酸盐等溶剂。
技术指标
生产技术
聚烯烃的生产方法有高压聚合、低压聚合(包括溶液法、浆液法、本体法、气相法)。聚烯烃的无规共聚物其结晶度、刚性,熔点比均聚物低,透明性获得改进,韧性和冲击性提高。一般无规共聚物中乙烯结合量提高1%,熔点降低5℃。气相法可生产高乙烯含量如12%的无规共聚物,丙烯与高碳1-烯烃的无规共聚物及三元共聚物如丙烯-乙烯-丁烯的三元共聚物等产品的应用范围能进一步拓宽。
纳米粉末材料是指平均粒径在100nm以下的材料。其中平均粒径为20~100nm的称为超细粉。纳米粉末材料具有相当大的相界面面积,它具有许多宏观物体所不具备的新奇的物理、化学特性,既是一种多组分物质的分散体系,又是一种新型的材料,能赋予基体材料新的功能。其关键技术:催化剂。
生产实例一 采用金属茂催化剂
在1980年德国科学家研究发现二茂基氯锆和甲基铝氧烷组成的复合催化剂具有高度催化活性。这种新型催化剂体系,是将金属茂和催化剂沉积在纳米二氧化硅载体上,具有催化效率高、价格便宜。用新型金属茂催化剂可生产纯度100%的烯烃共聚物。
这种新型催化剂分子在结构上和电子性能上同茂金属相似,含5个碳原子和一个硼原子;催化剂是二氯二乙基硼苯基锆,能在1atm(1atm=101325Pa)下和稍高于室温下使烯烃聚合。这种催化剂的活性极高,能精确控制聚合物分子链的长度。茂金属化合物和一些硼化合物等构成复合物时形成茂金属阳离子,对烯烃聚合产生良好的活性。
采用等规优异的茂金属催化剂和MAO组成的催化剂体系进行环戊烯的聚合,可选择性地得到加成体,此环状烃为聚合物,呈现出非常高的熔点,用于乙烯与烯烃聚合的催化剂为CpTiCl3/NSiO2(N-SiO2是用3-丙氨基三甲氧基硅烷与二氧化硅作用得到的载体),用于乙烯与辛烯的聚合,得到辛烯含量为37%的分子量分布窄的共聚物。
采用茂金属与Z-N复合催化剂可加速生成聚合物的反应,可使反应速率成倍增加。这种催化剂的制法是:将二氧化硅于600℃高温下焙烧后溶于异戊烷中,再将此悬浮液先后与二丁基镁、正丁醇反应,除去溶剂得自由流动的白色固体,含钛1.6%、镁1.38%。
将此固体悬浮液滴入(BuCp)2ZrCl2/MAO的甲苯溶液内,于55~60℃下脱除甲苯制成自由流动的茶色载体催化剂,含钛1.09%、镁0.9%、铬0.42%。
生产实例二 双金属复合催化剂
利用金属茂催化剂与齐格勒-纳塔催化剂的性能特点可制备双金属复合催化剂,生产双峰或宽分子聚合物。
具体制法是:将处理过的SiO2-异戊烷悬浮液相继与2mg BaCl2、亚丁醇和TiCl4反应,除去溶剂后,得白色固体,含Ti 1.6%、Mg 1.38%。
将此固体悬浮物滴入(BuCp)2ZrCl2/MAO的溶液中,于55~60℃下脱除甲苯得自由流动的茶色载体催化剂,含Ti 51.09%、Mg 0.90%、Zr 0.42%。用此Ti/Zr双峰催化剂可制备乙烯/1-己烯共聚物,用以改善加工性能。
生产实例三 超高效催化剂
Shell公司利用UCC公司的气相聚合技术和Shell公司的超高效催化剂制取丁-丙共聚物。
催化剂制备方法:使无水氯化镁47.6g、250mL萘烷与230mL 2-辛醇于130℃下反应3h制成均匀溶液后,再加入7.4mL的苯甲酸乙酯,于-10℃下边搅拌边滴加1500mL四氯化钛,在950r/min下,于90℃反应2h制成催化剂,含Ti 3.8%。
反应使用串联反应器,在第一反应器内加入130L己烷,升温至60℃,以己烷35L/h、三乙基铝45mmol/h、催化剂以原子钛1mg/h、乙烯4.3mol/h的流速同时输入反应器内,维持反应压力0.47MPa,反应器液体量保持130L,用泵将第一反应器内液浆输入第二反应器内,在第二反应器内以己烷25L/h、乙烯气体11.2mol/h的流速连续加入反应器内,再将适量氢气加入反应器的气相中,使乙烯与氢气的摩尔比为100:3,反应器内液体保持120L,聚合操作条件为温度85℃,压力0.72MPa,制成共聚体产物经离心分离,在N2气流下干燥制得。
