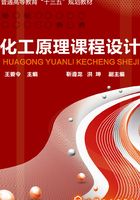
3.5 精馏塔塔板数的计算
板式精馏塔设计的一个重要内容便是确定所需要的塔板数。要计算实际塔板数,首先要求出理论塔板数;其次根据不同类型的板式塔确定塔板效率;最后根据理论塔板数和塔板效率求取实际塔板数。
而理论塔板数的确定是交替应用相平衡关系和物料平衡的操作线关系进行计算的。所以要首先确定汽液相平衡关系,其次确定回流比,进而找出操作线方程,最后再进行塔板数的计算。
3.5.1 汽液相平衡关系
汽液相平衡是精馏塔计算的理论依据,下面简单介绍一下汽液相平衡关系。
假设组分A和B形成理想液态混合物,组分A的平衡分压pA由于被组分B稀释而降低,依据拉乌尔定律,pA可用下式表示:
(3-20)
式中,表示纯液体A的蒸气压;xA表示溶液中组分A的摩尔分数。
同理,将上述关系应用于组分B,则有:
(3-21)
式中,表示纯液体B的蒸气压;xB表示溶液中组分B的摩尔分数。
依据道尔顿分压定律,混合液的汽相总压可表示为:
(3-22)
又由于xB=1-xA,上式中若省略下标A,液相组成用易挥发组分A的摩尔分数x表示,式(3-22)可写成:
(3-23)
式(3-23)也可整理为:
(3-24)
在一定的总压p下,对于某一指定温度t,可查得蒸气压数据、
,则可通过式(3-24)计算液相组成x。
又由道尔顿分压定律,易挥发组分A的汽相组成可用分压表示如下:
y=pA/p (3-25)
则组分B的汽相组成也便可知。
此处若引入相对挥发度的概念, (3-26)
则依然由道尔顿分压定律,式(3-26)可写成:
(3-27)
又二元物系可用单一变量表示相组成,此处用易挥发组分A的组成表示汽液相组成,且省略下标A,式(3-27)可写成:
(3-28)
式(3-28)表示互成平衡的汽液两相组成y与x的关系,称为理想溶液的汽液平衡方程式。当α值已知,便可由x(或y)求出平衡时的y(或x)。
图3-10给出了苯-甲苯物系在总压为1atm下的相平衡相图。在精馏操作中,广泛应用到汽液平衡组成的相图,又称x-y相图。由于汽相中易挥发组分的含量比液相中多,即y>x,所以,x-y汽液相平衡曲线与对角线相比,向上突出。x-y曲线突出得离对角线越远,说明易挥发组分的挥发度越大,越有利于在精馏过程中进行分离。

图3-10 苯-甲苯的x-y相图
3.5.2 物料衡算及操作线
为了计算离开各层塔板的组成,除了应用式(3-28)进行汽液相平衡计算以外,还需要计算自任一塔板下降的液相组成与其下层塔板上升的汽相组成之间的关系。由于在加料塔板上有物料进入,使得精馏段与提馏段的汽、液相流量有所不同。现分别就精馏段与提馏段分别进行分析。
(1)精馏段操作线
精馏段的操作过程如图3-11所示。

图3-11 精馏段的操作过程
塔板序号自上而下数,离开各层塔板的汽、液相组成分别以y1,x1,y2,x2,…,yn,xn表示。自第一层塔板上升的蒸气若全部冷凝,冷凝液的组成y1与给定的产品组分xD相等。基于理论塔板的概念,离开各层塔板的汽、液相达到平衡,则可根据汽液平衡关系式(3-28)计算出x1。
计算自第二层塔板上升蒸气的组成y2,则需要寻求其他关系。精馏段上升蒸气经冷凝后的冷凝液一部分(D)作为产品流出,另一部分(L)回流至塔内。基于恒摩尔流假定,离开各层塔板的液体流量均为L,气体流量均为V。对图3-11所示虚线范围进行物料衡算则有:
V=L+D (3-29)
Vy2=Lx1+DxD (3-30)
由以上两式可得,
(3-31)
由此便可计算出上升蒸气的组成y2。
同理,若是对整个精馏段做物料衡算,则可得
(3-32)
若引入回流比的概念,则式(3-32)可写成:
(3-33)
式(3-32)、式(3-33)均称为精馏段操作线方程,表示精馏段中相邻两层塔板之间的上升蒸汽组成yn+1与下降液体组成xn之间的关系。
精馏段操作线方程对应的曲线称为精馏段操作线,是一条斜率为(或
)的直线。精馏段相邻两层塔板之间的组成点(xn,yn+1)均在精馏段操作线上,如图3-12所示。

