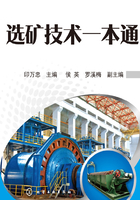
五、溜槽分选
47.溜槽选矿过程是如何进行的?
溜槽选矿是利用斜面水流的方法进行分选的过程。将矿粒混合物给入倾角不大的斜槽内,一般为3°~4°,不超过6°。在水流的冲力、矿粒的重力和离心力以及摩擦力的作用下使矿粒按密度进行分层。由于水流在槽中的速度分布是上层大下层小,故密度较大的矿粒集中在下层,受到较小的水流冲力及较大的槽底摩擦力,沿槽底缓慢向前运动,密度小的矿粒集中在上层,被水流携带以较快的速度从槽内流出。然后,按层分别截流即可得到密度不同的两种产物,即精矿和尾矿。
48.溜槽有哪几种?
溜槽的种类很多,按矿粒所受的作用力可分为重力溜槽、离心力溜槽;按入选粒度可分为粗粒溜槽、矿砂溜槽和矿泥溜槽。粗粒溜槽由于需要大量人工操作,常被跳汰机所取代。常用溜槽见表4-11。
表4-11 常用溜槽一览表

粗粒溜槽和矿砂溜槽主要用于金、铂、锡的砂矿以及其他稀有金属的砂矿,如独居石、锆英石等砂矿的选别,矿泥溜槽常用于钨、锡等矿石的选别。
49.选金用粗粒溜槽的结构和富集过程是怎样的?
选金用粗粒溜槽作为低品位砂金矿的粗选设备,具有结构简单、投资少、无药剂污染等优点。但其劳动强度较大,回收率较低,约为50%~60%。
这种粗粒溜槽的结构如图4-31所示,槽体为钢板或木板制成的长槽,长度在4m以上,宽为0.4~0.6m,高为0.3~0.5m。在槽底有钢制或木制横向或网格状挡板,图4-31所示槽底每隔0.4m设有角钢(50mm×50mm)制作的横向挡板。有的还在挡板下面铺置一层粗糙铺面,如苇席、毛毯、毛毡、长毛绒布等。槽的安装坡度一般为5°~8°。

图4-31 选金用粗粒溜槽
矿浆自高端给入,在槽内作快速紊流流动,旋涡的回转运动不断地将密度大的金粒及其他重矿物转送到底层,形成重矿物层并被挡板挡住留在槽内;上层轻矿物则被水流推动,排出槽外。经过一个时期槽底精矿较多时,停止给矿,加水清洗,再去掉挡板进行冲洗,最后,冲出槽底精矿。有铺面的要对铺面进行清洗,洗出物并入精矿。
50.扇形溜槽的工作原理是什么?
扇形溜槽的形状如图4-32所示。扇形溜槽的给矿端较宽,愈接近排矿端截面愈小。它的工作原理是当固体含量占50%~60%的矿浆由前面宽的一端进入溜槽,流向尖缩的排矿端。由于溜槽的倾斜度不太大(一般15°~18°),但矿浆的浓度较大,可以得到很平稳的矿流,与其他溜槽一样,矿浆在流动过程中固体物料便按密度分层,最下层的重矿物与溜槽底面发生摩擦,因而流动的速度很缓慢,而上面几层矿物由于较轻,所以随水流动速度很快。随着溜槽的逐渐尖缩,所形成的液流层便垂直分开,其结果是速度差越来越大。由于各层矿浆排出速度不同,在排矿端便形成一个扇形,借助截板可以分成重产品、中矿和轻产品。扇形溜槽广泛用于处理品位低的砂矿,也处理细粒级铁矿石、钨矿石和锡矿石,但不如处理粗粒效果高。

