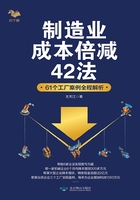
【案例8】效率攻关成功留住老客户
辅导对象是一家为国内外众多一线手机知名企业提供部品的大型企业,所供部品型号相对较少、数量巨大。调研刚刚结束,过完元旦的第2天,笔者就接到了一个不好的信息,出差到美国的国外营销总监发邮件称,一家一直合作的老客户将中断多年的合作关系,他目前在客户处一边被“修理”,一边在寻找缓和的余地。主要问题是上个月的交货数量太少,月平均交货数量达成率不足60%。最初客户电话投诉这个问题,没有引起各部门的重视,公司交货量一直没有明显提升,反而使客户多次调整生产线,导致客户生产效率和终端销量受到影响,客户总部对此极为失望,要求终止合作关系。
营销总监发送邮件说,客户基于这么多年合作的考虑,勉强答应给予企业两周的改善时间,如果还是不能按数量交货,将会把现有在生产的模具全数拉走,客户上个月中旬已经启用新的备用供应商。
作为企业的老客户之一,客户给出了最后通牒。企业董事长指示总经理必须想尽一切办法满足客户的要求,不能让客户流失。
大家都知道,开发一个新客户的总成本比维护一个老客户的总成本高出5倍以上。也就是说,如果老客户丢失,企业将花费5倍以上的时间、精力及资源寻找到一个新客户。
总经理为此立即召集生产总监、生产经理、品质经理、设计经理、模具经理、计划主管、主导工程师(属设计部)参加会议,主题就是讨论如何达成客户的交货需求。计划主管称客户的需求是每天交货38K(1K代表1000),实际产出只有30K,除去不良品数量根本不够交货。
这样的会议是众多企业里常见的一幕,看起来大家说的都有道理,却不能解决问题,主持会议的总经理听完大家的发言后沉默不语,他赞成并重复了生产总监的提法,让生产部想办法提升产出和良品率。生产经理又开始说回原来提到的那些因素,然后参会人员再次发言,发言内容和前面几乎一样,会议就这样开了一个小时,陷入僵局。
企业总经理这时邀请笔者参加了会议,针对交货问题提供一些意见。笔者了解完现状后,给出了五条意见:
第一,设计部工程师主导测量每套模具每个机台具体的产出周期,不要用一个固定的时间来计算产出,详细给出每台机每套模具每一班的定额,车间负责每台机两小时报告1次产量,对产出大于定额的一线员工给予现金奖励。
第二,以产出和良品率为导向,设计部主导、车间协助找到每套模具与每台机的最佳匹配,即使正在正常生产的机台也需要为这个部品交货让路。
第三,由车间主导,品质部及设计部协助,针对现有排名前5位的不良现象列出具体的改善动作和操作要求。
第四,模具部门主导将前12套模具的产出状况、品质状况问题点详细列出来,由设计部和模具部共同给出解决方案,在交货数量充足、有库存的情况下,由计划主管通知车间安排修模。
第五,将上述内容形成攻关方案,参与上述改善事项的人员每周交货数量达成给予一定的奖励。
企业总经理同意了上述意见。第2天再次召集会议:
一周后,12套模具的产出数量平均值达到了44K,最高的1天达到了47K。第2周产出数量平均值达到了45K,计划主管开始安排修模,后续的两周也都达到了交货数量。一个月后,营销总监发邮件表示感谢,称客户对上个月交货情况比较满意,没有再提终止合作的事,还下发了新的订单。之后的几个月里,这个客户没有再投诉过交货问题。
这个事例说明,攻关是打破管理僵局的有效手段,在关键时刻能够帮助企业化解困难与危机,攻关对品质成本、生产成本、管理成本都有明显的降低作用。