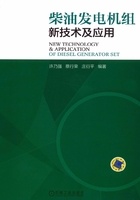
2.4 增压中冷及多气门技术
2.4.1 增压中冷技术
在发动机中,增加平均有效压力是提高和强化发动机功率的最有效措施之一。而增加平均有效压力通过增压来提高进气压力,增加燃烧的过量空气因数,同时增加柴油机的空气进气量,可有效降低大负载工况下的排气烟度、PM排放量以及燃油消耗。
增压方式取决于增压能量,增压方式有机械增压、废气涡轮增压、复合增压、气波增压,目前应用最广泛的是废气涡轮增压。废气涡轮增压因排气能量利用方式不同分为定压涡轮增压系统和脉冲涡轮增压系统,低增压的中小型发动机,高增压的车用柴油机采用脉冲涡轮增压系统,大型柴油机一般为定压涡轮增压系统。
涡轮增压系统分单级和多级,单级的压比从1.1~3.5,而二级的压比可达6.0以上。二级增压在增压器低转速的情况下获得较高的压比,而且不依赖于气体流量的大小,因此在提高进气压力的同时,扩展了增压器的工作范围,使得增压器适应发动机不同工况的需求,特别是改善了启动性能。
废气涡轮增压的特点:提高功率20%~50%;提高经济性能、机械效率和热效率(油耗降低5%~10%);降低排气噪声和烟度;加速性能差;热负载(活塞温度、涡轮前废气温度高)问题严重;机械负载(最高燃烧压力)大;对气温与气压敏感;易发生增压器低压级漏油高压级漏气现象。
中冷器是增压系统的一部分。当空气被高比例压缩后会产生很高的热量,从而使空气膨胀密度降低,而同时也会使发动机温度过高造成损坏。为了得到更高的容积效率,需要在注入气缸之前对高温空气进行冷却。这就需要加装一个散热器,中冷器使发动机的进气温度降低。发动机排出的废气有非常高的温度,增压器的热传导使进气的温度提高。且被压缩的空气密度会升高,导致空气温度升高,发动机的充气效率受到影响,若想要充气效率进一步提高,就要使进气温度降低。数据表明,在空燃比相同条件下,增压空气每下降10℃温度,发动机就能提高3%~5%功率。通常中冷器可以将气体温度从150℃降到0℃左右;如果燃烧室进入未经冷却的增压空气,除了发动机的充气效率会影响外,发动机容易导致燃烧温度过高,造成爆震等故障,而且发动机废气中的NOx的含量会增加,造成空气污染。
为了消除增压后的空气升温造成的不利影响,需要加装中冷器使进气温度降低。中冷器由铝合金材质制作。按照冷却介质区分,常见的中冷器有两种:风冷式和水冷式。
风冷式利用外界空气对通过中冷器的空气进行冷却。优点是整个冷却系统的组成部件少,结构比水冷式中冷器相对简单。缺点是冷却效率比水冷式中冷器低,一般需要较长的连接管路,空气通过阻力较大。风冷式中冷器因其结构简单和制造成本低而得到广泛应用,大部分涡轮增压发动机使用的都是风冷式中冷器。
水冷式利用循环冷却水对通过中冷器的空气进行冷却。优点是冷却效率较高,而且安装位置比较灵活,无需使用很长的连接管路,使得整个进气管路更加顺畅。缺点是需要一个与发动机冷却系统相对独立的循环水系统与之配合,因此整个系统的组成部件较多,制造成本较高,而且结构复杂。水冷式中冷器的应用比较少,一般在发动机中置或后置的车辆上,以及大排量发动机上使用。凡事有利就有弊,涡轮增压也不例外。发动机在采用废气涡轮增压技术后,工作中产生的最高爆发压力和平均温度将大幅度提高,从而使发动机的机械性能、润滑性能都会受到影响。为了保证增压发动机在较高的机械负载和热负载条件下,能可靠耐久地工作,必须在发动机主要热力参数的选取、结构设计、材料、工艺等方面作必要的改变,而不是简单地在发动机上装一个增压器就行了。由于这个改变过程在实行中难度颇大,而且还要考虑增压器与发动机的匹配问题,因此在一定程度上也限制了废气涡轮增压技术在发动机上的应用。
采用有效的空—空中冷系统使工作循环温度下降,增压空气温度到50℃以下,有助于NOx的低排放和PM的下降,目前大中功率柴油机普遍采用增压中冷型,不仅燃油经济性良好且有助于低排放。此外,涡轮前排气旁通阀的应用,可以改善涡轮增压柴油机的瞬态性能和低速扭矩,降低PM和CO排放。
2.4.2 多气门技术
发电机组用现代柴油机一般采用四气门结构。四气门发动机是指每一个气缸的气门数目有两个进气门和两个排气门的四气门式。
发动机配气机构中气门装置是一个主要组成部分。燃油发动机由进气,压缩,作功和排气4个工作过程组成。4个工作过程周而复始,顺序定时地循环工作是发动机连续运转的保证。
进气和排气两个工作过程,需依靠发动机的配气机构按各气缸的工作顺序准确地输送可燃混合气(汽油发动机)或新鲜空气(柴油发动机),以及将燃烧后的废气排出气缸。另外的压缩和作功两个工作过程,须气缸燃烧室与外界进排气通道隔绝,不让气体外泄,保证发动机正常工作。配气机构中的气门是负责上述工作的机件。
随着科学技术的发展,发动机的转速越来越高,发动机的转速可达5500r/min以上,只需0.005s时间可完成4个工作过程,柴油机的转速可达3000r/min以上;传统的两气门无法胜任这么短促的时间内完成换气工作,发动机性能的提高受到限制。扩大气体出入的空间是解决这个问题的方法。即用空间换取时间。解决问题的最好方法是多气门技术,直至80年代多气门技术应用才使发动机有了一次质的飞跃。
目前,多气门发动机常用的是四气门式。4缸发动机有16个气门,6缸发动机有24个气门,8缸发动机就有32个气门。气门数目增加就要增加相应的配气机构装置,构造复杂,排列在气缸燃烧室中心线两侧的气门由两支顶置式凸轮轴来控制。为了尽量扩大气门头的直径,加大气流通过面积,改善换气性能,气门布置在气缸燃烧室中心两侧倾斜的位置上,形成一个火花塞(或喷油器)位于中央的紧凑型燃烧室,有利于混合气的迅速燃烧。
四气门结构不仅使充气效率提高,由于喷油嘴可以布置在中间,使多孔油束分布均匀,为燃油和空气的良好混合创造条件;同时,在四气门缸盖上将进气道设计成两个独立的具有同形状的结构,以实现可变涡流。这些因素的互相配合,大大提高混合气的质量,有效降低碳烟颗粒、HC和NOx的排放,并有助于热效率的提高。
另外,在全电控柴油机中,电控可变气门技术即气门不需要凸轮轴驱动,而是根据其工况和电控气门的开启和关闭,由于这一全新技术还处于研究实验阶段,发电用柴油机还没有采用这种新技术。