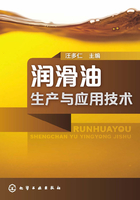
1.3 微晶蜡
微晶蜡(microcrystalline paraffin)CAS登记号67742-51-2;主要成分是支链烃,碳原子数为30~80,链烷烃含量0~30%。这种蜡的分子量高,熔点高,呈无定形或小结晶型。微晶蜡外观呈淡琥珀色或白色,在市场上常见的有75、80、85微晶蜡。与石蜡相比,微晶蜡硬度小、柔性好,受力情况下倾向于塑性流动,延伸度大,挠性好。蜡中含油质量分数在1%左右,蜡滴熔点大于700℃。
技术指标
微晶蜡一级品SH 0013—2008标准:颜色:<2.5号;含油量:<0.69%。
微晶蜡(地蜡)质量标准(80号国标):熔点:77~82℃;颜色:白色、微黄;形状:块状、颗粒。
晶蜡技术指标
85#专用微晶蜡(块、粒状Ⅰ型、Ⅱ型、Ⅲ型)主要技术指标:
生产技术
微晶蜡即人们所熟悉的石油地蜡。微晶蜡是通过一系列复杂的溶剂分离法从留在蒸馏釜里的渣油中分离出来的,它既有直链烷烃,也有支链烷烃或环烷烃。微晶蜡在硫化胶中的迁移速度相对较慢,形成防护膜的时间较长,但防护功效期长。
1998年美国有35%的基础油用加氢法生产。亚洲有30%的润滑油基础油用加氢法生产。加氢法生产的基础油中芳烃、硫、氮的含量很低,可使润滑油保持良好的氧化安定性和热稳定性,与添加剂等物品不容易发生反应。用加氢法生产润滑油是21世纪的发展方向。
我国石蜡基原油占总原油产量的70%以上,大部分石蜡基原油中含有一定的微晶蜡,我国大庆等原油微晶蜡资源丰富,是生产多品种包括硬质和软质微晶蜡的极为理想的原料。
本着充分发挥资源优势、发展特色产品的原则,采用低硫石蜡基原油,含蜡量高达23%,微晶蜡潜含量为30%,是发展石蜡和微晶蜡的理想原料。
生产实例一 用脂肪酸甲酯加氢制备
分别以Ni-Al2O3和NiAl2O4为载体制备用于脂肪酸甲酯加氢制备液体石蜡的催化剂,载体酸性影响催化剂生成液体石蜡的选择性,适宜工艺条件为:反应温度400℃,反应氢气压力为5.0MPa,空速为1.0h-1,氢、油摩尔比15.56:1。以Ni-Al2O3和NiAl2O4为催化剂,脂肪酸甲酯转化率达98.9%,正构烷烃选择性达100%。
用脂肪酸甲酯加氢制备液体石蜡为加氢脱氧反应,催化剂主要采用Ni-Mo/γ-Al2O3和Co-Mo/γ-Al2O3以及硫化处理的Ni-Mo/γ-Al2O3和Co-Mo/γ-Al2O3,虽然转化率较高,但在加氢脱氧过程中发生异构化和芳构化等副反应,同时采用硫化处理的催化剂将微量硫带入产品。开发具有高活性和高选择性加氢脱氧催化剂对高品质液体石蜡的生产十分重要。
(1)催化剂制备
①Ni/γ-Al2O3:将一定量Ni(NO3)2·6H2O溶于去离子水配成质量分数为20%的溶液,逐滴加到制备完成的纯Ni-Al2O3载体上,浸渍6h,100℃干燥24h,540℃焙烧,450℃用H2活化4h。
②Ni/Ni-Al2O3:将一定量的Ni(NO3)2·6H2O溶于去离子水配成质量分数为20%的溶液,逐滴加到制备完成的Ni质量分数为10%的NiAl2O4载体上,浸渍6h,在100℃干燥24h,于540℃焙烧,于450℃用H2活化4h。
(2)加氢实验 反应装置为一段加热夹套管式反应器,φ8cmX 40cm,催化剂置于反应器中部15~20cm恒温段,催化剂层高5cm,填充物采用粒径为2mm的小瓷球。采用压力控制阀,氢气质量流量控制器。
产品定量采用气相色谱法,使用Agilent 7890A GC气相色谱仪,色谱条件:色谱柱为Agilent 19091S-331石英毛细管柱,φ0.25mmX15m,FID检测器,柱温度250℃,以10℃/min进行程序升温,检测器温度350℃,汽化室温度400℃,N2流速25mL/min,H2流速30mL/min,空气流速400mL/min,进样的流量为0.5μL,修正面积归一法定量。
产品定性采用气相色谱质谱联用法,使用岛津GCMS-QP2010气质联用仪,色谱条件:初温70℃,保持3min,以3℃/min进行程序升温至220℃,保持15min,分流比50:1,以He作载气,柱流量1.5mL/min;质谱条件:离子源温度200℃。
分别以γ-Al2O3和Ni/γ-Al2O3为载体,负载20%Ni制备加氢脱氧催化剂,在反应氢气压力为5.0MPa、空速2.0h-1和氢油摩尔比为12.45:1的条件下,以γ-Al2O3为载体的催化剂,随着反应温度提高,脂肪酸甲酯转化率增加,以Ni/γ-Al2O3为催化剂;随着反应温度升高,脂肪酸甲酯发生脱氧反应速率加快,但生成的烷烃在载体γ-Al2O3表面酸性的作用下,又发生异构化等副反应,并随着反应温度的升高逐步加快。