图4-32 扇形溜槽
1—给矿嘴;2—侧壁;3—槽底;4—扇形板;5—分割器
51.影响扇形溜槽分选过程的操作因素有哪些?
影响溜槽分选过程的操作因素有:
(1)扇形溜槽的坡度一般比平面溜槽要大(常用16°~20°),目的是提高矿浆的运动速度梯度。
(2)给料浓度的变化也对分选过程有重要影响,在扇形溜槽中,保持较高的给料浓度是其分层的重要条件。
影响溜槽分选过程的结构因素有:
(1)尖缩比是指排料端宽度与给料端宽度之比,一般介于l/10~1/20。
(2)溜槽长度主要影响矿物在溜槽中的选矿时间,以1000~1200mm为宜。
(3)槽底材料应有适当的粗糙度,以满足分选过程的需要。常用的槽底材料有木材、玻璃钢、铝合金、聚乙烯塑料等。
52.圆锥选矿机的结构是怎样的?有何特点?
圆锥选矿机的工作表面可认为是由多个扇形溜槽去掉侧壁拼成圆形而成,分选即在这倒置的圆锥面上进行(如图4-33所示),由于消除了扇形溜槽侧壁的影响,因而改善了分选效果。最初由澳大利亚昆士兰索思波特矿产公司的赖克特(E.Reichart)研制成功的是单层圆锥选矿机,后来又制成了图4-34所示的双层圆锥选矿机和多段圆锥选矿机,以简化生产流程和提高设备的生产能力。

图4-33 单层圆锥选矿机
1—给料斗;2—分配锥;3—分选锥;4—截料喇叭口;5—转动手柄;6—高密度产物管;7—低密度产物管;8—高密度产物;9—低密度产物

图4-34 双层圆锥选矿机
1—给料斗;2—分配锥;3—上层分选锥;4—下层分选锥;5—截料喇叭口;6—高密度产物管;7—低密度产物管
目前国内外制造的圆锥选矿机均是采用多段配置,在一台设备上连续完成粗、精、扫选作业。为了平衡各锥面处理的物料量,给料量大的粗选和扫选圆锥制成双层的,而精选圆锥则是单层的。单层精选圆锥产出的高密度产物再在扇形溜槽上精选。这样由1个双层锥、1~2个单层锥和1组扇形溜槽构成的组合体,称为1个分选段。三段七锥圆锥选矿机的结构如图4-35所示。

图4-35 三段七锥圆锥选矿机的结构
1,8,15—给料槽;2,9,16—双层圆锥;3—上支架;4,5,11,12—单层圆锥;6,13,18—扇形溜槽;7—上接料器;10—中支架;14—中接料器;17—下接料器;19—下支架;20—总接料器
圆锥选矿机的影响因素与扇形溜槽的相同,但回收率比扇形溜槽的高,而富集比比扇形溜槽的低。它的主要优点是处理能力大,分选成本低,适合处理低品位砂矿。其缺点是设备高度大,在工作中不易观察分选情况。
圆锥选矿机的适宜给矿粒度为0.074~2mm,给矿浓度通常为55%~65%,DS2000型七锥圆锥选矿机的台时处理能力为50~80t;DS3000型七锥圆锥选矿机的台时处理能力为220~350t。
53.扇形溜槽和圆锥选矿机有哪些应用和特点?
扇形溜槽和圆锥选矿机的工作原理相同,都属于固定斜面溜槽。它们主要用于选别海滨砂矿或陆地砂矿。扇形溜槽结构简单,易于制造,有的还用它从选矿厂尾矿库的尾矿砂中回收重矿物。
扇形溜槽和圆锥选矿机的选矿具有如下特点:
(1)处理能力大 按每平方米占地面积计的生产能力可达数百千克到数吨。例如,规格为300mm×13mm×1000mm的扇形溜槽的单槽处理能力为0.9~1.4t/h;一台重2.5t的四段圆锥选矿机处理能力可达60~75t/h,故适合于处理矿石量很大且品位低的矿石。
(2)给矿浓度高,为50%~70%,因此省水。
(3)作业成本低廉,设备本身无运转部件,不消耗动力和药剂。
(4)扇形溜槽结构简单、轻便,造价便宜(我国一般均用木板做溜槽),用水量比其他溜槽少,生产率高。
(5)单台选别的富集比低,难以产出最终精矿。为克服这一缺点,常把数台扇形溜槽或圆锥选矿机组合起来使用。
(6)入选粒度范围较宽,为3~0.1mm,但回收细粒级效果较差。
54.螺旋选矿机的结构和分选过程是怎样的?
螺旋选矿机的结构如图4-36所示。它是把一个溜槽绕垂直轴线弯曲成螺旋状而做成的,螺旋有3~5圈,固定在垂直的支架上,螺旋槽的断面为抛物线或椭圆的一部分,槽底在纵向(沿矿流流动方向)和横向(径向)均有一定的倾斜度。由第二圈开始,大约在槽底中间部位设有重产物排料管(共4~6个),排料管上部装有截料器,它能拦截重矿物流使之进入排矿管排出,截料器的两个刮板压紧在槽面上,且其中的可动刮板可以旋转用来调节两刮板间张口角度大小,从而调节重矿物的排出量,如图4-37所示。为提高重产物的质量,在槽内缘设有若干个加水点,称为洗涤水,它由中央水管经过阀门给入槽内缘。

