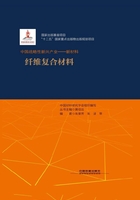
1.3 纤维增强复合材料的特点
1.3.1 复合材料的物理机械性能特征
由前面对定义的讨论可知,从组成上看纤维增强复合材料的最大特点就是含有增强纤维,尤其是长纤维,而纤维的承载方向无疑是轴向方向,在径向则主要靠远低于纤维强度的基体材料的内聚强度,这自然就导致了纤维增强复合材料的最大特点,也是与其他材料(如金属、塑料或粒子复合材料)之间的最大差别,即它们机械力学性能的各向异性(anisotropy)。
各向同性(isotropy)是指物质的性质在每个几何方向都相同。对于各向同性的物质,任何位置的取样和任何方向的测试结果都一样,都可以用来代表该物质的性质。对于各向异性材料则完全相反。以一块连续纤维复合材料层板为例,经向(也称为Warp方向、X方向或0°方向)同纬向(也称为Fill方向、Y方向或90°方向),以及同厚度方向(也称为高度方向或Z方向)的性质通常是不一样的,如图1-2所示。

图1-2 (0/90)非平衡平纹织物铺层的复合材料层板各个方向和抗拉强度示意图
由于先进复合材料中使用最广泛、种类最多、用量最大的是树脂基纤维增强复合材料,它们也常常被用来升级、替代较重的金属材料,另一方面金属材料是目前航空航天和高端工业使用最广泛的承载结构材料,因此以下的讨论着重在这类各向异性的复合材料和各向同性的典型金属材料的比较。同时由于后续章节对复合材料的各种力学性能有详尽的讨论,本节只做简单的介绍。除非特殊注明,本节所指复合材料的性能是指其0°方向性能。
纤维增强复合材料的力学性能基本上都是围绕着其各向异性而展开,即它们的性能基本上都源于其各向异性的结构,而其他物理性质主要取决于基体树脂和纤维-基体界面性质。表1-2所示为金属复合材料物理、机械力学性能的对比。
表1-2 金属和复合材料物理、机械力学性能的对比

纤维增强复合材料各向异性的特点对于材料设计和加工带来的优劣因人而异。对于习惯于金属设计的人来讲,显然复合材料设计起来更麻烦,尤其当载荷形式难以固定或多种形式的载荷可能作用于同一零部件时。但是,对于那些熟悉复合材料并精于优化设计的人,复合材料显然提供了更多,甚至近于无限的设计可能性,因为增强体和基体的组合基数本来就是巨大的,加上组合的形式、规格、参数等可控变量,无疑使得一切设计皆变为可能。另一方面,与各向异性共生的二维形态赋予了复合材料极其灵活的制造方法,在X、Y、Z方向都可以进行特殊设计,由此赋予零部件特定的各向异性。通过二维材料实现三维体制造的方式也使得内置部件和零部件整合变得容易多了。正是由于这种极其方便的可造性(tailorability),使得许多使用金属难以实现的复杂和复合的优化设计可以通过使用复合材料而得以实现,这在后面的章节中会有充分体现。
从机械力学上,众所周知,与金属材料相比,复合材料的最大优势是轻而强,也就是说,复合材料有更高的比强度和比模量。比强度和比模量由拉伸强度和拉伸模量除以密度得到,见表1-3。通常用来进行复合材料和金属比较的是比拉伸强度和比拉伸模量。需要指出的是,一般在比较各种复合材料同金属的拉伸性能时,都习惯性地使用增强纤维本身的强度,但是毕竟是复合材料,而不是纤维,才是材料最终的使用形态。因此笔者认为相对合理的比较应该是将复合材料中实际的纤维含量考虑进去,或者直接使用具体的复合材料的拉伸数据,尤其是当采用0/90的织物或准各向同性(quasi isotropic)的复合材料时更应该如此,见表1-3的最后三行数据。
表1-3 复合材料和金属材料的比抗拉强度和比拉伸模量

