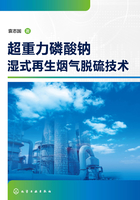
1.4 湿式烟气脱硫设备的研究进展
从上述文献来看,湿式再生烟气脱硫效率和投资的高低不仅取决于脱硫剂及其工艺,还取决于脱硫设备。因而开发传质效率高的脱硫设备、降低一次性投资,提高脱硫效率、降低运行成本也是当前烟气脱硫的研究热点之一。目前,在脱硫设备的研究方面,除了对现有吸收塔改造、内构件的结构优化等,也涌现出一些新型脱硫反应器,具有极大地优势,展现出广阔的应用前景,如旋流板塔、超重力旋转填料床等。
1.4.1 脱硫吸收塔的改进研究
湿式再生烟气脱硫系统中核心设备之一就是吸收装置和再生装置,常用的有填料塔、板式塔、喷淋空塔等传统塔,其中填料塔和板式塔通常存在阻力损失较大,操作弹性不够宽,气速受液泛限制而使设备单位体积的处理能力小、易堵,塔内液体受重力场限制,流动缓慢,分散性差、传质速率小,使投资和运行费用较大等问题;尽管喷淋空塔压降相对较小,处理气量能大一些,但要求吸收液循环量大,同样存在传质速率小,设备体积庞大等问题。尤其是针对烟气脱硫除尘过程,堵塔问题十分严重,1995年,谭天恩等发明了旋流板塔除尘脱硫一体化装置,简称旋流板塔,如图1-12所示,它是一种喷射型塔板洗涤器,关键部件为旋流塔板。

图1-12 旋流板塔结构示意图
塔板叶片如同风车叶片,气流在叶片导流作用下产生旋转和离心运动,吸收液通过中间盲板均匀分配到各叶片上,形成薄液层,在旋转向上的气流带动下产生旋转和离心运动,将液层分散成细小液滴,经旋流离心作用甩向塔壁,汇集于收集槽,经导流管进入下一层塔板的中间盲板,再次分散吸收。烟气在压力作用下从塔底部进入,穿过各层塔板,并在旋流塔板的结构部位形成大表面积的水膜,促进SO2反应吸收速率。塔板开孔率大,允许通过气速高,可以高负荷运行,且压降低,处理能力和操作弹性大。其气液接触时间较短,适合气-液快速反应吸收和直接接触传热等过程。因此,脱硫过程中所用的脱硫剂需要能够与SO2实现快速反应,不适合用碳酸钙等反应速度较慢的脱硫剂。随后,在旋流板塔的基础上,吴忠标、李立清、张志强等分别开发了大通量高效旋流板塔、喷淋旋流组合塔、冲击旋流塔、湍球塔、旋流板塔组合等脱硫装置,主要是对旋流板塔结构进行了创新、优化和组合,增加气液接触面积、简化结构、降低气相阻力,并结合相应脱硫吸收剂开发了系列的烟气脱硫除尘工艺,提高了脱硫效率,缓解了结垢堵塞现象,运行更加稳定,脱硫效率一般为70%~95%,除尘效率为90%~99.5%,全塔气相压降为1~1.3kPa。
为满足不断严格的SO2排放标准,进一步提高脱硫效率,尤其是能适应锅炉负荷波动和煤种变化等实际情况。一些环保公司结合现场施工和工程运行经验,通过在塔内增设多套具有导向和接力作用的旋流气动装置,利用烟气自身的动能产生气动旋流,使烟气在同样高度的筒体内旋转次数增加、延长通过路径,加剧气相湍动,烟气与吸收液在时间和空间上得到充分的碰撞、接触、溶解和反应吸收,使得脱硫率得到提高。另外,通过调整旋流板旋转仰角、角度和叶片尺寸来满足烟气的不同工况,提高脱硫率,降低阻力。经过多年的开发与完善,目前已成为国内湿法脱硫的主流设备,但仍存在液体循环量大,运行费用和投资高等问题。
