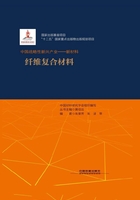
1.4 纤维增强复合材料的应用
在50多年的时间里,纤维增强复合材料从无到有,它们的应用深度和广度是许多结构和非结构材料难以比拟的,而最关键的应用领域,无疑是充分利用了这类材料最显著的特点:轻而强。在以下的简单介绍中,最多的应用是与运载工具的轻量化有关的,另外也有不少是利用其他特质,如碳纤维增强复合材料的低热膨胀率或者芳纶纤维增强复合材料的防弹性等。无论在哪个应用领域,复合材料都在以超常规的速度扩展,充分显示了它们的巨大作用和发展潜力。
1.4.1 航空应用
航空器通常又进一步划分固定翼(fixed wing)和旋转翼(rotocraft)两大类,固定翼里有大型商用飞机、区域喷气机、商务机和固定翼军用飞机等,旋转翼里也有民用和军用两大类。航空发动机/发动机也是该领域的一个重要部分。
在航空领域使用的先进复合材料较其他领域而言,无论是质或者量都一直处于领先地位,这固然是和航空领域能承受这些材料的较高价格有关,但更重要的是复合材料能给航空器带来它非常需要的减重效果。例如,按2013年的平均油价标准,飞机每减重1kg每年可以节省相当可观的燃料费用,见表1-4。
s 表1-4 2013年飞机减重1kg可省燃料费用

(来源:composites Forecasts& Consulting LLC)
如前节所述,虽然玻璃纤维增强的复合材料从1942年的XBT-16就开始用在飞机零部件制造上,但是由于玻璃纤维取代铝合金的减重效果较小,当时的应用主要是出于抗腐蚀或部件整合等,基本上是探索性质的使用。直到碳纤维复合材料的出现和复合材料性能的大幅提高,也就是进入先进复合材料阶段,一些重要的次承力结构(secondary structure)才开始使用复合材料。随后的发展一路攀升,先到次承力结构再到主承力结构(primary structure),先军机后民机,先小型机后大型机,直到今天以波音787和空客A350XWB为代表的大型复合材料飞机的问世和进入商业服务,显示了复合材料在航空领域的广阔前景。表1-5列出了一些代表性服务年代,以期展示这样一个发展轨迹。
表1-5 复合材料在飞机上的应用历史简表

续表

需要指出的是,美国宇航局(NASA)在促进先进复合材料在大型民用飞机上的应用功不可没。20世纪70年代,NASA曾通过“飞机节能计划”拨款6000多万美元帮助一些飞机制造商进行复合材料的设计、制造和测试,直接促成了复合材料在洛克希德、波音和道格拉斯等公司大型客机的主承力件上的使用[13]。
使用先进复合材料不仅实现了有效减重,而且大大减少了制造复杂性,例如空客A310的垂直尾翼,这个高8.3m、宽7.8m的大型件如果用铝合金材料制造需要2000多个零部件,采用碳纤维增强环氧复合材料后只需要不到100个零部件,堪称设计和制造的杰作。
在讨论复合材料用于航空领域时,一般都着重在国家或大公司主导的军用飞机和商用飞机,但是在欧美有一类自制飞机,他们多半由业余航空发烧友设计制造,然后申请航管部门的飞行许可。其实早期的飞行先驱,无论是李林塔尔(Otto Lilienthal)还是莱特兄弟(The Wright Brothers)都是这样开始的。一百多年来数不清的航空爱好者都希望利用当时最可靠、最便宜、最易加工的材料来制作飞机,而复合材料的出现和发展,给他们提供了前所未有的方便,许多设计都别具一格,数量也相当可观。另一类则将主要零部件成套出售,供发烧友自己装配,这些小型飞机的机身机翼常常是大块或整块复合材料制成,其中最有名的有兰克(Lancair)、卷云(Cirrus VK-30)和欧罗巴(Europa XS)等。
航空发动机是航空工业的重中之重,传统上是金属材料一统天下,但是近20年来,先进复合材料在这个领域从无到有,迄今已经占据了相当重要的位置,有人甚至将复合材料称为未来航空发动机的突破口。从用量来看,金属基复合材料在发动机上用量最大,陶瓷基其次,然后是树脂基。目前树脂基,尤其是双马酰亚胺基的复合材料已经成功用在最新一代的大型喷气发动机风扇整流罩(Fan Cowls)和叶片上。例如,在2016年实现量产的罗-罗公司Trent 7000发动机舱中的整流罩(见图1-3)就是由奥地利FACCAG公司(现属中航工业)采用全碳纤维复合材料制成,这款发动机安装在空客330neo飞机上。
金属基复合材料在航空发动机上使用时间较长,如涡轮叶扇、机匣、转子等,主要还是改善原有金属材料的性能。陶瓷基复合材料近年来发展很快,已经成功使用在最新的发动机排气喷管上。图1-4所示为由波音公司制造的迄今最大陶瓷基复合材料大型航空发动机尾气喷管,该喷管已经成功地安装在罗-罗公司最新Trent1000发动机上(见图1-5),通过波音787的搭载试验证明,使用这种氧化铝陶瓷基复合材料,不仅实现了减重,同时显著地减少了噪声。该发动机第二级“热区”的转动部件也将使用陶瓷基复合材料,因为陶瓷基复合材料的耐高温性,不再需要额外引入空气来冷却这些部件,加上取代金属而得到的减重效果,使得燃料效率得到有效提高。庞巴迪、巴西航空工业、西锐、赛斯纳、钻石、本田、三菱等商用机、通用机和商务机制造商的新一代喷气机所用发动机,也大多使用了复合材料叶片和发动机罩,以及数量不等的陶瓷和金属基复合材料零部件,在此不再一一详述。

