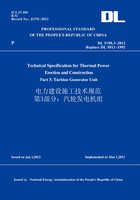
4.5 Bearing and Oil Baffle
4.5.1 Supporting bearings shall be checked before installation and comply with the following provisions:
1 All parts of bearing shall be marked with steel stamp,to ensure correct assembling of parts in location,fitting and direction.
2 The Babbitt metal load bearing surface shall be checked with oil immersion or coloring method,and there shall be no defect such as slag inclusion,porosity,pit or crack,the three wedge pad or tilting pad can be checked with UT and there shall be no disengagement.
3 The wedge oil gap and oil pocket shall be checked and shall comply with the requirements on manufacturer drawings.
4 The bearing horizontal joint surfaces shall be in proper contact,and there shall be no gap when checked with a 0.05mm feeler gauge.The bearing seat and bearing body shall be in close contact.There shall be full ring contact around the pad oil inlet hole and the cavity.
5 The joint surfaces between pad spherical surface and seat shall be smooth,and the area with contact point in every square centimeter on the contact surface shall account for over 75%of total area of the spherical face and shall distribute uniformly,there shall be no gap at the joint when checked with a 0.03mm feeler gauge,and poor contact between spherical face and its seat shall be repaired by manufacturer.There shall be no staggered part at the horizontal joint surfaces of assembled spherical pad and its seat.
6 The oil inlet holes of pad shall be clean and through,and shall be aligned with the oil supply holes on the bearing pedestals.For oil inlet hole with throttle orifice,the orifice diameter shall comply with the drawing requirements and be recorded.The thickness of orifice plate must not hinder the close contact between wedge and cavity.
7 The positions of I&C measuring point embedded in pad shall comply with requirements on drawings and the wiring shall be secure.
4.5.2 Installation of pad or pillow with cushion block shall comply with the following provisions,as shown in Fig.4.5.2.

Fig.4.5.2 Schematic diagram of lower pad cushion block
1 When the angle α between the centerline and vertical line of cushion blocks on both sides approaches 90°,the three cushion blocks and their cavity shall be in proper contact regardless whether the rotor is on the lower block,and there shall be no clearance when checked with a 0.05mm feeler gauge.
2 When the angle α between the centerline and vertical line of cushion blocks on both sides is less than 90°,and the rotor is on the lower block,the three blocks and their cavity shall be in proper contact,in the state the rotor is not on lower pad,there shall be no clearance for cushion blocks on both sides and there shall be a clearance of 0.03mm-0.05mm at the contact of lower block and its cavity.
3 An intact stainless steel shim shall be used as adjusting shim under the block,and the number of shims per block should not exceed 3,the shims shall be flat and free of burr or curled edge,and slightly narrower than the blocks.The diameter of bolt holes or oil inlet holes on the shim shall be slightly larger than the original holes and be aligned.After final locating,the number of shims in each set and the thickness of each shim shall be recorded.
4 When the color coating method is used to check the contact of lower block,the rotor shall be pressed slightly on the lower pad,and the area with contact point of cushion block with cavity in every square centimeter shall account for over 75%of cushion block area and shall distribute evenly.
4.5.3 The pad clearance of supporting bearing shall comply with requirements on drawings,and shall comply with the following provisions when there is no requirement on drawings:
1 When the journal diameter is greater than φ100mm,the top clearance of a cylindrical pad shall be 1.5/1000-2/1000 of the journal diameter,and the clearance on both sides shall be half of the top clearance.
2 When the journal diameter is greater than φ100mm,the top clearance of an elliptical pad shall be 1/1000-1.5/1000 of the journal diameter,and the clearance on both sides shall be respectively 1.5/1000-2/1000 of the journal diameter.
3 The following methods can be used to measure the clearance:
1)The top clearance can be measured with fuse pressing method,the fuse diameter can be 1.5 times the clearance to be measured,there shall be no clearance at the horizontal joint surfaces of pad after tightening the bolts.Make two or more consecutive measurements and take the average of these readings.Check the clearance at the upper pad edge on both ends with a feeler gauge,to verify the accuracy of previous measured values.
2)The clearance on both sides shall be that measured with a feeler gauge at the oil block slot,with an insertion depth of 15mm-20mm,and below the pad edge there shall be a uniform wedge clearance.
4.5.4 After the rotor is put into the supporting bearing,for either elliptical or cylindrical pad bearing,the contact angle of rotor and journal Babbitt metal should be 30°-45°,the contact area along the full length of lower pad shall be over 75%and in homogeneous distribution without deflection,any poor contact or pad clearance failing to meet the drawing requirements shall be handled by manufacturer.
4.5.5 The lower pad jacking oil pocket shall have a depth of 0.20mm-0.40mm,the oil pocket area shall be 1.5%-2.5%of the journal projection area,the oil pocket shall be in close contact with the journal on all sides,and the jacking oil passage shall be clean and through.
4.5.6 For a three-wedge pad,the length of oil wedge shall be rechecked,and the oil wedge depth b and the clearance a of oil block slot side and journal shall be rechecked as shown in Fig.4.5.6,the value a should be 1.2/1000-1.7/1000 of journal diameter,and the oil wedge shall not be trimmed.If the requirements are not met,it shall be handled by manufacturer.