将一份β-沸石催化剂装入一带搅拌器的压力容器内。β-沸石在150~400℃、5mmHg的压力下干燥和活化。将一份脂肪酸或酯,例如硬脂酸添加到反应釜或容器内密封后,在约300psi的惰性氮气或氮气-氢气存在下将混合物加热到约300℃,在此反应温度下继续反应1~2h,从蒸馏组分中回收石蜡,从硬脂酸中回收正十七烷。
改换成用硬脂酸乙酯为原料,石蜡可以在以下过程中产生。将一份β-沸石催化剂装入一带搅拌器的压力容器内。在β-沸石在150~400℃、5mmHg的压力下干燥和活化。将硬脂酸或酯,例如将硬脂酸乙酯添加到反应釜或容器内密封后,在约300psi的惰性氮气或氮气-氢气存在下将混合物加热到约400℃,在催化剂床层接触时间为2~5min,从蒸馏组分中回收石蜡,从硬脂酸乙酯中回收正十七烷。
生产实例二 润滑油
本工艺的润滑油没有特别的限制。生产过程包括溶剂萃取、加氢裂解、溶剂脱蜡、催化脱蜡、加氢精制,这些润滑剂基础油可单独使用,也可以组合使用。
纯化方法有加氢精制法、酸性白土或活性白土;脱蜡方法有溶剂脱蜡和催化脱蜡。通常情况下,在本工艺中,可以两种或更多种组合使用也可以单独进行。
用于加氢异构化,加氢裂化催化剂没有特别的限定,可以使用复合氧化物(例如,二氧化硅-氧化铝,或氧化硅-氧化锆)或优选使用在载体上含有沸石(ZSM-5,β-沸石或SAPO-11)的加氢异构化催化剂。
加氢裂化没有特别的限制,氢分压为0.1~20MPa,平均反应温度150~450℃,LHSV(液时空速)0.1~3.0h-1,氢/油比是50~20000。
本工艺制备的润滑油是以低黏度为目的,疏松石蜡优选相对低的黏度,油含量不超过0.5%,硫含量小于0.001%。
溶剂脱蜡使用甲苯-MEK(甲基异丙基酮)的混合溶剂在-25℃的温度条件下进行,过滤,获取润滑油基础油不同的黏度等级。也可以使用丙酮和MIBK(甲基异丁基酮)。过滤温度为-10℃,优选-40~-10℃。
采用助滤剂SM-40在微晶蜡生产过程中可以将蜡段、脱油段过滤速率同时提高10%以上。
采用轻脱沥青糠醛精制油,先将助滤剂与甲苯按1:7.5的比例配制成母液,温度控制在80~85℃,再用计量泵将母液加入到原料泵入口。助滤剂SM-40的应用加剂量控制为0.36%~0.60%,石蜡氧化首先生成过氧化物,然后再进一步生成醇、酮、酸等复杂的含氧化合物。
石蜡发汗和酮苯脱蜡联合生产炼蜡、粗蜡及各种特种蜡,主要是依据熔点差异,缓慢加热使软蜡融化,使之和油分一起从蜡膏结晶中渗出。发汗工段若操作不当也会造成含油量高或软蜡成分混入产品。
石蜡的精制主要是利用活性白土与氧化镁等的比表面大、选择性吸附能力强来进行吸附脱色,白土吸附的精制能力有限。还需要加入光稳定剂和抗氧化剂来改善产品质量。如果润滑油系统的生产顺序为先溶剂精制、后酮苯脱蜡,使石蜡先经过溶剂精制,则可以更好地发挥白土补充精制的作用。
在生产中,主要调整以下工艺条件。
(1)结晶系统 为改善结晶效果,调整预稀释溶剂与原料的比例为1.0,冷套管冷点温度控制在28~30℃。
(2)过滤系统 由于70#微晶蜡不易过滤,装置加工量应控制在30t/h,以减少蜡饼厚度来提高过滤速度,并适当提高蜡段、脱油一段、脱油二段的稀释、冷洗溶剂与原料的质量比例,对蜡膏中的油进行充分溶解,增大冷洗量来强化过滤机的洗涤效果。减五线原料到过滤机后,也可在脱油一段增加过滤机来保证过滤效果。
在生产过程中,过滤机温洗时间间隔分别为:生产蜡1.5h,脱油段40min。过滤机温洗成良性循环,以提高石蜡收率。
(3)冷冻系统 冷冻系统在加工减五线初期,由于冷点温度的提高,冷冻负荷增大,特别是在换料调整阶段,原料温度高,冷冻负荷大幅度增加。应根据原料的最终冷温度情况,及时增开冷冻机。
(4)助滤剂加入量 此次加工过程最初3d加入助滤剂的质量分数为0.05%,之后减少到0.02%。助滤剂加入量对过滤效果影响不大。
酮与苯脱蜡装置生产的产品质量完全符合70#微晶蜡的生产要求。
生产实例三 氢化
矿物油的相对密度小于1。某些合成润滑油具有较大的相对密度,能满足一些特殊用途的要求,用于生物降解的基础油有植物油、合成酯和聚乙二醇3种。
润滑油加氢处理是将原料中的非理想组分转化为理想组分,主要发生的反应有:加氢脱硫、脱氮、芳烃饱和、环烷烃的开环、烷烃和烷基侧链的加氢异构化等。
加氢处理工业化工艺是采用一段串联一次通过的工艺流程。
该技术是加工中间基原油生产中高档润滑油的重要手段。尤其是中压加氢处理工艺,可以利用炼厂现有条件(溶剂精制装置),配套建设中压加氢处理装置可减少投资;此外,氢耗低,有利于降低操作成本。