用负载茂金属催化剂及载体包括纳米蒙脱土、纳米皂石、纳米锂蒙脱石、合成云母、海泡石等为原料,经胺盐、氨基酸等处理而成的纳米材料,比表面积为100~640m2/g。由于采用纳米材料为载体,提高了催化剂的负载率、降低了助催化剂的用量,大大降低了催化剂的生产成本。该催化剂适用于烯烃聚合,性能优于粉末负载型催化剂制品。这类以铁和钴的配合物(配合物)为主成分的催化剂据称具有与茂金属催化剂相同的许多优点,它们和茂金属一样,能进行聚合的控制和同样的高活性。
生产实例四 负载齐格勒-纳塔催化剂
MgCl2-SiO2复合载体负载的齐格勒-纳塔催化剂不仅具有MgCl2载体负载催化剂的高活性,也具有SiO2载体负载催化剂的良好颗粒形态和分散流动性,而且还具有聚合反应平稳、聚合物颗粒形态好、堆密度大和细粉含量低等优点,是气相法聚乙烯催化剂中最为重要的一种。
电子给体在齐格勒-纳塔催化剂发展过程中起着举足轻重的作用,使它可以改善复合载体负载的齐格勒-纳塔催化剂中部分活性中心上单体的聚合速率,使聚合物的堆密度和熔体流动指数得到提高。
采用DOP为内给电子体,制备MgCl2-SiO2复合载体负载的齐格勒-纳塔催化剂。MgCl2:纯度99.9%。SiO2:955型,使用前经程序升温焙烧处理。正癸烷:分析纯,使用前经4A分子筛脱水。异辛醇、正己烷:分析纯,使用前经4A分子筛脱水。甲苯:分析纯,使用前经4A分子筛脱水。DOP:分析纯,使用前经4A分子筛脱水。三乙基铝:用正己烷稀释,1.0mol/L。1-己烯:质量分数97%使用前经4A分子筛脱水。乙烯:纯度99.99%。
(1)催化剂的制备 在氩气保护下,向反应器中依次加入正癸烷、MgCl2和异辛醇,并在一定温度下反应得到MgCl2醇化合物溶液,再向MgCl2醇化合物中加入一定量SiO2,反应一段时间后降温,滴加一定量的DOP与TiCl4,滴加完毕后缓慢升温,在一定温度下反应一段时间,用甲苯和正己烷洗涤产物并干燥,得到MgCl2-SiO2复合载体负载的齐格勒-纳塔催化剂。
(2)乙烯与1-己烯共聚实验 用N2气将高压反应釜反复置换3次以上,加入正己烷,同时加入三乙基铝、1-己烯和催化剂,开启搅拌(转速为400r/min),升温至70℃时通入H2,待反应釜内温度升至80℃时通入乙烯聚合。反应过程中,釜内总压保持在1.00MPa,反应2h。
研究表明:加入DOP可以改善催化剂的颗粒形态和均匀程度,且随着DOP加入量的增加,催化剂活性降低,共聚物的堆密度和熔体流动指数呈先升高后降低的趋势。当n(DOP):n(Mg)=0.10时,催化剂的形态和性能较好,共聚物的堆密度为0.35g/cm3,熔体流动指数(10min)为0.18g,粒径为75~750μm的颗粒的质量分数为98.36%。
生产实例五 乙烯-丙烯共聚物
本工艺涉及的支化聚烯烃聚合物的使用作为石油馏出物中的添加剂,如在燃料和润滑油中作为分散剂、清洁剂和/或增强性能的黏度指数改进剂。支化聚烯烃聚合物在掺入润滑油时,作为添加剂的组分可以赋予改善低温黏度和增稠效率但并不会产生不利配制的油的机械剪切稳定性影响。少量的支化聚烯烃聚合物混入配方中还可赋予洗涤剂和分散剂的属性。
作为众所周知的已经采用的烃类聚合物,石油馏出物的黏度随温度变化,特别是润滑油要求在更加广泛的温度范围内使用,润滑油添加剂的黏度指数越高,黏度随温度的变化越小。因此,在低温下的润滑油,可同时提供大的在发动机运转温度下的黏度。
美国专利US3522180、US3524732、US3879304、US4026809、US4089794、US4137185、US4146489、US4171273、US4320019、US4340689、US4357250、US4382007、US4500440、US4640788、US4699723、US4715975、US4732942、US4764304、US4812261、US4816172、US4820776、US4842756中基本上为线型的烯烃共聚物,尤其是乙烯-丙烯共聚物(以下简称为OCP)已被采用作为润滑油的黏度指数改进剂、倾点下降剂和分散剂。
