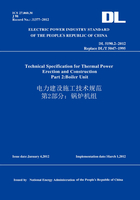
5 Heating Surface
5.1 General Provisions
5.1.1 This chapter may be applicable to the construction and acceptance of the boiler heating surface(including steam drum,the steam-water separator,the waterwalls,superheater,reheater,the economizer,the header,the desuperheater,and so on),the proper steam-water connecting pipes,the boiler water circulating pump and the start-up boiler water circulating pump,as well as the external heating surface,the steamcooled separator and other equipment in the circulating fluidized bed boiler.
5.1.2 Before the erection of the equipment in heating surface,the comprehensive counting shall be carried out in accordance with the supply goods list,the packing list and the drawings.More attentions shall be paid to checking the defects in the surface,including the crack,contuse,chap,flattening,sand inclusion,delamination,and so on.If any depth of surface defect is above 10% of the regulated pipe thickness and more than 1mm,the handling shall be carried out according to the requirements of Article 3.1.7 in this Part.
5.1.3 During piping,the attention shall be paid to inspecting the allowable deviations for the outer diameter and wall thickness of the pipes in the heating surface,which shall meet the requirements of Appendix J.If any deviation is more than the requirements of standard,the handling shall be carried out according to the requirements of Article 3.1.7 in this Part.
5.1.4 Alloy steel components shall meet the requirements of equipment technical documents.Before assembly and installation,the material shall be re-inspected and be marked at the obvious location.The marks shall be checked after erection.If there is any ambiguous mark,re-inspection shall be carried out again.
5.1.5 Before the assembly and installation of membrane heating surface,inspection shall be carried out to the geometric dimension of tube arrays and the location dimension of metal accessories,access holes and so on.The manufacturer's drawing requirements shall be met.
5.1.6 The ball-passing test for heating surface tubes shall meet the following requirements:
1 Ball-passing test shall be carried out before the assembly and erection of heating surface tubes,respectively.Steel balls shall be used and numbered with strict control.There shall be no ball left in the tube.After ball-passing test,the reliable closing measures and the record shall be taken.
2 The testing compressed air pressure should be no less than 0.4MPa.The blowing shall be carried out before the ball-passing test.The secondary pigging shall be carried out for any assembly without the header.The diameter of testing ball shall meet the requirements of Table 5.1.6.
Table 5.1.6 Ball diameter for ball-passing test(mm)

Notes:Di—The tube inner diameter(the inlet tube inner diameter Di shall be the actual measurement inner diameter.The inner diameter of internal screw tube Di shall be Do—2×wall thickness-2×screw height);Do—The tube outer diameter;R—The bending radius.
3 The pigging may be carried out with the wood balls for heating surface tubes whose outer diameter is more than 76mm.The light inspection may be carried out to the straight pipes.The header tube connection seat may be inspected with the wire rope whose diameter is equal to the steel ball diameter.The pigging shall be carried out to each tube in the trident pipes.
5.1.7 If there is a throttle device arranged at heating surface tubes or headers,the throttle device shall be kept unblocked.
5.1.8 The mechanical cutting should be carried out for heating surface tubes.If the flame cutting is used,the mechanical processing allowance shall be left in the cutting port sections.For the piping operation for heating surface tubes,the grooves shall be provided according to the manufacturer's drawing requirements and the piping clearance shall be uniform.The locations within the scope of 10mm-15mm from the pipe ends shall be ground cleanly until the metallic luster is exposed before the welding.
5.1.9 The piping ends of heating surface tubes and the tube center line shall be vertical,whose end sloping valueΔf shall meet the requirements of Figure 5.1.9 and Table 5.1.9.
Table 5.1.9 Tilting value of pipe end face(mm)


Figure 5.1.9 The schematic diagram of pipe end tilting
5.1.10 The inwalls of the butt joint for welding components shall be flushing,and the local indented joint value of the butt joint one-sided welding shall not exceed 10% of the wall thickness and shall not exceed 1mm.
5.1.11 The piping deflection for heating surface tubes shall be inspected with the ruler and the open joint within 100mm from the weld center shall not exceed 1mm.
5.1.12 The butt joint craters of heating surface tubes shall not be arranged in the bending locations.The distance between the crater and the pipe bending starting point shall be no less than the pipe diameter and 100mm(except the welding,forging and casting molding pipe fittings).The distance from the hanger frame edge shall be 50mm.
5.1.13 The distance between the adjacent two welds of the straight section in the tubes of the heating surface shall be no less than the pipe diameter,and it shall be no less than 150mm.
5.1.14 Before lifting the heating surface assembly,the re-inspection shall be carried out to the positions of all pivot and hoisting points,and the sizes of steeves.
5.1.15 When drilling holes in pressure-bearing pipes,the mechanical processing shall be adopted and flame cutting shall not be used.Any metal chips or other sundries shall not be fallen into the pressurebearing pipes.
5.1.16 For alloy steel bolts with the design temperature above 430℃and the diameter greater than or equal to M30,hardness tests shall be done one by one.The hardness value shall meet the requirements of DL 5190.5 Technical Specification for Thermal Power Erection and Construction-Part 5:Piping and System.
5.1.17 For the erection of the tubes in heating surface,the internal cleanness shall be ensured and there shall be no any fallen sundries.
5.1.18 The erection of the expansion indicator must meet the manufacturer's drawing requirements.The erection shall be firm,and the arrangement shall be reasonable.The indication shall be correct.
5.1.19 When heating correction is carried out to alloy steel components,the heating temperature shall be controlled below the steel critical temperature Ac1,which is shown in Appendix E.
5.1.20 When cutting the fins of membrane heating surface,the tubes shall be protected from any damage.The material and thickness of steel plates used for butt seams shall meet the manufacturer's drawing requirements.
5.1.21 The locking pins of the spring for heating surface hanging device shall be in the locking position during boiler hydrostatic test,and they can be removed before boiler ignition.