矿物油已被用来作为填充剂、软化剂、美国石油学会(API)基础油溶剂精制矿物油。这些大量的“常规”的基础油提炼使用芳烃溶剂萃取法,溶剂脱蜡,加氢精制,以减少硫含量,生产矿物油的硫含量大于0.03%(质量分数),饱和度60%~80%,黏度指数约90。
加氢精制的目的是降低含硫量使之≤0.03%,饱和程度为95%~98%。
加氢精制是在一定的温度、氢分压和催化剂存在条件下使石蜡中烯烃饱和,还原含氧、氮、硫的化合物以脱氧、脱氮、脱硫,并将带侧链的芳烃逐步转化为环烷烃直至直链烷烃,同时将不带侧链的稠环芳烃逐环分解,效果明显好于白土精制。
在氢化过程中,氢分压增加和空速降低有助于提高石蜡的产品质量。同时加氢操作的要求过高,特别是温度过高会发生碳链裂解和烃类异构化,使蜡含油量回升。
生产中选择控制加氢反应的条件要适宜。
含油蜡的预加氢选用Mo-Ni催化剂,在不同的精制条件下,根据不同的催化剂选择适宜的加氢工艺条件,对保证含油蜡的精制效果是十分重要的。Mo-Ni催化剂的裂解活性相对小于Mo-Co催化剂,更适用于含油蜡的加氯精制。
选用酮与苯混合溶剂脱油,溶剂组成为甲乙酮:甲苯为65:35。
原料蜡的罐储温度应控制在比低熔点高15~30℃,存放时间最好控制在15~30天以内,不要超过3个月,罐储温度过高、存放时间过长时蜡料将氧化变质,颜色变深(大于8号),使加氢的苛刻度增加,产品质量下降。
原料石蜡一定要进行充分的沉降、脱水。切忌在原料罐中边抽边进。若将水带入反应器将使催化剂活性下降,产品质量变差。
由于反应器内径较小,装填步骤采用自然装填法。
首先由反应器底部向上先后装填φ18mm、φ10mm及φ4mm瓷球各65kg,然后装填绿色复合催化剂2625kg,压上一层φ10mm瓷球130kg;安装隔板;再装入φ10mm及φ4mm瓷球32kg和65kg,接着再装填绿色复合催化剂2520kg,装好去污篮,再压一层φ10mm瓷球120kg。
氢化操作如下:硫化剂为二硫化碳,硫化油为轻质馏分油。预硫化结束后,退出硫化油并降温,当床层温度降至规定值时,换进原料蜡,调整工艺参数进入正常运转采用新的复合催化剂,在反应压力6.5~7.0MPa、温度257.3~267.0℃、空速1.33~1.48h-1及氢蜡体积比110~132的条件下,对蜡料进行加氢精制,还可制得符合国家标准GB 7189—94的食品级石蜡。
微晶蜡一段串联加氢:实际氢蜡体积比为800~1000,从实际生产的高压分离器的气体分析来看,氢纯度高达93%~95%,可循环使用。
脱油原料的预加氢应在保证原料中石蜡组分的特性指标不被破坏的前提下实现精制的目的。氢蜡体积比800、温度320℃、空速0.5h-1的条件下进行脱油原料加氢精制时在采用Mo-Ni催化剂加氢时活性明显高。
在加氢法生产基础油的技术主要由加氢裂化或加氢处理、异构脱蜡和加氢精制三部分组成。它的操作压力较高,为13~14MPa。加氢裂化或加氢处理的目的是把原料中的低黏度指数组分转化或裂化成高黏度组分;异构脱蜡主要通过催化异构来降低倾点,如石蜡烃,黏度指数174,凝点37℃,变成异构烃后,烃黏度指数略低,但凝点降到了-25℃,所以比溶剂脱蜡把蜡分离出去或催化脱蜡把蜡分解有更大的优越性,总收率可以得到提高。
加氢精制主要是解决全氢路线基础油因部分加氢芳烃引起的光安定性差问题。新的贵金属精制催化剂,可以在中压下进行加氢精制。
催化脱蜡工艺适用的原料范围相对较宽,试验原料为进口中东减压馏分的糠醛精制油,该原料催化脱蜡工艺在氢分压8.0MPa,反应温度380℃,体积空速0.5h-1的条件下,润滑油收率为66.4%,黏度指数为86,倾点由原料的47℃降低到-16℃。
异构脱蜡工艺对原料中的硫、氮含量有严格的要求,原料为进口中东减压馏分油的加氢裂化尾油,在氢分压15.0MPa,反应温度380℃,空速1.0h-1的条件下,液体收率为95.1%,350℃润滑油收率67.8%,黏度指数高达127,倾点由原料的39℃降到-12℃,是较好的VHVI基础油组分。
异构脱蜡与催化脱蜡不同之处在于异构脱蜡将大部分的蜡异构化成润滑油,不仅降凝效果好,而且副产品是质量好、价值高的低凝点中间馏分油。目的产品润滑油的黏度指数比溶剂脱蜡的黏度指数高,收率与溶剂脱蜡油相当或稍高。由于该工艺使用的是贵金属催化剂,为防止催化剂中毒,通常原料需要加氢预处理或使用加氢裂化尾油。
催化脱蜡和异构脱蜡工艺技术可以用糠醛精制油相加氢裂化尾油为原料,生产低倾点的润滑油基础油。