图1-3 罗-罗公司Trent7000发动机复合材料整流罩

图1-4 波音公司陶瓷基复合材料大型航空发动机尾气喷管

图1-5 安装了波音陶瓷基复合材料航空尾气喷管的罗-罗Trent1000发动机
用于飞机内部的复合材料对现代飞机的减重和运行贡献也非常大,但在文献中常常没有占据应有的篇幅,因为尽管这些复合材料大多是次承力结构或者是装饰性质,它们却占据了约飞机总重量的40%。而用于内部的复合材料的使用量也大大超过主承力结构的用量,只不过这些内部用复合材料只有部分使用了高性能纤维,而主承力结构则全部采用先进复合材料,尤其是碳纤维复合材料。
但是,先进复合材料用于航空领域的未来之星非无人机(UAV)莫属。无人机,尤其是军用无人机,在近年来发展极其迅速,而且在实战中成绩斐然。无论是美国中东军事行动中脱颖而出的固定翼捕食者(Predator)和全球鹰(Global Hawk),还是威力强大的旋转翼火力侦察兵(MQ-8),以及可以乱真的蜂鸟(Humming Bird)和其他数以百计的各类型号的军用、警用和民用的无人机,无一不是先进复合材料的用武之地。可以肯定地说,没有轻、强而且加工灵活的先进复合材料,无人机的发展无法达到现有的水平。未来的天空,将充斥着无数的无人机,而未来的空战,也很可能是由无人机来担任主角。按照美国空军的说法,F-35/JSF联合攻击机将是美军最后一款战斗机,当15年或20年后最后一架F-35下线之时,美军应该可以开始装备速度和性能都将比它们更优良的无人战斗机。
1.4.2 航天应用
航天飞行器和运载火箭对重量的敏感度更胜于航空器,一般来讲每千克的载荷大约需要500kg的火箭燃料,因此达成每一克减重效果的方案都是值得一试的。在人类征服太空的历程中,先进复合材料屡建奇功,现在已经成为这一领域重要的主体结构材料。
航天首要的是解决运载工具的问题,而运载工具不可或缺的是燃料。一般来讲,运载火箭自重(不包括燃料)的60%来自于燃料罐和氧化剂罐,传统的制罐材料是铝合金,如果换为碳纤维复合材料,可以减重30%,这样可以大大增加有效载荷,或者在同样载荷下减少一个推进发动机或一个助推火箭,意义重大。所以,近年来美国致力于发展这项技术,2012年NASA和波音的工程师采用美国氰特公司的新型非热压罐碳纤维复合材料,成功地设计制造了直径为5.5m的低温燃料罐(cryotank),这是迄今为止最大的火箭推进剂罐,如图1-6所示。值得一提的是,与DeltaⅣ-LH2铝合金罐相比,他们不仅实现了减重43%的目标,而且通过这种新方法减少制造成本25%(约800万美元)。目前,他们正在努力实现10m直径的新目标。
运载火箭的主要任务是将设备或人员送上太空轨道或其他星体,如月球和火星等。其中,卫星是目前最主要的太空设备,在各种卫星中,为了实现减重的目标,几乎没有不使用先进复合材料的地方。例如,载有太阳能设备的卫星或空间探测器,其太阳翼框架几乎都是采用碳纤维复合材料制造。国际空间站(international space station)是另一个应用先进复合材料的典范。在这个庞大的太空设备中,除了支撑8对共3000m2太阳翼的框架外,空间站几乎所有的桁架结构和压力容器都是碳纤维复合材料。中国的天宫一号空间站也充分利用了先进复合材料,它的许多结构件,包括推进舱、光学仪器安装台等,都有碳纤维复合材料的身影。

