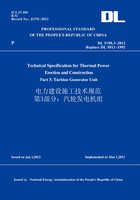
4.6 Steam Turbine Rotor
4.6.1 Rotor lifting shall comply with the following provisions:
1 Rotor shall be lifted using special cross arm and slings,which shall be properly kept.
2 Lifting positions shall comply with the requirements on manufacturer drawings,the lifting slings shall be wrapped and tied with soft materials,or cushion be used at the lifting position,the journal must not be used as lifting position.
3 When the rotor is put into the casing or lifted out of casing,a level meter shall be put at the rear journal to monitor and adjust the level,the level value shall be close to that when the rotor is in place,so that the rotor can be lifted and placed smoothly.
4.6.2 The appearance inspection of rotor before installation shall comply with the following provisions:
1 All parts of the rotor shall be free of grease,paint or rust.
2 All parts of the rotor shall be free of crack or damage.The journal,thrust collar,gears and couplings shall be smooth and free of burr.The balance weight,center hole plug and other parts shall be locked,and the couplings shall be checked as per 4.6.3.
3 The slots between fitted hubs adjacent to impeller shall be clean and free of sundries.
4 The journal ellipticity and non-cylindricity shall be less than 0.02mm.
5 The bending of shaft shall be measured and recorded,and its data and phase shall agree with the general assembling records of the manufacturer.The maximum bending difference in the middle of shrinking fit disc rotor of 6 stages or more shall be less than 0.06mm.
6 The ending run out of thrust collar shall be less than 0.02mm,and the run out shall be less than 0.03mm,it shall be treated by the manufacturer if it is not up to specification.
7 The testing position for axial displacement and differential expansion on the rotor shall be free of damage or unevenness.
8 The rotor blades and rings shall be free of looseness or damage,and be fit flatly,without unevenness.
9 Steam seal strips on the shaft shall be secure,without deflection or damage.
10 It is not allowed to make spectrum analysis of the rotor directly using a spectrum analyzer.
11 Static frequency test shall be performed for blades as required by manufacturer.
12 NDT for rotor center hole shall be performed in the factory of manufacturer,and the quality certificate shall be provided.
4.6.3 Inspection of couplings shall comply with the following provisions:
1 Parts such as keys,lock screws and nuts on the couplings shall be securely locked.
2 Steel stamps shall be made on coupling bolts,nuts and sleeves.
3 Coupling ends shall be smooth and free of burr.The ending run out shall be less than 0.02mm for a rigid coupling,and less than 0.03mm for a semi-rigid coupling or coupling on an extension shaft.The values and azimuth of high and low points of ex-circle radial run out of couplings shall be recorded respectively.
4 For a rotor with extension shaft,the radial run out of extension shaft shall be measured,and its value shall comply with manufacturer requirements.
5 The ex-circle or inner circle radial run out at the end spigot of couplings shall be less than 0.02mm,and the match of coupling spigots of two rotors shall comply with manufacturer requirements.
6 The inside of coupling bellow shall be clean and free of sundries,and the oil drain holes shall be well through.
7 After assembling of coil spring,claw or gear couplings,there shall be gap between the joined parts,to ensure movement of spring and relative movement of coupling halves,and the gap values shall be recorded.
8 The tooth side gap of a gear type coupling should be 0.10mm-0.20mm.
9 The gap of the device to prevent axial play of rotor for the flexible coupling shall comply with manufacturer requirements.
10 The coupling lubricating oil holes shall be clean and well through.
4.6.4 The journal up-rising inclination of turbine rotor shall be determined according to manufacturer requirements,if no up-rising inclination requirement is provided by manufacturer,the rear journal of the front(multi-cylinder)LP casing should be used as the zero reference point of up-rising inclination,and the up-rising inclination of other journals shall be adjusted following the shaft system centering and the values will only be recorded.
4.6.5 The centering of a single-casing unit rotor in the casing shall comply with the following provisions:
1 For rotor centering in the casing,measurement shall be made at the cavity designated by the manufacturer,the front and rear steam seals or oil baffle cavity of the casing shall be made as reference,the measuring point shall be smooth,and the measurements shall be made at the same position.
2 All parts of bearing shall be correctly placed and in good contact,to ensure that no radial change will take place at the center after turning the rotor.
3 To turn the rotor,temporary thrusting device and device to prevent rotation of bearing pad shall be provided.
4 Before turning the rotor,it shall be checked that no sundries is present between moving and stationary parts.When the rotor is turned with tools,the rotor,casing and bearing pedestals must not be damaged.
4.6.6 After completion of moving and stationary gap adjustment for casing and rotor,the relevant components of unit shall comply with the following provisions:
1 The front and rear cavity center value measuring positions shall be indicated and recorded.
2 The casing load distribution values shall comply with specification,and their values and casing horizontal up-rising inclination shall be recorded.
3 Conditions of lower pad Babbitt metal contact surfaces,pad cushion block and cavity contact surfaces and spherical contact surfaces shall comply with the relevant provisions in 4.5 of this part.
4 The contact surfaces between soleplate and bearing pedestals,soleplate and casing and claw and load bearing face shall comply with the relevant provisions in 4.4 of this part.
5 The sliding pins shall be adjusted up to specification and fixed.
6 Rotor coupling centering for double cylinder or multi-cylinder turbine shall be performed in sequence and be recorded.
7 The centering for devices such as main oil pump,worm wheel set and reduction gear in connection with rotor shall be performed concurrently before the final locating of shaft system.