加氢裂化的异构烷烃生物降解性能比PIB和PAO及芳香基础油好,有60%~70%可降解,而PAO和矿物油只有40%~50%可降解。工艺技术具有润滑油收率高,目的产品质量好,副产品价值高的特点。
生产实例四 深度加氢精制
深度加氢精制工艺生产白油是以环烷基油为原料,采用一段串联一次通过的工艺流程。催化脱蜡工艺是利用ZSM-5型分子筛择形裂化特性,将原料中的蜡转化成C3~C4气体和石脑油,再经过蒸馏从润滑油中脱除,而达到降低倾点的目的。催化脱蜡润滑油的黏度指数比溶剂脱蜡油一般要下降3~10个单位,润滑油收率与溶剂脱蜡相当或略低。
该原料催化脱蜡工艺在氢分压8.0MPa、反应温度380℃、体积空速0.5h-1的条件下,润滑油收率为66.4%,黏度指数为86,倾点降低到-16℃。
原料异构脱蜡工艺在氢分压15.0MPa、反应温度380℃、空速1.0h-1的条件下,液体收率为95%,润滑油收率67.8%,黏度指数高达127,是基础油组分。
生产实例五 高压加氢精制
为解决微晶蜡生产过程中的过滤速度问题,采用助滤剂SM-40在微晶蜡生产过程中可以将脱蜡段、脱油段过滤速度同时提高10%以上。
采用轻脱沥青糠醛精制油。先将助滤剂与甲苯按1:7.5(质量比)的比例配制成母液,温度控制在80~85℃,再用计量泵将母液加入到原料泵入口,以考察添加剂效果。根据对助滤剂SM-40的试验研究结果,本次添加剂量控制在0.36%~0.60%。
石蜡氧化是先生成过氧化物,然后再进一步生成醇、酮、酸等复杂的含氧化合物。
为解决微晶蜡加氢的质量问题,在工业装置上实现“微晶蜡一段串联加氢”工艺。
在生产微晶蜡期间,白土加入量为60kg/h。
为避免操作波动对产品质量带来影响,提前1天将高压加氢精制装置反应温度由275℃提高到280℃;反应压力也提前1天由135MPa提高到160MPa。为减少中间产品,在进料2h前调节高压加氢精制装置热高压分离器液位为25%,热低压分离器液位为20%,脱气塔的液位为30%,汽提塔液位为20%,真空干燥塔的液位为20%,氢气冷却温度为72~75℃。
通过对白土预精制-高压加氢精制装置操作参数调整,产品各项分析指标均达到70#食品级微晶蜡指标要求。
本工艺一段串联加氢装置主要的工艺技术特点是:①炉前混氢,工业氢纯度达95%以上,采用一次通过流程,从高压分离器分离出的氢气可送石蜡加氢或润滑油加氢装置利用。②原料蜡经过滤-脱气预处理,可避免溶剂、水分和机械杂质进入反应器。③为了充分发挥主催化剂的功能,采用了保护剂与复合催化剂复配技术。④微晶蜡一段串联加氢精制的产品采用0.3MPa的过热蒸汽汽提、真空干燥和过滤后处理的措施,以确保产品蜡质量合格。
生产实例六 纳滤
纳滤是新型的膜分离技术,截留的分子为纳米级,2价以上的离子和相对分子质量大于200的有机物被截留。聚酰亚胺纳滤膜具有优良的耐有机溶剂、耐热性和机械强度,是理想的石油化工用的纳滤膜,目前已在润滑油酮苯脱蜡工艺中回收酮苯溶剂中获得了应用,它能够在低温下回收酮苯溶剂,实现节能降耗、提高产能的目的,有效解决了酮苯脱蜡装置的生产瓶颈。据测算,在总能耗不变的情况下,采用膜分离技术可使酮苯脱蜡装置基础油产量平均提高25%(体积分数)以上,脱蜡油收率提高3%~5%。膜分离技术使单位能耗降低了近20%,安装费用只相当于采用一般技术的1/3,投资回收期小于1年。聚酰亚胺纳滤膜在-18℃、4MPa下分离酮苯脱蜡滤液时,通量达到14L/(m2·h),对润滑油截留率大于99%,滤液油含量小于0.2%。
应用技术
应用实例一 蜡基润滑剂
本工艺在于提供蜡基润滑剂涂层的实例中,液体润滑剂组分是不超过约60%(质量分数)的蜡。首选蜡应具有高硬度和高结晶。合适的蜡包括(但不仅限于)植物蜡、合成蜡、矿物蜡及其混合物。例如(但不仅限于):氧化石蜡、微晶蜡、硬脂酸蜡、聚乙烯蜡、氧化聚乙烯蜡、聚丙烯蜡、氧化聚丙烯蜡、石蜡油和矿物蜡等。
本工艺涉及的塑化聚烯烃组成,包括一个或多个聚烯烃和一个或多个反应性增塑剂,反应性增塑剂包括高纯度烃类流体组分,最好是分子内含16~100个碳原子。烃类流体组分的异构烷烃:N-石蜡的比例最好是1:1~4:1。在异构烷烃的混合物中含有大于70%的甲基异构烷烃混合物。这些烃类流体,运动黏度最好在10~2000cSt(1cSt=10-6 m2/s,余同),可选择低倾点最好范围从-20℃至约-70℃。聚烯烃组分中的反应性增塑剂包括线型或支链石蜡烃,数均分子量为500~21000。
应用实例二 润滑剂
润滑剂可降低塑料熔体的摩擦,这种摩擦又分外摩擦和内摩擦两类,由此相应的有外润滑剂和内润滑剂。