美国专利US3697429、US4507515、US5391617和US5451630中所述的线型乙烯-丙烯共聚物的组分可以进行调整,使增稠力和机械剪切稳定性之间具有优异的平衡性。为了实现最佳性能,通常测量-25℃下的剪切黏度。
美国专利US4116917、US4141847、US4788361、US4557849、US4849481、US4156673中所述的氢化的星形支化聚合物已用于改善低温的润滑油组分的流变学性质。这些氢化的星形聚合物中也可任选含有单体单元的单链烯基芳族的烃和用偶合的方法制备。
美国专利US4141847、US4358565、US4409120、US4427834、US4868245、US5141996、US5147570中所述的这些已官能化的二烯和任选的乙烯基芳烃的星形聚合物,不仅可提高稀释油的性能,还能达到其他可取的多官能的性能标准,如改进的剪切稳定性与润滑油的流变性能。
在美国专利US5030695技术中描述了一种用于生产聚烯烃的星形聚合物。在实例中,描述的是乙烯-丙烯共聚物,其中乙烯、丙烯和降冰片二烯共聚形成结节状的支链结构。另一个例子描述的是羟基封端的乙烯-丙烯共聚物,将其溶解在干的润滑油中。
本工艺的目的之一是提供燃料和润滑油添加剂组分的支化聚烯烃聚合物,之二是提供烯烃支化聚合物添加剂如洗涤剂、分散剂。
本工艺所用的双官能团的聚合性单体,可以选用丙烯酸或甲基丙烯酸酯、酰胺、酰卤或酸酐、乙酸乙烯酯、乙烯醇、乙烯基胺、乙烯基异氰酸酯、乙烯基硫醇类、乙烯基环氧化合物等。
在本工艺中丙烯与乙烯和任选的二烯单体的共聚单体是优选的,使用的乙烯共聚体,1-烯烃和共轭多烯单体可以是1,4-己二烯和7-甲基-1,6-辛二烯,α,ω-链二烯,如1,7-辛二烯和1,9-癸二烯、二聚环戊二烯、降冰片二烯及链烯基降冰片烯等。
本工艺使用金属茂催化剂生产分枝聚烯烃。所用的“金属茂催化剂体系”是指使用的过渡金属化合物包括金属如钛、锆、铬、铪、钇,含有至少一个是高度共轭的有机化合物的配位体(例如,环戊二烯或茚)。这种催化剂体系在美国专利US5017714、US5055438、US5064802、US5091352、US5120867、US5132262、US5171799、US5206197、US5281679、US5296433、US5321106、US5329033、US5374752、US5391789、US5441920中已经做了说明。可用作润滑油组合物中添加剂的聚烯烃支化聚合物,优选的Mn的范围是1000~10000。
下面介绍几种端不饱和预分枝聚烯烃的制备方法和步骤。
聚合物A 乙烯-丙烯聚合反应在1.5L的间歇式反应器中进行。向反应器内通入用300mL己烷。随后用乙烯(C2)和丙烯(C3)将反应器加压到0.8MPa,在反应器部的顶部空间达到丙烯与乙烯的摩尔比为2:1。控制反应器中的温度保持在40℃。随后通入4μmol的S-(2-茚基)2ZrCl2(硫桥接二茚基二氯化锆)和5mmol甲基铝氧烷。在聚合过程中单体浓度尽可能地保持恒定的剂量为20000L/h丙烯和100L/h乙烯。30min后减压,聚合反应结束。将聚合物溶液回收,蒸出溶剂,聚合物在真空、80℃下干燥。
聚合物B 乙烯-丙烯聚合反应在1.5L的间歇式反应器中进行。向反应器内通入300mL己烷,随后通入乙烯(C2)和丙烯(C3)将反应器加压到0.8MPa,在反应器部的顶部空间达到丙烯与乙烯的不同摩尔比。反应器中的温度保持在40℃。所用催化剂为Et(1-茚基)2ZrCl2,甲基铝氧烷作为助催化剂。在聚合过程中单体浓度尽可能地保持恒定的剂量为20000L/h丙烯和100L/h乙烯。30min后减压,聚合反应结束。将聚合物溶液回收,蒸出溶剂,聚合物在真空、80℃下干燥。