河北工业大学的张少峰等结合旋流板、筛板的优点,借鉴立体复合式塔板的结构,开发了一种立体旋液式并流塔板,如图1-13所示,通过流体力学性能和海水脱硫实验的考察。结果表明,采用全塔并流的操作方式避免了液泛和返混等不利现象的发生,具有较好的操作弹性,在大通量、高液气比条件获得到了好的传质性能,得到了实验条件下的影响规律和适宜操作参数,其液气比在8~30L/m3之间均可正常操作,并具有良好的吸收性能,脱硫率在85%左右。

图1-13 立体旋液式并流塔板
总体来看,针对目前湿式脱硫工艺的主流吸收设备吸收塔进行大量的开发,改进、优化和完善,旨在强化传质效率和降低压降,提高设备的利用率和脱硫率,促进烟气脱硫的大规模应用。但塔中液体流动仅借助于重力或比较小的离心力实现液体的分散和烟气接触反应,由于外力场比较弱,导致传质效率的提高有限,设备体积仍然庞大,一次性投资高。为此,新型脱硫设备的开发成为烟气脱硫研究的又一热点。
1.4.2 降膜式脱硫反应器
针对传统填料塔和板式塔脱硫过程存在结垢、堵塞、出口烟气易携带液滴,引起尾部设备的腐蚀,成本高,投资大等问题,赛俊聪等结合双循环湿式脱硫及降膜式反应器的特点,提出一种横向冲刷式双循环降膜湿法新型脱硫反应器,并引入翅片管束作为降膜载体用于反应器。脱硫反应器主体包括顶部的储液槽、布液器、翅片管束、吸收塔体及底部集液槽。其脱硫过程为:在给料槽中按一定比例配好的吸收液送入顶储液槽,浆液通过布液器分配给有序排列的管束,然后在翅片管束的表面形成均匀的液膜,被烟气横向冲刷与扰动,烟气中的SO2与液膜吸收反应而被脱除。横向冲刷式双循环降膜湿法新型烟气脱硫反应器结构如图1-14所示。

图1-14 横向冲刷式双循环降膜脱硫反应器
横向冲刷的烟气在管束间交替扩张和收缩的弯曲通道里流动,在管束间产生强烈的混合和扰动,使烟气对液膜的扰动作用增强,下降液膜形成强烈的湍流状态,使烟气与下降液膜接触得更加充分,气-液传质系数得到提高,有利于吸收的完成;同时,可减缓结垢速度。但研究结果中,脱硫率不高,低于70%,有待进一步的改进优化。
李玲洁等提出了一种列管式并流降膜塔脱硫反应器,分别以NaClO2和H2O2为氧化吸收剂,考察了实验条件对脱硫效率的影响规律,获得了86%~92%的脱硫率。相比于钙基脱硫方法,该设备简单,占地面积小,维护工作量少,适合于中小型燃煤锅炉烟气脱硫。张学景等以列管式逆流降膜塔为脱硫反应器,氢氧化钠溶液为吸收剂,进行了吸收反应传质建模和模拟烟气脱硫实验研究,进口SO2浓度以及吸收液循环流量对传质速率影响的计算值与实验值的最大相对误差小于20%,脱硫率在70%以上。
总体来看,降膜式脱硫反应器允许有较高的气体负荷,能促进液膜的湍动,传质效率高,由于反应器中液体停留时间短,主要适合瞬间、快速的脱硫反应,具有不容易堵塞等特点。但相比于填料塔,有效传质面积小,脱硫率难以满足排放要求。
1.4.3 撞击流脱硫反应器
因撞击流反应器能显著强化微观混合和相间传递的特性,传质系数是传统技术的几倍到十几倍。Tamir、Matthias、李发永、Berman等在3层同轴圆筒形撞击流吸收器中研究了Ca(OH)2悬浮液吸收烟气中的SO2。与传统吸收方法相比吸收效率显著提高,但其装置和流程比较复杂,难以在工程实际中应用。伍沅等发明了一种撞击流气液反应器,并进行了模拟烟气脱硫性能实验,结构如图1-15所示。