图3-12 精馏段计算的图解法
交替应用相平衡关系以及精馏段操作线关系可求得精馏段各个塔板上的汽液相组成。此种计算方法被称为逐板计算法,较为烦琐,但对于理解精馏过程至关重要。
在图3-12中再做出相平衡曲线,就可以用所谓的x-y图解法求取汽、液相的组成以及理论塔板数。对于给定的塔顶产品含量要求xD,在操作线上选定点a(xD,xD),由于自第一层塔板上升的汽相组成为y1,对于全凝器有y1=xD,从a点向相平衡曲线作平行线交相平衡曲线于点E1(x1,y1),依据点E1可确定x1。再从点E1(x1,y1)向操作线作垂线交点为A1,由于点A1在操作线上,所以该点的坐标应为A1(x1,y2)。依此类推,再从点A1(x1,y2)向相平衡曲线作平等线交点为E2(x2,y2),这样可以逐步求得离开各层塔板的汽、液相组成,直到加料板为止。
一般情况下,并不需要详细知道离开每层塔板的汽、液相组成,而只要求达到指定的分离效果的理论板数。为此,只需要数一数平衡线上的梯级数即可确定理论板数。这种方法称为x-y图解法,其理论基础仍然是交替应用物料平衡与相平衡关系。
(2)提馏段操作线
提馏段的操作过程如图3-13所示。

图3-13 提馏段的操作过程示意
自m层塔板下降的液相组成与自其下层塔板上升的汽相组成仍然符合相平衡关系。而对于物料平衡,由于在加料板上有进料的影响,使得提馏段的汽、液相流量与精馏段不同,此处假定汽、液相流量分别为L'、V',则对图3-13中虚线所示范围做物料衡算有:
L'=V'+W (3-34)
L'xm=V'ym+1+WxW (3-35)
由以上两式可得,
(3-36)
式(3-36)代表操作线上点(xm,ym+1)之间的关系。
省略下标,可得提馏段操作线方程:
(3-37)
式中,塔底产品产量W及其组成xW已知,但塔内的汽、液相流量V'、L'由于受进料的影响,需要根据进料状况具体分析。可能的进料状况有以下几种:过冷液体进料、饱和液体进料、饱和汽液混合物进料、饱和蒸气进料以及过热蒸气进料。
假设进料中液相所占的比例为q,则汽相所占的比例为1-q。如图3-14所示。