图1-6 NASA和波音联合研制的VBO复合材料燃料罐
复合材料的功能常常是多方面的,这在太空应用中尤其明显,值得一提的是哈勃望远镜。这台功勋卓著的太空望远镜,其最精密的光学设备舱就是采用碳纤维-环氧树脂复合材料制成,除了利用其减重的效果,还利用了碳纤维复合材料在经向的热膨胀系数几乎为零的特点,确保光学部件在太空的巨大温差条件下保持完美的聚焦精度。而美国的航天飞机(也称太空梭,space shuttle)外部隔热板采用碳/碳复合材料,则是利用其优良的导热性和耐烧蚀性。
近年来,美国和西方国家的民间太空计划在政府的鼓励下发展势头良好,未来的近地太空任务将逐步由民间公司和机构来完成,而政府机构,如美国NASA的主要任务将转向更高级的层次(如登月)或外太空探索(如火星探索和登陆计划)。位于美国加州的太空X公司(Space X)就是在这种背景下由传奇人物Elon Musk在2002年建立的,该公司2012年成功使用它的猎鹰(Falcon)火箭将他们的龙飞船(Dragon X)和一批重达400kg的设备送到了国际空间站,成为第一个到达国际空间站的私人飞行器。该公司已经同NASA签订了价值16亿美元的合同,在航天飞机退役之后承担在2013—2017年向国际空间站运送人员物资的13次飞行任务。该公司还计划在未来20年实现地球到火星的商业旅游。可以预见,这些进展以及雄心勃勃的计划,将会是先进复合材料技术得到进一步提升的新的契机。美国太空飞机(spaceplane)是另一个很好的例子,以2003年首飞的太空飞船一号(Spaceship One)为代表,它可以视为航天飞机的升级简化版,采用母机投放与火箭推进器结合,这种太空飞机从结构上几乎全部由先进复合材料制成,其发射和运行比航天飞机便宜很多,它后续的太空飞船二号(Spaceship Two)也是如此。本来计划在2015年春通过太空飞船二号实现首次商业化载人太空旅行,但是2014年10月31日,太空飞船二号在进行飞船释放试飞中,与母机分离不久就发生了爆炸,坠毁在美国加州的莫哈维沙漠,两名太空飞行员一死一伤,爆炸原因是飞行员在没有达到既定马赫数时提前解锁了飞船的活动“羽毛”尾翼。这个变故虽然会推迟原定的载人太空旅行时间,但飞船的拥有者维京星际公司表示第二艘太空飞船二号样机的制造已经完成了80%,很快就能继续完成飞行测试任务。图1-7所示为太空飞船二号及其投放母机。

图1-7 太空飞船二号及其投放母机
作为美国新一代载人航天器的猎户座飞船(Orion)不仅是美国新登月计划的运载工具,也将是近地轨道之外的外太空探索计划的主力飞船。根据NASA的资料,其先进性标志之一就是在其设计制造中大量使用先进复合材料,例如各种功能舱的结构件(composite structures)和复合材料隔热层,如图1-8所示。
在外太空(deep space)的各种无人探测器上,都有大量的先进复合材料。最新一代的火星探测器好奇号(Mars Curiosity Rover)上,除了传统的复合材料结构件和光学基座外,其太阳能板框和隔热防护层也是碳复合材料。