图4-36 螺旋选矿机
1—给矿槽;2—冲洗水导槽;3—螺旋槽;4—螺旋槽连接法兰;5—尾矿排出溜槽;6—机架;7—重矿物排出管口

图4-37 截料器
1—排料管;2—固定刮板;3—可动刮板;4—压紧螺钉;5—螺母;6—垫圈
分选时,矿浆自槽上部匀矿器沿槽宽均匀给入,矿浆在沿槽流动过程中发生分层,重矿物进入底层,并在各种力的综合作用下向槽的内缘运动;轻矿物则在快速的回转运动中被甩向外缘。于是,密度不同的矿粒即在槽的横向展开了分带,如图4-38所示。沿槽内缘流动的重矿物被截料器拦截,通过排料管排出,由上方第一至第二个排料管得到的重产物质量最高,以下重产物质量降低。槽内缘所加洗涤水把重产物夹杂的部分轻矿物冲向外缘,有利于提高精矿的质量。尾矿则由最下部槽的末端排出。

图4-38 矿粒在螺旋槽内的分带(黑色颗粒表示重矿物,白色为轻矿物)
55.螺旋选矿机的操作要点有哪些?
(1)给矿粒度最大为6mm。有过大矿块进入时,会扰动矿流和阻塞精矿排出管。片状大块脉石也对选别不利。因此入选前要用筛子篦出大块。另外入选物料含泥多时会使分选效果变坏,因此含泥多时要预先脱泥。
(2)控制好给矿量。当含泥多精矿又较细时,给矿量可小些;精矿粒度粗含泥少时,给矿量可大些。对给矿浓度要求不严格,浓度在10%~30%范围内变化对选别指标影响不大。
(3)洗涤应从内缘分散供给,以免冲乱矿流,洗涤水量大,精矿品位高,但回收率降低;洗涤水小,对提高回收率有利,洗涤水由上往下应逐次加大。
(4)精矿产率是通过转动截取器的活动刮板来调整的,截取的精矿太多时,精矿品位会降低。活动刮板的适宜位置应通过取样考查来确定,有了经验后再灵活掌握。
56.螺旋溜槽和螺旋选矿机有什么区别?
螺旋溜槽和螺旋选矿机的外形和工作原理基本相同,但两者在结构、性能和使用方面有区别,主要不同有如下几点:
(1)螺旋选矿机的槽底断面线为抛物线或椭圆的一部分,而螺旋溜槽的槽底断面线为立方抛物线,因此,螺旋溜槽的槽底宽而平缓,更适合于处理细粒物料。
(2)螺旋溜槽是在槽末端分别接取精、中、尾矿,而螺旋选矿机是在上部截取精矿,在槽末接尾矿。
(3)螺旋溜槽没有洗涤水,而螺旋选矿机加有洗涤水。
(4)螺旋溜槽的入选粒度比螺旋选矿机小,螺旋选矿机的适宜入选粒度为2~0.074mm,而螺旋溜槽适宜的处理粒度为0.3~0.04mm。
(5)给矿浓度方面,螺旋溜槽要求浓度高,一般不低于30%,而螺旋选矿机浓度要求不严格,下限可到10%。
57.螺旋溜槽有哪些优缺点?
螺旋溜槽在选别赤铁矿、回收尾矿中的重矿物以及选别稀有金属及有色金属矿物中得到广泛应用,这是因为它具有如下优点:①本身无运转部件,不消耗动力;②设备占地面积小,处理能力大;③因给矿浓度高又不加洗涤水,因此省水;④操作方面要求的条件(如给矿粒度、浓度等)不苛刻,选别指标较稳定。
缺点是设备高差较大,往往需要砂泵提升矿浆才能给矿。另外,精矿品位稍低。