图3-14 提馏段的操作过程示意
进料为混合汽液进料;液流;
气流
对加料板做物料衡算,则有:
L'=L+qF (3-38)
V'=V-(1-q)F (3-39)
联立求解式(3-37)、式(3-33)两条操作线方程,可以求得两条操作线的交点d,连接点d与点(xW,xW)便是提馏段操作线。
联立式(3-38)、式(3-39)以及式(3-2),可求得:
(3-40)
该方程代表了两条操作线交点d的轨迹,从该式可以看出它完全由进料状况以及进料组成决定,称为进料线方程。
根据精馏段操作线与提馏段操作线,利用x-y图解法,便可求出整个精馏塔所需要的理论板数。
3.5.3 回流比的选择与确定
(1)回流比的选择
回流比R的选择,关乎塔的制造费用与操作费用,选择回流比R应当使总费用最小。但是对于课程设计而言,很难得到计算各项费用的准确数据,故常常取一个经验数据,通常取回流R为最小回流比Rmin的1.1~2倍。
(2)最小回流比Rmin的确定
在设计条件下,如选用较小的回流比,两操作线向平衡线移动,达到指定分离程度所需要的理论板数增多。当回流比减至某一数值时,两操作线的交点落在平衡线上,此时理论板数为无穷多,此即为指定分离程度时的最小回流比。最小回流比的计算公式为:
(3-41)
式中 ye——操作线与平衡线相交时的汽相组成;
xe——操作线与平衡线相交时的液相组成。
【设计分析1】当回流比选的偏小,则所需理论板数多,在操作时能顺利完成分离任务及要求,但设计出的塔板结构对蒸汽及液体负荷的弹性则降低;若回流比偏大,设计出的塔板结构能承担较大的负荷,但理论板数少,在估算塔板效率时宜选偏小值来满足分离任务及要求。一般来说,对于难分离或分离要求较高的混合物通常选用较大的回流比;而为了减少加热蒸汽消耗量等从节能方面考虑则宜采用较小的回流比。统计表明,实际生产中的操作回流比以1.6~1.9倍最小回流比的范围使用较多。
3.5.4 理论塔板数的计算
精馏塔理论塔板数的求取方法有多种,一般可选用逐板计算法、直角梯级图解法、捷算法等,下面分别简要加以介绍。
(1)逐板计算法
逐板计算法也叫解析法。根据理论塔板的概念,假定离开每层塔板的汽、液相组成达到平衡。如果采用全凝器,那么离开第一层塔板的汽相组成y1与塔顶产品组成xD相同,而塔顶组成往往是给定值,应用相平衡方程,可求得离开第一层塔板的液相组成x1,再应用操作线方程,由x1计算出由下层塔板上升的汽相组成y2。这样依次交替应用相平衡关系与精馏段操作线方程逐板计算每层理论塔板的汽、液相组成,直至达到进料浓度,此处应为进料板。接下来,由精馏段操作线方程改为提馏段操作线方程,仍然交替应用平衡线方程与操作线方程进行逐板计算,直至液相组分小于塔底产品组分。此种计算方法概念清晰,结果准确,特别适用于相对挥发度较小难以分离的物系。但是,该方法的缺点是计算较为繁杂,不过可应用现代计算机技术,以帮助克服此困难。
(2)直角梯级图解法
直角梯级图解法本质原理上仍然是交替地应用相平衡关系及物料平衡关系,只是该方法是在x-y图上交替应用两个平衡关系,较为直观地绘出梯级来代表理论塔板。其具体步骤如下。
①在x-y图中作出待分离混合物系的相平衡曲线以及对角线,如图3-15所示。

图3-15 冷液进料时理论板数的图解法示意
②在x轴上分别定出x=xD、xF、xW三个点,并通过这三个点依次向对角线作垂线分别交于点b、f、a。
③在y轴上定出yc=xD/(R+1)点c,连接ac,即为精馏段操作线。
④由进料状态求出q线的斜率q/(q-1),通过点f作q线。
⑤q线与ac的交点设为点d,连接bd,即为提馏段的操作线。
⑥从a点开始,在相平衡线与精馏段操作曲线之间作直角梯级。当直角梯级跨过点d时,这个梯级就相当于加料板。然后改为在相平衡线与提馏段操作曲线之间作直角梯级,直至梯级跨过点b为止。根据理论塔板的概念,一个直角梯级代表一块理论塔板,所有绘制的直角梯级数即为理论塔板数,同时也确定了进料板,最后一个直角梯级代表了再沸器。
该方法与逐板计算法相比,不太精确,为了得到较为准确的结果,可以采用适当的放大比例进行作图求解。尽管没有逐板计算法精确,但由于该方法简单直观,仍然得到了广泛的应用。
(3)捷算法
通过分析理论塔板数N与回流比R之间的关系可知,当回流比R从最小回流比Rmin增大至适当的回流比时,理论塔板数N随之从无穷大减小至一个适当的值,当全回流时,理论塔板数向某一有限值Nmin逼近。如果能够找出R、Rmin、Nmin、N之间的定量关系,便能确定所需要的理论塔板数。依据这一想法,前人曾对多种二元和多元物系在不同的精馏条件下的数值进行整理,得知以上四个数据之间的确实存在着近似的定量关系,用该关系作图便被称为吉利兰关联图,如图3-16所示。