Fig.4.5.6 Schematic diagram of three-wedge pad
4.5.7 Installation of tilting pads shall comply with the following provisions:
1 When the pads are checked with a micrometer,the permissible deviation in thickness is 0.03mm.
2 When the indicated shaft diameter of tilting pads is greater than φ400mm,the clearance between pads should be 1.5/1000-2.0/1000 of the shaft diameter,when the shaft diameter is smaller than φ400mm,the clearance between pads should be 1.3/1000-2.0/1000 of the shaft diameter.The deviation of pad top clearance from manufacturer design value can be trimmed by adding or removing shims on the back of pads,excessive deviation or poor contact between pad and journal shall be handled by manufacturer.
3 For a four-pad tilting pad,the top clearance is as shown in Fig.4.5.7-1,and can be measured with a depth micrometer;for a six-pad tilting pad,the top clearance is as shown in Fig.4.5.7-2,and can be measured using the fuse pressing method.

Fig.4.5.7-1 Schematic diagram of top clearance measurement for four-pad tilting pad

Fig.4.5.7-2 Schematic diagram of six-pad tilting pad
1-upper half of pad sleeve;2-upper pad;3-pad suspension screw;4-lower half of pad sleeve;5-lower pad
4.5.8 Inspection of thrust bearings before installation shall comply with the following provisions:
1 Pads of thrust bearing shall be numbered and measured one by one,their thickness permissible deviation is 0.02mm,if the permissible deviation is exceeded,correction shall be made at the general assembling according to grinding trace.If large trimming is required,it shall be done at the back of pad and records shall be made.
2 The positions of temperature measuring points for thrust bearing pads shall comply with requirements on drawings and the wiring shall be firm.
3 The load face of thrust bearing locating ring shall be smooth,the thickness permissible deviation at points along the perimeter shall be 0.02mm,and be recorded.
4 When the thrust bearing locating ring is fitted,the appropriate state is that it can be driven in gently with a hand hammer.
5 The supporting spring at the bottom of thrust bearing shall be free of jamming,the supporting force of springs shall be close to the weight to be supported,and after the rotor is put in place,the original longitudinal up-rising inclination of horizontal joint surfaces shall remain unchanged.
4.5.9 The testing of axial clearance and contact surfaces of thrust bearing pad shall comply with the following provisions:
1 The thrust bearing pad clearance adjustment shall comply with requirements on drawings,and should be 0.25mm-0.50mm if it is not indicated on drawings.
2 To measure the thrust bearing pad clearance,the upper and lower thrust pads,locating ring and upper and lower pad sleeves shall all be mounted in place.The turbine rotor shall be pushed to and fro in axial direction.
3 The thrust force to push the rotor shall comply with manufacturer requirements,and should be 20%-30%of rotor weight if there is no requirement from manufacturer.The jacks shall be arranged symmetrically on the left and right sides.The thrust bearing shall be monitored using a dial gauge and no axial displacement shall occur,it shall be fixed again if any displacement occurs.If the measurement deviation in a number of pushes exceeds 0.03mm,the cause should be found out and corrected,before a new measurement is made.
4 For a unit with Kingsbury thrust bearings,the thrust clearance can be measured by moving the thrust pad sleeve with the thrust bearing adjustment mechanism,as shown in Fig.4.5.9-1.