图1-8 猎户座飞船复合材料隔热层
航天用途的先进复合材料还会继续主导新型复合材料的探索发展,2013年NASA牵头成立了一个由美国六大航空航天企业(贝尔直升机、GE航空、洛马公司、洛索普格鲁曼、波音和普惠发动机)的先进复合材料研究联盟(Advanced Composite Research Part-nership),旨在加速复合材料的研发、认证和使用,并使其能在航空和其他高端工业领域推广。
1.4.3 其他军事应用
先进复合材料因其优异的性能和初期高昂的价格,基本上都是先在军事用途上得到使用和推广,然后逐步向其他领域和民用扩展。除了前面讲到的航天和军机,复合材料在其他军事领域应用也非常广泛。一般来讲可以大体分为陆地结构、海洋结构、人身防护、车辆防护和武器等几大用途。
复合材料用于陆地结构由来已久,主要利用其轻强并易于搭建的特性。比较值得一提的是,对爆炸物损失具有特殊防护功能的复合材料在反恐战争中起到了作用,为了使得新的战时建筑物具有很强的防护能力,或者需要对原有的墙体或掩体进行方便有效的加固,美国军队使用了一种特殊编织的芳纶网,用酚基树脂和其他树脂通过手糊方式粘贴在墙体上,固化后的复合材料保护层极其坚固,在外部爆炸物的攻击下能有效保护内部人员。
先进复合材料是现代海军的利器,有的用途甚至是使用其他结构材料无法替代的,例如潜艇的耳朵——声呐系统。声呐系统一般位于潜艇的鼻端,声呐舱外部是艇身的一部分,因此既要能够承受深海高压,又要对声呐信号有高透明度。能够满足这种要求的材料很少,而高强玻璃纤维增强的环氧树脂复合材料则能完美胜任。现代军舰的上层结构、隐形舰艇的主体结构也都大量使用先进复合材料。先进复合材料还能帮助军事舰艇工程师实现一些独特的设计,例如美国海军最新型的登陆快艇(advanced combatant craft),船体采用了新型碳纤维共固化三明治结构,并且不与甲板直接连接,这样既减轻了重量又加强了行驶稳定性。美国海军耗资40亿美元建造的新型驱逐舰(Zumwalt-class,见图1-9)堪称应用先进复合材料的典范。这种驱逐舰为钢质船体,但是它的甲板上部是一个全部采用复合材料制成的“超级结构”甲板室(见图1-10),该结构的墙体由巴萨木与T700碳纤维聚酯复合三明治层板制成,室顶由玻纤加碳纤维与防火酚基树脂层板制成,这种超级结构大大减轻了该舰的上层重量,提高了稳定性和行驶精度,同时也提高了其雷达隐身性,是未来战舰的发展方向。

图1-9 美国新型驱逐舰
雷达和卫星是现代军人的眼睛,雷达卫星天线罩是整个监控系统重要的部分,其结构材料最初是钢,后来发展为更轻的铝合金,但是大功率高灵敏度的雷达不仅面积大,而且要求转向精准,背面的支撑结果具有高的刚度和稳定性,反射面近乎镜面等,采用金属材料不仅加工困难,而且造价高昂,因此碳纤维复合材料被广泛用于制造各种类型的雷达罩,特别是大型雷达罩。一般来讲,这些雷达罩的弧形面由多块碳纤维三明治结构拼制而成,背面支撑由碳纤维实心层件制成。