①外润滑剂的作用主要是改善聚合物熔料与设备的热金属表面的摩擦状况,使塑件容易脱模,它与聚合物的相容性较差,容易从熔料中往外迁移,在成型过程中能在熔料与模具间形成一层很薄的隔离膜,使塑料不黏住模具表面。
②内润滑剂与聚合物有良好的相容性,它在聚合物内部起着降低聚合物分子间内聚力的作用,从而改善塑料熔料的内摩擦生热和熔体的流动性。内润滑剂和聚合物长链分子间的结合是不强的,它们可能产生类似于滚动轴承的作用,因此自身能在熔体流动方向上排列,从而互相滑动,使得内摩擦力降低。
润滑剂的品种相当多,常用的外润滑剂有石蜡、硬脂酸及其盐类;内润滑剂有低分子量的PE、PTFE、PP等。这些低分子量的聚合物不但是优良内润滑剂,而且也是很好的外润滑剂。有时候,一种润滑剂的效果往往不理想,需要几种润滑剂配合使用,由此就产生了复合润滑剂,可以起到多方面的作用,效果更好。润滑剂的用量一般为0.5%~1%。
真空精炼中的溶剂精炼基础油的一步蒸馏分离最初是用糠醛溶剂萃取,然后加氢裂化,溶剂脱蜡后,在甲基乙基酮、甲苯混合溶剂中进行。蜡在溶剂脱蜡脱油去除是获得蜡部分(以下简称“WAX1”作为润滑油的基础油为原料使用)。
起始材料蜡WAX1技术指标
WAX1在加氢裂化催化剂存在下,在氢气压力为5MPa,平均反应温度350℃,空速1h-1下进行。加氢裂化催化剂用硫化催化剂是镍和15%的无定形硅,以氧化铝为载体[硅石:氧化铝钼(质量分数3%)=20:80(质量比)]。
将由加氢裂化得到的分解产物进行真空蒸馏,得到的润滑油馏出物相对于原料油(体积)为26%。甲乙酮-甲苯混合溶剂的溶剂/油比为4,过滤温度-25℃,以获得润滑油基础油(D1~D3进行溶剂脱蜡的润滑油馏出物),具有不同的黏度等级。
润滑油的性质和性能评价试验的结果(质量分数,%)如下。
续表

应用实例三 润滑油基础油
USY沸石800g和200g的氧化铝黏合剂的混合物捏合成型为圆筒状,直径为1/16in(1in=0.0254m)(约1.6mm),高度为6mm。成形后在450℃下烧制3h得到载体。含铂的量为0.8%(质量分数)。载体在水溶液中浸渍后在120℃下干燥3h,在400℃下烧制1h得本催化剂。
将200mm所得到的催化剂填充到固定床反应器内,用于链烷烃的含烃进料的原料油的加氢裂化/加氢异构化反应器中。在此步骤中所用的油与链烷烃含量为95%和碳原子数分布为20~80(以下称为“WAX2”)的FT蜡。加氢裂化的条件是在氢压力为3MPa,反应温度为350℃,LHSV为2.0h-1,以及分解/异构化生成油中,得到含有30%(相对于起始原料)的沸点380℃(分解产物)及以下的裂解深度产物。
起始原料蜡WAX2的技术指标
通过以下方式获得上述的加氢裂化/加氢异构化工序的分解/异构化生成油,然后进行真空蒸馏,得到润滑油馏分。之后进行溶剂脱蜡,控制溶剂/油比为4,过滤温度-25℃,用甲基乙基酮-甲苯混合溶剂,获得的润滑油基础油(D4~D6),具有不同的黏度等级。
上述润滑油各黏度等级有更长的使用寿命与优异的热稳定性和氧化稳定性和抗氧化性。
应用实例四 润滑油基础油
基础油D2:石蜡加氢处理的基础油[饱和含量94.8%(质量分数),硫含量<0.001%,运动黏度(在100℃)4.1mm2/s,黏度指数121,折射率(20℃)1.4640]。
基础油D3:石蜡溶剂精炼基础油[饱和含量为77%以上的质量分数,硫含量0.12%,运动黏度(在100℃)4.0mm2/s,黏度指数102]。
①不含硫的无灰抗氧化剂组成部分
A1:烷基二苯胺。
A2:辛基-3-(3,5-二叔丁基-4-羟基苯基)丙酸酯。
②无灰抗氧化剂含有硫作为构成元素,有机钼化合物
B1:无灰二硫代氨基甲酸(硫含量:29.4%质量分数)。
B2:钼-铵衍生物(钼金属量:10.0%质量分数)。
③抗磨剂
C1:二烷基二硫代磷酸锌[磷含量:7.4%(质量分数),烷基:正辛基]。
C2:二烷基二硫代磷酸锌[磷含量:7.2%(质量分数),烷基:仲丁基混合物]。
④无灰分散剂
D1:聚丁烯琥珀酸亚胺(双型,重均分子量8500,氮含量:0.65%质量分数)。
⑤无灰摩擦改进剂
E1:甘油脂肪酸酯(MO50,花王公司的产品)。
⑥其他添加剂
F1:含金属清洁剂,黏度指数改进剂,降凝剂,消泡剂。
所述内燃机的润滑油组分的实例表现出优异的氧化稳定性和优异的低摩擦性,摩擦系数小于0.1。
用于内燃发动机的润滑油,从有效利用资源的观点出发,润滑油用户的成本较低。
本工艺所述的动力传动系装置的润滑油组分中含有的聚(甲基)丙烯酸酯系黏度指数改进剂,为总质量的0.1%~10%。