1-thrust pad;2-fixing bolt of adjusting block;3-lower adjusting block;4-supporting block;5-supporting ring;6-housing liner;7-oil seal ring;8-adjusting block;9-adjusting block pin;10-anti-rotation key;11-anti-rotation key fixing bolt;12-housing;13-bearing pedestal;14-throttle orifice bolt;15-nut Detail of thrust bearing adjusting mechanism

Fig.4.5.9-1 Kingsbury thrust bearing
1-fixing wedge;2-adjusting shim;3-adjustable wedge;4-adjusting bolt support plate;5-hexagon bolt;6-adjusting bolt nut;7-adjusting bolt;8-tightening wire;9-adjusting shim;10-spring washer;11-hexagon bolt
5 To check the contact surface of thrust pads,the upper and lower pads shall be fitted as required in item 1,and check shall be made by turning the rotor.The area with contact point in every square centimeter on each thrust pad shall account for over 75%of the pad total area(excluding area of oil wedge)and shall distribute evenly,otherwise it shall be repaired.
6 When the contact of half-ring thrust pad Babbitt metal is checked,the inlet and outlet oil wedge slope and chamfer shall also be checked,the contact of spherical seat and the fitting clearance shall comply with the requirements as shown in Fig.4.5.9-2.
4.5.10 For a rotor journal with flanges at both ends,the flanges shall have sufficient axial clearance from the pad end,to ensure free expansion of rotor during operation.
4.5.11 Installation of oil baffles shall comply with the following provisions:

Fig.4.5.9-2 Double-wedge and island type spherical seat thrust bearing
1 Oil baffles shall be securely fixed,the maximum clearance at split joint must not exceed 0.10mm,and there shall be no offset.
2 The edge thickness should be 0.10mm-0.20mm,the inclined edge shall be on the outer side and the oil baffle drain hole shall be towards the oil chamber.
3 The oil baffle clearance on pad and bearing pedestals shall be checked with a feeler gauge and shall comply with manufacturer requirements.
4 The oil baffle clearance of a Mitchell thrust bearing(as shown in Fig.4.5.11)or an integrated thrust bearing formed by it shall comply with the specifications in Table 4.5.11.
Table 4.5.11 Oil baffle clearance of a Mitchell thrust bearing


Fig.4.5.11 Schematic diagram of a Mitchell thrust bearing
4.5.12 There shall be an appropriate clearance from the pad locking disc,braking pin and thermometer socket to the pad,the locking disc and braking pin shall be able to function without seizing;the locking disc shall be 0.03mm-0.20mm lower than the pad horizontal joint surfaces.
4.5.13 The pad tightening force shall comply with manufacturer requirements,and shall comply with the following provisions if there is no requirement from the manufacturer:
1 The tightening force should be 0.05mm-0.15mm for cylindrical pads and be 0.00mm-0.03mm for spherical pads,this value can be increased as appropriate for bearing pedestals on both sides of HP and IP casings,provided that the maximum value of tightening force in cold state must not exceed 0.25mm.
2 The fuse pressing method shall be used to measure the pad tightening force,and this measurement must not be performed concurrently with pad clearance.
4.5.14 Installation of bearing covers shall comply with the following provisions:
1 The inside of bearing pedestals shall be clean and free of sundries,all parts have been installed in place,the clearance complies with specification and bolts have been tightened,a joint inspection has been made by steam turbine and I&C specialties and signature for concealing has been made.
2 The bearing oil cup socket shall be tightly combined with bearing,to prevent leakage.
3 Sealing coating material shall be applied on bearing pedestals horizontal joint surfaces and vertical joint surfaces of oil baffle and bearing pedestals.
4.5.15 Special tools shall be used to lift the turbine rotor for removing the lower pads,before dismantling,all pipes and parts hindering lifting shall be removed in advance,and the lifting height shall be limited to meeting the requirement to remove lower pads;when the upper steam seal has been installed,the lifting height shall be monitored with a dial gauge,the lifting shall not be greater than the upper steam seal clearance;it is not allowed to remove lower pads simultaneously at both ends.