聚合物C 按照聚合物A的反应过程在反应器内进行乙烯聚合。向反应器中加入750mL五甲基己烷。接着,将反应器加压至0.8MPa,保持反应温度在185℃。接着加入MgCl2附载的钛催化剂(钛的浓度为0.002mmol/L)和0.05mmol/L的三乙基铝。乙烯在聚合过程中压力尽可能地保持恒定。10min后减压终止聚合反应。通过蒸发溶剂和在60℃下真空干燥回收聚合物。
聚合物D 按照聚合物A的反应过程在反应器中将丙烯进行聚合。向反应器中加入500mL庚烷。接着,将反应器加压至0.7MPa。将反应器的温度保持在40℃。接着加入Me2Si(2,4-Me2 Cp)2ZrCl2[二甲基硅烷桥二(2,4-二甲基环戊二烯)二氯化锆]和32mmol/L的甲基铝氧烷。丙烯在聚合过程中压力尽可能地保持恒定。30min后终止聚合反应器中减压,通过蒸发溶剂和在60℃下真空干燥回收聚合物。
聚合物E 按聚合物B的步骤进行乙烯-丙烯-1-辛烯的三元共聚合,将单体和催化剂组分连续地供给到反应器中,将聚合物溶液从反应器中连续地除去。
生产实例六 聚α-烯烃
取AlCl3摩尔分数4%和n(AlCl3):n(乙酰丙酮)=2:1加入干燥的100mL锥形瓶,搅拌均匀后缓慢滴加14.8g(20mL)1-辛烯(纯度99%),恒温水浴控制并保持反应温度25℃,反应4h时间后将产物移入分液漏斗。经碱洗、水洗至中性后静置分离,减压蒸馏除去未反应单体,封存。采用蒸馏前后分别称重的方法计算PAO收率为96%。聚α-烯烃黏度指数为173,凝点-40℃。
色谱条件 液相反应产物采用SP-6000型气相色谱仪进行定性与定量分析,色谱柱长30m,采用氢火焰离子化检测器,进样量0.2μm。程序升温条件:50℃保持4min,以10℃/min速率升温至300℃,保持20min。按面积归一法计算质量分数。
以AlCl3-乙酰丙酮配合物为催化剂,1-辛烯为原料低聚成聚α-烯烃来合成润滑油。最佳工艺条件为AlCl3摩尔分数4%,n(AlCl3):n(乙酰丙酮)=2:1,反应温度25℃,反应时间4h。
生产实例七 聚α-烯烃合成油制备过程中BF3配合物的分离及回收
聚α-烯烃合成油(PAO)是由α-烯烃在催化剂作用下经低聚反应和加氢饱和反应制得的纯度非常高的油品。与矿物基础油相比,PAO具有黏度指数高、倾点低、高氧化安定性、低挥发性等优点,并且可根据需要调整原料组分和聚合度,获得黏度范围较宽的产品。聚α-烯烃合成油的性能好坏主要取决于PAO产品的聚合度和分子量分布,因此,选择合适的催化剂是提高产品质量的关键。
目前用于α-烯烃低聚反应制备润滑油基础油的催化剂体系包括茂金属催化剂、铬金属催化剂、路易斯酸催化剂、Z-N催化剂和离子液体催化剂等。制备PAO完成后路易斯酸配合物必须从产品流中加以分离、脱除及回收,原因如下:①提高聚α-烯烃产品质量;②节约催化剂成本;③减少催化剂排放对环境的污染。BF3配合物是路易斯酸配合物催化剂的典型代表,国外低黏度合成油有80%以上采用BF3配合物作催化剂。
以BF3配合物为例,吸附法分离回收BF3配合物的原理是将聚合反应后的液流与固体吸附剂接触,其中BF3被吸附,从有机液体中分离出来,吸附饱和后用加热、N2置换等方法解吸BF3。常用的吸附剂有SiO2、聚乙烯醇、聚丙烯腈、金属氟化物。SiO2吸附法用SiO2颗粒吸附聚合反应有机液中的BF3,吸附在较低温度下进行,吸附饱和后,低压加热SiO2到100℃释放BF3。此方法可以将BF3从配合物中分离出来,极性化合物留在有机液中。为了提高吸附效率,结合现代高新技术对SiO2颗粒作改进,如将SiO2制成纳米SiO2、微球SiO2,增大吸附剂的比表面积。SiO2颗粒内存在硅氧烷、硅烷醇基等官能团,可能会将BF3分解,造成分离出来的BF3难以再利用。所以,在SiO2吸附剂制备过程中应该尽量提高SiO2纯度,减小杂质基团硅氧烷、硅烷醇等对吸附的不利影响。