图1-15 撞击流脱硫反应器结构示意图
撞击流气液反应器模拟烟气脱硫实验过程为:模拟烟气分两股,以相同流量通过进气管,携带由喷嘴分散成滴状的吸收剂(吸收剂也分成两股进入进气管)从进气管射出进入撞击流吸收室后在中心处相向撞击,形成高度湍动的撞击区,在其中完成吸收。吸收SO2后的分散相液体依靠重力下落,经排液管排出。在吸收室的上方设置挡板除雾,净化后的气体经排气管放空。结果表明,该吸收器具有良好的脱硫效果。为了适应处理大气量的要求,伍沅等设计了多功能组合撞击流气液反应器。在此基础上,李勤等以Ca(OH)2浆液为吸收剂进行脱硫实验,在液气比为0.84L/m3、进口烟气中SO2浓度为3200mg/m3、烟气流速为7m/s、雾化压力为1.0MPa、钙硫比为1.4时,吸收剂利用率为55%~64%,脱硫效率为92%~94%,总体积传质系数达0.5~11/s,高于一般的反应器,证明其优良的传质性能。然后以稀氨水为吸收剂进行脱硫实验,液气比为0.52L/m3,SO2入口浓度为2800mg/m3,氨水浓度为2%时,脱硫效率达96%左右。
可见,撞击流技术在烟气脱硫方面具有体积传质系数高、所需设备体积小、流体阻力小等优势,适用于碱液脱硫的快速不可逆的化学吸收过程,为满足现行排放标准其脱硫率还需要进一步提高。
1.4.4 超重力脱硫反应器
在化学工程领域,以小的设备体积、少的资源及能量消耗获得更高的传递效果为目标的过程强化是化工界不断追求的目标。超重力技术是近年来新发展的强化相间传质、反应及混合的新型技术,在过程强化方面效果突出。自20世纪70年代诞生以来,得到了迅速发展。目前,已在气体净化、废水处理、纳米材料合成、有机合成等方面得到初步应用,投资省,节能降耗效果显著,具有广阔的应用前景。
(1)超重力的基本原理及其特点
超重力是指物质在比地球重力大得多的环境下,所受到的力(包括离心力、引力或排斥力),超重力场即是任一瞬间物质在旋转体内各点所受的离心力分布总和。在地球上,获得超重力最简便有效的方法就是通过高速旋转产生的离心力来实现,其强度取决于旋转体的转速和直径大小。通常,用于化工过程强化的超重力是通过填料层的高速旋转来实现,这种装置称为超重力装置或超重机(High Gravity Rotary Device,Higee),也称为旋转填料床(Rotating Packed Bed,RPB)或旋转填充床、旋转床,其典型结构如图1-16所示。

图1-16 旋转填料床结构示意图(气液吸收过程)
1,6—密封;2—转子;3—填料;4—壳体;5—液体分布器;7—轴
旋转填料床由壳体、轴、转子、填料、液体分布器和密封装置等组成。电动机带动转子及其填料高速旋转,液体由转子中央的液体分布器分布后,均匀喷洒在填料的内缘进入填料层,在离心力作用下,沿径向由内向外流动,最后以切线方向离开转子被甩到壳体内壁收集,汇集于底部经液体出口流出。对于气-液逆流接触方式的旋转填料床,气体在压力作用下,进入旋转填料床的外腔分布后,由转子的外缘穿过填料向内缘运动,与液体在填料中逆流接触,到达转子内缘后,经中心的气体出口排出。气、液在此过程中与填料多次碰撞、分散与聚并,液体以微米甚至纳米级的液膜、液丝和液滴等形态存在,形成极大的且快速更新的相界面,从而强化了气液间的混合、传质与反应过程。传质系数比塔设备提高1~3个数量级,单位设备体积的生产能力提高1~2个数量级。因此,旋转填料床又称为“化学工业的晶体管”。