58.影响螺旋选矿机和螺旋溜槽选别的因素有哪些?
影响螺旋选矿机和螺旋溜槽选别指标的因素同样是包括结构因素和操作因素两个方面,其中结构因素主要有:
(1)螺旋直径D 螺旋直径是螺旋选矿机和螺旋溜槽的基本参数,它既代表设备的规格,也决定了其他结构参数。研究表明,处理1~2mm的粗粒物料时,以采用ф1000mm或ф1200mm以上的大直径螺旋为有效;处理0.5mm以下的细粒物料时,则应采用较小直径的螺旋。在选别0.074~1mm的物料时,采用直径为500mm、750mm和1000mm的螺旋溜槽均可收到较好的效果。
(2)螺距h 螺距决定了螺旋槽的纵向倾角,因此它直接影响矿浆在槽内的纵向流动速度和流层厚度。一般来说处理细粒物料的螺距要比处理粗粒物料的大些。工业生产中使用的设备的螺距与直径之比(h/D)为0.4~0.8。
(3)螺旋槽横断面形状 用于处理2~0.2mm物料的螺旋选矿机,螺旋槽的内表面常采用长轴与短轴之比为2:1~4:1的椭圆形,给料粒度粗时用小比值,给料粒度细时用大比值。用于处理0.2mm以下物料的螺旋溜槽的螺旋槽内表面常呈立方抛物线形,由于槽底的形状比较平缓,分选带比较宽,所以有利于细粒级物料的分选。
(4)螺旋槽圈数 处理易选物料时螺旋槽仅需要4圈,而处理难选物料或微细粒级物料(矿泥)时可增加到5~6圈。
影响螺旋选矿机和螺旋溜槽选别指标的操作因素主要有:
(1)给矿浓度和给矿量 采用螺旋选矿机处理2~0.2mm的物料时,适宜的给矿浓度范围为10%~35%(固体质量分数);采用螺旋选矿机处理-0.2mm粒级的物料时,粗选作业的适宜给矿浓度为30%~40%(固体质量分数),精选作业的适宜给矿浓度为40%~60%(固体质量分数)。当给矿浓度适宜时,给料量在较宽的范围内波动对选别指标均无显著影响。
(2)冲洗水量 采用螺旋选矿机处理2~0.2mm的物料时,常在螺旋槽的内缘喷冲洗水以提高高密度产物的质量,而对回收率又没有明显的影响。一台四头螺旋选矿机的耗水量约为0.2~0.8L/s。在螺旋溜槽中一般不加冲洗水。
(3)产物排出方式 螺旋选矿机通过螺旋槽内侧的开孔排出高密度产物,在螺旋槽的末端排出中间产物和低密度产物;螺旋溜槽的分选产物均在螺旋槽的末端排出。
(4)给矿性质 主要包括给矿粒度、给矿中低密度矿物和高密度矿物的密度差、颗粒形状及给矿中高密度组分的含量等。工业型螺旋选矿机的给矿料粒度一般为-2mm,回收粒度下限约为0.04mm;螺旋溜槽的适宜分选粒度范围通常为0.3~0.02mm。
59.铺面溜槽的结构是怎样的?
铺面(布)溜槽的结构如图4-39所示,可用木板或铁板制作。槽宽1~1.5m、长2~3m。头部有分配矿浆用的匀分板,槽底面不设挡板,而采用表面粗糙的棉绒布、毛毯、棉毯、尼龙毯等做铺面。工作时槽面坡度为7°~8°,匀分板角度为20°~25°。选金时的入选粒度小于1mm。可用于处理混汞或浮选的尾矿。给矿浓度为8%~15%。