金属氟化物吸附法用金属氟化物(可以是锂、钙、锶或钡)分离及回收BF3配合物。金属氟化物选择性吸附配合物中的BF3生成四氟硼酸盐。将四氟硼酸盐加热分解成BF3和金属氟化物,解离后的金属氟化物循环利用。此法可以高效分离回收催化剂,没有副产物,并充分利用了金属氟化物和BF3的化学性质,两者之间的吸附属于化学吸附,吸附选择性大,吸附作用强。
对于吸附法的研究主要集中于新的无毒、高效、可再生吸附剂的开发和已有吸附剂的优化改进。以上几种吸附剂中,SiO2颗粒和金属氟化物是具有较为应用前景,这两种吸附剂工业上应用广泛、无毒,可循环使用。对这两种吸附剂的进一步研究可以从以下两方面展开:①利用现代高新技术处理吸附剂,增大吸附剂的比表面积,提高单位质量吸附剂的吸附量;②进行吸附和脱附条件的研究,优化实聚合油中使用最广的低黏度油,占整个PAO用量的90%,主要用于发动机油、液压油、ATF液、齿轮油、军事工业用油、近海钻井液、光纤填充油等。低黏度润滑油生产过程中多以路易斯酸配合物为催化剂,采用此类催化剂生产的聚合油具有收率高、分子量分布窄、选择性好等优点。
各种方法和工艺中,目前实现工业化的只有裂解法,裂解方式有闪蒸、真空蒸馏、热N2吹扫、直接加热等。若选用热N2吹扫和直接加热裂解,要注意加热温度的控制,尽量减少由热裂解引起的烯烃异构化等副反应。若选用真空蒸馏和闪蒸的裂解方式则要注意裂解压力的控制,尽量保证裂解充分。在各种裂解方式中,裂解效果最好的是真空蒸馏裂解,其次是热N2气提裂解。国外对PAO制备过程中BF3配合物分离及回收的研究开展较早,技术较先进,对于工业上规模较大的PAO制备过程中BF3配合物的分离及回收优先选用裂解法,结合具体情况选用合适的裂解方式,再与其他化工单元操作相结合。
在美国专利US4032591、US44331971、US4227027、US5846429、 US69399439、US39297491、US6410812B1中对此工艺有较为详细的说明。
应用技术
应用实例一 乙烯-1-丁烯共聚物润滑油
本工艺涉及乙烯和1-丁烯的衍生聚合物,特别适合用作润滑油添加剂。本工艺还涉及改善油溶性分散剂添加剂的润滑油组分中的聚合物的制备。
混合物典型地包括至少一种烃基础油和一种或多种添加剂,其中各添加剂用于改善性能和属性为应用的目的,例如,用于润滑油、加热油、柴油机油、中间馏分的燃料油等。
改进剂一般为油溶性的聚合物长链,通常的烃类聚合物的数均分子量在20000~200000的范围内。润滑油组分含有典型添加剂,也可以影响该组分的黏度特性。分散剂是通常提供的亲油性组分的油溶性和极性组分的聚合材料,通常具有的数均分子量为10000或更小。分散剂为包含氮和酯基的烃类聚合物。最常用的是聚异丁烯的烃类聚合物,其他也可以采用烃类聚合物,如乙烯-α-烯烃共聚物。其主要功能是保持油中的悬浮液在使用过程中通过氧化等形成任何不溶性物质,从而防止淤渣絮凝和产生沉淀。分散剂的量取决于所控制的有效性功能的特定的材料。市售的发动机油通常包含尽可能多的活性成分,分散剂约为4倍。
本工艺配制成的分散剂和改良剂足以满足低温和高温黏度要求,而且还能达到有效分散和满足其他性能标准,如倾点和浊点,这可能需要添加其他的添加剂。
在最常规的分散剂中,聚异丁烯(PIB)的烃链数均分子量(Mn)为900~2500。当聚异丁烯的分子量小于300时结果性能很差,Mn小不足以维持充分溶解在润滑油中的分散剂。另外,超高分子量PIB(Mn>3000)在许多操作下变得非常黏稠,难以处理。PIB分子量增加至5000~10000时该问题变得更加严重。
末端烯键式不饱和的聚异丁烯(所谓的“反应性聚异丁烯”)的聚合由BF3催化。具体可参见美国专利US4152499。然而,反应性聚异丁烯仍可含有大量的不饱和链。