与常规传质设备相比,具有如下一些特点:
①强化传质效果显著,传递系数提高了1~3个数量级;
②微观混合均匀,时间极短;
③对于气液接触过程,气相压降小,能耗少;
④填料持液量小;
⑤物料停留时间短(0.1~1s),特别适用于一些竞争性化学反应过程;
⑥开、停车方便,且达到稳定时间短;
⑦设备体积小,占地面积和投资省,安装维修方便;
⑧填料层具有自清洗作用,不易结垢、堵塞。
(2)超重力烟气脱硫研究进展
旋转填料床作为一种新型高效传质反应器,用于强化SO2的吸收过程已成为研究热点。陈昭琼等将螺旋型旋转吸收器应用于烟气脱硫,在模拟烟气平均气速0.16m/s,SO2进口浓度3000mg/m3,液气比10~16L/m3,转速500~1300r/min的条件下,用清水作吸收剂,脱硫率达70%~80%,用含催化剂Mn2+的水溶液作吸收剂,脱硫率达90%~95%;且脱硫率随液气比和转速的增加而升高,转速的影响最为显著。同时采用CO2-NaOH体系测定了该吸收器的比相界面积、液相传质系数和液膜厚度随操作参数的变化规律,在实验条件下,比相界面积为5~11cm2/cm3,是B-25型旋流塔板的20倍,液相传质系数约为0.08cm/s,且均随转速的增加而增大,液膜厚度约为0.1~0.25mm,结果表明,螺旋型旋转吸收器具有气液接触时间长、液膜厚度比重力下薄,传质效果好、不易堵塞等优点。
柳来栓等以Mg(OH)2、Ca(OH)2、H2O为吸收剂,以逆流旋转填充床为吸收设备,进行了模拟烟气脱硫实验,在空床平均气速为0.35m/s,气液反应时间为0.21s的条件下,着重考察了吸收液流量、吸收剂浓度、进气SO2浓度和旋转床转速对3种吸收剂的传质速率影响。结果表明,3种吸收剂吸收SO2的传质速率随旋转床转速、液体流量和进气SO2浓度的增大而升高,其中碱性悬浮液的传质速率是纯水的3~4倍;在超重力场下,Ca(OH)2悬浮液吸收SO2的过程仍受液膜传质阻力影响,并非完全气膜控制,适宜质量浓度为0.05%,Ca/S比为1.68时,脱硫率达92%。
潘朝群等以多级雾化超重力旋转床作为NaOH-Ca(OH)2双碱法烟气脱硫工艺中的吸收设备,在平均空床气速为2.06m/s,气液反应时间为0.19s的条件下,进行了模拟烟气脱硫实验。结果表明,脱硫率随再生液的pH值、液气比的升高而增大,随进气SO2浓度的升高而降低,在适宜工艺条件pH=12.6~13,液气比1.9~2.2L/m3下,进气SO2浓度6350mg/m3的脱硫率达60%~85%,这很难满足目前的排放标准。
王永刚等以逆流旋转填充床为吸收设备,NaOH溶液为吸收液,在平均空床气速为0.53m/s,气液反应时间为0.13s的条件下,进行了模拟烟气中SO2的脱除实验研究。结果表明:脱硫率和气相总体积传质系数KGa随液气比和NaOH浓度的增加而增大;随旋转床转速的增大,先减小后增大,随进气中SO2浓度的增加而减小;在适宜工艺条件:进气中SO2质量浓度小于5g/m3,吸收液浓度为0.1mol/L,转速为1200~1600r/min,液气比为3~4L/m3,脱硫率达99%以上,KGa>0.211/s。