本工艺优选的金属清净剂,可以提及的有碱土金属磺酸盐,碱土金属酚盐和碱土金属水杨酸盐。含量没有特别的限制,优选为0.01%~0.2%。当用作本工艺的动力传动系的移动设备的润滑油组分,尤其是手动变速箱用润滑油时,金属清洁剂的含量为0.2%~0.35%(质量分数)。
本工艺优选的抗氧化剂,在于能进一步提高热稳定性和氧化稳定性。作为抗氧化剂,最优选的是酚类抗氧化剂和胺抗氧化剂。
抗氧化剂种类:2,6-二叔丁基-4-甲基苯酚、烷基酚、双酚和酯,包括(3,5-二叔丁基-4-羟基苯基)脂肪酸(丙酸等)或(3-甲基-5-叔丁基-4-羟基苯基)脂肪酸(丙酸等)与一元醇或多元醇,如甲醇、辛醇、十八烷醇、1,6-己二醇、新戊二醇、硫代二甘醇、三甘醇、季戊四醇等的酯。优选用量为总质量的0.01%~5.0%。
通常用作摩擦改进剂的是胺化合物、酰亚胺化合物、脂肪酸酯、脂肪酸酰胺、脂肪酸金属盐和具有至少一个C6~C30等的烷基或烯基,特别是C6~C30的直链烷基或直链的链烯基。
胺化合物选用琥珀酰亚胺。脂肪酸酯优选直链脂肪酸与脂肪族单胺或脂肪族多胺的酰胺。脂肪酸金属盐有碱土金属盐(镁盐,钙盐等)或C7~C31的直链或支链的,优选直链脂肪酸的锌盐。
润滑油组分优选地包含一个或多个选自胺摩擦改进剂、酯摩擦改进剂、摩擦改进剂的酰胺和脂肪酸的酸性摩擦改进剂中,从改善的观点出发,最优选的是胺摩擦改进剂、脂肪酸的酸性摩擦改进剂和酰胺摩擦改进剂中的一种或多种。摩擦改进剂的含量基于组合物的总质量计优选为0.03%~3.0%。此外,一个根据本发明的动力传动系的移动设备的润滑油组分作为手动变速器用润滑油时,摩擦改进剂优选用量为总质量的0.5%~1.5%。
此外,还可包含其他添加剂,如腐蚀抑制剂、防锈剂、破乳剂、金属钝化剂、倾点下降剂、橡胶溶胀剂、消泡剂、着色剂等。
应用实例五 润滑油基础油
两冲程发动机会产生大量的污染,其中包括两冲程汽油发动机润滑油的燃烧、浓烟和泄漏的两冲程汽油发动机润滑油通过排气口。两冲程汽油发动机润滑油的大多数是低沸点烃类溶剂和矿物基础油配制。已经使用的酯基油可以减少潜在的危险和减少排放黑烟排放,但这些润滑油不具有非常良好的氧化安定性。已经使用聚α-烯烃制造基础油,具有改进的低温性能,但聚烯烃及酯基油非常昂贵和供应有限。改善两冲程汽油发动机润滑油组分,包括较昂贵的基础油,并满足标准机构设置的要求,是理想的。两冲程汽油发动机润滑油组成具有良好的低温性能、良好的汽油相容性和高氧化稳定性,具有较高的闪点和减少易燃。
两冲程汽油发动机润滑油基础油组分(质量分数)如下:90%~97%的石蜡;3%~10%的环烷基油;1%的清洁剂/分散剂。
应用实例六 食品用润滑剂
本工艺产品用于润滑食品包装,润滑食品容器和润滑输送装置,可移动容器或容器加上食物成分在生产过程中的润滑剂。
美国专利US4929375和US5073280、US5009801、US5863874、US5723418、US5863871、US5559087、US5352376、US5244589、US5182035、US5174914所述的水基润滑剂,通常用于传输装置的过程中,例如,饮料的灌装容器。水基润滑剂一般往往是不利的,因为使用大量的水,需要湿的工作环境,增加了微生物的生长。
本工艺优选的润滑剂组分可以含有各种天然的润滑剂,石油润滑油,合成润滑油和润滑脂。天然的润滑剂包括植物油、脂肪油、动物油脂等。石油润滑油的例子包括矿物油,各种黏度石油馏出物和石油产品。合成油的例子包括合成烃类、有机酯、高分子量的醇、羧酸、磷酸酯、聚醚(PFPE)、硅酸盐、硅树脂(如有机硅表面活性剂)、氯三氟乙烯、聚苯醚、聚乙二醇、乙二醇共聚物、乙烯和氧化丙烯、多羟基化合物等。有用的固体润滑剂包括二硫化钼、氮化硼、石墨、二氧化硅粒子、硅橡胶和聚四氟乙烯(PTFE,聚四氟乙烯)、氟乙烯-丙烯共聚物(FEP)、全氟烷氧基树脂(PFA)、乙烯-氯三氟乙烯的交替共聚物(ECTFE)、聚(偏二氟乙烯)(PVDF)类似物。
配方如下:甘油(96%活性)77.24%;去离子水20.71%;微晶蜡2.05%。
应用实例七 汽车发动机清洗剂
配方:芳烃25~100份、石蜡烃25~100份、烷基酚聚氧乙烯醚10~25份、烷基磺酸盐1~10份、乳化剂1~10份、硅酸钾1~10份、氢氧化钠10~25份、乙二醇和异丙醇1~10份、磷酸1~10份、乙二胺四乙酸0~10份、水0~1000份。
本品制成浆状物,用于洗刷汽车发动机上的油污。经刷洗5~15min后,再用清水冲净,去污效果良好。
应用实例八 汽车发动机清洗剂
配方:烷基醚酯6%~10%、烷基酚醚酯7%~10%、四氯乙烯20%~30%、三氯乙烯12%~18%、脱臭煤油10%~20%、白溶剂油15%~25%、甲基溶纤剂4%~6%、丁基溶纤剂3%~6%。