乙烯-1-丁烯共聚物的制备:在连续聚合中,连续地注入乙烯气体进入液体中,组分基于单体总重量40%(质量分数)的1-丁烯、含8.5%(质量分数)的乙烯和60%(质量分数)的异丁烷。含有乙烯、1-丁烯和异丁烷以568L/h的连续速率加入配有搅拌器的沸腾反应器内,反应器还配有用于控制温度的速率约370kg/h的给水夹套,其特征在于在反应器中形成的塔顶的蒸汽经回流冷凝器冷凝并返回到反应器中。催化剂溶液的制备是将固体1,1'-二甲基甲硅烷-双(4,5,6,7-四氢茚基)二氯化锆溶解在10%(质量分数)的甲基铝氧烷-甲苯溶液中,使得Al:Zr的摩尔比为500:1。将催化剂溶液连续泵入沸水反应器中的速率应足以提供的Zr物质的量浓度为2.5μmol/L。反应器的温度保持在160℃,压力保持在170~175psi(1psi=6894.76Pa)(约13X105Pa),连续搅拌反应的速率为300r/min,在反应器中的停留时间为1h。
从沸腾的反应器中连续供给的商品流经骤冷鼓,与350μmol/L NH4OH水溶液接触后从产物中除去未反应的单体、溶剂、水和骤冷氮气汽提聚合物产品,然后过滤,以除去催化剂残余物。
乙烯-1-丁烯共聚物的产量是约70kg/h。该共聚物的乙烯含量为22.8%(质量分数),通过1 H NMR测定分析,该聚合物的Mn 为4666,MWD(分子量分布)为2.3。
应用实例二 乙烯-1-丁烯共聚物润滑油
按上例的方法,控制反应器中的温度和压力分别为175℃和225psi(约16.5bar),在此条件下进行聚合。此外,反应物流包括38.5%(质量分数)1-丁烯和足以提供19%(质量分数)的乙烯,基于单体总质量61.5%(质量分数)的异丁烷组成的液流,加入速率为403kg/h。乙烯-1-丁烯共聚物的产量是98kg/h。该聚合物的乙烯含量为38.9%(质量分数),Mn为4325,MWD 为2.34。
应用实例三 再生润滑油
润滑油由80%~90%的基础油和10%~20%的添加剂组成,主要化学成分是多种烃类以及少量非烃类的混合物。主要应用于设备的润滑,还可用于消除噪声和冷却。润滑油在长期使用过程中,因为氧化作用产生了许多氧化物,如羧酸和有机酸的盐类、沥青质、炭渣、油泥;由于机械部件的磨损,润滑油中会混入金属屑;发动机润滑油会混入水分、油泥和炭粒,使用一段时间还会被汽油和柴油等稀释而造成闪点下降、黏度变小,从而失去原有油的使用性能,上述原因造成不能继续使用的润滑油统称为废油。
其实,在废润滑油中真正变质的只是其中的百分之几,主体仍为基础油。我国目前对废润滑油的回收利用率只有20%,多数废润滑油被直接排放或被作为燃料燃烧,严重污染了环境。因此,开发废润滑油再生技术对保护环境、节能降耗有十分重要的意义。
废润滑油再净化技术包括沉淀、离心、过滤、絮凝、吸附等技术。其中,沉降、离心、过滤可去除废润滑油中的水分和一般悬浊的杂质。加入一种具有氨基结构的化合物作为絮凝剂,可使细小的胶体颗粒凝聚成大的颗粒,通过沉降或离心达到分离的目的。
该絮凝剂中氨基基团的氮原子还可受废润滑油中氧化物的氧原子吸引而导致氨基中的氢原子活泼起来形成氢键,使废润滑油中的氧化物钝化,同时通过吸附架桥、沉淀物网捕作用把废润滑油中的积炭、颗粒和胶泥等缠绕包裹起来,在外界提供的动力情况下脱稳沉淀下来。在絮凝剂用量为1.2%(体积分数)、搅拌时间为5min、反应温度为750℃、沉降温度为800℃、沉降时间为2.0h的条件下,废润滑油絮凝脱色效果最佳。废润滑油经过絮凝脱色和白土精制后理化指标得到了较大改善。
应用实例四 废润滑油的再生处理
采用磺酸盐阴离子表面活性剂与聚氧乙烯非离子表面活性剂复配絮凝剂,以活性白土为吸附剂,对废润滑油进行再生处理。最佳絮凝条件:温度为850℃,150g废润滑油所需2种絮凝剂用量分别为3.7g和1.3g。最佳吸附条件:活性白土用量为12.3%,温度为1100℃,时间为90min。