4.6.7 The center permissible deviation of turbine shaft system shall comply with manufacturer requirements,and the provisions in Table 4.6.7 shall be complied if there is no requirement from manufacturer.
Table 4.6.7 Center permissible deviation of shaft system(mm)

Note:values in this table include no additional compensation,and in the work,necessary correction shall be made based on the compensation data provided by manufacturer.
4.6.8 Centering for shaft system shall comply with the following provisions:
1 The relative positions of both end faces of coupling shall be aligned with the marks made by manufacturer;if there are no such marks,the run out of both end faces shall be supplementary to each other,with due consideration on mutual alignment of all bolt holes;after final alignment and connection of couplings,marks shall be made.
2 For each measurement,the couplings of the two rotors shall be turned by 90°in the same direction,the turning angle shall be the same and the measuring point locations on both couplings shall remain unchanged.
3 Ending run out shall be measured at 180°to each other,dial gauge shall be set at two corresponding points with equal radius,and half of the maximum difference of all data shall be taken for a full turn.To measure the coupling radial run out,dial gauge shall be set at the ex-circle of coupling,and the maximum difference of all data shall be taken for a full turn.
4 When dummy pad is used for centering for a rotor supported by only one bearing,after connection with coupling and removing the dummy pad,the cavity center value at the coupling shall remain unchanged.
5 When the rotor is set to place,make sure that the rotor is not pressed on the oil baffle or steam seal.
6 During measurement,there must be no rigid connection between the rotors,each of them shall be free.
7 The shaft system centering tool shall have sufficient rigidity and be mounted in a secure and reliable manner.When dial gauges are used in coupling centering,the gauge stand shall be secure.After a full turn of the coupling back to the initial position,the reading of the dial gauge in circumferential direction shall be back to the original value.
8 The clearance between coupling end surfaces can be measured with gauge blocks or feeler gauges,which shall not exceed four layers in total during measurement.
9 Rotors shall be turned according to relevant stipulations in 4.6.5.
10 During centering of shaft system,the oil baffle cavity shall be maintained within the specified range.
11 The journal up-rising inclination with design value as zero should remain unchanged.
12 Between the casing and soleplate,bearing pedestals and soleplate,pad block and soleplate and between pad blocks,clearance shall be checked using a 0.05mm feeler gauge.
13 During shaft system centering,the water volume in condenser shall comply with the manufacturer requirements.
14 In centering for couplings of a rotor with three supports,the reserved lower end faces gap between couplings shall comply with the manufacturer requirements,and it should be 0.15mm-0.25mm if there is no requirement from manufacturer.
15 After connection of shaft system,couplings shall be checked for concentricity,and the permissible deviation in concentricity shall be 0.02mm.
4.6.9 After initial centering of shaft system,and before connection of shaft system couplings,the shaft system center shall be re-measured in the following phases:
1 After connection of condenser with casing.
2 After completion of foundation secondary grouting and tightening of anchor bolts.3 After tightening of joint surface bolts following cylinder covering.
4 After connection of steam lead,large diameter cold drawn pipe and casing.5 After release of vibration isolator spring of elastic foundation.
4.6.10 For rigid or semi-flexible couplings requiring reaming for bolts on field,bolt tightening shall comply with the following provisions:
1 Before reaming or boring,the coupling center shall be checked as specified,and the strength of secondary grouted concrete shall be 70%and over.
2 The two couplings shall be aligned at the relative positions of centering.
3 Before reaming or boring,the couplings shall be connected temporarily,and after temporary connection,the shaft system concentricity shall be measured,and its permissible deviation is 0.02mm.First,two opposite holes at 180°shall be reamed at the couplings,and coupling bolts be prepared as required by manufacturer,after tightening,turn the rotor and then other bolt holes can be reamed in sequence.Cold spring shall be done for coupling bolts symmetrically in diameter direction.
4 During reaming or boring,no other work that may affect the connection of shaft system shall be performed.
5 The finished bolt holes shall be perpendicular to the flange end faces of couplings.The fitting between bolts and bolt holes shall comply with the provisions in GB/T 1800.1-1800.2-2009,the gap between bolt and bolt hole shall be H7 and h6,the surface roughness shall be no greater than for pin cylinder and not greater than
for pin hole.Lubricant shall be applied when bolts are fitted,which shall be knocked in gently with a copper rod.After fitting,corresponding steel stamp marks shall be made for bolts and bolt holes.
6 The tightening torque and elongation of coupling bolts shall comply with the manufacturer requirements.
7 In case of loose fit of coupling bolts and bolt holes without reaming,the coupling spigot fit shall comply with the manufacturer requirements,and the concentricity after fitting shall be checked.
8 Before fitting,the coupling bolts and nuts shall be weighed one by one,and the total weight difference of two bolts and nuts in the symmetrical diameter direction of coupling shall be less than 10g.
4.6.11 When adjusting shims are provided between the couplings of two rotors,the reaming or boring shall also comply with the following provisions in addition to those in 4.6.10:
1 The thickness of shims shall be the average of left and right measured gaps between the two couplings at the time of rotor locating,with machining permissible deviation as 0.02mm,the surface roughness shall be no greater than,and there shall be no burr,crack or oily dirt.
2 Shims shall be in place when reaming is done for couplings.
4.6.12 When a bridge gauge is used to measure and record the journal height,the gap of bearing bridge gauges with journal should be about 0.50mm;the bridge gauges shall be put on the bearing pedestals split and be clearly marked,bridge gauges shall be in good contact with bearing pedestals plane;the bridge gauge number and direction and journal height shall be recorded.