师彬等分别以乙醇胺和乙二胺/磷酸缓冲溶液为吸收剂,在逆流旋转填充床中对模拟工业废气中的SO2进行了脱除实验研究。结果表明,脱硫率随液气比、吸收剂温度和浓度的增加而升高,随平均空床气速的增加而降低,随旋转床转速的增加先升高后降低;乙醇胺为吸收剂的适宜条件:平均空床气速为0.15m/s,气液反应时间为0.16s,液气比为1.25L/m3,旋转床转速为700r/min,吸收剂温度为45℃和乙醇胺质量浓度7%,当进气中SO2体积浓度为3%时,出口气体中的SO2浓度为750mg/m3;乙二胺/磷酸缓冲溶液为吸收剂的适宜条件:平均空床气速为0.10m/s,气液反应时间为0.26s,液气比为2L/m3,旋转床转速为700r/min,吸收剂温度为35~55℃、pH=7和乙二胺浓度为0.3mol/L,当进气中SO2体积浓度为1.5%时,脱硫率达92%~95%;单级还达不到现有的排放标准。
王俊等以并流旋转填料床为脱硫设备,分别以亚硫酸钠、氢氧化钠和碳酸钠为吸收剂,在平均空床气速为1.62m/s,气液反应时间为0.07s的条件下进行了模拟烟气脱硫实验研究。结果表明,脱硫率和气相总体积传质系数KGa随钠离子浓度、旋转床转速和液气比的升高而增大,随NaOH在液相中的比例增加而增加,随进气中SO2浓度的增加而减小;在相同操作条件下,碳酸钠溶液的脱硫效果比亚硫酸钠好,碳化硅整形填料的脱硫效果好于不锈钢丝网填料,但前者的制作过程繁琐、工艺复杂、韧性有所欠缺;在进气SO2浓度为3420~3580mg/m3,吸收液中Na+浓度为0.25mol/L,液气比为0.88L/m3,超重力因子为100的条件下,脱硫效率高达91.5%(出口气体中SO2浓度约为300mg/m3),还需要进一步脱除。
姜秀平等以逆流旋转填料床为吸收设备,柠檬酸钠缓冲溶液为吸收剂,在平均空床气速为0.07m/s,气液反应时间为0.50s的条件下进行了模拟烟气脱硫实验研究。结果表明,脱硫率和气相总体积传质系数KGa随超重力因子、液气比、吸收液中柠檬酸浓度和pH值的增加而增大,随进气中SO2浓度的增加而减小;在适宜工艺条件:柠檬酸浓度为1mol/L、初始pH值为4.5左右,超重力因子为54~90,液气比为3~7L/m3下,进气SO2浓度为4500mg/m3时的脱硫效率达98%左右,出口SO2浓度可降至100mg/m3,KGa达1.4~21/s。穆文菲等以上述相同的设备和吸收剂,在平均空床气速为0.24m/s,气液反应时间为0.15s,进气中SO2浓度为8571mg/m3的条件下,进行了模拟烟气脱硫实验研究。结果表明,在超重力因子为54~90,柠檬酸浓度为1.5mol/L,初始pH值为5.0,液气比为7L/m3的适宜工艺条件下,脱硫率稳定在99%左右。表明旋转填料床具有适应烟气SO2浓度变化范围宽,脱硫率高。
