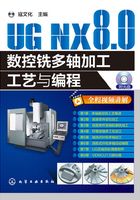
1.5 多轴铣工艺实施步骤
多轴铣工艺实施的基本步骤概括起来有以下要点。
(1)根据2D图纸绘制3D图,即建立CAD/CAM模型
读懂图纸,严格依据图纸绘制3D图。绘制图形后,必须将2D图纸中的全部尺寸进行检查,建立尺寸检查记录表。如果客户已经提供了3D图,这一步就可以省略。但是必须对接受的3D图模型进行全面的检查,检查内容有:
①图形单位英制还是公制,如果是英制,转化为公制,图形实际大小不能改变;
②如果原图是其他软件绘制的,尽可能采用IGS、X_T或者STP格式转化,确保图形特征完整,必要时把中间绘制的曲面和曲线也一起转化,有时会给编程做辅助线带来方便;
③分析有无掉面或者图形有破孔等情况,如果存在这些缺陷,就必须补全图形。
(2)图纸分析、工艺分析
制定整个零件的加工工艺,明确多轴切削工序承担的加工内容及要求。
在大型正规企业,零件加工的整体工艺是由专职的工艺员制定的。工艺员所制定的加工工艺必须符合本企业的实际情况,充分利用现有的人力、物力和财力。本企业不具备条件的,才可以考虑与其他企业合作,进行外发加工。
作为多轴铣数控编程工程师需要了解零件的整体加工工艺,尤其了解数控加工工序的任务,要准确绘制出CNC加工时初始毛坯的3D图,CNC所需要的基准是否齐备,如果基准不全就需要和工艺员沟通协商确定这些基准到底由哪个工序加工。另外,对加工材料的牌号和硬度必须要清楚,以便确定合理的切削参数。
(3)确定多轴加工的装夹方案
对于多轴加工,这一步十分重要。根据CNC的加工内容结合零件形状要预先指定合理的装夹方案。一般来说需要C轴旋转的、类似旋转零件的可以考虑有三爪夹盘。超出三爪卡盘范围的,可以考虑在圆柱毛坯上车出凹槽,在机床的C轴旋转台上用压板装夹。必要时要专门设计出专用夹具,用专用夹具来装夹。
不管采取哪一种装夹方案,必须在编程图形里绘制出相应的3D实体图,再转化2D工程图。2D图发给相关部门加工,3D实体图转化为STL文件以便在VERICUT仿真时调用。绘制3D夹具图的目的是,确定刀具偏摆的极限位置,防止刀具运动时超出极限位置而碰伤夹具和工作台。
(4)编制数控编程及制定加工工步(即数控程序文件)
这是数控编程的核心内容,就是说在正式编程前,事先初步规划需要哪几个数控程序,给每一个数控程序安排其加工内容和加工目的、所用刀具及夹头的规格、加工余量等粗略步骤。多轴铣加工和三轴铣加工加工方法类似,也应该遵守开粗、清角、半精加工、精加工的编程步骤。
以上第(1)~(4)步骤完成以后再进行数控编程就会做到胸有成竹。
(5)定义几何体、刀具及夹头
进入UG的加工模块,切换到几何视图,先定义加工坐标系,这时需注意:如果采用双转台XYZAC型机床加工时,编程用的加工坐标系的原点应该与机床的旋转轴A和C的轴线交点重合;再定义加工零件体、毛坯体。
切换到机床视图,初步定义编程所用的刀具和夹头。
(6)定义程序组,创建各个刀路的轨迹线条
必要时在编程图形里创建辅助面、辅助线,恰当选用加工策略,编制各个刀路。
尽可能采取固定轴定向加工的方式进行大切削量的粗加工、清角和半精加工,精加工才采用联动的方式加工。要时刻确保不要使旋转工作台在旋转时承担过大的重切削工作。
(7)UG内部刀路模拟仿真
多轴铣刀路由于刀具沿着空间偏摆运动复杂,数控编程工程师要力争在编程阶段排除刀具及夹头与周围的曲面产生过切或者干涉。为此,编程时要特别重视对刀路进行检查。发现问题及时纠正。初步进行后处理生成加工代码NC文件。
(8)VERICUT刀路仿真
对于多轴铣编程来说,最大的困惑就是,在UG环境里检查刀路并未发现错误,而实际切削时可能就会出现一些意想不到的错误。这是由于UG模拟的刀路里G00指令和实际机床加工有差别,另外各个操作刀路之间的过渡和实际机床运行有差别,导致UG的仿真与实际有差别。这一点应该引起特别注意。
而VERICUT可以依据数控编程NC文件里的G代码指令、刀具模型,根据事先定义的机床模型、夹具模型、零件模型可以很逼真地进行仿真,最后还可以分析出加工结果模型和零件模型的差别,有无过切和干涉,一目了然。
(9)填写数控程序CNC工艺单
这是数控编程工程师的成果性文件,必须要清楚地告诉操作员以下内容:预定的装夹方案、零点位置、对刀方法;数控程序的名称、所用的刀具及夹头规格、装刀长度等。要求操作员严格执行。(10)在机床上安装零件
如果操作员按照CNC工艺单实施确有困难,需要变更装夹方案或者装刀方案的,要及时反馈给编程工程师。不能自行处理,否则可能会带来重大的加工事故。
根据CNC工艺单,在机床上建立加工坐标系,记录零件的编程旋转中心相对于机床的A轴及C轴旋转中心的偏移数值,将这些数值反馈给编程工程师。
(11)加工现场信息处理
编程工程师根据操作员的反馈信息,修改或者检查数控程序,设置后处理参数,最后进行后处理,将最终的数控NC文件及CNC工艺单正式分发给数控操作员进行加工。
(12)现场加工
操作员正式执行数控程序加工零件。作为操作员主要职责是正确装夹工件和刀具、安全运行数控程序,避免操作时出现加工事故。
操作员先要浏览数控程序,从字符文字方面检查有无不合理的机床代码;其次要适当修改程序开头的下刀指令和程序结尾的回刀指令,使刀具在开始时从安全位置缓慢接近工件,加工完成时在合理的位置提刀到安全位置。五轴联动式的提刀要确保正确。
一般情况下,应该快速运行所有的数控程序、观察主轴及旋转台运动,没有问题以后就可以正式切削零件,加工时适当调整转速和进给速度倍率开关,完成后先初步测量,没有错误就可以拆下准备下一件的加工。