图4-39 铺面(布)溜槽
1—匀分板;2—铺布;3—槽体
铺面溜槽的工作方式为间歇式。矿浆自匀分板上部给入进入槽底后形成均匀流层,重矿物沉积在槽面上,轻矿物随矿浆流排出。当沉积物积累到一定数量后(比如经过一个班或几个班时间),停止给矿,将铺布取出,在容器中清洗回收重矿物。然后将铺布铺好,进行下一周期的工作。
60.皮带溜槽的结构是怎样的?
皮带溜槽是沉积排料型连续工作的微细粒级物料精选设备,其基本构造如图4-40所示,主要分选部件是低速运动的皮带,皮带上表面长约3m,宽1m,倾斜5°~17°,距首轮中心0.4~0.6m处经均分板给料。矿浆基本呈层流流态沿皮带向下流动。在流动的过程中,不同密度的颗粒基于前述的分选原理发生分层,位于上层的低密度颗粒随矿浆流一起由下端排出,成为低密度产物。从给料点到皮带末端为设备的粗选带,其长度为2.5m左右。分层后沉积到皮带面上的高密度颗粒随带面向上移动。在皮带上端给入冲洗水,进一步清洗出低密度颗粒,从给料点到皮带首端这一段长约0.4m,为精选带。高密度颗粒随带面绕过首轮后,加水冲洗并用转动的毛刷将高密度产物卸下,从而实现连续作业。

图4-40 皮带溜槽的结构
1—带面;2—天轴;3—给水均分板;4—传动链条;5—首轮;6—下张紧轮;7—冲洗高密度产物水管;8—毛刷;9—高密度产物槽;10—机架;11—调坡螺杆;12—低密度产物槽;13—滑动支座;14—螺杆;15—尾轮;16—给料均分板;17—托辊
皮带溜槽的富集比和回收率都比较高,但设备的生产能力很低,所以主要用作一些微细粒级物料的精选设备。影响其分选指标的因素主要是带面的运行速度、带面坡度、粗选和精选段的皮带面长度等。
带面的速度越大,粗选时间越长,精选时间越短,适宜的带面速度约为0.03m/s;适宜的带面坡度为5°~17°。操作中的调节因素是冲洗水量和给矿浓度等。给矿的适宜固体质量分数值为25%~45%,在此范围内波动对选别指标影响不大;最终的精选作业冲洗水量以5~7L/min为宜,初次精选以2~4L/min为宜。皮带溜槽的给料粒度一般为-0.074mm,有效回收粒度下限可达0.01mm,但多数为0.02mm。
61.40层摇动翻床的结构是怎样的?有何特点?
摇动翻床是一种沉积型间歇工作设备,整个过程都是在控制机构监控下自动完成。设备共有40层床面,分为2组,分别安装在2个框架内(见图4-41)。床面采用玻璃钢制作,长1525mm,宽1220mm,每层厚1.5mm,床面间距12.5mm。两侧用厚塑料板与框架连成一体,工作时床面倾角为1°~3°。两个框架连同传动装置用2根钢丝绳悬挂在钢架上。