图1-10 朱级驱逐舰复合材料甲板室
防弹是军事材料所需要的一种重要功能,传统的防弹材料是钢,效果好,但是不堪重负。复合材料是迄今能够全部或部分替代钢材的优良防弹材料。目前,使用最广的个人保护防弹材料采用陶瓷加金属加复合材料的复合方式,最新的发展是将金属甚至是陶瓷完全去掉,以求获得最大限度的减重。以军用头盔为例,美国陆军2011年新换用的军用头盔(enhanced combat helmet)就是用碳纤维预成型体同超高分子量聚乙烯共模塑而成,与上一代的由芳纶和酚基树脂复合材料制成的头盔(advanced combat helmet)相比重量略有减轻,但防弹功能提高了10%。
军用车辆的防弹轻量化多年来一直没有停滞,传统的钢板装甲已经很少使用,复合材料防弹板的使用直接提高了装甲车的运动性和燃料效率。随着现代战争和反恐需要,防弹复合材料的设计和制造也面临新的挑战和机遇。美国纽约“9·11”恐怖袭击导致联邦政府要求所有民航飞机驾驶舱门都必须达到新的防弹要求,而全球恐怖分子普遍使用的地雷和路边炸弹对军用车辆甚至是民用车辆都提出了新的挑战。例如,为了对应这种威胁,美国驻阿富汗和中东的军用运兵车和巡逻车都采取了独特的V形复合材料防弹底盘设计,这种由美国AGY生产的新型高强玻纤增强的酚基树脂层板比原有的防弹板防弹效果增加了5%~10%,重量也同时得到进一步减轻。
新的更优化的复合材料将碳纤维、芳纶、玻纤或其他纤维合纺或叠加使用,新的纤维编织方式如3D织物也显现出了独特的优势,这样制成的复合材料不仅防弹性能得到提高,重量和制造成本也将进一步减少。另一方面,大量的材料数据和新的计算机模拟系统在未来的优化中有重要作用,例如美国的VCM(volumetrically controlled manufacturing)系统,工程师如果输入设定的防弹级别、重量或密度极限、尺寸及其他数据,VCM系统会选择最佳的复合材料层板结构、加工方式和模具要求。有报道称,根据这种优化方法得到的同等重量的超高分子量聚乙烯和芳纶的杂化纤维复合材料头盔的防弹效率比ACH头盔提高了35%,可以阻挡7.62mm的狙击步枪子弹。
复合材料还有很多其他军事用途,其中包括用以制造各种枪托的高韧性耐火复合材料,用以制造高精度轻型子弹弹壳(sabot)的碳纤维材料,用于电磁炮滑膛的碳纤维材料等,在此就不一一详述。
1.4.4 汽车和轨道交通应用
复合材料自诞生起,就开始在大众交通中得到应用,如最早的酚醛木屑/电木制成的高档汽车仪表盘。当玻璃纤维增强的复合材料出现后,通过注塑、挤出、层压、手糊、SMC、BMC等成型方法制造的复合材料,以各种不同形式应用在汽车和轨道交通车辆,以及附属设施如交通标志、地铁电缆支架、疏散平台、枕轨等之上,数不胜数。由于本节着重在先进复合材料方面,因此对这些传统应用领域不加以详述。
高性能纤维增强的复合材料由于价格偏高,尽管在近20年中有长足发展,迄今还主要用在高档或特殊车辆制造中。例如,布加迪、兰博基尼、保时捷、奔驰、宝马和奥迪某些车型的发动机罩、翼子板、车门、车顶、导流板、轮毂等,一些豪华车型甚至使用了全复合材料底盘或车架,如法拉利(见图1-11)、布加迪、保时捷等。但是,随着能源价格的攀升和环保意识的不断加强,交通工具的节油问题成为国家、社会和消费者越来越关注的问题,甚至关系到一个国家的发展战略。在全世界范围内,交通工具的轻量化已经成为一种新技术的标杆和发展趋势,世界各国甚至对汽车减排从法律角度定出了时间表。与航空工业同样的道理,实现汽车轻量化,同样是节省能源的最有效途径之一,也是国际先进汽车制造商所追求的重要目标。当节能型汽车逐渐成为发展主流的今天,与之配套的轻型油电和全电发动机对整车的减重提出了更高要求。而复合材料作为轻质高强、以塑代钢的重要材料将在汽车轻量化技术推进过程中成为主流材料,这已经成为了汽车工业界的共识。无论是传统汽油车、油电两用车和全电车,减重都已经全方位提上了日程。一些汽车企业甚至与复合材料或纤维制造企业合资或形成战略合作来实现这一目标,例如宝马与SGL、戴姆勒克莱斯勒与东丽、丰田与东邦、奥迪与沃斯等。而针对汽车和轨道交通工业的特殊性,先进复合材料行业做出了很多努力,例如通过降低原丝成本、大丝束纤维开发、液体成型和零部件一体化(part consolidation)来实现成本控制,通过开发快速固化体系、使用热塑性材料和高压注入设备来提高单位时间的零部件产量,目前已经取得了实质性进展,为先进复合材料在汽车和轨道交通上的大规模使用奠定了基础。
迄今为止,在实现从金属结构到复合材料结构整车的规模化生产这一非常难以达到的目标方面,德国的宝马公司(BMW)以其全电驱动、碳纤维复合材料乘员舱轻型轿车i3(见图1-12)成为全球汽车行业的领跑者。i3的乘员舱包括车架、车门、后门和车顶,由16个主要零部件组成,全部采用50k大丝束碳纤维预成型体和高压树脂转移成型(HP-RTM)工艺制造,其使用的环氧树脂固化时间小于10min,注射压力高达4 MPa。宝马公司从2003年开始,就率先使用RTM成型生产M系跑车的碳纤维车顶,受到车主喜爱,同时取得了加工经验。在此基础上公司于2009年启动i3计划,2013和2014年分别在欧洲和美国上市,以每充电一次行驶160km的效率受到消费者青睐,在5年内实现了量产和销售,非常不容易。也许是为了控制成本,与波音和空客不同的是,其与三菱丽阳(Mitsubishi Rayon)和SGL合作生产碳纤维原丝和碳丝,实现供应链的纵向整合,然后在宝马德国Leipzig工厂完成从碳纤维预成型件到复合材料零部件的生产和装配。目前已达到日产100辆i3的能力,而且生产速度还在继续提高。不仅如此,宝马公司表示,采用复合材料生产乘员舱比用金属更为简单,同时具有更高的零部件尺寸精度,成功展示了先进复合材料用于汽车大型结构件的广阔前景。

