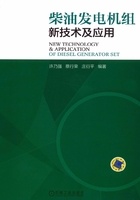
2.5 智能变速风扇及其他
2.5.1 智能变速风扇
风扇是发动机功率的消耗者,最大时约为发动机功率的10%。为了降低风扇功率消耗,减少噪声和磨损,防止发动机过冷,降低污染,节约燃料,欧洲许多运输车辆上采用离合器以实现风扇变速。
在柴油发电机组行业,柴油发电机组作为通信电源的终极保障,以其高可靠性和性价比等优势得到广泛应用。随着通信规模的爆发性增长,特别是大型枢纽、数据中心的集中建设,其备用发电机组功率需求达50000kVA以上,单机功率也高达2000~3260kVA。
智能变速风扇采用电控硅油离合器技术,根据机组负载的不同,通过ECU(Electronic Control Unit,微机控制器)监控不同散热器组件的温度值,依据温度值与转速百分比的对应关系,ECU向离合器发出转速命令,通过PWM(Pulse Width Modulation,脉冲宽度调制)形式实现风扇转速的无级、连续智能控制,从而达到优化冷却系统,改善柴油发电机组的节能环保运行等的核心技术及效果。
目前的柴油发电机组,大都采用水箱带风扇冷却,风扇靠柴油机上的动力直接驱动,机组运行时,冷却风扇转速一直与柴油机保持同步,从空载至满负载始终在额定转速1500r/min附近,即不论机组的负载大小,冷却风扇都送出最大的风量和最大功率的能耗。通信行业配套的大功率机组,柴油机冷却风扇的功率高达80kW以上,必须优化其冷却系统。
柴油机工况的特性是:柴油机机身(水温)温度,保持在较高(通常为80~98℃)状态的带载能力及效率是最佳的。在柴油机启动至投入负载这阶段,应该使水温快速升高,然而,冷却风扇却始终全功率反方向降低温度,造成很多无功损耗,特别是极端低温的环境,能耗及环保的影响更为明显;另外,在机组整个带载过程,最佳的工况是使柴油机的发热与风扇的冷却效果保持相对平衡。为此,应用变速风扇,是优化冷却系统,实现柴油机始终处于最佳工况并大幅降低能耗、改善燃烧效果及减少排放的有效途径。
如图2-46所示为配置智能变速风扇的机组外形图,如图2-47为智能变速风扇节能效果图。可以直观看出,应用智能变速风扇的效果。
图2-46 配置智能变速风扇的机组外形图
1—底座 2—柴油机驱动轮 3—电控硅油风扇离合器 4—散热水箱 5—风扇 6—从动轮 7—传动带 8—离合器智能控制模块CPU 9—柴油机 10—集成控制电缆 11—柴油机ECU 12—发电机 13—发电机组控制器
当柴油机启动后,风扇处于怠速,其风量及消耗功率最小,使机组暖机并快速进入带载最佳转态,减少无功损耗及降低噪声;在进入带载或满载前(柴油机上节温器打开后),通过智能调节风扇的风量,优化柴油机的冷却平衡,在满足柴油机最佳运行温度的同时,最大限度地提高设备的效率和降低风扇功率,达到节能减排的目的。
1.电控硅油离合器系统及控制原理
电控硅油离合器系统主要由硅油离合器、控制器Di、速度传感器和柴油机固有的散热器(水箱)组件、风扇、柴油机控制单元ECU等组成如图2-48所示。控制原理如下:
图2-47 智能变速风扇节能效果图
图2-48 电控硅油离合器Di控制原理
1)通过ECU监控各种相关温度值:水箱、中冷器、排气、机油和燃油等。
2)根据温度值与转速百分比的对应关系,ECU向离合器发出转速命令,通过PWM形式实现风扇转速控制。
3)电控硅油离合器采用失效保护措施:如果离合器断电,则全速运转,确保万无一失安全可靠运行。
由上可知,电控硅油离合器系统特别简单、可以很方便地在任何现有柴油机加装应用。冷却风扇转速(功率)的优化,反馈信号采集完整、控制可靠简捷。