综合超重力烟气脱硫研究文献,不难发现:旋转填料床的平均空床气速为0.07~2.06m/s,气液反应时间为0.07~0.54s,液气比为0.5~7L/m3,其中,潘朝群等研究的多级雾化超重力旋转床的平均空床气速最高为2.06m/s,其次是王俊研究的并流旋转填料床平均空床气速1.62m/s,两者在适宜条件下的脱硫率最高达85%和91.5%,显然难于满足现有的排放标准,其他研究的平均空床气速为0.07~0.51m/s,脱硫率能够满足现有的排放标准。对比现在常用的喷淋空塔气速为3~4.5m/s,液气比为13~16L/m3,气液反应时间为2~5s来看,旋转填料床的反应时间大大缩短,液气比更小,强化脱硫效果显著,设备体积大大地缩小,可节省投资和空间,但气速偏低,需要进一步研究较高气速下的工艺条件及其设备结构对脱硫率和传质系数的影响,以充分发挥旋转填料的优势。
1.4.5 结论
我国是以煤为主要能源消费的国家,近十年来,SO2排放量一直位居世界首位,也是我国大气主要污染物之一,并以酸雨、雾霾等多种形式对生态环境造成了严重破坏,特别是近几年,出现长时间雾霾天气的频率越来越高,对国民经济和人民生活造成了极大的负面影响,因而继续增加烟气脱硫投入、提高脱硫效率,严格执行烟气排放新标准势在必行,特别是中小型锅炉的烟气排放。而目前我国烟气脱硫使用最多的是比较成熟的湿式石灰/石灰石-石膏法和循环流化床半干法烟气脱硫技术,它很难经济地达到新排放标准,且随着烟气脱硫设备运行数量不断增加和规模不断扩大,脱硫副产物石膏的处理问题变得日益突出;而另一方面,我国硫资源相对缺乏。所以,湿式再生烟气脱硫技术将成为新一轮技术发展的主流方向,是适合我国国情的脱硫技术,既可实现烟气中SO2的资源化治理,缓解我国大量进口硫黄的现状,又能产生良好的经济效益,以抵消脱硫装置的部分运行费用,达到治理环境和发展经济的双赢目的,对于环保和国家经济建设意义重大。
目前湿式再生脱硫工艺中的脱硫剂以磷酸钠盐最具有应用潜力,相对其他可再生的脱硫剂具有更稳定的物理化学性质,不降解变质、不挥发、损失小,且为常规的化工原料(钠碱和磷酸)、廉价易得,硫容量大,脱硫反应快,效率高等优势。但关于该工艺的脱硫机理研究较少,缺乏对工艺的优化和创新,导致与其他湿式可再生烟气脱硫工艺一样,主要采用塔设备作为吸收和再生装置,存在再生能耗高、系统复杂、工艺长、投资大、亚硫酸的氧化等缺点而未被广泛应用。因而,有必要对其脱硫机理进行深入研究,寻求高效率的传质、传热设备、创新工艺,降低氧化,以进一步降低成本,对促进湿式磷酸钠盐脱硫以及再生烟气脱硫技术的发展和应用具有重要的理论价值和现实意义。
因目前湿式脱硫工艺中主要采用塔设备,具有处理量大、技术成熟等优势,但存在传质系数低,设备体积庞大,投资运行成本高等问题,虽开发出了旋流板塔对其脱硫效率有所提高,但增加幅度不大,效果不突出,还难以达到由于排放标准日益严苛而进行的深度脱硫工艺改造升级的要求。而旋转填料床能够极大地强化气-液间的传质,且具有物料停留时间短等特点,如将其用于磷酸钠缓冲溶液烟气脱硫的吸收和解吸工艺中,一方面可极大地强化SO2的吸收和解吸过程的传质,提高吸收和解吸速率,缩小设备体积,降低液气比及费用;另一方面,可大幅度缩短吸收阶段脱硫液与烟气中氧气的接触时间,降低亚硫酸盐的氧化速率、副盐的生成和吸收剂的消耗,提高SO2的回收率。因此,针对上述情况,提出旋转填料床-磷酸钠湿式再生烟气脱硫工艺,并采用了θ环高效填料作为旋转填料床的填料,进行了工艺及其工艺参数对脱硫率、解吸再生率的影响规律研究,拟探索出一种低成本、高效率的资源化烟气脱硫工艺及其装置,这将对节能减排工作产生深远地影响,具有重大的环境经济价值。