图1-11 法拉利Enzo的碳纤维复合材料车架与车顶

图1-12 德国宝马公司全电驱动碳纤维复合材料乘员舱轻型轿车i3
用于汽车制造的几乎所有的金属结构件都已经受到了先进复合材料的挑战,一些看来是金属材料的保留零部件也不例外,例如奥迪在2014年已经试制成功了玻纤环氧树脂的螺旋弹簧并安装到了高档车型上,这种复合材料弹簧虽然比原有的钢质弹簧稍粗,但是重量减少了40%,更多的好处是这种弹簧不会生锈,而且汽车的操控性更好。不难看出,先进复合材料对金属和其他机构材料的挑战不仅仅是一对一的取代,更是对零部件功能的升级和优化。因此,这种取代一旦发生,一般来说很难逆转,因为这种特别的现象,如今正在发生的这种变革也被一些人称为一场汽车领域“静悄悄的革命”。
值得特别指出的是,高性能热塑性树脂基的复合材料在交通工具的轻量化中将发挥巨大作用,这不仅是因为这类复合材料具有优良的韧性和损伤容限,其原材料不需要像热固体系那样特殊的存储条件,可以回收重复利用;更在于这类材料可以像金属材料那样实现快速成型甚至焊接,非常适合大众交通制造领域快速大批量零部件生产要求。目前的制约热塑形复合材料快速发展的因素除了其原料价格昂贵外,高成型温度也是主要问题之一。但是,近年来这方面进步很大,一些专用体系相继问世,如RTM级的尼龙6和缠绕用的聚甲醛等。2014年,美国Johnson Control公司采用尼龙6和玻璃纤维复合材料生产的协调功能座椅,充分利用了复合材料的功能集成模塑特点,既轻便可靠,又能提高舒适度和美观,是传统金属座椅无法比拟的。
先进复合材料用于公共交通巴士和轨道交通结构件的程度也在不断扩大,主要原因是轨道交通的轻量化压力不如航空和汽车工业大,但是巴士和轨道交通作为大众交通工具,对制造成本更为敏感,因此复合材料的较高价格成为障碍之一,造成了玻璃钢成为这些应用领域主要复合材料的现状。不过玻璃钢的缺点显而易见:强度有限、使用温度不高、工作环境有害,等等。随着电动巴士的普及,以及高铁提速、地铁和轻轨的发展需要,轻量化的要求一再提高,先进复合材料必然会逐渐取代传统玻璃钢,成为新一代公共交通的发展动力。作为有益的尝试,2014年伦敦地铁完成新车型复合材料车门的结构测试,平均每列地铁列车减重1.25t,同时大大加快车门的开关速度。德国Voith公司也刚刚完成了轨道交通用复合材料冲击杠的研制,这种玻璃纤维增强的复合材料取代钢制的冲击杠,每节车可以减重600kg。
汽车和轨道交通将是未来先进复合材料的主战场之一,因为该领域材料用量大,要求复杂并多样,对成本和制造速度敏感,机遇和挑战同样显著。
1.4.5 能源应用
除了传统的陆地和海洋油气应用的复合材料外,如管道、抽油杆、平台、浮筒等,近年来先进复合材料用于能源领域比较多的有风能、太阳能和车用电池,复合材料拉挤电缆芯也是一个活跃的能源应用方面。
风力发电机组的叶片大都采用玻璃纤维增强的复合材料制造,已经有几十年的历史。由于风力发电效率与叶片直径成正比,新一代的风机叶片尺寸不断增大,目前最长的可达75m。这样一来至少产生了两大挑战,一是叶片的减重,二是制作叶片工装的减重。前者的解决方案是采用碳纤维加强筋加上碳纤维叶端,后者同样是采用碳纤维或碳纤维加玻璃纤维的复合材料工装,尤其是那些叶片需要加热固化工艺所需的工装,因为大型金属工装的重量对于加热冷却和移动实在是太困难了。从全球范围看,风电作为一种清洁能源,装机容量一直呈上升趋势,对复合材料的需求会存在相当长的时间。其中,尤其值得关注的是近海风电场的崛起,拥有漫长海岸线的美国和英国在近两年都会有多个大型近海风电场投入建设或使用,美国能源部也持续对近海风电(包括固定和浮动平台机组)大量投入,仅2014年的研究和示范项目经费就接近1亿美元。图1-13所示为安装在苏格兰梅希尔的第一批6MW近海风电机组的叶片,这种全新的两叶设计同样采用复合材料制造。