用再精制的方法对废润滑油进行再生。再精制方法主要有硫酸-白土精制、加氢精制、溶剂精制等。
硫酸-白土精制技术对劣化程度较深的废润滑油再生,可以去除废油中的含氧化合物、含硫化合物、含氮化合物,以及使用过程中产生的胶质、沥青质、沥青酸、炭粒等,再生后的油质较好,可以达到基础油的标准。改进的硫酸-白土技术,可以使酸渣进行循环使用,改变硫酸的加料次数等。
加氢精制是在氢气加压和催化剂存在下,使油品中的硫、氧、氮等有害杂质转变为相应的硫化氢、水、氨而除去,并使烯烃、二烯烃和芳烃部分加氢饱和,以改善油品的质量。
小分子烷烃精制是基于小分子烃溶解润滑油中分子量较低的烃类等理想成分,而分离出分子量高的非理想组分的原理。目前,用乙烷、丙烷等小分子烷烃进行废润滑油再生,采用该方法对废润滑油再精制,所得油品品质较好。
精制的原理是对废润滑油中的极性非理想成分(如芳烃、烯烃、含氧化合物)具有较大的溶解度,因此,在溶剂精制过程中,非理想组分逐渐溶解于溶剂中,从而达到非理想组分和理想组分的分离,实现废润滑油的再生。
用NMP(甲基吡咯烷酮)精制对废润滑油中的非理想组分具有很好的溶解能力和选择性,并且具有高化学稳定性、热稳定性和低毒性等优点,是一种绿色溶剂。
分子蒸馏是一种高效的非平衡蒸馏技术,减压蒸馏是废润滑油再生工艺中精制程度最深、再生效果最好的技术,是一种高效的非平衡蒸馏技术。
将20.0kg废润滑油80%加温沉降10h,用过滤袋精细过滤。滤液预热至120℃,送入精馏塔精馏。
改进的填料精馏塔适合高黏度度润滑油的精馏,用以脱除其中的溶剂油等轻组分;设备为精馏塔的再沸器,冷凝器集轻柴油冷凝器捕集汽油及水分。
分子蒸馏能够达到的真空度,理论操作温度可根据Clausius-Clapeyro方程得出,三级分子蒸馏的温度为190℃、233℃、325℃。三级均采用导热油加热和调温水冷凝。
用泵将原料输送至分子蒸馏柱中进行第一级馏分切割;第一级的轻组分作为第一级产品保存,极少量不能被捕获的轻组分进入冷凝器中冷凝;重组分为分子蒸馏的原料进行第二级馏分切割;依此类推至第三级,重组分成为蒸馏残渣。
对废润滑油分别进行糠醛-NMP精制实验结果表明:糠醛精制的最佳的剂-油比为1.5,最佳精制温度为800℃,NMP精制的最佳剂-油比为1.0,最佳精制温度为600℃。在最佳工艺条件下,回收的废润滑油黏度指数为102.6。
应用实例五 离心法除渣工艺
对装置沉降产生的含沉渣聚α-烯烃合成润滑油(PAO)加热至80℃后,对直接离心分离和加白土助剂离心分离条件为:离心机转速7000~8000r/min,离心时间0.5~1h,相对于24h以上的沉降法除渣工艺,离心法除渣可以实现快速分离,收率也比沉降法除渣高3%。
一步除渣法是烯烃聚合反应后先不除渣,在进行中和反应及白土精制后通过过滤进行除渣,在不同的Ca(OH)2加入量(4%)和等量的白土(3.0%)下,Ca(OH)2的加入量对收率的影响不明显,产品收率在89%~91.33%之间一步除渣工艺提高了7%以上。随着Ca(OH)2用量的增加,过滤越来越容易,过滤速率也越快。
应用实例六 燃料配方(体积分数,%)
应用实例七 PAO的生产
将AlCl3与α-烯烃(1-辛烯、1-癸烯或它们的混合物)加入三口瓶,充分搅拌,温度明显上升(一般为25~30℃)时水浴冷却;上升至80℃时开始聚合,由于该聚合反应为放热反应,反应温度会继续升高,在AlCl3加入量相同的情况下,不同α-烯烃聚合可达的最高温度不一样;当温度升至最高点后开始下降,此时开始加热,温度升至140~150℃时恒温2h,反应过程中保持搅拌;随后至少静置24h,当温度降至50℃时加入Ca(OH)2,升温至80℃恒温10min,加入活性白土,继续升温至140~150℃恒温1h;过滤并将滤液进行减压蒸馏,蒸出轻组分,剩余馏分即为PAO。