本品适用于发动机油污的清洗,产品性能温和,除油污效果优良,能在金属表面形成酯膜,具有防锈、防腐蚀,延长设备使用寿命,除油迅速,不用擦洗,方便省力等特点。
应用实例九 汽车发动机去油污剂
配方:环烷烃和石蜡烃25~100份、芳烃25~100份、烷基酚聚氧乙烯醚10~25份、乳化剂1~0份、氢氧化钾10~25份、硅酸钾1~10份、磷酸1~10份、乙二胺四乙酸0~1份、乙二醇异丙醚1~10份、水10~1000份。将上述各组分混合,搅拌成均匀的糊状物即得成品。用本品刷洗发动机5~15min后,以清水冲净,即可完全除去油污。
应用实例十 燃料
由10%的微晶蜡和90%的六亚甲基四胺组成。将两者混合、熔化,真空下压缩成型。产品易于点燃,燃烧时不熔化,适合作野外烹饪燃料。
应用实例十一 固体燃料
将1kg石蜡置于夹层锅内加热,待全部熔化后在搅拌下加入炭粉、锯末。保持温度为60℃,搅拌5min使其混合均匀。待物料冷却到25℃以下时,在搅拌下用喷雾器将乙醇喷入原料中,迅速搅拌均匀后,将混合物料装入模具,放在冲压机上压制成型。将已成型的原料块放入预先熔好的微晶蜡中,沾上一层薄薄的蜡层后取出,经冷却和包装即可出售。
应用实例十二 复合硫化橡胶
使用含有复合组合物的橡胶硫化助剂是在橡胶混炼领域通常已知的方法,如将各种硫可硫化或过氧化物硫化的组成橡胶与各种常用的添加剂材料(如硫给体)混合,以及各种活化剂、延迟剂和加工助剂,如油、树脂(包括增黏树脂)和其他常规的增塑剂、填料、颜料、脂肪酸、氧化锌、蜡、抗氧化剂和抗臭氧剂、防焦剂和塑解剂。
氧化锌的典型用量(质量分数)为1%~5%。常常使用微晶蜡。缓凝剂的典型用量为0.05%~2%。塑解剂的典型用量为0.1%~1%。典型的胶溶剂可以是五氯硫酚和二苯甲酰氨基二苯基二硫化物。
含有本工艺所述的复合橡胶的硫化温度为180℃。硫化过程中,可以使用压机或模具加热,用过热蒸汽或热空气或在盐浴中加热。
橡胶硫化后含有复合组合物,温度范围在100~200℃,该橡胶可以有各种用途。例如,可以制成皮带、软管、垫圈和空气弹簧。
应用实例十三 基础油生物降解技术
在我国,大部分废旧润滑油得不到及时有效的回收处理,成为不可再生润滑油。以废旧润滑油回收利用技术先进的美国为例,其有效回收并利用的废润滑油仅占废旧润滑油总量的18%,大部分废旧润滑油将流入环境。此外,部分成品润滑油在生产、加工、储运及使用过程中因工艺本身或操作不当等因素,将不可避免地直接进入环境,成为不可再生能源。由于废旧润滑油中含有环烃、芳香烃等有毒害石油烃组分及锌、铜、镉等重金属,难于降解,在环境中长期滞留并累积,使环境污染日益加剧。
不可再生润滑油生物降解技术具有不产生二次污染、处理成本低等优势。该技术基于微生物种类和功能的多样性,利用特定培养和降解条件下,微生物能以润滑油为唯一碳源和能源实现生物降解的本质属性,达到清除或部分消除润滑油的目的。当前,已分离出的润滑油降解菌涵盖了细菌和酵母两大类,代表性菌种包括假单胞菌属(Pseudomonαs)、诺卡氏菌属(Nocαrdiα)、不动杆菌属(Acinetobαcter)、红球菌属(Rhodococcus)、土壤杆菌属(Agrobαcterium)、德巴利酵母菌属(Debαryomyces)和罗尔斯通菌属(Rαlstoniα)等。其中诺卡氏菌属、不动杆菌属、假单胞菌属和罗尔斯通菌属较为常见。
基础油的组分是影响润滑油生物降解特性的决定因素。
矿物油占据了85%以上的润滑油基础油市场。矿物润滑油一般由C18~C50的长链烃化合物构成,包括高沸点、高分子量烃类和非烃类混合物,主要分为链烷烃、环烷烃和芳香烃。其中以链烷烃最易降解,其他两类性质相对稳定。自然界中的大部分微生物都具备代谢这些化合物的烃解能力,目前已发现细菌39个属、真菌19个属、酵母菌17个属的微生物能够实现降解。
微生物通过两种不同机制作用于底物:一是特异性附着机制,微生物通过菌毛或细胞膜表面的脂蛋白形成疏水表面,进而附着于水中的油滴上;二是烃类乳化机制,利用细胞在特定培养条件下能够释放出乳化剂乳化矿物润滑油成颗粒状,从而增大相互接触和利用表面积。利用戈登氏菌属降解矿物基础油的过程中,发现菌株分泌生物表面活性剂使培养液中油层分散成小油滴,并形成橘红色絮状沉淀。在投入脂肪酰基氨基酸表面活性剂后,菌株的降解能力得到显著改善。此外,针对矿物润滑油中的不同组分,微生物遵循不同的降解途径:①微生物中具有混合功能的氧化酶催化氧化烷烃生成醛和脂肪酸,脂肪酸通过氧化被微生物吸收,并放出CO2;②环烷烃在微生物中两种氧化酶的协同氧化作用下开环,再通过氧化降解,最终被微生物吸收;③芳香烃在氧化酶的作用下开环氧化,并最终被微生物吸收。假单胞菌具有很强的链烷烃降解能力,废油去除率达到67%。