2.电控硅油离合器工作原理
电控硅油离合器工作原理如图2-49所示。
图2-49 电控硅油离合器工作原理图
1)当控制阀打开时,硅油从硅油腔进入工作区域,硅油进入工作区域后通过硅油表面张力传递动力,由主动盘带动风扇旋转。同时硅油在离心力的作用下,通过回流管流回储油腔。
2)控制阀的开关由电磁线圈控制。当电磁线圈通电时,控制阀门关闭;当电磁线圈断电时,控制阀门打开。通过PWM形式,可以方便地实现电磁线圈对应开关量,进而使控制阀处于闭环受控状态。
从上面可知,硅油离合器的核心工作原理:主动盘(柴油机驱动),透过硅油表面张力传递,使从动盘(安装风扇)实现可控差速旋转;转速差靠硅油工作区域充满程度改变其张力的大小来实现;而硅油工作区域充满程度则由电磁阀的开关量,通过PWM命令控制调节;PWM的信号源取自相关温度值,从而实现智能、电控、闭环和精准的优化柴油机冷却系统,达到节能环保的目的。
3.主要技术特点
智能变速风扇,采用独特的设计思路,巧妙地将大部分构件集合于最小体积内的硅油离合器之中,其主要特点:
1)应用范围广泛:可以满足任何柴油机的改装。
2)装配便捷:结构紧凑、安装简单,可以装配在曲轴或传送带轮上。
3)功率范围大:单个最大功率可达45kW、扭矩为250N·m、风量为55776m3/h、静压为834Pa,可以单个或多个使用。
4)节能减排运行:能根据柴油机冷却需要响应不同的最佳转速,减少不必要的功率消耗,节省燃油,降低排放。
5)使用寿命长:相比电磁离合器,采用高稳定性的硅油柔性控制,零件几乎没有磨损、没有冲击力,可靠性极高、使用寿命长。
6)效率更高:相比液压驱动离合器,不需要其他额外零部件和电源,效率更高,特别是高电压柴油发电机组,液压的动力源很难满足。
7)较高的性价比:少投入、高收益,既节能、又环保,具有较高的经济和社会效益。
相比常规恒速风扇,智能变速风扇的节能效果特别显著,最高可达50%以上。同时也能进一步改善低温气候操作性能,降低柴油机排放,降低散热器堵塞,延长传送带的使用寿命,减少尘土的产生和降低风扇噪声等效果,切实能为用户创造额外的价值,这对于不断提高柴油发电机组的应用技术水平具有一定的意义。
2.5.2 废气再循环(EGR)技术的应用
废气再循环(Exhaust Gas Recirculation,EGR)的技术在发达国家的先进内燃机中普遍采用,其工作原理是气缸内引入少量废气,这种不可再燃烧的CO2及水蒸汽废气有较大热容量,使燃烧过程的着火延迟期增加,燃烧速率减慢,缸内最高燃烧温度降低,使NOx的生成被有效破坏。EGR技术可明显降低发动机NOx排放,但对大型柴油机,倾向于使用中冷EGR技术,该技术不仅能使NOx明显降低,其他污染物也能保持低水平。
内燃机在燃烧后排出的气体含氧量极低,此排出气体与吸气混合后使吸气中氧气浓度降低,因此会产生下列现象:含氧量比大气更低会降低燃烧时(最高)的温度,对氮氧化合物(NOx)产生抑制。燃烧温度降低时,会降低气缸与活塞表面、燃烧室壁面的热能发散,另外,会降低因热解离造成的损失。发动机部分负载为气缸内在非EGR时,为了提供等量的氧气量,因此需将油门开大,结果吸气时的吸油(油门)损失较低,燃料消费率提高。此即为在一次行程下活塞吸入的氧气降低时,如同使用小排气量引擎加速前进时有一样的效果。EGR的返流量依燃油引擎在吸气量中最大为15%,而怠速时与高负载时会停止。引擎负载较高,会使用到EGR技术达到排气量标准。