图4-41 40层摇动翻床示意图
1—机架;2,3—上、下组床面;4—悬挂用钢丝绳;5—翻转床面汽缸
这种设备的特点是在2组床面中间装有不平衡重锤,用1台功率为367.5W的直流电动机带动作旋转运动。不平衡重锤的质量为6.8kg,距旋转轴的轴心300mm,转动速度为150~260r/min,随着不平衡重锤的转动,床面亦作回转运动,其振幅为5~7mm,为了保证床面运动平稳,在框架两侧用弹簧张紧。
矿浆由分配箱分别给到每个床面上,在沿床面流动过程中因受到回转剪切而松散,并发生分层。高密度颗粒沉积在床面上,低密度颗粒随矿浆流一起排出,经过一段时间后,停止给料,借汽缸推动使床面倾斜,沉积在床面上的高密度颗粒随即滑下,然后给入低压水冲洗床面。约经过30s的冲洗时间后,床面恢复原位,继续进行下一个分选周期。
40层摇动翻床的分选工作面面积达74.4m2,而占地面积仅有4.6m2,选别-0.074mm的锡矿石时,处理能力达2.1~3.1t/h,给矿浓度一般为15%,回收粒度下限以石英计时可达0.01mm。这种设备的缺点是床面间的垂直距离太小,当床面上出现物料分布不均等异常情况时,难以被发现和及时处理。
62.横流皮带溜槽的结构是怎样的?有何特点?
横流皮带溜槽是与摇动翻床配套使用的微细粒级物料精选设备,其结构类似于皮带溜槽与摇床的联合体。它的分选工作面是一用四根钢丝绳悬挂在机架上的无极皮带,带面沿横向倾斜,纵向则呈水平。在带面下面安置不平衡重锤,皮带在沿纵向缓慢移动的同时,作回转剪切运动。图4-42是单侧试验型横流皮带溜槽的结构示意图。矿浆由带面上方一角给入,在沿横向流动中发生分层,高密度颗粒沉积在带面上随皮带运动,通过中间产物区进入精选区,借横向水流冲走混杂在其中的低密度颗粒,最后利用冲洗水将其冲入高密度产物槽中,低密度产物及中间产物则由侧边排出。

图4-42 单侧横流皮带溜槽结构示意图
工业生产中使用的横流皮带溜槽相当于将两台单侧试验型溜槽合并在一起,给料从中间的脊背向两侧流下。带面上分选区的分布情况如图4-43所示。

图4-43 双侧横流皮带溜槽带面上分选区分布
63.振摆皮带溜槽的结构是怎样的?有何特点?
振摆皮带溜槽也是微细粒级物料的精选设备,其结构如图4-44所示。设备的主体工作件为一弧形无极皮带,带面绕皮带轮运行,同时在摇床头带动下作差动振动,并在摆动机构带动下作左右摆动,摆角在8.5°~25°。带面纵向坡度为1°~4°,在首轮带动下以大约0.05m/s的速度向倾斜上方运行。给料点设在距首轮大约800mm处,给料匀分板设在皮带两侧,每当皮带摆至最高位置时,矿浆即轮番给入。矿浆流在凹下的皮带表面上,也作左右摆动,形成浪头、浪尾交替运动(见图4-45),同时又沿皮带的倾斜方向向下流动。带面的差动运动有助于物料的松散分层,带面的差动运动推动颗粒运动的方向指向带面倾斜的上方。

图4-44 800mm×2500mm振摆皮带溜槽的结构
1—选别皮带;2—皮带传动电动机;3—摇床头;4—摆动驱动电动机;5—给料装置;6—低密度产物排出管;7—高密度产物槽;8—摆动机构;9—给水斗;10—喷水管;11—振动驱动电动机

图4-45 矿浆在皮带面上的横向流动
矿浆流在带面上作非恒定流动,其运动轨迹呈S形,矿浆的剪切流动及带面的振动促使物料很快按密度发生分层。微细的高密度颗粒被浪头携带到皮带两侧,并在那里沉积下来;高密度粗颗粒则沉积在皮带中心附近。沉积下来的高密度颗粒随带面一起向上移动,通过给料点进入精选区,在那里进一步被水流冲洗,以清除夹杂在其中的低密度颗粒,最后绕过首轮,用水冲洗排入高密度产物槽内。在皮带中心附近的上层矿浆流中主要悬浮着低密度颗粒,它们随矿浆流一起向下流动,从皮带末端排出,成为低密度产物。
振摆皮带溜槽的生产能力很低,单台设备的处理量只有40~70kg/h。但由于它交替地利用了湍流松散和层流沉降,所以分选的精确度很高,其最大优点是可以分开微细粒级物料中密度差较小的组分,因此适合做精选设备,尤其适合处理其他细粒级物料分选设备产出的中间产物。其回收粒度下限可达0.02mm。