假单胞菌属广泛存在于各类型污染环境中,成为环境自净化菌群中的优势菌属,能够降解原油、润滑油、柴油以及多环芳烃等化合物,这其中尤以恶臭假单胞菌和铜绿假单胞菌得到了更广泛的研究。此外,从油污染土壤中分离出一株细菌,经鉴定为诺卡氏菌,该菌通过分泌加氧酶实现开环裂解完成芳香烃代谢的关键步骤,经薄层色谱-氢火焰技术(TLC-FID)检测证实诺卡氏菌能够降解矿物润滑油中的链烷烃、芳香烃和树脂,对芳烃的降解率为38.13%。红球菌属以环己烷作唯一碳源和能源,最适作用温度为25~35℃,最佳pH值为6~8,在此条件下,环己烷达到最大降解速率。
从废旧润滑油中分离出多株野生型石油烃的降解菌,这些菌种活力明显高于来自油污染环境中的微生物菌种,且这部分菌种表现出极高的耐油特性,能够在水分活度极低的复杂的石油烃组分中进行代谢。
菌种改良矿物基础油生物降解的关键在于微生物菌种的活力。以提高菌种活力为目的的菌株降解能力是提高废旧润滑油生物去除效率、消除环境污染的重要研发方向。
利用氦氖激光器在632.8nm波长下以不同剂量辐照芽孢杆菌(Bαcillus),诱变处理后培养,对残留基质进行色谱分析,经辐射后的菌株对链烃分子的降解率提高了近40%,达到98.12%,多环芳烃则基本上被完全降解。
在现有菌种资源基础上,开展多菌种协同降解润滑油已成为提高废旧润滑油生物去除效率的有效方法。可以对难降解污染组分,利用特异性的菌种资源进行强化降解,此法类似于油污染环境生物修复技术中的使用外源微生物强化难降解有机物的去除,使润滑油的生物降解更为彻底。从润滑机油污染土壤中分离筛选出假单胞菌、节细菌属(Arthrobαcter)和分枝杆菌属(Mycobαcterium),在相同条件下,这3种菌对二十八烷的降解效率分别为51%、34.3%和45%,而3种菌株混合后的协同降解率可以达到72%,明显提高了对二十八烷的降解率。利用假单胞菌、苍白杆菌(Ochrobαctrum)、博德特氏菌(Bordetellα)和戈登氏菌,采用不同的菌种组合降解HV1500型矿物基础油,发现多菌种(两种以上)复合降解效率高于两菌种的联合降解,更优于单一菌株。可见,多菌种协同降解具有对复杂组成的矿物润滑油可以大幅度提高生物降解效率,且具有以简便、易行、可靠等优势。
综合述评
润滑剂可分为内润滑剂与外润滑剂(但两者无严格界限,有时内润滑剂亦能起一定外润滑作用,反之亦然)。内润滑剂一般具有极性,可包覆在PVC颗粒的表面,并具有一定程度的渗透性,在聚合物塑化过程中,饱和限以下不形成润滑相,即溶解于PVC颗粒内部及外部,减少颗粒与颗粒之间、熔融后分子与分子之间的摩擦力,不影响制品的透明度,如十八烷醇等。
外润滑剂一般为非极性物质,在塑料加工过程中,只在PVC颗粒外表形成极强的润滑分散相,很难渗透入PVC颗粒内部,在加工过程中,延长PVC的塑化时间,只在PVC颗粒之间、颗粒与加工模具之间减少摩擦力,如石蜡等。
PP、ABS等塑料加工传统使用石蜡作为润滑剂,但随着塑料加工自动化、高速化发展趋势以及适应碳酸钙、滑石粉等填料以提高塑料强度,降低成本需要,用专用石蜡来替代普通石蜡已在某些塑料制品加工得到了应用。润滑效果不但明显降低了加工能耗,有利设备维护,有利于提高产品强度和光洁度、亮度,而且由于增强了与碳酸钙、滑石粉之类填料的润湿作用,有利于减少树脂比例,降低产品成本,目前应用和发展潜力很大。
微晶蜡具有硬度小、柔韧性好、受力情况下倾向于塑性流动和延伸度大、挠性好、对油品的凝胶强度大等独特的性质。这些特性决定了它有着极为广泛的用途,可用于润滑剂、上光、纺线涂蜡等,具有广阔的市场前景。由于微晶蜡对发展调配蜡、特种蜡和热熔黏合剂等起着决定性作用,表现出不可替代性,所以微晶蜡产品的市场潜力很大。
氧化微晶蜡尚有许多新用途正在开发,目前得到广泛应用的是金属及金属制品防锈蚀、塑料润滑用蜡、乳化蜡等领域。
微晶蜡世界市场缺口较大,由于缺少合适的原料及生产难度大等原因,实际生产量远远不能满足要求,随着环保要求日益严格,今后微晶蜡产品的需求将以每年2%的速度递增。与此同时,微晶蜡生产过程中生产的光亮油也具有广阔的国内市场,由于国内光亮油产量少,多数润滑油生产厂家依靠进口。微晶蜡独特的性质使得微晶蜡可以不经改性直接使用,广泛应用于化妆品、食品及食品包装、橡胶助剂、热熔胶、医药、乳化炸药、油墨、涂料、上光、纺线涂蜡、铸铁、电子电器绝缘、文教用品(如橡皮泥、蜡纸、蜡笔)等方面。