EGR技术在1970年触媒转化器实用化以前,因燃油机无法使用氧化催化来净化NOx的情况下而导入。但是在无法精密控制返流量与燃料喷射量的情况下,为了使燃料能够稳定,使吸气混合比必须设的很高造成燃油会过剰、使燃料消费率恶化。后来、随着控制技术的提高且触媒转化器的实用化,NOx的排出与燃料消费率提高的问题现在已经可以解决。原理上EGR在柴油机没有节流阀时,减低油门损失上是没有效果的,但在1990年前期在EGR研究中发现,以减低NOx为目的的排气中存在大量二氧化碳与水蒸汽与大气来比有较高的热容量,对于燃料消耗率的提升有一些效果。
在吸气与排气的管道间接上插有控制阀门的管子来实现排出气体的返流,控制流量的变化是利用控制阀门的开闭时间。由于有返流的高温排气,所以可以忽略充填吸气低下的效率,因此大型柴油机几乎装有用热交换器制成的冷却机构(COOL EGR)。多数会将引擎的一部份冷却水分流,将吸收的热量用冷却机构来进行散热,但会使散热器负载额外增加30%,所以增大冷却风扇等其他设备将导致重量增加。另外,大型的装有涡轮增压器的柴油机在高负载时进行EGR,吸气会比排气压力大、会使单纯的阀门开关返流无法进行。因此须设置EGR控制阀门止回阀。理论上若能改变EGR量就有可能将柴油机的节流阀取消,但在点火时困难,大量的EGR会造成不稳定的燃烧,以及在怠速时无法达成稳定的状态,使其难以实用化。EGR与稀薄燃烧技术有很大的关联性,还有气缸内直接喷射技术中稀薄混合气下燃烧如何能稳定等问题。
2.5.3 后处理技术
排放后处理技术是指为了降低发动机尾气的排放,而对发动机进行适当的处理而不使环境污染的技术。排放标准从国Ⅱ到国Ⅲ,燃油喷射系统是关键技术,而从国Ⅲ到国Ⅳ,排放后处理技术就必须结合使用。目前,国际内燃机行业从欧Ⅲ发展到欧Ⅳ,后处理技术主要有两种基本体系。在欧洲倾向于SCR(选择性催化还原)体系,利用尿素溶液处理尾气中的氮氧化物;在美国和日本倾向于EGR(废气再循环)体系,即通过微粒催化转换器(Diesel Particulate Fi-iter,DPF)或微粒捕集器,EGR(废气再循环)技术对燃烧产生的微粒进行处理。因国情不同,各国企业选择的技术路线也不同。
在技术路线方面,国内生产柴油机主流企业基本达成共识,未来国内柴油机排放升级的主要技术方向将采用SCR。目前,康明斯、玉柴、潍柴等都采用了SCR技术。
更适合中国市场的SCR系统有以下特点:1)SCR系统能使燃油消耗更加节省。相对于EGR+DPF系统SCR系统的燃油消耗稍低一些,它的尿素水溶液消耗量的补偿可在燃油消耗上得到。2)如果采用此技术,在很长时间内可以满足排放法规的要求,直到引进欧Ⅴ乃至更高排放标准。3)在EGR+DPF系统中,冷却器的体积需要增加,而SCR系统只需一个附加的贮藏罐。4)降低发动机的复杂性。SCR系统可以同时满足国Ⅲ、国Ⅳ的标准,可以提前在部分地区引进。
2.5.4 乳化柴油的应用
稳定的含水乳化柴油是柴油加水掺和而成的乳化剂,使用这类改进型燃料的目的是有效降低柴油机的排放,尤其是PM和NOx。在美国该应用较为普遍,我国在这方面研究较为深入,成果可喜。经过实验加水20%的乳化柴油70天不分层,大型柴油机在100%负载工况应用中,节油明显而且功率不减,比柴油动力输出上升4.3%,而且PM和NOx排放明显下降。这项技术对低排放尽管有好处,但水结冰、水对发动机的腐蚀等潜在的问题尚待解决。乳化柴油(微乳化柴油):是水(或甲醇)和柴油通过乳化剂、助乳化剂在一定乳化设备经乳化而形成的油包水型透明乳液,微乳粒径小于100nm;微乳的乳化剂用量远大于乳化的用量;微乳化剂较乳化剂的稳定性好。
应用特点:
机械搅拌操作简单,能耗低(油燃烧释放热的减少低于水量的比重,即燃烧率提高),乳化后其燃烧排放的颗粒物PM10、氮氧化物NOx污染明显减少,燃油效率提高等优点(二次雾化的结果等),柴油乳化可分为两种:在线乳化燃烧和预乳化,在线乳化对柴油机有较高要求,需要改造柴油机或添加装置,一般市场很难接受,所以预乳化工艺成为研究热点,我国柴油乳化技术研究起步较晚,目前尚未有掺水量高、稳定性好的乳化柴油投入市场,河南农业大学研制的CZF-A型乳化柴油和TA-1型乳化柴油,其节油性能高、稳定性好、着火点高,对乳化柴油的制备工艺研究得较为详细,所制备出的乳化柴油14.0%掺水量,与一般柴油外观一致,且有较高的稳定性。
乳化柴油是一种很有发展前途的替代燃料,不仅节能,而且使环境污染大大减少,必将替代传统柴油。面对日益严峻的环境污染和能源危机,加快研究乳化柴油的配制技术具有重要意义。
2.5.5 机油消耗控制技术
柴油机的机油消耗的高低是衡量柴油机功能是否良好的重要标准,控制柴油机的机油消耗量可以减少能源浪费,减少人类对能源的开采,保护环境,实现可持续发展。
柴油机正常运行机油的消耗量一般相当于柴油消耗量0.4%~2.5%,若超过该数值,表明柴油机运行时消耗的机油过多。柴油机机油消耗过多主要有三个原因:一是机油由缸套活塞组窜入燃烧室;二是机油沿气门与导管的间隙落入燃烧室;三是机油从其他密封处渗漏。
为了控制机油消耗量,进而达到控制柴油机颗粒物排放,在机油消耗控制技术方面,柴油机作了以下改进:
1)结构上气缸体采用圆形水套;加大缸盖螺栓的沉头,采用PT网纹,采用先进的活塞环结构与材料,增大缸套上部的冷却强度等。
通过对曲轴箱负压、配缸间隙、气缸孔实际工作圆柱度及活塞环参数改进试验和分析,得出了小型单缸柴油机减少机油消耗量降低颗粒排放的技术措施和机理。
2)柴油发动机通过开发新的活塞环,换用新式节能活塞环,尤其是油环,提高刮油能力,防止燃烧室窜入机油。
气缸盖罩迷宫油气分离等技术降低发动机的机油消耗,将机油与燃油消耗比控制0.05%之内。
3)多缸柴油机可设置滤网式通气孔,单缸柴油机可以安装负压阀,曲轴箱内保持为负压或零压,防止出现正压。
4)及时更换磨损的气门导管,防止机油沿气门杆落入燃烧室。
5)采用密封胶粘剂,能起密封、防漏、紧固和堵塞缝隙的作用,达到防止机油渗漏的目的。
6)更换机油应做到定期。当机油变稀或老化导致润滑作用失去时,要及时更换新机油。
7)机油滤清系统一般包括全流式和旁通式滤清器。一个设计良好的滤清系统可降低发动机的磨损和机油的消耗量,并对发动机的排放起到控制作用。因而,能在经济和环境两方面获益。要致力于研究采用全流式细滤器的优点以及旁通式滤清器的使用。
在机油缸套活塞组柴油机排放的颗粒物中,有相当一部分来自馏分较重的机油的燃烧。烧机油是指机油通过一定的途径进入了发动机的燃烧室,(主要是由于活塞环损坏导致汽缸漏气,机油窜入燃烧室)。与混合气一起参与燃烧。进行定期保养非常重要,若这种现象长期出现,不但耗损机油较大,而且机油燃烧生成的杂质将会造成燃烧室积碳的增加,进而影响发动机的使用性能。
柴油机排放限值标准的要求日益严格,必须有效控制发动机烧机油的现象,在保证发动机正常运转的前提下,最大限度地降低机油的消耗。活塞环的优化设计和制造及缸套间的科学配置对降低柴油机的机油消耗非常重要。
社会的进步,科学技术的快速发展,人们对柴油机的要求越来越高,新技术的应用应围绕节能环保展开,在结构上要求轻便、紧凑;在噪声控制上,重视噪声源的控制,如机体部件精度提升降低机械噪声;在排气消声上,采用新的降噪材料及结构;在尾气排放上,从满足国Ⅲ向国Ⅳ及国Ⅴ的排放标准进行新的后处理技术应用;发动机的各部分传感器精度越来越高,电控技术日新月异,这些都是提升排放标准的保证;柴油及润滑油质量的提升确保了发动机的使用性能,柴油机将在社会发展中发挥更大的作用。