图1-13 两叶近海风电机组翻转形成的直升机平台
电池驱动的清洁能源汽车是近年来发展的热点之一,按照目前的水平,电池的重量和尺寸较大,因此对减重和安全防护是不小的挑战。复合材料具有轻而强的特性以及抗腐蚀性,已成为许多型号电车的电池密封舱的不二选择。
复合材料电缆芯是近年来才发展起来的新技术,传统的高压电缆芯主要是钢,少量地使用铝合金。其主要缺点是太重,因此下垂严重,尤其是增加载荷的情况下更明显,使用碳纤维复合材料是一个很好的解决方案。热固和热塑树脂体系都已经有用于这一用途的,成型方法主要是连续纤维单向拉挤。热固性环氧树脂体系是目前最成熟的技术,但是其较长的固化时间影响了生产效率,还有很大的提升空间。相反热塑性树脂体系的生产速度可以很高,值得关注。例如,美国塞拉尼斯公司用热塑形聚苯硫醚与航天级的碳纤维通过拉挤成型的电缆芯就具有优异的拉伸和耐候性能,这种电缆芯进一步采用聚醚醚酮缠绕,然后再与铝质电线绕制成电缆。所制成的电缆不仅质轻,抗电偶腐蚀,而且能有效增加载荷并且能在180℃下正常运行。
1.4.6 体育休闲用品应用
可以这么说,先进复合材料的出现改变了体育竞赛的水准和竞赛范围,近现代的体育竞赛不仅仅是体能和技能的竞赛,还是科学技术的竞赛。在世界范围内,许多热门的运动项目都用到复合材料,例如滑雪板、钓鱼竿、保龄球、网球拍、赛艇、冲浪板、冰球棍、风筝和自行车、一级方程式赛车或美国杯帆船等。制造它们的复合材料包括所有的纤维和树脂,种类数不胜数,每年所消耗的碳纤维从重量上远超过了航空航天工业的用量。
复合材料还使许多失去腿的残疾人跑起来,完成了他们的运动梦,有些残奥冠军双“腿”就是用碳纤维环氧树脂复合材料单向预浸带制成,而腿箍则是由碳纤维环氧织物预浸料制成,如图1-14所示。
无论是从新材料的引入还是新的加工方式实施,复合材料在运动休闲这个领域仍在以很高的速度发展,其主要动力是很多曾经是“高档运动”的项目在世界范围日益普及,因此参与的人越来越多,对运动装备的需求越来越大;其次是过去仅限于专业运动的装备,现在因为人们经济能力的提高和装备价格的下降而逐渐成为了大众的常规装备,从而大大提升了对复合材料的需求量。自行车就是一个典型的例子,以前碳纤维车架的自行车仅是世界级运动员的专属设备,而今天的普通自行车爱好者不用花太大价钱,就可以拥有一辆不错的有碳纤维车把、车叉或车架的自行车,其普及程度可想而知。

