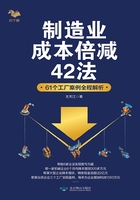
【案例15】辅导机加工外协厂商提质降价
这是一家多年前笔者辅导过的中型机械厂,中间曾陆续辅导过1期,这次进行第3期辅导。这次辅导其中的一个工作重点是提升机加工外协厂商的品质状况。
作为机械厂,这家企业电气类的零部件标准化程度较高,采购的重点是选择合适的供应渠道和比价,供应链管理相对容易;而机加工的种类多、数量少、批量小,一部分加工件只有1件,尺寸多、物料流转多,供应商分散,供应商数量60家以上,供应链管理相对复杂。
对这些供应商实地考察后发现,这些企业的规模参差不齐,规模大一些的供应商有100多人,大部分供应商的规模在50人以内,还有一部分供应商只有几个人,企业老板有时还需要参与生产。品质管理也是多种多样,有的企业有专职的品管人员,约占15%;有的企业用车间生产管理人员代替品管,约占45%;剩下的企业没有配置品管人员。这些供应商中,有一部分属于独家供应商,由于技术原因、品质原因、单价原因、付款原因无法短期内找到数量众多的替代供应商,个别独家供应商难以要求和改善。这样的局面让人灰心丧气,感觉无从下手。
反过来想一下也释然了,现有一些中小企业的供应链就是这个状况。这家企业也一样,就是这么一群小微企业的供应商们支持着这家机械厂的大发展。对这家企业的供应链来讲,从某种程度上说,这也是一种“奇迹”,这已经不是在“制造”而是在“创造”,这种局面肯定是企业的过渡阶段,只有正视这些问题,才有机会解决这些问题。
从品质数据来看,经过不断的努力,外协进料合格率已从5年前的70%左右进步到现有的92.3%,离目标值97.5%还有5.2%的差距,折算成加工零件件数是约80万件×5.2%=41600件。也就是说,每月有3467件、每天有116件机加工零部件不良,这些不良会造成欠料,影响生产进度、交货进度,需要耗费大量的人力、物力去处理、去解决,外协进料合格率制约着客户交付满意度。
经过内外部详细调查、走访、论证,与各部门各级人员多次讨论,笔者列出了机加工外协厂商的品质提升思路,并与企业董事长、各部门管理人员达成一致,总体思路如下:
(1)供应商品质标准的完善:供应商所供零部件必须有书面的、双方签字认可的检验标准和检验手法说明(含检测工具),并确保更改时双方保持一致。
(2)通过采购货款支付周期杠杆撬动供应商老板质量意识的改变,只有供应商老板对质量方面有所改变,供应的零部件质量才有可能变好。
(3)现有每月各类供应商品质排名必须由供应商老板、品质负责人签字盖章回传,排名靠后的企业除延迟货款外,供应商老板及品质负责人必须来本公司检讨、报告所供零部件的后续品质改善具体动作。
(4)对品质排名一直靠后且改善意愿不强的供应商进行逐步淘汰,采购部针对这几家供应商所供零部件开发出一定数量的新供应商进行储备。
(5)因为所供零部件严重影响本公司的效率、造成返工、造成拆解报废产生费用的,除要求供应商承担损失外,也需要供应商老板及品质负责人来本公司检讨并报告后续品质改善具体动作。
(6)通过提高供应商对品质问题的认真度,结合品质辅导过程中供应商提出的各种问题,认真检讨本公司存在的内部供应链综合管理问题,本公司设立供应商品质投诉专线(打印在《采购订单》上),欢迎供应商投诉本公司图纸问题、变更问题、检验标准问题、吃拿卡要问题等。
(7)对供应商品质状况进行准确分类,区别对待,分别设定质量管理目标,新的年度重新签订品质保证协议(含设定后的质量管理目标)。
(8)针对个别关键部件厂商(如YH、BC)采用先维系感情(需要董事长参与),再切入辅导,最终改善质量(前提是财务保证货款按时支付)的策略。
(9)所有外协供应商质量“自我管理”体系完全建立(让供应商品质辅导不再有盲区):
·设定制程/终检(每个供应商工序不一样,这里是指零部件交付本公司前的最后一道工序)控制点。
·设定专人对应本公司交货零部件质量管理。
·本公司进行考评认证(认证的人数可以多,防止认证人员流失后品质再次失控,负责对应本公司交货零部件质量管理的专人建议供应商增加薪资,增加的薪资列为品质考核,参与辅导的供应商一开始可以由本公司SQE-供应商质量工程师参与打分考核)。
·重要零部件交货时附出货检验报表。
·如交货后零部件产生返工由供应商品质认证者带队到本公司执行返工。·供应商内部建立品质问责制度等。
(10)针对本公司进料、制程、客户端反映的每一单供应商品质问题,一律要求分析出发生原因、流出原因、临时对策(列出具体动作)、长期对策(列出具体动作),列出责任人、监督人(主要由本公司SQE负责)、改善完成时间、验证结果并记录、改善奖惩措施。
(11)SQE的职责完善:外出辅导必须提供第9点、第10点所列所有事项的检查记录(现有SQE人数不够,需要增加1人)、所辅导的供应商来料品质状况与SQE每月绩效挂钩。
(12)公司对外出辅导人员给予足够的政策支持和便利(如出差费用补贴、餐费标准、派车安排等),不要过度限制,导致辅导人员不想出去、不愿出去,出去了带有情绪从而解决不了问题。