图3-16 吉利兰关联图
图中以X=(R-Rmin)/(R+1)为横坐标,以Y=(N-Nmin)/(N+1)为纵坐标。应用该图时,可以根据已知条件求算出横坐标X的值,从图上查出对应纵坐标Y的值,从而可以求得理论塔板数N。吉利兰关联图中的曲线也可以近似用其拟合的关系式代替:
Y=0.75(1-X0.567) (3-42)
捷算法求解理论塔板数的步骤:
①先按设计条件求出最小回流比Rmin,并选择操作回流比R。
②计算全回流下的最小理论板数Nmin。
③利用吉利兰关联图,计算全塔理论板数N。
④用精馏段的最小理论板数Nmin1代替全塔的Nmin,确定适宜的进料板位置。
最小理论塔板数Nmin、Nmin1可按以下两个公式确定:
(3-43)
(3-44)
式中,a表示物系的平均相对挥发度,可用求解。式(3-43)计算所得的最小理论塔板数不包括塔底再沸器。
该方法与逐板计算法相比,较为粗略,适用于设计过程的初步估算。
3.5.5 实际塔板数的计算及塔板效率
在实际的精馏操作过程中,由于汽液相接触时间有限、液沫夹带等原因,汽液相通过塔板接触进行传热、传质后离开塔板,一般情况下不能达到理想的平衡状态。用塔板效率来表示汽液接触时的传质完善程度。
通常用全塔的总板效率来表示塔板效率。总板效率是指在一定的分离要求与回流比下所需要的理论塔板数NT与实际塔板数Np之比,即
ET=NT/Np (3-45)
通过上式,若得知总板效率便可求得所需要的实际塔板数。
但是,塔板效率与塔板的结构、需要分离的物料性质以及操作状况等众多因素有关。事实上,在板式塔设计中,将所有影响传质过程的动力学因素全部归结到塔板效率上了,很难从理论上定量考察塔板效率,至今未获得令人满意的解决方法。通常基于经验数据来确定塔板效率,工业上测定值通常为0.3~0.7。一般有如下方法来确定塔板效率。
①参考使用过程中的同类型的塔板、物系性质相同或相近的塔板效率的经验数据。
②在生产现场对同类型塔板、类似物系的塔进行实际测定,可得出可靠的塔板效率数据。
③在没有可靠的经验数据或实测数据作参考时,可采用奥康尔的蒸馏塔效率关系图来估算全塔效率,见图3-17。此图是经过对几十个生产中的泡罩塔与筛板塔实际测定的结果,实践证明此图也可用于浮阀塔的效率估计。图中ET、a、μL分别表示全塔效率、平均塔温下的相对挥发度以及进料液在塔顶和塔底平均温度下的黏度。图中曲线也可以用多种关联式表示,应用较广泛的关联式包括:O'Connell关联式ET=0.49(aμL)-0.245;Eduljee关联式ET=51-32.5lg(aμL)以及其他众多关系式。

图3-17 精馏塔的全塔效率
【设计分析2】其他常用计算塔板效率的方法:
(1)Drickaner-Bradford方法
从大量烃类及非烃类工业装置的精馏塔实际数据归纳而成。
ET=0.17-0.616lgμ (3-46)
式中 μ——塔进料液体平均摩尔黏度,cP(1cP=1mPa·s)。
(2)O'connell方法
在32个工业塔和5个实验塔的基础上,得到计算公式:
ET=49(μα)-0.25 (3-47)
式中 μ——塔进料液体平均摩尔黏度,cP。