图1-14 碳纤维复合材料腿脚
1.4.7 海洋应用
复合材料在军用舰艇、海洋能源领域的应用在前面已经做了简单介绍,本节主要介绍其他海洋用途,这些用途大致可以归为游艇(yacht)、大型游船(cruise ship)和运输船。
传统玻璃纤维加不饱和聚酯复合材料,也即玻璃钢,用于制造各型大小游艇游船已有相当长的历史,至今仍然是该领域使用的主要材料。先进复合材料,尤其是碳纤维复合材料,随着其制造成本的改善,也开始迅速进入。最明显的进入是用于桅杆和甲板,不仅能达到减重效果,而且能够通过降低重心大大增加船艇的稳定性和操控性。同样的优势也体现在用于大型游船和集装箱船的上层结构上。可以肯定地讲,如果价格具有竞争性,先进复合材料可以全面取代传统复合材料用于海洋领域,从而大幅提高这些结构的能源效率,同时实现一些独特的设计和审美理念。近年来,发展较快的高速快艇以及基于节能环保的船舶轻量化也有助于实现这种转变。
可以预见,未来复合材料制造的私人游艇、帆船、快艇和摩托艇等将会进一步普及,同私人飞机一样,成为继汽车之后复合材料应用新的增长点。图1-15所示为一家位于杜拜的公司PCT在2011年推出的40英尺(1英尺=0.3048m)FARR400,号称世界上第一款非专业用途大众版全碳纤维复合材料帆船,全部采用碳纤维真空灌注环氧树脂制造,具有极好的操控性。2012年,一艘由德国Yachtbau公司制造的太阳能驱动船Turanor Planetsolar号(见图1-16)成功环游世界,这艘明星船的船体全部由碳纤维环氧树脂三明治结构复合材料制造,堪称轻量化和节能环保的杰作。

图1-15 FARR400碳纤维复合材料帆船

图1-16 复合材料船体太阳能驱动船Turanor Planetsolar号
1.4.8 基础设施应用
在基础设施的应用领域中,先进复合材料减重的功能显得不那么明显,但是它们的抗腐蚀、高强度、加工方式多样的特点则得到了充分体现。复合材料在该领域的传统应用有各类储罐、管道、立柱加强等,大规模用于建筑还只是近十年的事。
建筑物是人类的安身之所,是文明的标志之一。复合材料具有用于建筑的所有要素,它们轻而强,能制成各种形状和结构,能抗腐蚀、抗风雨、抗冷热、抗火抗辐射,但是它们在建筑,尤其是大型建筑或建筑物基础的应用上一直没有大的发展。究其主要原因主要有三方面:一是与传统建筑材料木材、钢筋和混凝土相比成本高很多;二是建筑法规缺乏对复合材料的涵盖;三是建筑师工程师还不知道或不熟悉复合材料的使用和功能。但是,近年来情况有了明显改观。首先是复合材料的成本,包括原材料和制造成本不断降低,性能和品种不断增加,最终性价比优势开始显现。二是建筑业对复合材料的不断重视,例如美国2009年开始将复合材料加入国际建筑规范(International Building Code)的材料选项中,其中的第26章允许将纤维增强复合材料用于内墙和天花板以及其他内外部非承重结构的建造。2014年,美国Composite Panel System公司首次成功展示了功能、价格具有竞争力的复合材料民房地下室墙基(见图1-17),它们不仅比传统的浇筑混凝土墙基坚实耐久、环保节能,而且整个安装仅需两小时。更好的是这些墙体内外都不再需要进行粉刷或防水处理,该项技术已经开始在美国推广。
复合材料的特性使得这类材料特别适合用来建造对各种自然灾害和极端条件有高度抵抗力的应急性建筑物,如地震、飓风、极端潮湿或白蚁重灾区等。虽然复合材料在这方面的应用已有相当长的时间,但还会继续得到扩展。
建筑师们也日益将复合材料看作展示他们创造性和美学风格的载体,2015年完成的美国圣弗朗西斯科(旧金山)现代艺术博物馆(见图1-18)的外立面就是一个很典型的例子,该博物馆的12层楼高的外立面采用复合材料建造,以达到设计师独特的设计美学效果。这个设计需要用七百多个大型复合材料模塑件拼合而成,充分利用了复合材料的轻质特性,否则是无法达到安装要求的。采用复合材料同时也保证了结构的防水性、防火性、细部造型的生动和整体的一致性,这是迄今美国国内最大的复合材料建筑结构。

图1-17 复合材料地下室墙基

图1-18 美国圣弗朗西斯科(旧金山)现代艺术博物馆复合材料外立面效果
复合材料在其他大型基础设施的应用并不多见,主要是由于价格的原因。例如,一般的机动车桥梁,采用普通复合材料的桥面比钢筋混凝土桥面至少贵一倍,因此除了那些无法解决承重而必须使用轻一些的复合材料桥面工程外,对于一般的桥梁或道路工程来说很难采用。业内认为,除非复合材料桥面的总价格即材料加安装的总造价,能够降至比其他解决方案约贵15%或更少的程度,否则大面积推广会有较大困难。