(13)禁止参与供应商辅导人员(主要是SQE人员)在供应商处就餐(列为长期制度),外出辅导供应商产生的餐费由本公司全额承担,参与供应商辅导人员需要签订《廉洁自律声明》并在本公司对全员公示,另拟定正式通知请各供应商签字回传。后续如果发现有辅导人员在供应商处就餐,将对责任人进行行政处分,对违规接待的供应商,月度评比中直接降一级处理并减少采购数量。
(14)与计划辅导的供应商签订《供应商品质辅导协议》,明确辅导事项及辅导过程中的责权利。
(15)本公司内部需要提供的辅导支持:①工艺技术辅导支持:工程部;②品质辅导支持:品质部。
这些思路逐一形成可执行方案签发后,对机加工外协供应商的品质辅导就紧锣密鼓地开始了。第一批供应商的辅导由笔者亲自带队,依据思路和方案糅合多种落地管理思想,制定了针对这次辅导用的《供应商辅导改善验证查检表》。后续的辅导证明,这份表格可以在所有的供应商辅导中使用。
辅导人员与供应商见面后除了常规的寒暄客套外,立即切入正题,按该表格的内容对每一个出现过品质问题的零部件进行再次讨论、分析和记录。这份表格先将品质问题的原因分为发生原因(即为什么会发生这个品质问题)和流出原因(为什么会流到客户处,发生品质问题不一定会流到客户处,可以“堵”住不流出,具体可参考本书案例6中的“品质漏斗”)。两大原因分开叙述,再针对这两个原因列出临时对策、长期对策,分别制定改善动作、责任人、完成时间,这些内容确定后由本公司SQE加以实地验证,最后双方共同确定激励措施。
在讲述发生原因、临时对策时,供应商老板和管理人员大都能说出几点,到了讲述流出原因、长期对策时,有的供应商人员开始紧张说不出原因,显然这并不是辅导的目的。辅导人员关注的重点是供应商的改善动作和完成后的效果,供应商想不到的对策,就由参与辅导的人员一一给予补充并与供应商达成共识。
这样一轮问询、辅导下来,第一批的供应商所供的有品质问题的主要零部件都填写了《供应商辅导改善验证查检表》,填写完成的记录双方参会人员共同签字确认。有了改善动作后,由本公司SQE到各供应商处巡查、监督,这批供应商的内部掀起了品质改善的热潮,有不少供应商派出了员工到本公司学习。
表1-3是某关键零部件机加工外协厂第一轮品质辅导后填写的一份《供应商辅导改善验证查检表》。
第一轮辅导完成后,由企业方的品质部开始主导第二轮辅导、第三轮辅导……逐步覆盖了90%以上的机加工供应商。
半年后,大部分供应商完成3轮辅导。经统计机加工外协进料合格率为97.75%,提升了5.25%,超目标0.25%达成;数量上,月平均进料在9.6万件,同比增加了35万件。
另统计,上一周期采购平均降价1.39%,其中外协降价率为1.46%、外购降价率为1.32%,外协降价比例首次超过外购降价比例,与过往外购降价容易降价比例高,外协降价困难、降价比例低的情况形成了鲜明的对比。
在辅导供应商的过程中也遇到了个别不配合的供应商,使采购不得不启用备用供应商。如外协钣金件,原供应商无法配合辅导,采购启用了一家距离较近的备用钣金厂商,该厂商承接了公司近40%钣金件的外协。经过定期辅导后,物料的品质和交期反而比前一家供应商更稳定,价格在原采购价格基础上降价幅度为15%~20%。
据财务统计,这一周期内机加工外协降价金额第一次超过了100万元。
采购经理反映,没有想到外协降价能超过外购降价,这些参与辅导的机加工外协供应商知道公司是在真心帮助他们改善,品质管理严格对他们内部整体的管理帮助较大,品质辅导传递的这些管理方法同样可以在其他客户的产品上适用。在此期间,我们采购和这些供应商无论是谈品质、谈成本、谈交期都特别好沟通,容易达成共识,降价只是这几轮供应商品质辅导过程中的副产品。
在笔者参与辅导的供应商中,有一家至今记忆犹新。这是一家不到10人的电镀厂,去过两次给了企业老板一些管理上的指导和经营上的建议,老板虽然充满感激但电镀品质却提升不大,我们还是安排人员定期给予辅导。两个月后,电镀厂老板主动找到我们,说他经过这段时间的技术钻研,有办法解决目前电镀不良品率高的问题。电镀厂老板主动表示,电镀液并非全部进口,并且多次使用,加上长时间没有更换新电镀液,这是造成电镀品不良品率一直居高不下的主要原因。他提出了针对本公司的电镀产品更换德国拜耳电镀液的建议,电镀产品公司每公斤只需要增加1元费用,剩下的费用由他的公司承担,电镀良品率将会有较大的提高。经公司评审、核算后同意了他的提议,3周后更换了电镀液,电镀产品品质状况果然有了质的提升。


其实,这些小微企业也需要有人指导,这些小微企业老板对真心帮助他的人充满感激。企业在其规模小的时候主动与供应商形成良好的互助关系,供应商做大了,不会轻易离开,你的企业做大了,供应商可以跟着一起发展。
从一些破产的知名企业状况来看,供应商往往也是压垮企业现金流的最后一根稻草。辅导过程中可以看到,一些客户和供应商辅导后,和管理咨询辅导的感受一样,大家形成了难忘的记忆,有的形成了师徒关系、朋友关系,而不仅仅是商业活动中的利益关系。
供应商辅导从成本面来看更不应该被忽视,供应商现有的生产工艺、技术水平可以用来检视采购价格、了解行业上游的发展状况,供应链的新工艺、新材料、新技术一定程度上左右了本行业企业的成本,如果能够快人一步了解并应用到这些新的事物,企业的总成本就有机会领先一步。