注:表中纤维及其复合材料的拉伸数据为轴向(0°)拉伸数据;复合材料数据为典型值。
从表1-3中的比强度和比模量数据可以看出,参与比较的三种金属材料的比强度和比模量(也就是比刚度)相当,而金属基的硼纤维铝复合材料则明显高于它们,因此如果采用这种复合材料代替这三种金属材料将具有减重效果。玻璃纤维是一个分界线,从比模量来看,使用玻璃纤维增强复合材料与金属材料相比并没有优势,但强度略好于金属,由此可见,玻璃纤维增强复合材料在航空航天上减重效果有限。这类材料仍然得到广泛使用的主要原因是因为它们的其他特性,如加工性、雷达波透明性、耐腐蚀性、成本等。从表1-3中看出,芳纶复合材料具有相当不错的比强度和比刚度,从理论上讲是良好的减重材料,但是由于它们的吸水性高(可达7%)、压缩强度低,实际上它们作为结构材料的使用程度有限,而主要是用于航空器内部部件(因为它们的高阻燃性)或防弹器械(因为它们的高韧性)。反观碳纤维的数据,则显现出很好的综合性能,其比强度和比刚度都大大高于金属材料,加上它们不错的压缩强度、极低的热膨胀系数和吸水率、高的热稳定性,以及与所有的基体(聚合物、碳、金属和陶瓷)优良的复合性和加工性,再加上可控的、稳定的制造工艺和不算离谱的价格,当仁不让地成为先进复合材料,尤其是航空航天用先进复合材料的主力军。
前面已经提到过,复合材料的综合性能是由增强体、基体和它们的界面决定的。一般来说,增强体主导了复合材料的拉伸、抗弯强度和模量,而基体决定了复合材料的使用温度、环境耐候性和耐溶剂性。那些由增强体和基体共同决定的性能,如压缩、抗剪强度和模量、损伤容限、耐湿热性等,多半也是由基体性能主导,由界面性能决定的。界面性能对复合材料性能有巨大贡献和作用,界面的存在是复合材料的固有属性,但不是所有从事复合材料行业的人都对界面都有充分的认识。虽然在选择增强体和基体时,客观上也在选择界面,但是只有对界面有意识地进行匹配和优化,才能真正达到对复合材料使用的优化。例如,如果使用纤维的直径为7mm,体积分数为60%的复合材料制成1mm厚的层板,那么1m2的层板中含有的界面面积约为350m2,这是一个不可忽视的因素,甚至对材料的物化力学性能有决定性的作用。使用偶联剂来增强玻璃纤维同基体的黏合从而提高其复合材料的多种强度是通过界面改性提高材料性能的经典例子。
1.3.2 复合材料的应用局限与改进方向
毋庸置疑,与典型金属材料相比,先进复合材料也有其不足之处。首先是其厚度方向(Z方向)强度不足,虽然这个缺点可以有限地通过使用二点五维或三维增强体改善,但是由于这种方法不能完全避免纤维的弯折,无法达到X、Y方向可能达到的强度。尽管如此,这仍是目前最有效的方法,即使用三维编织的纤维预成型体通过液体树脂或树脂膜成型。但是,三维编织纤维预成型体价格昂贵,而且难以编织大型零部件,应用的广泛程度受到很大限制。复合材料另一个比较明显的缺陷是它们比金属材料低的损伤容限以及对内部损伤探测困难。低损伤容限的弱点对热固性聚合物基复合材料尤为明显,好在通过各种增韧手段以及对增强体及其表面的改性,或者使用二到三维的纤维预成型体,都能大大改善材料的损伤容限。另一方面,复合材料的损伤(不是破坏)常常表现在层间分离,这种损伤在材料受到低速冲击时,如掉落的工具或冰雹等,尤为典型。在这种情况下,尽管材料的表面往往没有任何凹陷或破坏,但内部可能已经产生分离或分层,造成事故隐患。虽然无损检测(non-destructive inspection,NDI)方法如超声波C扫描等日益先进和普及,但毕竟价格不菲,操作也颇为复杂,因此复合材料,尤其是热固性复合材料的增韧一直是领域内一个非常重要的研究方向。热塑性复合材料损伤容限高,而且可以像金属那样进行焊接,因此在这方面有特别的功用,不过它们的加工难度和其他不足使得它们无法完全取代热固性复合材料。此外,含有碳纤维的复合材料与金属接触情况下的电化学腐蚀也是需要注意的。其他方面如复合材料的高成本和回收重复利用难度等,此处不一一讨论。
需要说明的是,有些复合材料的性能是逐步得到认识和认可的,例如在波音787的研制过程中,曾有相当多的批评声音和质疑,认为如果飞机紧急迫降或摔机着陆时,复合材料机身会破裂、燃烧并释放出有毒气体,后来波音公司在FAA(美国联邦航空管理局)的监督下做了实地测试,大量的数据表明复合材料机身在这些情况下,并不比金属机身会更加危险或释放出更多的有毒气体。
总之,复合材料各向异性的特质使得它们在设计上和使用上都需要进行与各向同性的金属材料完全不同的考量,必须对它们物理和力学性能的方向性有充分的认识,才能达到对复合材料的最佳设计和利用。