以1-辛烯或1-辛烯与其他α-烯烃混合后的烯烃为原料制备PAO,采用单一的1-辛烯制得的PAO的运动黏度高于采用混合烯烃原料制得的PAO,而黏度指数则低于采用混合α-烯烃原料制得的PAO。不同原料制得的PAO的凝点均不同。
采用不同的α-烯烃制备PAO时,AlCl3用量不同,所制得的PAO的性能不同。
当采用1-辛烯为原料时,PAO的收率和运动黏度均随AlCl3用量的增大呈先增大后减小的趋势,当AlCl3用量为3%(质量分数)(基于α-烯烃的质量)时,运动黏度达最大值;黏度指数则随AlCl3用量的增大而减小,但降幅不大。当采用1-辛烯为原料时,选择AlCl3用量为2%~3%(质量分数)较适宜。
α-烯烃中具有广泛用途的是C6~C18(或C20)直链烯烃,国外通常采用性能更优越的C8~C20。正烯烃为原料生产聚α-烯烃合成润滑油基础油(PAO),且产量呈逐年上升趋势,年均增长率为10%~15%。PAO具有黏度指数高、凝点低和高温氧化稳定性优良等特点,尤其是其黏温性能、低温性能以及热氧化安定性的综合性能好,是最具发展潜力的合成润滑油。
合成润滑油是指完全采用有机合成方法制备,具有一定化学结构和特殊性能的润滑油。国外早期采用石蜡裂解法生产α-烯烃,所得到的液态混合α-烯烃主要为C6~C18,其中正构烯烃约占40%。采用C8~C10为原料制得的PAO,黏温和低温性质都极佳,对各种添加剂相容性良好,可作为高档合成润滑油。
综合述评
PAO具有液相范围宽、黏温性能好、倾点低、黏度指数高和蒸发损失小等优点,因此,许多高档的润滑油品中PAO已普遍被优选作为润滑油的基础油。PAO一般以α-烯烃(主要是C8~C12)在催化剂作用下聚合(主要是三聚体、四聚体和五聚体)而得到的一类比较规则的长链烷烃,在各类合成油中性能较优,且比其他合成润滑油价格低廉、生产工艺简单。聚α-烯烃的化学结构决定了其质量和性能。
用以润滑、冷却和密封机械的摩擦部分的物质根据来源有矿物性润滑剂(如机械油)、植物性润滑剂(如蓖麻油)和动物性润滑剂(如牛脂),此外还有合成润滑剂,如硅油、脂肪酸酰胺等。润滑油种类很多,应用广泛。润滑剂也常用于塑料等加工中改进流动性和脱模性,防止在机内或模具内黏着而产生鱼眼等缺陷。
塑料润滑剂,用于提高体系流动性,降低加工电流;用于玻纤等增强体系,能很好地提高玻纤/矿物的分散性,改善树脂与填料的结合力,防止玻纤外露,使制品具有更佳的表面光亮度、柔滑性与光洁度。
矿物润滑油为现代广泛应用的液体润滑剂。石油经过精制工艺制得的单一馏分的优质基础油可直接使用,如仪表油、冷冻机油和变压器油等。把不同黏度的基础油互相调和,或在基础油中加入所需的添加剂,可得到不同使用性能的润滑油。前者如机械油、汽轮机油、轧钢机油和航空润滑油等,后者如齿轮油、汽油机油、柴油机油、压缩机油和抗磨液压油等。
用有机合成的方法制得并具有特定结构和性能的润滑油,如硅油、硅酸酯、磷酸酯、氟油、酯类油和合成油等。合成润滑油按使用性能可分为高低温润滑油、抗燃润滑油、极压润滑油、防护润滑油、抗辐射润滑油、抗氧化润滑油、高真空润滑油、电气用润滑油和金属加工油等。
由稠化剂和基础油复合的具有塑性的润滑剂,有时还可根据需要加入各种添加剂。基础油在润滑脂中约占90%,对润滑脂的性能影响很大。稠化剂是润滑脂的重要组成部分,在润滑油中加入稠化剂后,才能形成具有一定结构形式的润滑脂。
稠化剂可分为皂基和非皂基两类。皂基稠化剂指各种脂肪酸金属皂。脂肪原料一般采用各种动、植物油脂以及从其中分离出来的脂肪酸和各种合成脂肪酸。形成金属皂的原料一般是碱金属、碱土金属的氢氧化物(如氢氧化钙、氢氧化钠等)、纯石灰和硫酸铝等。
非皂基稠化剂主要有:烃基稠化剂,如石蜡和地蜡;无机稠化剂,如膨润土和硅胶等;有机稠化剂,如阴丹士林蓝染料、酞菁铜、芳基脲、聚脲、聚四氟乙烯、氟化乙烯丙烯共聚物和全氟聚苯等;填料,如石墨、二硫化钼和炭黑等。